发动机缸体加工过程动态SPC 质量控制系统设计
2019-1-2 来源:合肥工业大学机械与汽车工程学院 作者:孙 迪
摘要:针对发动机缸体加工过程质量控制问题,首先分析了发动机缸体加工工艺,并对关键质量控制点进行了阐述;其次,在分析缸体机加工过程实时数据采集流程的基础上,建立了一套动态SPC 控制系统(Dynamic SPC,D_SPC);然后,详细阐述了D_SPC 的硬件架构和软件架构,并介绍了D_SPC 质量控制系统的功能模块。最后,以缸孔孔径的测量为例,说明了该系统可以有效地解决缸体机加工过程的质量控制问题。
关键词:发动机缸体加工;统计过程控制;质量控制系统;实时监控
0 引言
发动机缸体的机加工质量是发动机最终质量的重要保障,其质量的优劣,是衡量一个发动机装配性能和运行可靠性的重要指标[1] 。在缸体制造过程中,产品制造质量管控能够对产品的生产质量起到在线监测、把关、预防、改善的作用。统计过程控制(StatisticalProcess Control,SPC)则为产品的质量分析和控制提供了方法支持[2] 。通过SPC 控制图可及时甄别出生产过程出现的异常趋势,根据不同的判异规则,及时找出异常发生的具体原因并加以排除,保证产品不在有异常的环境下完成生产,从而保证产品质量。由此可见,要想提高发动机缸体加工过程质量,必须提升机加工过程的质量控制水平。
为此,国内外学者从不同角度对制造过程质量监控做了大量研究。综合运用神经网络、统计过程等理论与技术,姜兴宇等[3] 利用一种动态工序质量控制模式用以解决网络化制造环境下工序质量难以控制的问题。ALANEME K K 等[4] 从SPC 动态控制、模糊综合评判和专家知识库等方面综述了质量管理,分析了制造过程中质量异常控制等方面的处理技术。翟敬梅等[5] 提出了一种基于质量统计控制和粗糙集理论的质量集成模型,并发展了一种工序质量诊断模型,用以研究生产参数在工序质量控制过程中的重要性。针对质量诊断过程中出现的不确定、模糊性问题,侯世旺等[6]提出了一种质量推理系统,利用模糊逻辑确定质量诊断过程中质量异常发生的程度。基于标准化样本方差和霍特林模型,赵永满等[7] 提出了一种联合控制图,用于监控质量二元过程中均值向量和协方差的变异。为了让传统的计算机辅助质量系统实现质量过程控制、随业务需求改变而柔性重构的功能,李成等[8] 提出了一种基于工作流程模型的质量系统体系结构。刘春雷等[9] 针对传统质量控制方法在解决小批量生产中的局限性问题,提出了一种工序控制系统,应用于制造过程的质量预防、诊断与分析改进。
上述研究为制造过程质量控制提供了方法和技术支撑。动态制造过程质量控制方法可以很好地解决产品制造过程的质量控制问题,提升产品的质量和生产过程稳定性。复杂产品的制造过程质量控制是质量控制的重点和难点,为此本文以发动机缸体机加工过程质量控制为例,运用动态SPC 质量控制系统来提升其制造过程质量。
1、缸体加工过程及参数分析
发动机缸体作为发动机的关键组成部件,其加工图2 D_SPC 的数据库模型过程由多道工序完成,每道工序具有繁多的质量控制特性需要进行分别控制。缸体在完成粗加工后,依次经过以下操作过程:①缸体产品出生证(唯一编码)打刻,方便后期的质量数据采集、分析和追溯;②缸体清洗,然后进行缸体的油道试漏检测,主要包括压力测试、泄漏量测试等;③曲轴盖螺栓拧紧,控制10 个曲轴盖螺栓的力矩和转角;④缸孔综合测量,主要是对上游工序的综合加工结果进行把关控制,主要包括曲轴孔直径(每个孔取三个截面和两个方向)、曲轴孔圆柱度、缸孔直径(每个孔取三个截面和两个方向)、缸孔圆柱度;⑤缸孔的水道试漏,主要包括压力测试和泄漏量测试。
2、缸体加工过程D_SPC 系统架构
综合考虑发动机缸体加工过程的关键质量特性,为更好地满足其加工过程的质量控制要求,构建了D_SPC 系统架构。如图1 所示,主要分为检测层、数据采集层、服务层3 个部分。
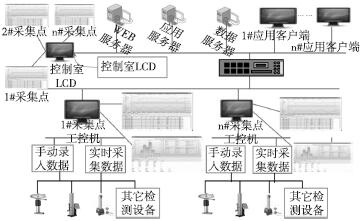
图1 D_SPC 系统架构
