提高大型数控旋压机加工精度的调试方法及研究
2018-2-1 来源:北京航空制造工程研究所 作者:王海涛 李初晔 关大力
摘 要: 针对自主研发的大型旋压机,装配完成后,通过调试过程以及对调试方法的研究,积累了大量机械、工艺、电气和液压等方面的经验,优化了加工工艺和控制参数,提高了机床的加工精度和稳定性,效果显著。
关键词: 大型数控装备; 调试; 加工精度; 参数
大型数控装备与国家的重大战略息息相关,是制造产业链中关键的基础装备,从一定程度上体现了一个国家前沿的制造能力和制造水平,是国民经济和国防安全的重要保障,同时也是我国实现工业化振兴的重要支撑。
大型立式数控强力旋压机作为大型数控装备的一个代表,是国内首台具有完全自主知识产权的大型专用装备,填补了我国在该类装备领域的战略空白,达到了国际先进水平,打破了国外相关加工技术的封锁局面,满足了我国航天领域回转体大型关键件的旋压成型加工,为我国军工行业提供了强有力的技术支持。
该数控装备为三旋轮 120°均布的封闭式框架结构( 如图 1 所示) ,总重量达 600 余吨,整体高度 17 000mm 左右,占地面积约 25 000 mm × 23 500 mm,单旋轮最大推力可达 1 000 k N。因此,大型立式强力旋压机具有受力结构合理、吨位重、外形大、负载高以及工作状态复杂等特点。
大型立式数控强力旋压机装配完成后,根据用户需求,随后展开一系列的调试工作。由于该大型数控装备为国内首台,而且对加工精度要求较高,另外,各部件的功能结构、液压冷却润滑系统和控制系统相对都很复杂,目前国内尚无该方面的调试经验可以借鉴,加之该装备担负着重要的国防生产任务,因而,调试工作面临前所未有的挑战。
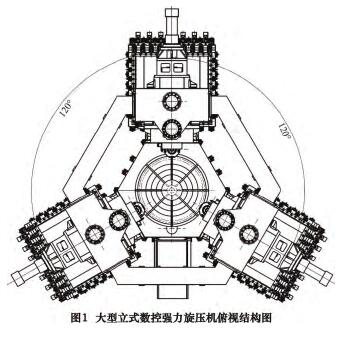
为了使该装备尽快在最短时间内发挥应有的作用,满足生产的需要,针对试运行和加工过程中出现的影响设备运行和加工精度的问题,进行相应的研究和调试,并予以解决。1 调试流程简述通过分析大型立式数控强力旋压机的结构特点、功能属性、工艺要求和技术参数等实际情况,在充分论证的基础上,制定 了调试的具 体方 案流程,如图 2所示
。
由流程框图可以看出,整个设备的主要调试工作和顺序都已经逐一列出。接下来,参照流程框图,着手开始设备的调试工作,为提高调试的效率,有些调试工作可穿插进行,针对调试过程中出现的实际问题和情况,在一定范围内,可以进行适当的调整。根据调试现场的环境和条件,结合设备的实际,将调试过程大概划分成以下几个部分:
1. 1 准备工作
在调试工作展开之前,首先对设备周边清理干净,检查机床所有垫块是否都已受力,如有松动,务必进行调整使其着力。然后对机电液及附件进行全面的自查自检,对于能够进行检测的项目,比如工作台的水平、立柱和滑枕导轨面的垂直和水平等,都必须复检并进行记录。
再者,在设备通电前,要严格检查所有接电位置是否正确可靠,接地是否良好,如没有问题方可送电。另外,还要检查确认液压、润滑油以及冷却水的容量等情况。
1. 2 基本动作和功能的调试
包括机械、液压、电气以及冷却润滑等。这期间,逐一对动作和功能进行调试,以下仅列出几项,用以说明:
( 1) 检查主轴电动机的正反相,如果接反,需及时调整,类似的工作还包括油泵和水泵等电动机。
( 2) 检查操作面板各按键是否完好灵敏,数据传输接口是否完好。
( 3) 检查数控系统与设备之间的数据传输功能。
整台设备需要调试的动作和功能非常繁杂,其中很多项的调试都需要反复多次进行,对调试的情况和结果,也都需仔细观察和检测。对于出现的特殊问题,在研究和论证后进行调试,直至符合使用要求。
1. 3 机电液的联合调试
