工具摇动对超声波加工微孔深径比的影响
2020-8-13 来源:大连理工大学机械工程学院 作者:雷森旺 周凯 余祖元 李剑中
摘要:微细超声加工深孔时会出现加工速度太小或加工力过大的现象,导致深孔加工无法继续。 为此采用辅助工具摇动的方法进行微细超声微孔加工实验,成功加工出直径约为 92 μm、深径比大于 10 的微孔,且加工效率明显提高。 同时研究了工具摇动对加工效果的影响。
关键词:工具摇动;微细超声加工:深孔
随着科技的不断发展,航空、医疗、精密仪器等行业对微细零件的需求量与日俱增,在涌现出的诸如微细电火花加工、微细电化学加工、激光加工及微细超声波加工等特种加工方法中,超声波加工通过磨粒冲击脆硬性材料, 可加工导电或非导电材料,且不受材料导热性的影响,能够加工出高深径比和复杂三维型腔的零件[1]。
在前人对微细超声波加工的研究中,有通过数学建模对工具磨损进行预测[2],有对材料去除模式即对塑性和脆性去除进行探索[3],也有对加工质量、精度影响因素的探究[4],但对微细超声加工深孔的研究文献很少。
安成明等在影响微细超声加工效率的加工参数研究中发现,以加工力反馈控制的恒力进给加工时,加工效率会随着孔深度的增加而逐渐降低,认为其原因可能是:当孔越深时,加工区域与外界磨粒之间的交换过程越困难,从而降低了材料去除率[5]。 Tateishi 等在用传统微细超声加工单晶硅上的深孔时,证明了加工开始产生的边缘缺陷并非由于加工深度大而造成的,且认为无法加工深孔的
原因是:在恒速加工时,加工深度增加,孔底部无磨粒进入,导致磨粒无法得到交换,且加工力随着工具向下进给而增大,甚至会使工具折断而导致加工无法继续。
基于此,Tateishi 等利用电流变流体辅助超声加工方法,成功地加工出直径为 100 μm、深径比为 10 的孔[6]。 王丹等采用五因素五水平正交试验方法,分析了不同加工参数对微晶云母陶瓷的微细超声加工工具体积损耗率的影响,并选择较优的参数组合在微晶云母陶瓷片上加工出直径为 80 μm、深度为 530 μm、 孔侧壁锥度小于 0.5°的深通孔,其深径比为 6.625,但加工时间较长,达 4.5 h[7]。
在电火花加工模具实践中,通过电极摇动可减少切屑在放电间隙的堆积,从而避免了加工过程中的短路和拉弧[8]。 余祖元等用微细电火花辅助电极摇动的方法在不锈钢上成功加工出深径比为 18 的微孔[9],并认为利用工具摇动可增加加工屑的活动空间,便于排除加工屑,从而既能提高深径比,还能提高加工效率和精度。 此外,通过设计不同的工具摇动轨迹,可加工出不同形状的孔。
然而,在用微细超声加工深孔时会出现加工速度减小[5]或工具折断[6]等现象,造成深孔加工无法进行。 对此,本文提出一种结合工具摇动的微细超声加工方法。 在进行深孔加工过程中,当工具进给到一定深度后,工具摇动增加了空间,便于排除加工屑,促进加工区域的磨粒更新,从而达到提高微细孔加工效率和深径比的目的。
