激光切割技术在船舶制造中的应用现状与发展趋势
2018-6-21 来源:转载 作者: 陈希章,苏传出,程军辉
摘要:激光切割具有切割效率高,切割精度高,热变形小,割缝质量与切口面垂直性好等优点,在钣金、汽车、机械等行业已经得到大量应用,但由于船舶切割自身的特点,激光切割在该行业未能大面积推广。本文总结了激光切割技术的原理与特点,回顾了激光切割技术在船舶制造中的应用现状及存在的问题,重点对现状进行了分析和展望,从性价比、装备柔性化和质量等方面进行了深入分析并提出了应用建议。
关键词:激光切割;船舶制造;应用现状;发展前景
船舶行业是金属焊接和切割的大户,其制造涉及的主要工序之一就是切割和焊接。船舶行业近些年来经历了快速扩张又突然萎缩的过程。
2016 年是船舶工业“十三五”的开局之年,2017年是全球造船业深度调整、我国船舶工业进入全面做强阶段的关键之年。
据中国船舶行业协会统计数据,经过市场调整,船舶行业出现一些新的特点,船舶行业总体经济总量幅度变化不大的情况下利润有一定幅度下滑,在总体订单有所下降的情况下,出口订单有所回升,同时船舶行业产业集中度进一步提升,目前前十名的船舶企业占据市场的53.4%以上。随着市场竞争的激烈、利润的下滑和质量要求的提高,船舶行业对制造质量更加重视,而作为切割大户,激光切割在新形势下进一步迎来爆发的机会。激光切割作为一种高效、绿色、高质量、高精度的技术,是促进船舶工业发展及船舶加工制造优化的基石,对船舶行业实现减量化、轻量化、再制造、降低成本,减少工时以及节能环保等方面发挥重要作用。另外,激光切割工艺还是船舶结构前船板备料的理想手段,顺应目前船舶结构大型化制造精度化,建造高效化的发展趋势。本文针对激光切割技术原理和特点,船舶制造领域激光切割技术的应用现状、存在问题及其应用前景进行论述。
1. 激光切割技术
(1)激光切割原理
激光切割是典型的热切割方法,其通过激光器产生高能量密度的激光束,并利用激光镜组聚焦光束,照射工件,且以连续重复的脉冲作业方式,加热工件材料,使其迅速发生熔化、汽化、烧蚀形成孔洞。同时借助与光束同轴的高速气流吹除切口处熔融废料,完成工件的切割分离。激光切割的原理如图1所示。
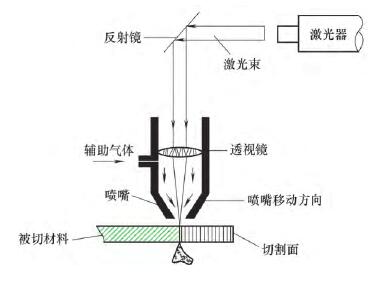
图1 激光切割原理示意
(2)激光切割的特点
第一,切割质量好:激光光斑小、能量密度高、切割速度快、激光切割切口细窄平整,切缝表面光洁美观,表面粗糙度只有几十微米,切割零件的尺寸精度可达±0.05mm,工件变形小,热影响区小,适应性与灵活性高,可作为最后一道加工工序,无需二次加工,减少加工成本。
第二,切割效率高:基于激光的光学特性与传输特性,激光切割可在配有多台数控操作台的激光切割机上实现数控操作。同时,只需修改数控程序,就可实现多形状零件的切割,其中包括二维与三维切割。
第三,非接触式切割,减少工具成本:激光切割时它不像传统切割方式,其割炬不与工件接触,无需更换“刀具”,不存在刀具磨损,加工多厚度或多形状零件,只需改变激光器的激光输出参数即可实现。因此激光切割是一种绿色环保加工手段,激光切割过程噪声小、振动小,不产生污染。
第 四 , 切 割 材 料 种 类 多 ,切割速度快:激光切割材料种类繁多,包括金属、非金属、复合材料、木材等。且激光切割速度快,用功率为4000W的激光切割12mm厚30°坡口的低碳钢,坡口切割速度每分钟可达2200mm,用功率6000W的激光切割8mm厚22.5°坡口的不锈钢,坡口的切割速度每分钟可达1500mm。
