热轧铸锭铣床翻转机技术改造
2017-6-22 来源:烟台南山轻合金有限公司 作者:李俊丰,孙 妍
摘要: 文章列举了热轧铸锭铣床翻转机使用过程中暴露出的问题,并针对这些问题做出相应的技术改进,效果良好。
关键词: 铣床; 铸锭; 翻转机; 垂直夹紧; 侧夹紧
1.设备概况
南山轻合金热轧引进进口铸锭铣床加工系统,该系统包括锯床、1#铣床、1#翻转机、2#铣床、2#翻转机,见图 1。其工作流程为,铸锭从锯床上料,经锯床锯掉头尾后进入 1#铣床铣削 1 个上面、1 个侧面和 2 个斜角,然后进入 1#翻转机将铸锭翻转,翻转完毕传送到2#铣床加工 1 个上面、1 个侧面和 2 个斜角,加工完毕经 2#翻转机直接传出,用起重机吊走。由于 1#翻转机衔接两台铣床,日常工作载荷大,联机使用频率高,且设备存在一定缺陷,所以频繁出现铸锭翻转后下降颤动、液压缸不同步、铸锭跑偏、翻转机窜动、翻转圆盘开焊等故障,其是否稳定运行,直接影响铝铸锭铣削加工系统的效率。为此,我公司成立铸锭翻转机技术攻关小组,针对翻转机存在问题进行攻关,以提高设备性能,保证机组正常连续生产。本文主要介绍铸锭翻转机关键部位存在的问题以及提出的技改方案。
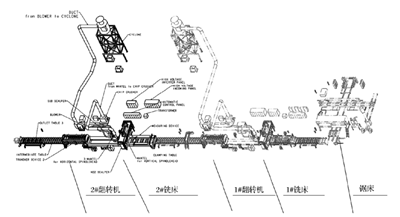
图 1 铝铸锭锯铣加工系统
2.垂直夹紧液压缸不同步问题
2.1 翻转机动作过程
铸锭在铣床上加工完上表面、2 个斜上角及 1 个侧面后,进入翻转机。铸锭移动至图 2 所示位置后停止( 左端面对齐,由位置传感器确定) ,接着 2 个垂直夹紧油缸伸出,带动大梁和 8 个压块压紧铸锭上表面,使铸锭压紧在下表面辊道上; 侧夹紧装置( 图 4 所示) 顶住铸锭 1 个侧面,然后翻锭机在链条带动下开始绕中心轴线旋转 180°,此时大梁和垂直夹紧油缸位于翻锭机下方; 2 个垂直夹紧油缸收缩,带动大梁和 8个压块缓慢下降,铸锭也随之缓慢下降落到辊道上,此时铸锭未加工表面处在上方; 翻锭机辊道开始转动,使铸锭传送至 2#铣床工作台,从而可以对铸锭未加工表面进行铣削。
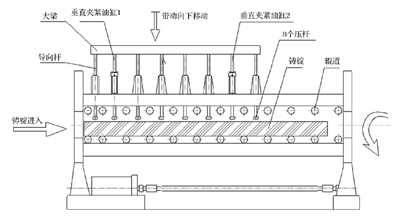
图 2 翻转机翻转前工作示意图
2. 2 故障现象
铸锭翻转机翻转铸锭后,经常会出现 2 个垂直夹紧油缸下降动作不同步,致使垂直夹紧装置卡住的现象,导致铸锭无法正常落在辊道上。实际生产时,只好临时采用对油缸排油的方法让活塞收缩,严重影响正常生产。此外,夹紧油缸托铸锭下降过程中颤抖严重,经常性的剧烈颤抖导致翻转机圆盘频繁开裂,严重时导致翻转机框架大梁出现裂纹。
2. 3 故障分析
