小批量汽车冲压模具技术的研究及应用
2023-6-29 来源:中国第一汽车集团有限公司 作者:马望 闫彦
随着社会不断发展,人们的生活方式也在发生着改变,一成不变的生活节奏已不能满足人们的日常需求,私人定制的个性化生活已经开始被越来越多的人所接受。据统计,美国有 85% 的汽车消费者会选择定制化汽车,而日本也有将近80% 的消费者会选择个性化汽车定制。
汽车定制化可大致分为 3 个级别 : 第一个级别就是简单的对车身颜色、轮辋样式及内饰选材等方面进行固有化的装配 ; 第二个级别为大规模定制化,就是汽车供应商进行模块化生产,用户可以根据个人需求对车辆的动力及车身材料等进行自主选择 ; 第三个级别为分散个性化生产,这是汽车定制服务的最高级别,其抛弃了流水线和模块化生产的固有模式,可完全按照用户的需求进行个性化生产,比如劳斯莱斯车型,就是完全按照用户的需求进行装配,真正做到了纯手工定制化生产,并保证每台劳斯莱斯车型都是独一无二的。
我们依据以上几种定制化级别,应用到汽车车身外观,就是对车身冲压件的变更。传统的冲压模具开发周期长、成本高,已不适合开发周期短、批量相对较小的定制化生产的开发特性,这就需要寻求一种适应多产品、小批量的冲压模具技术及标准。根据以上思路,我们参照汽车产量的不同,结合不同的模具开发模式,细化研究小批量汽车的模具生产方式,不仅起到了降低生产成本和提高产品质量的目的,也促进了定制化汽车的应用。
一、基于小批量技术研究
1.规划与工艺
小批量模具根据生产总纲领,可大致分为试制工装(如图 1 所示)、半工装(节约修冲模具)、全工装模具(如图 2 所示)等,半工装模具根据产量的不同,又可对模具结构进行不同等级的划分,达到节约工装成本的目的。
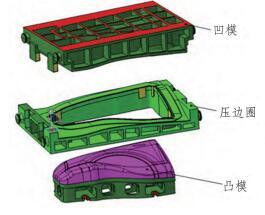
图 1 试制工装
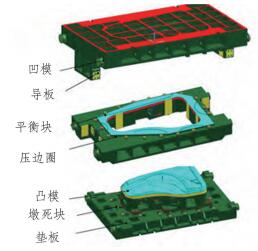
图 2 全工装
首先,确认半工装与全工装模具的平衡点。根据实际生产经验,车型总生产钢领在 5000 台份以上,建议采用全工装批量模具的开发方式 ;对于总纲领低于 5000 台份,根据车型的实际规划钢领,进一步进行分解,对于总纲领低于 100台的,建议采用纯试制工艺及试制工装的形式的进行模具设计制造 ; 总纲领在 100-5000 台之间,建议按照量产工艺进行模具设计制造,而此纲领区间的模具结构及工装形式,根据零件的复杂程度和重要程度进行差异化区分,采用半工装与全工装相结合的方式,而且模具结构在大批量模具的基础上进行减配优化。
将以上讨论进行整理,详见表 1:
表 1 车型规划与工艺工装关系表
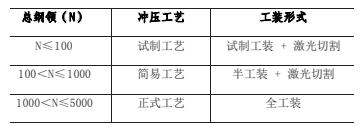
2.模具技术标准
