大型数控龙门铣床主轴柔性传动系统的创新设计
2017-7-26 来源: 成都利君实业股份有限公司 作者:燕文
摘要:相对于大型数控龙门铣床而言,主轴在铣床整体中占据关键地位,与铣床使用年限、加工精度等存在密切关联。大型数控龙门铣床内的主轴装置在滑枕处,和传动轴直接连接,而传动轴另侧和减速器连接,减速器相连于驱动电机,借助传动轴将驱动电机旋转运动传至主轴。主轴传动系统与传动轴的质量性能的高效与否,对大型数控机床龙门铣床的整体性能产生直接作用,其主轴柔性传动系统的创新设计显得尤为重要。
关键词:主轴;传动系统;创新设计
铣床指的是通过铣刀对工件展开铣削加工,可以在铣床中展开平面、沟槽、分齿零件、螺旋形表面和不同曲面的加工工作。与此同时,铣床还能够切断、加工回转体表面与内孔。因大型数控龙门铣床的生产效率与生产质量均高,在机械制造领域的应用较为广泛。
1.铣床及铣床滑枕研究现状
1.1 铣床研究现状1.1 铣床研究现状
在 1884 年间,龙门铣床得以发明;随着现代社会的高速发展,半自动铣床出现并得到应用,通过挡块工作台可实现 “ 进给 - 快速 ”,以及 “ 快速 - 进给 ” 的自动转换。在龙门铣床的应用过程中,其加工精度与使用年限得到飞速提升。随着数字化控制的广泛应用,在提高铣床自动化方面做出较大贡献。
早在七十年代,微处理数字控制系统与自动换刀系统在铣床方面得到广泛应用,在丰富其加工功能的同时,有效提高了效率与质量。在机械事业的成熟发展下,大部分机床操作开始采用数据编程,降低了劳动强度。同时,其适用范围和布局形式得到多元化发展,包括升降台铣床、龙门铣床、单柱铣床、单臂铣床等。
1.2滑枕研究现状
龙门铣床在加工大型工件斜面、平面中的应用较为广泛,尤其是大批量生产制造。大型龙门铣床的门式框架有立柱、顶梁构建而成,横梁可沿立柱导轨升降,装有铣头的滑枕装配在横梁上方,能够沿着横梁导轨进行横向运动。此外,部分铣床立柱还可以安装有水平主轴的铣头,能沿立柱导轨展开升降。这部分铣头能够对多个表面一同加工。每一铣头都装有相应的变速设备与驱动电机、主轴附件等。加工过程中,工作台中的工件可以随着操纵位置展开运动。
滑枕为大型数控龙门铣床的主要构件,其性能高效与否对机床工作效率产生直接影响。在机械制造领域一步步走向成熟的过程中,对大型零部件的要求逐渐提高。利用该零部件,能够实现对端面、内孔与外圆的车削加工,并丰富其平面、沟槽、曲面、斜面、内孔及外圆的铣削加工工作。可以从滑枕材料与主传结构等方面提升龙门铣床的强度,考虑到球墨铸铁的工艺性能,其强度、塑性、动负荷性能;相对于一般灰铸铁而言,其弯曲疲劳限度可超出 1 倍以上。自传统滑枕的工作过程中,其传动轴两侧的轴承支撑容易出现摩擦起热,阻碍铣床的安全运作。为解决这一难题,可以在铣床滑枕传动轴的构架中采用有限元分析技术,进一步改善传动轴的性能与结构,利用相关程序避免计算流程的复杂化,有利于提高设计质量,控制设计时间。
2.铣床滑枕柔性传动轴设计
2.1 主轴传动系统结构改良方案
考虑到主轴传动系统的不同影响要素,可以着手于结构进行改善,为提高大型数控龙门铣床的使用年限和加工精度,对主轴柔性传动系统展开研究。一般来说,传统主轴系统传动系统为刚性,传动轴两侧有轴承作为支撑,在加工、安装过程中要注意相应孔的同轴度;因传动轴的长度值较高,很难保障相应孔的同轴度。此外,经改善后的主轴柔性传动系统,去除传动轴两侧的轴承支撑。通过柔性传统系统的自主调整,使得两侧位置不对应时能够自行调节,保证扭矩的可靠性。该传统系统仅需两个待加工的孔,利于传动系统加工精度和工艺性能的提高,合理控制了费用支出。
2.2材料选择
在材料选择过程中,需明确零部件的使用标准,考虑到载荷部位的危险性,要明确材料的重量比值、抗疲劳与抗断裂性能。大型数控龙门铣床主轴柔性传动系统的创新设计,突出了扭矩强度与韧度。例如:钛,外形类似于钢铁,材质却坚韧轻盈,密度较低;与铂金熔点相似,在 1675℃之间,在军工及航天精密零部件中得到广泛应用。因钛的抗腐蚀特性明显,能够完整放置于任一强碱、强酸内,具备太空金属的使用优势。