该项工作是一个系统性的“工程”,是整个调试工作的关键。主要目的就是为设备的整体运行、加工可靠以及稳定的协同联动,提供坚实的基础和保障,成功与否,最终决定该设备研发的成败。
1. 4 加工调试
包括试加工和实际加工两个阶段,是对设备加工精度、运行稳定性和可靠性的提高和完善。
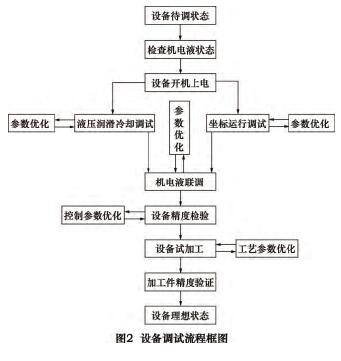
2 、问题的提出
大型立式数控强力旋压机的液压润滑冷却调试、坐标运行调试和机电液联调等前期调试工作,为旋压加工生产提供了坚实的基础和保证。对工件进行旋压加工时,旋轮径向推力 F1最大可达 1 000 k N,纵向推力 F2最大为 700 k N,工作台最高转速 n 能达到 100 r/min,如图 3 所示。因此,旋压工件的过程对设备加工能力带来了严峻的考验和检验,特别是对高强度钢和超高强度钢的旋压加工,尤为突出。

在加工过程中,由于受机械、控制、工艺、液压等综合因素的影响,设备加工运行中出现了一些问题,主要
表现如下:
( 1) 旋压过程中产生振动,影响工件外观质量。
( 2) 纵向导轨有“爬行”现象。
( 3) 连续旋压时,后面工件比前件壁厚偏薄。
( 4) 主轴回油时,有跳闸现象发生。
( 5) 其他原因。
3 、分析解决
针对上节在旋压加工中出现的 4 类重要问题,分别经过有针对性的分析、研究和论证,找出问题发生的主要原因,并提出解决问题的针对性措施。
( 1) 振动的发生,不但影响产品的外观质量,长时间的反复振动,也会影响设备的连接刚性,降低机床的加工稳定性和可靠性,降低加工精度。导致振动产生的因素比较复杂,在旋压过程中,通过反复多次对相关参数数值进行实时监测,观察和记录振动发生的坐标位置、旋压力大小的变化、工艺参数等数值,结合加工后的旋压件壁厚和直径的测量结果、表面振纹和外观质量的实际,梳理出导致振动的原因,对机床进行调试,情况如下所述:
①原因一: 三旋轮旋推力不平衡,偏载较大。受加工工艺的影响,横向推力偏载量在旋压过程中有时超过了平均值的 20% ,该载荷改变了受力平衡状态,进而引发振动。参照旋压工艺压下量参数,结合旋压加工过程,通过实时监控系统,对旋压力( 控制系统通过采集压力传感器反馈数据) 进行调整,使得三旋轮旋压推力差在 5 k N 以内,精旋时更小。
②原因二: 芯模紧固差,旋压时整体刚性不足。该情况导致工作台回转时,径跳方向和大小发生不断的变动,也是引起振动的重要原因之一。改进现有芯模的固定方式,周边增加连接固定件,既能增强芯模的整体刚性,又能方便快捷地调整芯模径向跳动,在很大程度上可以使振动得到减小。
③原因三: 旋轮切入工件时线速度不匹配。增加和实时采集旋轮的测速功能,保证旋轮线速度 v1和工件线速度 v2的合理匹配( v1≈v2) ,如图 4 所示,以减小旋轮与工件瞬接触时的冲击载荷,减小或消除由该因素导致的振动。
④原因四: 加工工艺参数不合理。不合理的工艺参数,也会导致旋压时的振动,不仅影响工件的加工精度,也对设备造成损害。
由于该机床是国内首台最大的立式旋压装备,工艺都是全新的,对于该结构类型机床的加工工艺参数的制定,需要经过多次的摸索才能逐步趋于合理。因此,根据工件的材料、尺寸等条件,对加工工艺参数进行相应的调整,也有利于减小和改善振动情况。
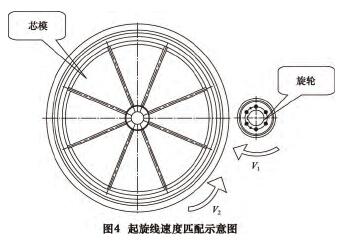
( 2) 爬行的发生,往往影响设备的加工精度、表面粗糙度和定位精度,也是振动产生的原因之一,是重型机床和精密机床必须解决的问题。该设备导轨为带润滑的滑动导轨,经检查,是由于润滑系统供油不稳定造成的,润滑系统是设备正常运行必需的重要条件之一,当发生故障时,就会导致润滑状态不稳定,特别是润滑不足时,导轨出现爬行现象,从而影响机床加工工件表面质量。
