机体顶面螺纹孔多工位全自动加工设备的研制
2020-5-18 来源: 一拖( 洛阳) 开创装备科技有限公司 作者:周瑞婷
摘要: 介绍了用于完成发动机机体顶面螺栓孔螺纹加工的多工位全自动机床的设计思路。以简约、高效、低成本为主要设计原则,通过合理设计机床整体布局和功能部件,研制出了完全符合工艺要求,满足用户需求的机床。
关键词: 发动机机体; 螺栓孔; 螺纹加工; 多工位全自动; 整体式移位滑台
柴油机机体顶面螺栓孔的攻丝工序为其加工的典型工序,由于孔的数量太多,且孔的分布的规律性极强,一般情况下不会因为品种更新而改变此类孔的坐标及大小,所以非常适合采用专机加工所有的顶面螺栓孔。
对于大型柴油机机体,其顶面螺栓孔的直径较大,所以需要采用较粗的主轴加工,而由于其数量多,且孔距较近,所以很难利用一台专机的一个主轴箱,完成所有的顶面螺栓孔的加工。如图 1所示为八缸机体顶面螺栓孔,图 2 为六缸顶面螺栓孔,图 3 为机体顶面螺栓孔局部剖视图。一般采用多台机床,每台机床加工其中一部分孔的方式完成加工,但是由于大部分用户投资的资金有限,很难投资多台机床进行此工序的加工,所以我们有必要研发一台专用机床来完成所有顶面螺栓孔的加工,以提高我公司此类产品的市场竞争力。
此台机床就是我们为客户研发制造的一台立式单面四工位攻丝专用机床。此项目能在一台机床上分工位完成八缸机体( 见图 1) 缸孔周围( 共48 个孔) ,六缸机体( 见图 2 ) 缸孔周围( 共 38 个孔) 的顶面螺栓孔的加工。
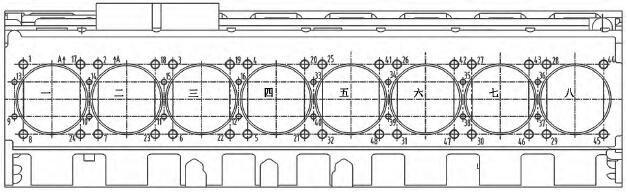
图 1 八缸机体顶面视图
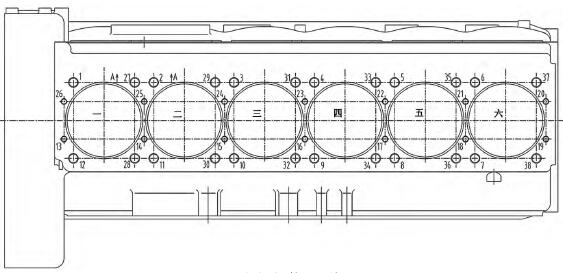
图 2 六缸机体顶面视图
1 、机床概述
1. 1 机床主要部件及布置形式
如图 4 所示,机床采用立式单面四工位布置形式,机床的基础部件为一个整体式移位滑台,移位滑台上安装有一套夹具,移位滑台后部连接着一个立柱底座,立柱底座上面安装有一个立柱,立柱上安装有一个 HY63 液压滑台,液压滑台上面安装有一个 TD63 动力箱,动力箱上安装有一个主轴箱,主轴箱前部的主轴上安装有刀辅具。在中间底座沿上下料方向的两端,分别安装有上料装置和下料装置,用以实现工件的四工位的移位动作,以及工件的自动上下料动作。
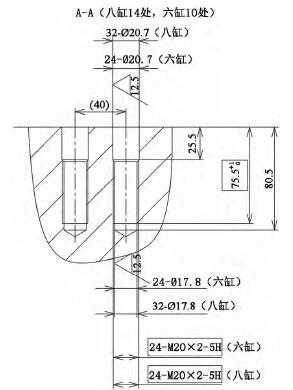
图 3 机体顶面螺孔剖视图
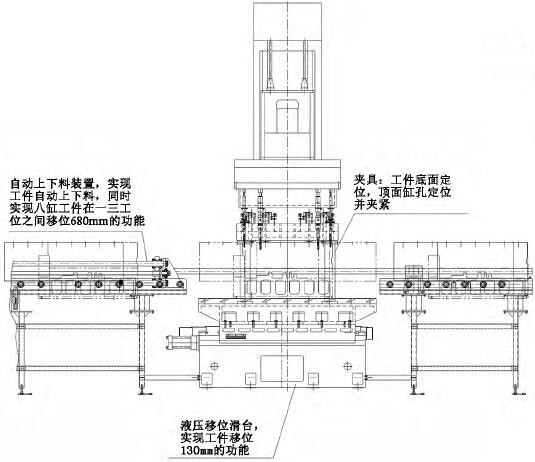
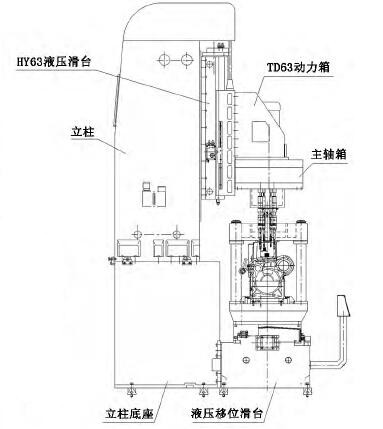
图 4 机床主视图与侧视图
机床采用干式加工,配有自动润滑丝锥的煤油冷却装置。