综合考虑产品的重要程度和难易程度,可分为三大类 : 外覆盖件、高强钢零件和其它零件。外覆盖零件表面质量要求较高,工艺设计和模具结构尽可能分析充分,从而保证产品质量,将返修工时控制在合理范围之内。高强钢零件因其屈服强度较高,材料成型时的流动会导致模具磨损严重,因此批量大的话,要适当提高工作部位材质强度,必要时需要对模具局部进行淬火。其它零件可依据行业标准进行设计开发。
(1)模具材质
一般分为铸造模具及钢板模具,铸造模具需要制作泡沫实型,然后铁水浇铸而成,钢板模具是在采购型材的基础上进行加工。铸造模具的模座选用材料为 HT300,钢板模座选用材料为 45钢。对于模具工作部位的材质,试制模具因批量小,一般材料采用 HT300 和 45 钢,若生产纲领较大,需要提升模具材质,一般材料选用 MoCr铸铁或 Cr12MoV。
(2)导向结构
模具导向方式大致分为导板或导柱两种方式(见图 3),批量较小的模具利用模具本体加工面进行导向,不需要安装导板或导柱等导向。批量较大的车型可根据实际情况增加导板或导柱。通常根据零件的重要程度和复杂程度去判断是否增加导向,其目的是保证零件尺寸的稳定性和一致性。
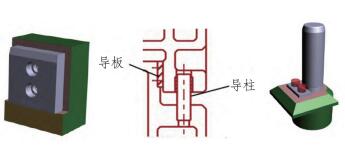
图 3 导板导柱示意图
(3)侧翻结构(CAM)
侧翻结构可分为斜楔翻边和侧翻机构翻边。侧翻机构较为简单,在小批量模具中,负角翻边的零件通常采用侧翻机构。侧翻机构与传统的批量模具的斜楔结构不同(见图 4),它一般实现水平方向翻边,导向面与工作台平行。用斜楔机构翻边的时候,要将零件旋转到合理的角度,以满足斜楔翻边需求,尽量避免成型类翻边。
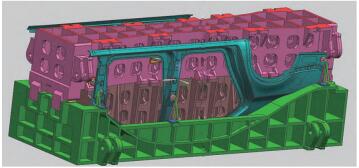
图 4 侧翻机构
(4)加强筋参数
正常量产模具对寿命、强度要求较高,因此型面、主筋、副筋参数较大。小批量模具因其生产数量少,模具寿命要求没有批量模具那么高,因此降低模具结构参数标准是可行的。
综合以上因素,总结归类具体参数,模具技术标准详见表 2。
表 2 模具技术标准表
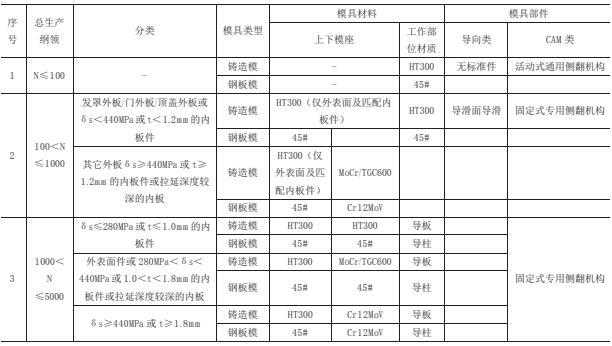
3.支架 / 胎具的激光切割技术
小批量零件在生产规划时,修边冲孔多数采用激光切割加工工艺,应用定位支架 / 胎具的结构来实现切割时的定位。为规避以往的激光切割定位支架 / 胎具重复定位精度低、制作效率低、成本高、不易存放等缺点,可以从设计技术、结构开发、制作工艺三方面来进行优化。
(1)设计技术
①基准统一。定位工装对零件的定位基准
要与零件的 RPS(定位点系统)文件保持一致。RPS 文件中标明了零件的定位孔和定位面,在整车的加工制造、检测及模具、检具、夹具设计制造中都应按照 RPS 文件确定的定位系统确定基准点,因此在激光切割定位设计时也要遵循这个标准,保持定位系统的一致性(如图 5 所示)。
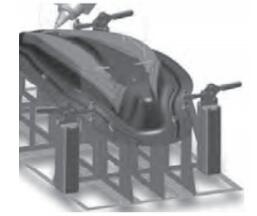
图 5 激光切割支架示意图
②回弹校型。由于车身钣金件型面比较平缓,局部强度低,尤其是外覆盖件,零件本身形状固化强度不足,冲压完成后,零件型面或多或少会出现回弹或塌陷问题。为保证零件在切割过程中与检测和装配状态下一致,需在零件切割部位增加局部回弹校型结构。