通过优化润滑系统的管路和布置方式,并增加了润滑量进出的检测和调整功能,使得整个导轨润滑形成一个实时监控和反馈的封闭系统,确保了润滑的合理性和准确性,消除了由此引发的“爬行”问题。
( 3) 经对旋压加工的分析,主要原因是芯模发热膨胀所致。
根据测量的结果,对数据进行分析,通过加工程序参数,做出相应的补偿。再者,可以适当增大旋压时的冷却量,以减小芯模的膨胀量,减小壁厚差值。另外,也可以根据实际情况,调整加工工艺或生产节拍,最大限度地提高工件壁厚差的精度。
( 4) 通过观察,主要原因是主轴冷却油的输入量Q1和输出量 Q2不匹配,造成循环过程的不平衡,使得回油泵超负荷运行,积累到一定程度,便发生跳闸现象。
通过计算和核对设备所需冷却油的流量,对回油油路的布置进行改进和优化,在冷却油的进油口和回油口增加流量传感器,通过数控系统对流量进行实时监测,如图 5 所示,并根据实际情况,调整进出油口的冷却量,既准确量化了冷却量,又避免了故障的发生。
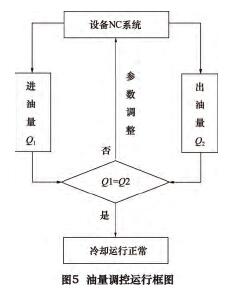
( 5) 至于其他影响设备振动的原因,从机床的数控系统方面做一个简述。该设备的数控系统属于包括电流环、速度环、位置环三环节的一个控制系统。例如,当改变位置环增益时,可以相应改变系统的固有频率,进而使得系统的响应速度发生变化。通过优化和调试系统伺服参数,使其处于最佳状态,避免系统振荡发生,保持系统的稳定,提高系统的控制精度,同时,配合机械上的一些调试调整,也可减小和改善机床的振动情况。
通过以上调试工作的有序实施,熟悉并掌握了大型数控装备调试的流程和方法,对研制开发该类型重大装备,积累了大量一手的资料和经验,与此同时,也进一步提升了大型数控强力旋压机的加工稳定性和可靠性,满足了生产的要求。
4 、结语
通过大型立式数控强力旋压机的调试工作,有以下几点启发:
( 1) 大型数控装备在设计、制造、管理等方面和国外的先进水平还存在着较大的差距,我们需要通过自己的努力,在学习和借鉴国外先进技术的基础上,不断探索和积累装配、调试、工艺等方面经验,以此反过来促进设计和制造水平,逐步缩小和国外的差距。
( 2) 国内大型数控装备所取得的成果,很多都是通过引进、消化、吸收后的再设计、再制造,如果我们在这个过程中不能有新的感悟和创新,就很难达到或赶超国际先进水平。因此,通过对设备进行调试,对调试过程中机电液所出现的问题进行综合分析研究,从根本上促进对大型装备研制综合专业水平的提升。
( 3) 大型数控装备的创新研发,不能一蹴而就,了解和把握自身的强项,正视国外先进技术的现状,找出突破口,在设计、制造和调试等工作中稳中求升。
( 4) 本文仅仅针对大型立式数控强力旋压机在调试过程中出现的问题进行分析、研究和解决,完全可以以点带面,借鉴和应用于其他大型数控装备的调试工作,提高大型装备的调试水平。大型数控装备的调试工作,是一项综合性、系统性和实践性的重要工作,本文所提出的方法虽然只是针对大型立式数控强力旋压机,但是对于该类型和其他类型的大型数控装备的调试工作,具有一定的借鉴和指导作用,也希望通过本文,起到抛砖引玉的效用,对于以后国内各行业所开发的新型的、填补国内空白的大型数控装备,能够在调试、装配、改进完善等各类工作上,作深入细致的研究,总结出更多更好的方式方法和实践经验,提高我国重大装备的创新力和国际市场的竞争力,为国家大型数控装备的研制工作增砖添瓦。
投稿箱:
如果您有机床行业、企业相关新闻稿件发表,或进行资讯合作,欢迎联系本网编辑部, 邮箱:skjcsc@vip.sina.com
如果您有机床行业、企业相关新闻稿件发表,或进行资讯合作,欢迎联系本网编辑部, 邮箱:skjcsc@vip.sina.com