2. 激光切割技术在船舶方面的应用现状
(1)船舶切割特点
船舶行业对于船体分段转配精度要求高,构架转配间隙必须控制在1 m m 范围。以往船舶制造企业一般采用等离子对肋板下料时,为了保证装配间隙,在肋板上均设置修割余量,这需要在现场装配时手工进行修割,修割质量参差不齐,割缝内残留氧化物,同时增加了装配工作量,装配周期增长,致使整个分段建造周期延长。另外,采用激光切割机下料取消了装配余量后,消除了现场修割的现象,减少了人工和材料浪费,构架装配速度明显加快,装配质量提升显著。
(2)激光切割技术在船舶制造中的应用优势
近几年,“精密造船”和“快速造船”成为船舶制造业发展的主要趋势,激光切割技术得到了快速发展,占据了整个激光加工行业的70%以上。船舶制造行业主要以钢板原料为主,使用激光切割板材,可代替一些需要采用复杂大型模具的冲切加工方法,大大缩短生产周期和降低成本。目前,船舶行业船体板材零件下料方式主要采用火焰切割、等离子切割、剪切加工以及激光切割。其他切割方式相对于激光切割有诸多不足,例如火焰切割与等离子切割割缝宽、切割精度差,易产生有害气体,环境污染大。而激光切割对于船板切割来说,具有切割精度高,热变形小,减少二次加工(如铣边、钻孔等)、转运、打磨,尤其小圆、小孔、曲面加工等优点,符合船体分段转配精度要求,能充分保证构架装配间隙控制在1m m范围,但其在钢材方面的实用切割速度相对等离子切割要差。低碳钢在不同切割方式下切割速度与切割厚度的关系,低碳钢在不同切割方式下切割效果分别如图2与表1所示
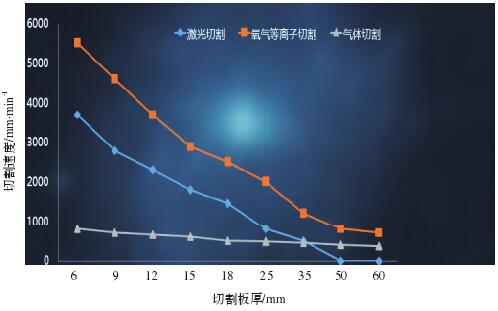
图2 低碳钢在不同切割方式下切割速度与切割厚度的关系
表1 低碳钢在不同切割方式下切割效果
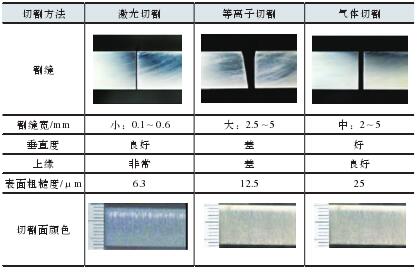
在船舶制造领域,激光切割避免了等离子对肋板下料时,为了保证装配间隙,而在肋板上设置修割余量,并通过人工进行修割,造成修割质量参差不齐的情况的发生。从而减少装配的工作量、装配周期、材料与人工成本浪费。通过激光切割的船用钢板,割缝质量好,切口面垂直性好,无挂渣,氧化层薄,表面光滑,无需二次加工,可直接焊接,且热变形小,曲线切割精度高,减少配合工时,实现无障碍切割高强船板。船舶内构材间隙量的偏差如图3所示。
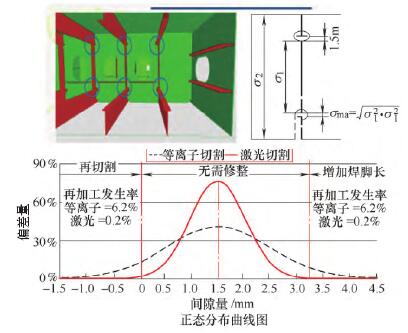
图3 船舶内构材间隙量的偏差
(3)激光切割技术在船舶制造中的应用现状
目前,CO2激光切割技术是全球造船生产用的最为普遍的制造加工技术。常用的5~6k WCO2激光器切割速度与等离子相比差,无法满足船舶制造业现下速度与效率优先的要求,并且其设备和机器维护成本高,回报少,满足不了造船业的需求。虽然它在船舶上的应用情况并不理想,但也逐步被采用,用于造船领域的激光切割源和相关切割加工设备构架的技术与工艺都有一些新进展。4k WCO2激光器切割效果如图4所示。
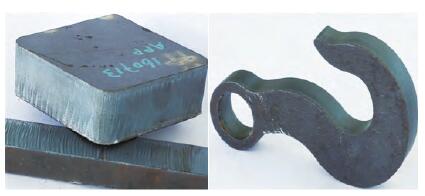
图4 4 k W CO2激光器切割效果