③支撑面选取原则。支撑截面应考虑定位的稳定可靠,以及支架 / 胎具的钢性和强度。选取原则是尽量靠近工序件的边缘、避免和修边线重叠或靠近、避免选取在过度圆弧区域等(如图 6所示)。
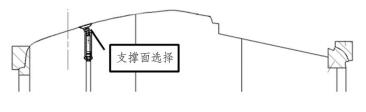
图 6 支撑面选择
(2)结构开发
激光切割定位支架 / 胎具采用薄钢材插装结构(如图 7 所示), 薄钢材厚度为 1.5mm,材料为 Q235。断面上以 50mm 为增量 , 每隔100--200mm 设计一个插脚,底板上也相应地设计插槽。整个结构先进、合理、紧凑。对于型面特殊的大型定位支架 / 胎具可以考虑设计若干个卡板来增强支架的强度和刚性。
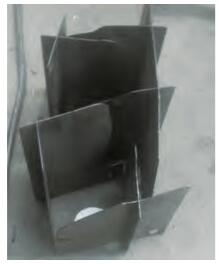
图 7 激光切割插装结构图
(3)制作工艺
激光切割定位支架 / 胎具完全采用 CAD/CAM 一体化制造技术,使得复杂的三维零件定位问题转化成了较简单的二维数控编程问题,降低技术门槛。整个加工可实现单工序加工,使用激光切割机就可以完成全部的加工。激光切割支架三维图如图 8 所示。
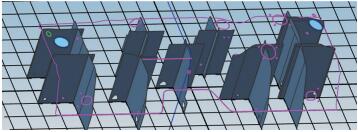
图 8 激光切割支架三维图示
二、典型件示例
以某车型侧围外板零件的生产工艺为例,介绍上述标准的应用。侧围外板总纲领为 200台,采用试制工艺,规划八工序,一序板料处理,用激光切割对板料进行成形前预处理 ;二序拉延成形,用简易拉延模具对板料进行成形压件 ; 三序激光加工,采用激光切割支架定位,对拉延工序件进行初修 ; 四序手工处理,使用通用垫铁对工序件指定区域折弯 ; 五序翻边整形,用简易模具对折弯工序件进行翻边整形处理 ; 六序翻边,使用专用翻边机构对工序件摆放特定角度进行翻边处理 ; 七序激光加工,采用激光切割支架对工序件进行精修 ; 八序手工处理,对前序翻边工艺豁口进行补焊修复处理。简易模具材质采用 HT300,局部工作部分进行表面处理,此案例选用本技术标准即可满足车型纲领规划,又可减少生产准备周期,同时能达到降低工装成本的要求。工序简图详见图 9。
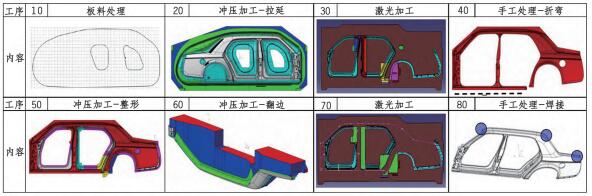
图 9 侧围外板工序简图
三、结论
本文通过对多款小批量汽车冲压模具的研究,得出适用于总纲领小于 5000 辆份的模具技术标准,按此标准既能体现传统冲压生产的经济性,又保证了产品的质量及稳定性,对汽车定制化的模具开发模式起到指导作用。
投稿箱:
如果您有机床行业、企业相关新闻稿件发表,或进行资讯合作,欢迎联系本网编辑部, 邮箱:skjcsc@vip.sina.com
如果您有机床行业、企业相关新闻稿件发表,或进行资讯合作,欢迎联系本网编辑部, 邮箱:skjcsc@vip.sina.com
更多相关信息