钛合金薄壁件 3D 打印工艺技术
2024-7-2 来源: 航空工业航宇救生装备有限公司 作者: 关要轩 李 湘
【摘要】: 针对钛合金薄壁零件在新品制造中,存在生产周期长、成本高、加工变形等诸多问题,通过对合金薄壁壳体零件采用 3D 打印制造技术,对 3D 打印毛坯设计、设备选择、成型过程控制、后续处理,以及后续机加进行引用研究。该研究应用对航空新品类似零件的生产加工有很好的使用和参考价值。
【关键词】: 钛合金 ; 薄壁件 ;3D 打印 ; 支撑设计 ; 加工变形 ; 膨胀芯轴
前言
钛合金是一种非常重要的有色金属,比强度高且有密度小,并具有良好的高温变形性能、耐腐蚀性能等优点,在航空航天、工业、国防、医疗等领域得到广泛应用。采用传统的铸造和锻造等增材方法所制得的复杂的钛合金零件,由于材料利用率低、成本高、工艺复杂以及后续机械加工困难度高 ,严重影响其广泛应用。而 3D 打印技术与传统工艺加工方法区别很大,有着极高的材料利用率,相比传统的成形加工方法有着极大的优势,能够将初始设计、工艺验证与生产制造紧密结合,可快速实现小规模产品创新,缩短研发时间。而本单位近几年在科研新品试制任务与日俱增,现有制造技术很难满足其周期和质量要求。本文将以钛合金薄壁筒类的壳体零件为例,对 3D 打印成型和后续机械加工进行应用探索。
1. 零件工艺分析
1.1 结构特征
壳体是航空飞机救生产品上的重要零件,其三维模型如图 1 所示,零件材料为钛合金,主体结构是薄壁筒类结构,外形壁板、螺杆、进气连接装置是悬臂结构,内筒、螺杆、壁板和进气孔有精度较高的装配需求,其余外圆表面无配合要求。
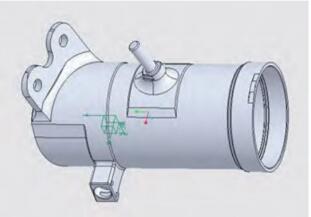
图 1 壳体零件三维模型
1.2 材料分析
壳体零件材料牌号为 Ti6AlV4,具有材料密度小、熔点高、强度高、导热系数小等特点,而且具有较好的机械性能和耐腐蚀性,在航空航天和汽车制造领域得到广泛应用。其详细参数如表1 所示。
表 1 材料成分和物理特性
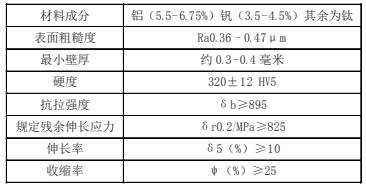
2. 工艺设计
2.1 工艺难点
①零件精度要求较高,为复杂异形件,具有曲面框支撑结构,零件曲面法向缺少支撑,会产生较大变形,需要强支撑以控制变形 ;
②产品强度要求较高,退火不能完全释放内应力,残存较大内应力导致产品变形 ;
③零件外表面不再机加工,需要通过合理摆放及支撑控制生长方向,以控制变形量。
2.2 设备选择
根据工艺要求 ,3D 打印粉末选取的是钛粉Ti6Al4V。打印设备型号 MX400,设备成型空间为400mm×400mm×400mm,能够满足铝合金、钛合金、高温合金、不锈钢等多种金属的增材制造。设备主要包含激光器、扫描振镜、控制系统、监控系统、铺粉和供粉系统等模块。
2.3 三维模型设计
由于 3D 打印设备的加工精度较高,打印工件外型尽可能不留余量加工,但是在有配合要求或者超出设备加工精度的部位可以预留 2mm 余量,另外还要根据后续机械加工装夹方式的需要,添加工艺夹头。
根据设备加工范围和零件尺寸,如图 2 所示可采用多件排版加工能够大幅提升 3D 打印生产
效率。
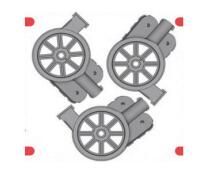
图 2 激光打印排版