1 、实验准备
1.1 实验设备
图 1 是微细超声立式加工装置的示意图。 该装置包括微细工具电火花制备模块、精密伺服进给模块、微细超声加工模块及加工力监测模块,其实物照片见图 2。
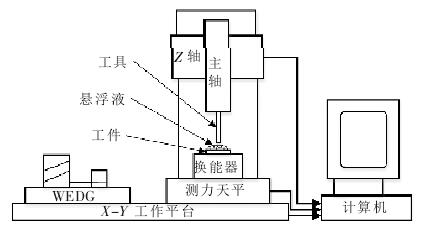
图 1 微细超声加工装置结构示意图
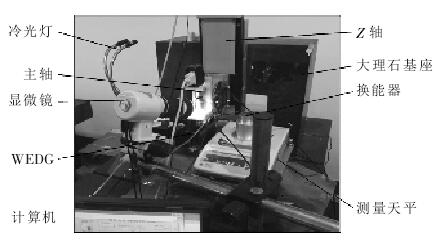
图 2 微细超声加工装置实物图
微细工具电火花制备模块由 RC 脉冲电源、放电状态检测和 WEDG[10]走丝机构组成,主要用于微细工具的在线制备。 精密伺服进给模块采用高精度运动平台,其定位精度为 1 μm,精密旋转主轴的径向跳动小于 1 μm,最高转速达 40 000 r/min。 微细超声加工模块主要由超声波发生器、 超声波换能器、加工力状态监测装置及磨粒悬浮液组成,其中,超声波发生器的振动频率约为 35 k Hz,振幅可调节范围为 0.3~3 μm;加工力监测装置采用称重范围为1100 g、感量为 0.001 g 的精密电子天平对加工力进行实时测量;磨粒悬浮液由金刚石粉末与去离子水按一定质量比配制而成。
1.2 实验条件
实验采用恒力加工、工件振动[11]的方式进行,实验条件见表 1。 实验过程中,每一个摇动半径对应一系列的摇动速度, 当摇动半径和摇动速度均为 0时,即工具不摇动;振幅通过调节超声波发生器的输入电压大小进行控制;悬浮液由金刚石磨粒和去离子水配制而成,其质量分数为 3%。
表 1 实验条件
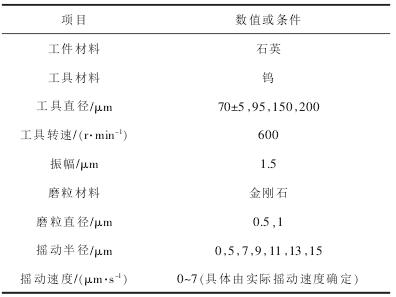
本实验为圆孔加工,工具的摇动运动示意见图3。通过 X-Y 双轴联动实现圆形摇动轨迹,即工具在转动进给的同时,沿着圆形摇动轨迹运动。
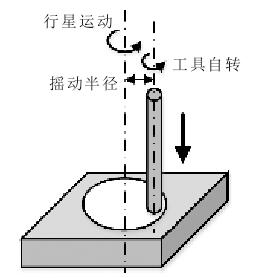
图 3 工具摇动运动示意图
1.3 实验方法
将大小合适的石英片通过强力双面胶粘在换能器振动头上,并在石英片上滴加悬浮液。 工具的磨损长度通过加工前后对工件上同一点进行探测的 Z 轴坐标之差得到,测量的加载力值为 0.01 g,
其计算示意见图 4。 为保证测量值的准确性,加工前后采用多次探测并取其平均值。
本文设置加工力的最大值为 3 g。 在实验过程中,通过改变进给速度保持加工力在一定范围内波动(恒力加工)。
图 5、图 6 分别是正常加工和无法继续加工的力信号曲线。 当加工无法继续时,工具与孔底部之间的磨粒较少或没有磨粒,工具将直接撞击工件,导致力信号曲线波动剧烈,同时也没有产生正常去除材料的力信号(图 5 所示虚线框中的曲线)。 当进给速度小于 0.2 μm/s 且力信号曲线波动迅速时则停止加工,此时的进给深度作为最终进给深度,再减去工具磨损量,即可得到加工孔的深度。