现阶段,在龙门铣床主轴柔性传动系统所用的材料中,钛合金的强度最高。钛合金以钛为前提,融入相应的合金元素,具备良好的工艺性能与韧度。能够在两侧不对心的状况中传递转矩,利于延长系统的使用年限,合理控制对心难度与成本支出,及时消除风险隐患。
2.3 过渡曲线确定
在计算机技术高速发展的背景下,有限元方法的应用逐渐普遍。通过对每一过渡曲线进行有限元分析,核对分析内容,可有效避免传统轴间过渡的圆角应力集中现象。在分析过程中,可采用由下至上的建模形式(点 - 线 - 面 - 体);可构建二维面积网络,通过旋转得到相关三维映射网络有限元模型,该构建流程较繁琐,却有利于提升计算速率,保障计算数据的精准度。大型数控龙门铣床主轴若星传动系统的过渡主要采取样条曲线,利用过渡端和两侧轴承的连接,不仅能够控制应力集中,还能延长其使用年限。
3.传动轴结构设计
3.1 传动系统模型元件确定
一方面,惯性元件。主要指的是每一轴的旋转质量,即皮带轮、齿轮、卡盘等零部件。在传动系统运作过程中,这部分零部件的动力学原理,着重体现在转动惯量中。通常来说,一根轴中的惯性元件,能将这部分质量集中至轴两侧,出现等效圆盘,扭转变形忽略不计,则可以作为刚性圆盘使用,转动惯量主要为:

为转动惯量;m 为等效圆盘质量;p 为等效圆盘的等效直径。另一方面,弹性元件,即两大等效圆盘间的轴段,对传动系统的作用主要体现在自身的扭转刚度。利用轴段间的转动惯量,能够在刚性圆盘中重叠,来控制轴扭转刚度的精准度。
3.2 参数转换
具体参考主轴传动系统的建模知识,可以将轴扭转刚度值与转动惯量有效转至输出轴 3,转换之后的惯量为 164.01×103、146.06×103、8.71×103;其扭转刚度则为 45.63×105、4.21×105、1.93×105。
3.3 模态参数计算
以相关数学模型为基础,模态参数的计算则需要程序编写,并详细解出固有振幅、频率及模态柔度、势能分布率,绘制相关程序图。计算内容主要有元件总数、频率方程、扫频初值、扫频终值、扫频步长、频率方程、系统模态柔度、动能分布率、势能分布率、固有频率等;此外,要划分相应的性能参数数组、状态矢量数组、传递矩阵数组、矩阵数组等。合理控制模态柔度与势能分布率、扭转固有频率;参考动能分布率,适当降低质量。
3.4 传动系统动态设计
以模态参数计算为前提,适当提升、降低元件刚度和质量。参考建模流程,合理分配齿轮与输出轴惯量。切实考虑轴自身刚度,轴承刚度、跨距等影响要素;在提高轴刚度的同时,需要适当增加其直径、刚度,降低跨距。此外,要适当降低轴、齿轮质量,如缩短轴长、缩小直径、改善齿轮构架。另一方面,要参考能量平衡理论和模态柔度设计相关内容,科学分配阻尼。通过品质因素、阻尼比、粘性阻尼系数与对数减缩、损耗因子,呈现振动系统的阻尼特征。因阻尼均小,科学增强相应模态的弹性能分布率中的子结构阻尼。通常为了表征系统阻尼特性,会涉及到粘性阻尼系数 c、损耗因子 η、对数减缩 δ 等,它们间存在一定等效关系:
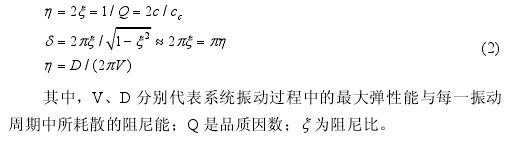
4.总结
本文着重分析了大型数控龙门铣床主轴柔性传动系统的创新设计,就传动轴结构、参数等提出进一步的改善方法。利用有限元计算方法,论证设计内容的可行性;分析传动轴的模态,不断寻找设计弊端,改善模拟技术,来保证计算数据的精准性,做到具体问题具体分析,控制实验成本。
投稿箱:
如果您有机床行业、企业相关新闻稿件发表,或进行资讯合作,欢迎联系本网编辑部, 邮箱:skjcsc@vip.sina.com
如果您有机床行业、企业相关新闻稿件发表,或进行资讯合作,欢迎联系本网编辑部, 邮箱:skjcsc@vip.sina.com