根据对零件的主要特征分析,产品属于筒类薄壁类结构,打印摆放需要考虑零件整体圆筒结构尺寸的一致性和变形趋势,以及打印时层层铺粉熔融特点,选择零件竖直摆放是比较科学合理。对零件进行摆放角度确定后,为了减小外形悬臂结构在打印过程中在重力影响下的流体变形,需要在悬臂特征下方增加支撑结构,选择斜面端朝下,兼顾支撑材料最小化,支撑方案如图3 所示。
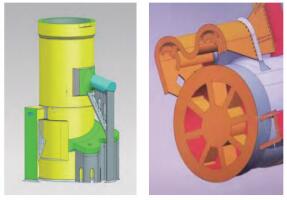
图 3 毛坯余量与支撑设计
3. 打印过程控制
3.1检查基板
在开始打印前,需要确认激光打印区域与排版图一致,打印时基板表面应无渣、氧化物、油污等多余物,如有锈迹可用砂纸进行打磨。基板是打印工件的基准,也是工件的附着载体,材料需与工件材料一致,表面平面度≤ 0.03mm,表面粗糙度≤ Ra0.8,平面度在 0.03mm。
3.2 添加粉末
添加的钛合金粉末之前应进行检查,确保无污染,无结块,无色变。添加前应在烘箱80℃ ±15℃环境下加热不少于 1 小时,并使用指定密度的筛网筛分添加,保证粉末的流动性。添加粉末的体积要大于打印工件体积的两倍,以避免开仓加粉导致设备暂停的情况出现。
3.3 环境确认
设备打印前,需对其运行环境、硬件状况等进行确认 : ①设备工控机硬盘应有足够的存储空间,防止因存储空间不足加工过程中数据的丢失。②惰性气源充足(氩气纯度≥ 99.99%),保证加工过程中建造环境的氧含量稳定。③设备所处空间环境温度保持在 15-30℃之间,湿度小于50%,防止粉末受潮以及器件损坏。④检查水路、电路、防静电装置是否正常。
3.4 3D打印工艺参数设置
先将工件的 “.slc” 格式的实体切片文件导入填充软件中,并对其填充参数激光功率、速度、扫描间距、扫描方式、填充线循环角度、轮廓间距、填充偏置等信息进行设置,如表 2 所示,最后将“.epi” 格式文件存入打印设备中。
表 2 工艺参数
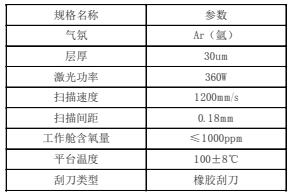
开始打印前应首先将料缸上升 0.3mm,防止因料缸中粉末沉降造成首层供粉量不足的现象 ; 其次可适当增大初始打印供料倍数,保证粉量充足 ; 为保证粉末的利用率,加工 20 层后可逐步调小铺粉倍数,每调节 1 次铺粉倍数观察 2次铺粉情况 ; 最后启动 “开始打印” 按键后,系统自动准备加工环境,待加工条件达标后自动打印。打印过程中操作人员应定时巡查,主要工作包括 : 观察氧含量 <1000ppm,环境温度在 20-35℃之间,湿度 <90,设备铺粉粉面是否平整,工件有无翘曲,粉末是否充足。
3.5 清理工件
工件打印完成后,将成型缸慢慢升起,用毛刷将基板上粉末清扫到落料口下的回收瓶内,卸下基板后用防爆吸尘器清理工件及基板表面浮粉,便于后面检测外观和热处理。需要注意是 :操作人员须戴好防尘口罩、橡胶手套和防护服,及时用防爆吸尘器吸走扬尘。
3.6 检查工件
检查工件外观形态与设计模型的一致性,且工件间无任何粘连 ; 工件、试样、基板结合正常,无开裂,工件及试样任何部位无肉眼可见裂纹 ;工件外观颜色一致、无磕伤、划痕、碰伤等缺陷,且无残留粉末。
4.3D 打印后置处理
3D 打印工件的后处理工序主要包含热处理、去支撑、特种检查、吹砂及后续加工等。根据钛合金沉积态和热处理后的残余应力研究资料表明,经退火热处理后,打印工件的残余应力能够明显降低,且分布均匀。如果金属粉末不够干燥或者吸附空气杂质,在打印过程中还会存在氩气泡,将导致工件内部产生孔隙,形状呈细小球形,经热等静压处理后,内部孔隙会有所减小,但对材料力学性能影响不大。
4.1 热处理