近年来,国内少数具有雄厚实力的造船厂,江南长兴造船基地也已引进世界先进的“搭载型(CO2)激光切割机”,但激光切割机搭载技术,国内外也就日本的技术应用比较乐观,它的成功或失败,也为国内造船行业提供宝贵的经验。同时,随着国内制造业的发展,光纤激光器也都得到快速发展,其高功率下具有极好的光束质量、高电光转化效率、相同功率下的小体积、光纤传输带来较好的工作柔性,以及几乎免维护的高可靠性等形成的综合优势,已经对传统的(CO2)激光切割构成了挑战。随着光纤激光切割加工中厚板效果的不断改进,国内不少切割设备的生产商都已经进入或正准备开展配置光纤激光器的数控激光切割机的研制阶段,以及一些院校、机构、学者已在研究光纤激光器的切割效果。例如:Jae Sung Shin等人通过6k W光纤激光器研究高速光纤激光对不锈钢板的切割性能,最大切割速度每分钟可达72mm,可切割60mm厚不锈钢板且切口形状和割缝宽度优良,如图5所示。
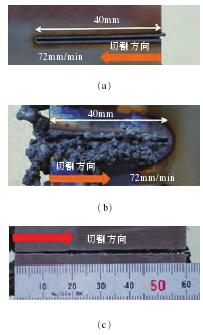
图5 切割60mm厚不锈钢板的切割速度
Antti Salminen等 人 用 5 k W 的 光 纤 激 光 器 对10m m不锈钢板和4m m铝板进行了惰性气体辅助激光切割。研究了激光功率、切割速度、焦点位置和辅助气体压力对切割性能和切割质量的影响。确定了不同激光功率下的最大切割速度,并研究了不同切割参数的组合,优化切割效果,得到优质切口等。参数为激光功率4k W,切割速度为每分钟1m,氮气2MPa的10mm厚不锈钢板的切割效果如图6所示。
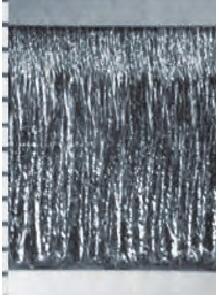
图6 激光功率4k W,切割速度为1m/min,氮气2MPa的10mm厚不锈钢板
现阶段光纤激光器的输出功率已达到50k W,但目前的开发重点还是放在1~4k W的激光器上,并以此为基础研发10k W的激光器,实现激光器的产业化发展,解决船舶、航天航空、汽车制造的切割与焊接问题。同时,激光切割技术为了适应切割情况与环境,充分被船舶制造业利用,其和机器人相结合,形成机器人切割系统。进入2000年,德国的KUKA、瑞士的ABB、日本的FANUC等机器人公司均研制激光机器人和激光切割机器人的系列产品。机器人技术与激光技术的结合是目前应用于船舶制造行业或是整个制造业的主流趋
势。
3. 激光切割在船舶行业应用的趋势及建议
如前所述,激光切割质量优势明显,在汽车、钣金、机械等领域得到大面积推广,就船舶行业来讲,也早已引起重视。沪东中华造船集团、江南造船集团、外高桥造船有限公司和上海宝山钢铁股份公司等早在2005年左右就与国内高校研究院所合作进行激光切割和焊接的研究,目前国内江南造船厂、武汉船厂等大型造船企业业已采用激光切割进行船板的加工。但客观的讲,在国内船舶行业,激光切割并未占据主导地位,主要原因包括:
①激光切割成本相比传统切割方法高。②激光切割的大型设备不适合船舶行业的制造特点,如现场施工、分段作业、工作环境复杂等。③切割效率没有明显优势,尤其是船舶行业的厚板切割。④激光设备维护复杂对工人要求高、成本高等。就目前行业的现状情况,随着激光器价格的逐步下降和智能化水平的提高,激光切割技术将逐步在船舶行业得到
大量应用。
主要原因包括:
(1)成本问题船舶行业(c)图5 切割60mm厚不锈钢板的切割速度(a)40mm72mm/min切割方向40mm72mm/min切割方向切割方向(b)最关心问题之一即切割成本,目前传统的工艺一般包括板材进厂+ 火焰切割或等离子切割 + 人工去毛刺+人工坡口或修边机开坡口+摇臂钻钻等包括大约5个工序+4次零件搬运,工艺相对繁复,成本浪费,若采用激光切割代替,则工序可简化为板材进厂+激光切割(激光切割+激光坡口+激光钻孔),在时间成本、人力成本、场地成本等方面均得到降低。为进一步直观比较相应成本,本文经过测算,并与伯纳激光科技等多家公司核实,给出表2~表4的对比数据。
表中的试验和核算中采用统一条件,所用材料为Q345B,板材规格2200mm×6000mm×25mm,切割6张,单张切缝数量为7,切 割 总 长 度 2 5 2 m , 板 材 重 量15543k g,采用直线下料切割方式。成本的核算考虑人力成本、材料损耗、附件损耗、切割气体成本等。由表格可以看出,激光切割已经具有明显优势。
表2 火焰切割成本
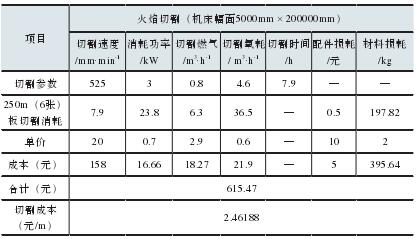
表3 等离子切割成本
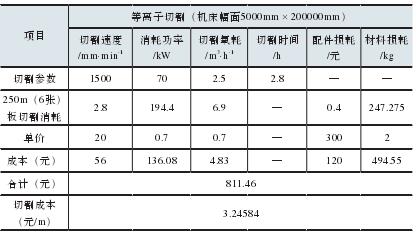
表4 激光切割成本
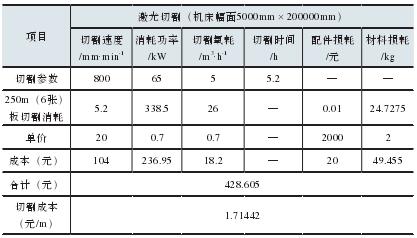
(2)激光设备的柔性化、智能化逐步适应船舶行业的发展
近些年国内大型装备的智能化水平有所突破,基于CNC、机器人机器组合的各类装备很多具有模块化、智能化的实用技术,如南通中远川崎智能生产线能适应复杂情况下的制造系统。这对于船舶行业的分段制造、户外作业以及复杂生产环境具有良好的适应性。除了装备外,工艺最终决定了使用效果,因此科技人员通过实时监测与控制机械切割过程,完成工艺信息的采集与分析,同时融入多个能场与工艺,实现工艺改良的重要手段,进而提高激光切割效果,简化切割工序,缩减工期与成本。
(3)激光器的发展降低了设备、维护成本
随着大功率光纤激光器与半导体激光器制造技术的快速发展以及相应的加工技术水平的提升,光纤激光器与半导体激光器的高效、节能、精密的切割特点,迎合市场需求,符合当下激光制造技术的发展方向,应大力推动光纤激光器与半导体激光器的产业化与市场化及其相应设备与控制技术的开发完善。而相应设备的进展又进一步提高了设备的集成度和柔性水平,针对船舶舾板工作对切割机的特殊要求和船体结构所用型材加工形状的多样性,激光切割头多自由度优化设计、旋转控制方式与控制系统的研发迫在眉睫,同时重视机器人与机械视觉检测系统在激光领域的应用研究,实现监测切割路径,高精度切割,无人自动操作,来提高作业质量和作业效率,有效控制切割质量,降低生产成本和安全风险。
中国船舶行业主动适应新常态,转型升级成效明显。战略性、前瞻性产品研发稳步推进,如7万总t级自主知识产权豪华邮轮、3.88万t智能示范船、第七代超深水钻井平台、新型极地自破冰科考船、超大型乙烷运输船(VLEC)等逐步在开发和生产,在国内订单下降的情况下,出口订单在稳步增长。相应具有研发优势的企业进一步突出特色, 产业进一步集中,尤其是前10名的企业占据半壁江山,而这些必将进一步推动对高质量制造的需求,推动激光切割在该行业的应用,而激光行业也必将进一步适应船舶行业的需求,朝着进一步降低成本、高质量、智能化的方向发展。
投稿箱:
如果您有机床行业、企业相关新闻稿件发表,或进行资讯合作,欢迎联系本网编辑部, 邮箱:skjcsc@vip.sina.com
如果您有机床行业、企业相关新闻稿件发表,或进行资讯合作,欢迎联系本网编辑部, 邮箱:skjcsc@vip.sina.com