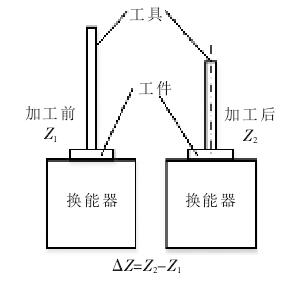
图 4 工具磨损计算示意图
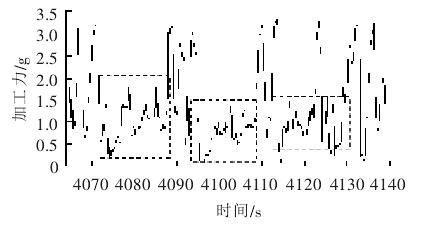
图 5 正常加工时的力信号曲线
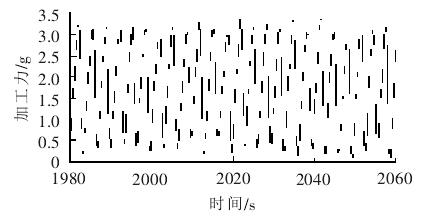
图 6 无法继续加工时的力信号曲线
2 、实验结果及分析
2.1 无工具摇动加工实验
在进行无工具摇动微细超声深孔加工实验时,记录工具进给一定深度所用的时间,以验证文献[5]中的现象是否为共性。 如表 2 所示,1#~6# 是无工具摇动时各孔的加工参数。 在实验中发现
,未使用工具摇动进行深孔加工时, 达到一定进给深度后,工具只能以很小的速度向下进给,耗时长。
根据实验数据绘制进给深度与加工时间的关系曲线, 由图 7可见,当工具进给到一定深度后,其进给速度会逐渐减小,即加工速度减慢,加工效率降低,与文献[5]描述的一致, 其中 1# 工具所对应的曲线的减小趋势最明显。
此外,4# 工具加工的孔,其深径比最大,为 6.38,孔径为 107.7 μm;但耗时较长,约 49 min。
表2 各孔的加工参数
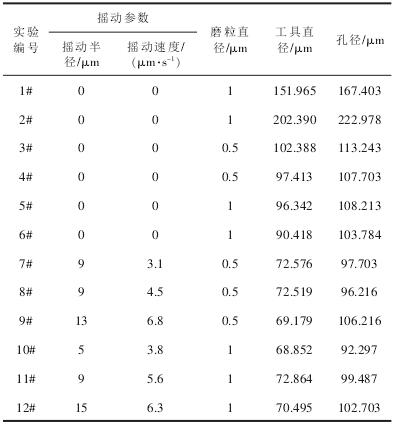
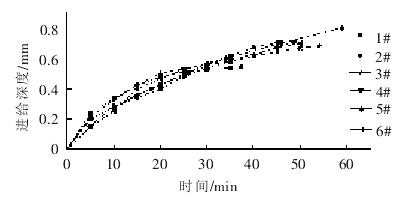
图 7 无工具摇动加工时的进给深度与加工时间的关系曲线
2.2 工具摇动加工实验
以 100 μm 作为微孔的目标直径进行工具摇动微细超声深孔加工实验,并与无工具摇动加工进行比较(以 6# 工具为代表)。
表 2 所示 7#~12# 是工具摇动时各孔的加工参数,根据实验数据绘制进给深度与加工时间的关系曲线,对比 6# 工具可发现,使用工具摇动加工时,达到一定进给深度后,工具仍能以较大的速度进给, 且加工力波动在设定范围内,用时也较短。 如图 9 所示,10# 工具加工的微孔直径约为 92 μm,深径比为 10.1,耗时 25 min。
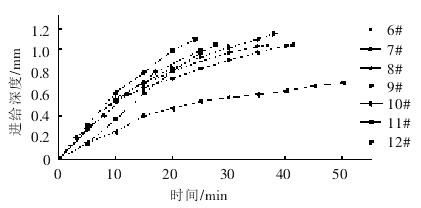
图 8 工具摇动加工时的进给深度与加工时间的关系曲线
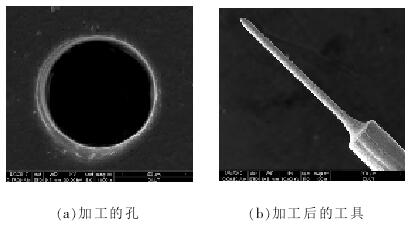
图 9 深径比为 10.1 的孔及加工后的工具
2.2.1 工具摇动对深径比的影响
图 10 是工具摇动加工微孔和无摇动加工微孔的深径比。 分析可知,1#、2# 工具的直径较大,分别为 152、202 μm, 所加工孔的深径比最小;3#~5# 工具的直径均为 100±5 μm,6# 工具的直径为 90 μm,所加工孔的深径比均在 6~7 之间;7#~12# 工具的直径为 70±5 μm,且采用摇动加工后,存在摇动半径,所加工孔的深径比均大于 9。 因此,使用工具摇动进行微孔加工,可使孔的深径比有较大的提高。