1. 2 机床动作循环
人工吊装工件到上料辊道上,摆杆输送装置将工件输送到夹具内,利用两个缸孔插销,同时夹紧,立式滑台向下进行第一工位加工循环; 完成后,移位滑台带动工件移位到第二工位,立式滑台向下进行第二工位加工循环; 完成后,拔销,夹紧放松,摆杆输送装置将工件输送到第三工位,利用两个缸孔插销,同时夹紧,立式滑台向下进行第三工位加工循环; 完成后,移位滑台带动工件移位到第四工位,立式滑台向下进行第四工位加工循环;全部加工完成后,摆杆输送装置将工件输送到机床外下料辊道上。这是八缸的加工循环,六缸只需两个工位就可完成全部螺纹孔的加工。从机床上料到加工完成、下料,全部为自动完成循环。
2、 机床主要创新点
2. 1 多工位加工
利用缸体孔的分布规律,采用多工位加工,完成全部螺栓孔螺纹的加工。
通过分析工件上孔的排布情况,我们发现可以利用缸体上孔的分布规律,见图 1,一号缸孔周围的 1、17、24、8、9、13 六个孔,如果向右平移一个缸孔距 170 mm,则与二号缸孔周围的 2、18、23、7、10、14 六个孔完全重合,后面所有缸孔周围的孔都符合此规律。
于是我们设想,如果采用一个主轴箱将每个缸孔周围的 1,13,9,8 一组四个孔的坐标处设置四根主轴,将此作为一个单元,当这个单元的 1、8号刀具移动到 17、24 位置时,13、9 号位置处的刀具刚好可以藏入一号缸孔中。若干个这种单元的主轴排成一个主轴箱,这样再通过工件移位一定的步距,就可以实现将所有孔在一台机床的一个主轴箱上全部加工。
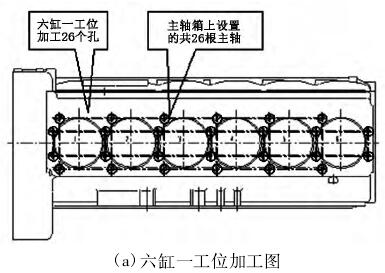
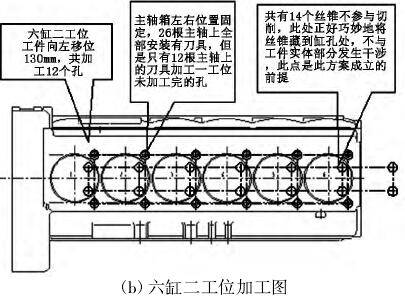
图 5 六缸各工位加工图
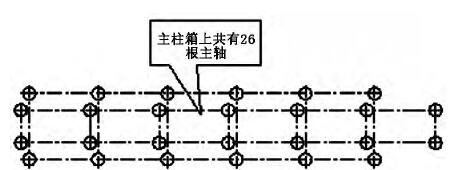
图 6 机床刀具排布图
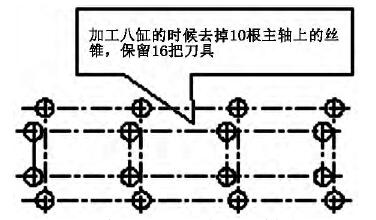
图 7 加工八缸时刀具排布图
六缸各工位加工图如图 5 所示。机床刀具排布图见图 6,加工八缸体时刀具排布图见图 7。八缸各工位加工如图 8 所示。
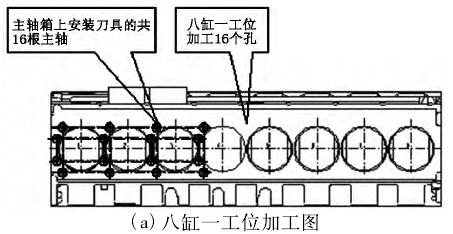
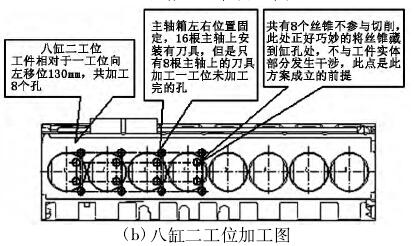
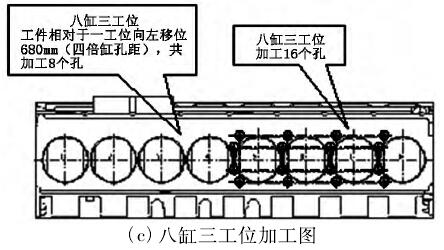
图 8 八缸各工位加工图
2. 2 四工位加工方式