从铸锭翻转机液压控制系统上看,2 个垂直夹紧油缸的回路各有 1 个流量控制阀控制。原设计的初衷是通过单独调节每个流量控制阀来保证 2 个油缸同步,但每次调节好后,再继续工作( 尤其是铸锭尺寸变化) 时,2 个夹紧油缸不同步的故障又再次出现。从图 2 翻转机翻转前示意简图里,可以看到,2 个夹紧油缸的中心与铸锭中心( 重心) 存在偏差。尚未翻转时,铸锭本身的重心并未落在 2 个垂直夹紧油缸上,此时2 个油缸活塞杆伸出,直至压紧铸锭,2 个油缸受力基本相等。但是,在反转 180°后,此时铸锭的重量全部落在 2 个垂直夹紧油缸上,由于铸锭中心( 重心) 距离2 个夹紧油缸距离不同,因此,这 2 个油缸活塞受力是不同的( 右边油缸受力大于左边油缸) ,再加上液压设计流量补偿功能设计的不完善,从而造成 2 个夹紧油缸活塞运动速度不同步,铸锭无法正常落在辊道上。
2.4 解决方案
首先,改变翻转机铸锭传送位置,即将翻锭机垂直夹紧机构的位置移向中间( 在图 2 中,夹紧机构向右移动) ; 同时采用中间定位的方式,让不同长度的铸锭均停止在中间位置,从而使铸锭中心和 2 个垂直夹紧油缸的中心重合,这样,无论油缸活塞伸出或收回时,这 2 个油缸受力基本保持相同。其次,原设计中翻转机夹紧装置由 2 个液压缸驱动,还设有 6 个导向柱,导向柱太多摩擦力不均匀也对翻转机翻转后的夹紧、打开产生影响; 现将原来的 6 个导向柱改为 2 个,取消导向柱之间的连接大梁,每个油缸并联一个导向柱,避免了因导向柱和连接大梁受力不均扭曲而造成液压缸卡死的现象。此外,在两个垂直夹紧架侧面各增加 1 个接近开关,一旦出现一侧液压缸先夹紧问题,另一侧仍然会在系统补偿下继续动作,直至另一个接近开关被触发,夹紧油缸停止动作( 图 3) 。改造后,铸锭翻转完成后,垂直夹紧液压缸托着铸锭下降平稳,没有颤动和铸锭砸翻转机现象,圆盘和翻转框架再未出现开裂问题。
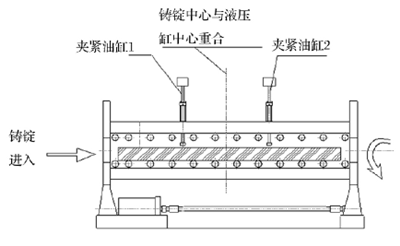
图 3 改造后翻转机示意图
3. 侧夹紧梁连接销断裂
3. 1 侧夹紧梁的作用
铸锭进入翻转机,当垂直液压缸夹紧后,侧夹紧液压缸开始动作,直至夹紧大梁与铸锭侧面接触,防止铸锭在翻转时发生倾斜和滑动,铸锭向侧夹紧方向翻转。
3. 2 故障分析
侧夹紧装置因液压系统限制,偶尔会出现侧夹紧两个液压缸动作不同步问题,由于之前侧夹紧装置的2 个液压缸是用 1 根大梁连在一起,所以一旦出现液压缸动作不同步,就会导致单端大梁与铸锭接触,另 1个液压缸动作不到位,使这端的侧夹紧大梁与铸锭之间有间隙,在翻转时出现铸锭侧滑,撞击大梁现象,导致大梁定位销断裂。
3. 3 解决方案
将侧夹紧大梁取消,每个液压缸单独驱动 1 个夹紧块,每个夹紧块边部同垂直夹紧装置一样各安装 1个接近开关,改造前后对比见图 4、5; 铸锭垂直夹紧后,侧夹紧开始动作,当一侧夹紧接触后,该侧停止动作,而另一侧仍然推进,待另一侧接近开关触发后液压缸停止运动,铸锭被完全夹紧,开始进行下一步动作。改造后侧夹紧装置运行稳定,没有出现铸锭侧滑及撞击夹紧大梁现象。