工件在检查外观后,一般应在 24h 内进行去应力热处理。在实际热处理过程中选用电加热炉进行热处理,热处理时带着基板一起,为了控温精准,可在热处理过程中安放了负载热电偶,保证温度均匀一致性,用于监控工件实际温度,具体参数见图 4。
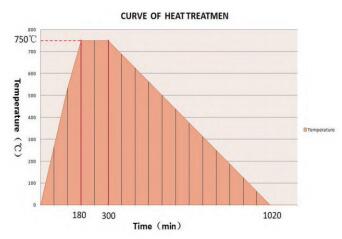
图 4 温度控制曲线
4.2 去支撑
工件热处理后可使用线切割设备切掉基板,再安排钳工去除辅助支撑架。由于大部分支撑结构为薄壁或者桁架细条状组成,可以使用钳子等工具进行拆除。连接处如有毛边等残留,可以风枪、砂纸等工具进行修整和打磨抛光。
4.3 特种检验
由于钛合金 3D 打印加工特点,工件内部会产生微气孔、未融合、裂纹等缺陷,因此在机械加工前要进行荧光、X 光、超声波检查,确保打印毛坯无缺陷。同时需要对毛坯强度和化学成分通过试件进行检验,确保强度和材料成分合格。
4.4 喷砂
零件 3D 打印后表面存在粗糙度不均匀、热处理后存在氧化膜、线切割后存在油污等现象,因此需选用喷砂工艺来提高工件表面粗糙度,使工件表面露出均匀一致的金属色,提升工件外观。
4.5 机械加工
依据机械加工艺方案加工内孔时,使用自制三爪卡盘将整个外圆夹紧,从一端使用粗精镗内孔时,由于深度较大、镗刀悬伸长,加工过程中会产生振动,导致内孔尾部表面粗糙度差,取下工件后内孔还会叠加变形。在粗精加工外形时采用芯轴工装,能定位装夹能到矫正作用,但是加工完取下工件时,内孔没有支撑导致变形 ; 另外去除 3D 打印加厚夹头也会产生应力释放,导致工件变形。为了解决机械加工完后工件多项尺寸超差、报废现象,制定解决措施如下 :
①车削内孔粗精加工分开,调整余量分配,消除变形量。内孔预留 1mm 余量,加工至尺寸¢81H8,作为芯轴定位基准。
②设计车削膨胀芯轴代替三爪卡盘夹紧,消除夹紧力的影响。工步 1 以密封槽端内孔为基准使用膨胀芯轴定位装夹,加工 M84×1 内螺纹和¢ 82H8 内孔 ; 工步 2 以¢ 82H8 内孔为基准定位以及用 M84×1 内螺纹夹紧,加工右端内孔和密封槽。
③将精车内孔调整到数铣外型后面,消除再次装夹加工带来的变形,通过预测变形,改变数铣走刀路径,切削层加工策略由深度优先,调成深度优先,减小变形。
④采用¢ 32 内冷减震刀杆,以及加车刀刀尖半径 0.4,刀具前角 5°,后角 15°,可有效消除过程震动,提高刀具寿命。
⑤通过优化切削参数,调整切削线速度,主动避开震动区间。采用较低的线速度、大切深、小切宽或大切深、大切宽的加工参数,此时的切屑形成效果好,材料去除率较高。
⑥优化 3D 打印毛坯余量,使余量均匀分布,减少内部应力产生。
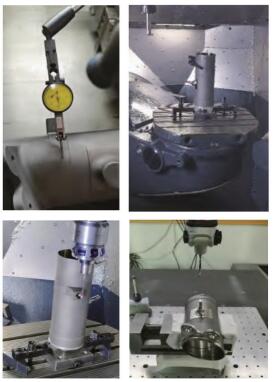
图 5 机械加工过程
5. 结束语
通过 3D 打印技术在钛合金薄壁零件制造工艺中的应用实践,积累了基于增材制造工艺经验,为后续类似零件的加工提供借鉴方法。3D 打印制造具有周期短、精度高、零件近净成形等特点,能够让新产品设计摆脱传统制造工艺限制,实现产品结构功能一体化、轻量化、集成化,以及快速更新迭代,从而降低科研成本。
投稿箱:
如果您有机床行业、企业相关新闻稿件发表,或进行资讯合作,欢迎联系本网编辑部, 邮箱:skjcsc@vip.sina.com
如果您有机床行业、企业相关新闻稿件发表,或进行资讯合作,欢迎联系本网编辑部, 邮箱:skjcsc@vip.sina.com
更多相关信息