采用液压移位滑台与摆杆输送相结合的方式实现八缸机体的四工位加工。通过综合考虑工件长度、摆臂厚度及维修调整的方便性等各种因素,最终确定了工件的输送步距为 2300 mm。而八缸机体从上料位至一工位,只需要走步距的一部分1620 mm,通过在摆杆输送上增加挡料油缸的方式来实现; 通过液压移位滑台实现工件从一工位到二工位移动,在二工位加工完成后,工件又通过移位滑台从二工位回到一工位。然后,摆杆输送带工件走完剩下的步距,把工件从一工位送到三工位; 再次通过液压移位滑台实现工件从三工位到四工位的移动和加工完成后回归到三工位。最后,摆杆输送带工件走整个步距,将工件从三工位输送到下料位,完成八缸机体的自动上下料,如图9 所示。
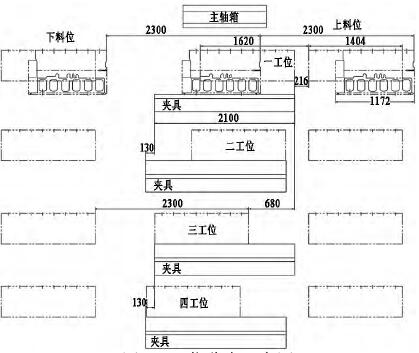
图 9 工位分布示意图
2. 3 攻丝
由于所加工孔在前序加工成的底孔为一个台阶孔,如图 10 所示,沉孔和螺纹孔直径差别很小,单边仅差 0. 35 mm,而螺纹孔的精度要求较高,螺纹要达到一级精度,而且,螺纹孔的位置度及与顶面的垂直度都要求较高。攻丝机构为浮动攻丝,丝锥旋转进给时摆动较大,难免会和沉孔产生干涉,不仅影响工件的品质,还会使丝锥磨损,影响螺纹孔的加工精度。我们采取增加导向衬套粗导向攻丝心杆外圆的方式,限制丝锥摆动的程度。如图 11 所示。
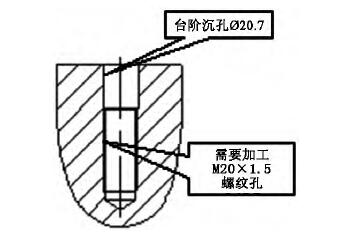
图 10 M20 × 1. 5 螺纹底孔
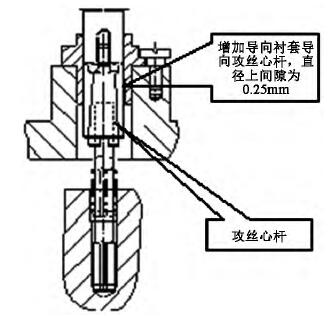
图 11 攻丝时导向情况
2. 4 润滑
此台机床用户要求对丝锥进行润滑,但是又不能采用湿式加工,且不能有大量的润滑煤油流入机床内。针对此种情况,结合机床分工位加工的情况,我们对煤油润滑控制部分进行了创新设计,如图 12 所示,采用八个电磁阀分别控制一部分孔的方案,当加工不同工位时,打开需要的几个电磁阀,采用组合的方式,保证所有工位加工时,只有需要加工的孔处进行润滑,这样最大程度避免了煤油的浪费,也符合绿色环保的理念。
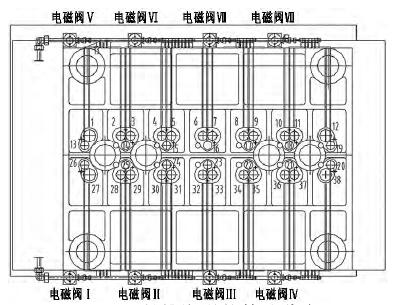
图 12 丝锥润滑的管路分布
3 、结论
此项目已于 2015 年 6 月顺利通过终验收。使用情况良好,获得用户好评。此项目的实施对我公司承接此类柴油机机体顶面攻丝,有非常重大的现实意义,通过此项目,我们针对此类丝孔较密集的工件,多了一种在单台机床加工所有丝孔的工艺手段,且此方式成本较原有方式大大降低了成本,为我们以后承接此类项目打下了坚实的基础。
投稿箱:
如果您有机床行业、企业相关新闻稿件发表,或进行资讯合作,欢迎联系本网编辑部, 邮箱:skjcsc@vip.sina.com
如果您有机床行业、企业相关新闻稿件发表,或进行资讯合作,欢迎联系本网编辑部, 邮箱:skjcsc@vip.sina.com
更多相关信息