D_SPC 系统通过标准化数据接口与设备、生产线、ERP 系统等集成在一起,是上层系统和底层设备间的中间系统。检测层和数据采集层实时采集缸体机加工过程的关键质量数据,并根据设置的判异规则,实时绘制动态SPC 控制图,并通过企业的统一信息服务平台进行发布。在缸体的制造过程中采集的数据主要包括缸体质量特性数据、产品异常信息、纠正与改善信息、分析出的异常信息、检测设备数据信息等。这些信息以手动或自动方式存入不同的数据库中。自动采集的数据输入至D_SPC 系统,自动生成各类控制图,分析产品当前的制造过程是否处于稳定状态;手动录入的数据可以用于后期对生产过程的统计分析和追溯,为生产过程产品的质量改善提供支持。控制室LCD 用于显示各个数据采集点的实时数据分析图,并计算出上控制线、下控制线、CPK(工序能力指数)等。服务器主要由实时数据采集服务器、历史数据服务器和WEB 服务器三部分组成,以此为D_SPC 系统的运行提供支撑。
3、缸体加工过程系统设计
3. 1 D-SPC 的数据库模型
图2 所示为D_SPC 系统的整体数据库结构。主要包括产品_产品清单、工作站清单、质量规范清单、人员_人员基本信息表、人员_部门基本信息表、质量分析设置表、工作站_质量规范关联表、产品_故障类型表、产品_故障类型清单、档案_产品故障与故障原因关联表、档案_故障产品详细信息表、权限_权限基本信息表、工作站_人员关联表。上述数据库模型阐述了各个表之间的对应关系,以及表中的主键和外键约束,为建立规范化的数据模型打下了基础。
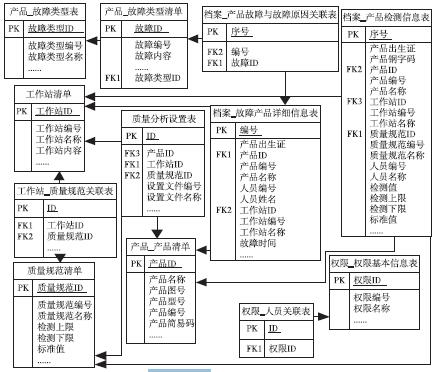
图2 D_SPC 的数据库模型
3. 2 D_SPC 的软件架构
根据上述D_SPC 质量控制体系和数据库模型,本文构建了D_SPC 的软件架构。如图3 所示,主要由底层数据采集、系统总体业务、系统总体功能、企业信息系统数据通信接口、数据处理中心和关键质量信息发布等六部分构成。
底层数据采集模块主要是开发一套生产车间底层控制系统,从PLC、智能仪器仪表和机器设备进行自动数据采集,具备手动数据录入功能。系统总体业务包含建立产品基本信息、定义工作站信息、配置产品对应检测规范信息、系统权限管理、人员基本信息、系统数据采集客户端定义、样本规则定义、判异规则定义、故障原因分析、控制图自定义设置等内容。系统总体功能主要是对产品信息、工作站信息、质量规范信息、权限信息、人员信息、采集数据信息、故障原因信息等进行管理。
企业信息系统数据通信接口主要是通过Webservice、Files、Socket、Message queue 等接口方式, 将MES、ERP、PDM 等系统的关键数据接收至D_SPC 系统,对D_SPC 的使用提供支持,并可以将采集的质量数据、分析结果数据实时上传至上层应用系统。数据处理中心为各个功能模块数据处理提供支持,动态采集的生产过程。实时数据被存入实时数据库,用于生产过程的实时状态监控和控制。历史数据被存入历史数据库,用于对生产过程信息的追溯和统计分析。需要进行网页发布的数据被存入Web 数据库,用于信息的网页发布和多部门间的共享。关键质量信息发布主要是将制造过程中的质量数据和统计分析数据实时向工人或质量管理人员发送,包括各个工序的生产能力指数、返修率、合格率等。
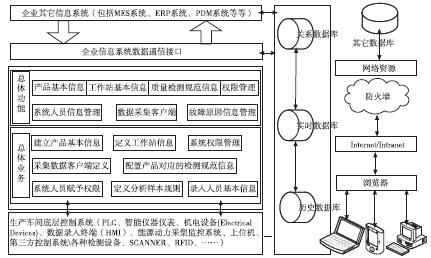
图3 D_SPC 的软件模型
4、应用实例
综合上述分析, 本文基于. NET 平台中, 采用SQL2008 数据库,采用C#语言开发了D_SPC 系统的原型系统,并将该原型系统应用于发动机缸体制造过程中。图4 所示为关键工序SPC 实时监控界面,主要含异常处理按钮、标题区、功能按钮区、原始数据区和控制图区。
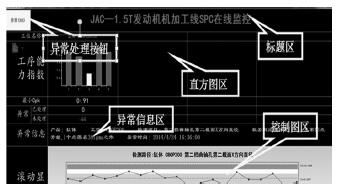
图4 D_SPC 系统在缸体制造过程中的实例
在该监控画面上,可以实时显示关键质量控制点的工序能力指数,异常信息,动态SPC 控制图等信息,管理人员通过办公室的LED 大屏幕就能实时监控生产现场的生产状况。
5、结论
本文构建了一种面向制造过程的动态SPC 质量控制体系,详细阐述了D_SPC 的体系架构、数据库模型、软件架构。该系统能够根据实时制造工况信息对当前在制品的质量进行动态分析,保障了产品的整体制造精度和稳定性。动态对在制品的质量状况分析能及时甄别出制造过程中的异常情况,及时给出预警提示,防止出现批量不合格品,为生产过程的主动质量控制提供了思路和方法。本文构建的系统可推广应用到缸盖加工过程、发动机装配过程、变速箱装配过程等机械产品的制造过程中。
投稿箱:
如果您有机床行业、企业相关新闻稿件发表,或进行资讯合作,欢迎联系本网编辑部, 邮箱:skjcsc@vip.sina.com
如果您有机床行业、企业相关新闻稿件发表,或进行资讯合作,欢迎联系本网编辑部, 邮箱:skjcsc@vip.sina.com
更多相关信息