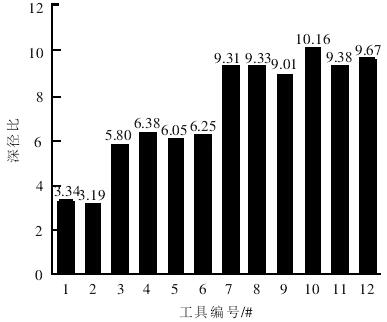
图10 工具摇动对孔的深径比的影响
2.2.2 工具摇动对加工效率的影响
由图 8 可知,使用工具摇动进行加工,在提高孔的深径比的同时,还缩短了加工时间,提高了加工效率。 由于工件材料去除率反映了微孔直径、加工深度、工具损耗和加工时间等情况,因此能综合反映出超声微孔加工效率和综合性能。 本文通过计算各孔的材料去除率来对比加工效率。 材料去除率vw的计算公式为:
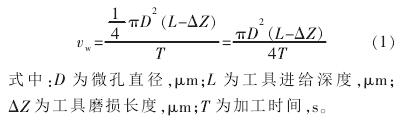
由图 11 可见,1#、2# 工具加工的材料去除率较大,主要是由于工具直径较大,故加工能力强;3#--6# 工具的直径相差不大 , 故材料去除率差别也较小; 在使用工具摇动加工后,7#~12#
工具加工的材料去除率均有所提高, 其提高程度与摇动参数有关。
为了探究工具摇动参数对材料去除率的影响,在相同的摇动半径下,选用不同的摇动速度进行超声微孔加工实验,并取相同的进给深度为 1.05 mm,工具直径为 71±3 μm,其他实验条件同表
1。
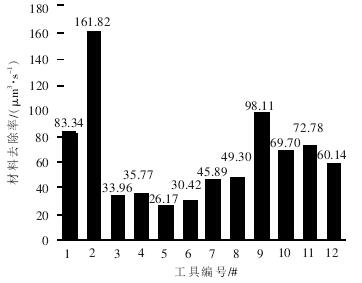
图 11 工具摇动对孔的材料去除率的影响
由图 12 可看出,当工具摇动半径一定时,材料去除率随着摇动速度的增加而增大。 分析原因:摇动速度增加时,处于工具端部下方的加工区域移动速度加快,孔底部的材料更快地被去除,从而提高了材料去除率;同时,工具与加工孔侧壁间的悬浮液流动加快, 促进加工屑的排出和孔底磨粒的交换。
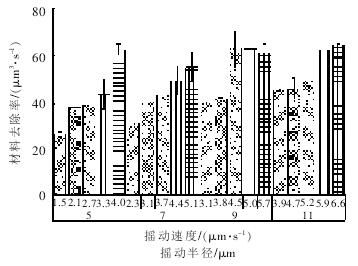
图 12 材料去除率随工具摇动速度的变化(粒径 1 μm)
另外,摇动半径为 9 μm 时,材料去除率先增大、后减小,这可能是由于随着摇动速度增加到一定值并超过了该加工条件下的加工能力后,加工效率随之降低。
由图 13 可看出,材料去除率均随着摇动速度的增加呈先增大、后减小的规律。 这可能是由于使用直径为 0.5 μm 的磨粒时,加工能力减小,随着摇动速度增加,更快地达到加工能力的最大值。
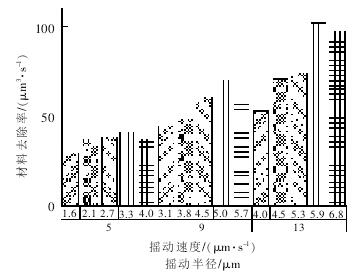
图 13 材料去除率随工具摇动速度的变化(粒径 0.5 μm)
由于实际摇动速度与给定摇动速度存在很大差异,故未进行相同摇动速度、不同摇动半径下的加工实验,但对此种情况下的材料去除率做了如下猜测:随着工具摇动半径的增加,去除的材料体积将增多,材料去除率随之会减小;当摇动半径增加后,工具与孔侧壁间的距离将增大,便于加工屑的排出和孔底部磨粒的交换,这会促使材料去除率增大。