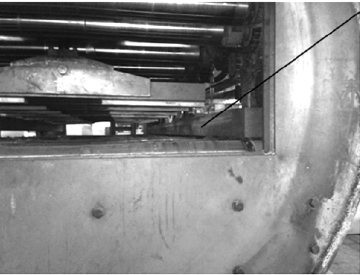
图 4 改造前侧夹紧装置
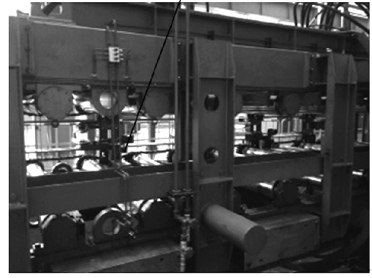
图 5 改造后侧夹紧装置
4.翻转机翻转后已加工的铸锭下表面粘铝
4. 1 故障现象
1#铣床铣削好的铸锭进入翻转机,翻转后传入 2#铣床,但是由于铸锭在进入翻转机前,上表面存有未能吸走的铝屑,铝屑被垂直夹紧块压到铸锭表面,一方面在铣削完毕的表面产生缺陷,另一方面压到垂直夹紧的尼龙压块上,损伤尼龙压块,在后续铣削的铸锭上产生压痕。
4. 2 故障分析
铸锭上存有铝屑主要有两方面原因,一方面,铣削加工时铝屑回收系统回收不完全; 另一方面,翻转机前端的铸锭吹扫系统风力不够。
4. 3 解决方案
(1) 改造主铣刀盘和侧铣刀盘的护罩。在保证铣削最大加工量时刀盘护罩不与铸锭接触的情况下,在刀盘护罩上焊接扁铁圈,增加铝屑吸收量;
(2) 改造翻转机入口空气吹扫。将原来 DN25 的压缩空气管改为 DN50 的压缩空气管,将原 1 个吹扫54喷嘴增加到 3 个,见图 6。
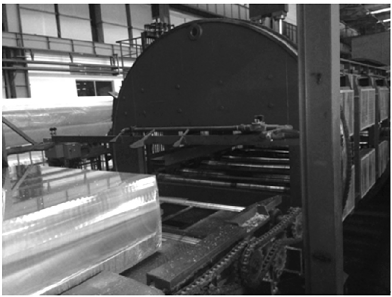
图 6 改造后的吹扫系统
改造后的铝屑吸收效果明显提高,即使个别未吸净的铝屑也被翻转机进口空气吹扫系统吹掉,彻底避免了铝屑压入的缺陷。
5.其他问题
翻转机传动辊道链条张紧支架频繁变形,以及驱动电机底座螺栓松动严重的问题。
5.1 故障现象
翻转机每工作一段时间,就会出现传动辊道链条张紧支架变形,以及驱动电机底座螺栓松动的问题,虽然链条张紧支架和电机底座螺栓一再加固,但仍不能解决这一问题。
5.2 故障分析
经过现场观察发现,外方调试时将翻转机辊道驱动链条调整过紧,每次传送铸锭时,由于链条太紧造成所有辊道同时驱动,电机启动扭矩太大,同时也易导致张紧装置受力过大而损坏。
5.3 解决方案
将所有辊道的链条张紧装置进行调整,避免过紧和过松,并在驱动电机底座固定处增加防窜动挡块。改造后铸锭运送平稳,未出现链条张紧装置损坏和驱动电机螺栓松动的问题。
6.结论
通过对翻转机垂直夹紧、侧夹紧大梁液压缸动作不同步的改造,以及对铝屑压入铸锭问题的解决,铣床翻转机运行逐渐平稳,整套铣床系统月产量提高30% 以上,铣床的开机率也明显提高,改造效果明显。
投稿箱:
如果您有机床行业、企业相关新闻稿件发表,或进行资讯合作,欢迎联系本网编辑部, 邮箱:skjcsc@vip.sina.com
如果您有机床行业、企业相关新闻稿件发表,或进行资讯合作,欢迎联系本网编辑部, 邮箱:skjcsc@vip.sina.com