由于上述两个原因,材料去除率可能随着工具摇动半径的变化而不呈现出明显的规律。
2.2.3 工具摇动对工具磨损的影响
在微细超声加工过程中, 特别是长时间加工,工具磨损较严重。 工具磨损与加工时间、工具直径、磨粒大小、静压力、振幅等有直接关系[12]。 本实验中,加工深孔的时间较长, 对工具磨损的影响较大;同时使用了工具摇动, 其对工具磨损的影响尚不明确。 在实际生产中,衡量工具是否耐磨损,不只考虑工具磨损速度,还要考虑相应的加工速度,故采用工具相对磨损率作为衡量工具耐磨损的指标。对上述实验中不同工具的相对磨损率进行了比较,工具相对磨损率 θ 可表示为:
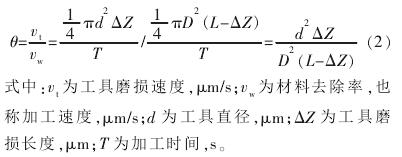
图 14 是工具 1#~12# 的相对磨损率。 可见,使用工具摇动后,工具磨损加快。 分析原因:工具摇动促进了加工屑的排出和孔底部磨粒的交换,同时加快对工件和工具材料的去除,导致工具磨损增大。
2.2.4 工具摇动对加工间隙的影响
在超声加工微孔过程中,加工区域与外界磨粒会随着悬浮液的流动进行交换,且高速运动的磨粒对侧壁也会造成很大的冲击,因此孔的尺寸相比于工具尺寸有所增大,在孔壁与工具之间会形成加工间隙,间隙的大小将影响所加工孔的尺寸。
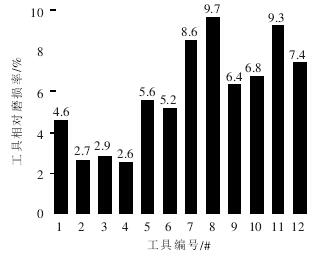
图 14 工具摇动对工具相对磨损率的影响
通过对上述实验中单边加工间隙的计算和比较,分别得出了无工具摇动和工具摇动时的单边加工间隙 Dg的表达式:
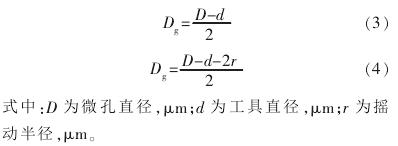
图 15 是不同的工具加工孔的单边加工间隙。由 7#~12# 对应的工具摇动后的实验数据可见,单边加工间隙有减小的趋势。 分析原因:当工具摇动后,磨粒与外界的交换通道加大,对孔侧壁的冲击作用减小,故加工间隙减小。
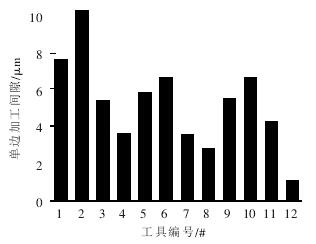
图 15 工具摇动对单边加工间隙的影响
4 、结束语
本文提出了辅助工具摇动的微细超声深孔加工方法。 通过工作平台 X-Y 轴的联动进行圆周运动,实现圆形摇动轨迹,结合传统微细超声加工,成功加工出深径比为10 的微孔, 且加工效率明显提高。
在研究摇动参数对加工效率的影响时,发现材料去除率会随着摇动速度的增加而增大,有时摇动速度增加到一定程度后会使材料去除率减小,并猜测摇动半径变化对材料去除率的影响无明显规律。同时,使用工具摇动进行微孔加工时,会使工具磨损增加,而加工间隙减小。
投稿箱:
如果您有机床行业、企业相关新闻稿件发表,或进行资讯合作,欢迎联系本网编辑部, 邮箱:skjcsc@vip.sina.com
如果您有机床行业、企业相关新闻稿件发表,或进行资讯合作,欢迎联系本网编辑部, 邮箱:skjcsc@vip.sina.com
更多相关信息