摘要:高速往复走丝电火花线切割机床大锥度(≥±5°)切割时,受到诸多因素的影响,尤其是电极丝采用导轮定位产生的结构误差的影响,加上切割时工作液不能很好地包裹住电极丝并随着电极丝沿倾斜方向进入加工区域,使其加工精度和表面粗糙度比直体切割时差很多,对于锥度零件的多次切割特别是大锥度零件的多次切割则显得更加困难,其根本原因是没有能够保持电极丝空间位置及稳定性的随动导丝器和喷水机构。为此,设计了一种随着电极丝倾斜能随动导丝并跟踪喷液的六连杆大锥度随动导丝及喷水机构。通过试验,在相同加工参数条件下,新型随动机构与现有机构相比,圆锥加工误差从80μm减小到40μm,表面粗糙度Ra从4.059μm减小至3.495μm,多次切割后加工精度可以达到25μm(锥度±20°,工件厚40mm),表面粗糙度Ra达到1.670μm。
关键词:高速电火花线切割;大锥度;随动机构;多次切割
0 引言
作为高速往复走丝电火花线切割(HSWEDM)机床的重要品种———锥度线切割机床已广泛应用于成形刀具、电火花成形加工用电极、塑料和橡胶挤出模、拉丝模、模具镶拼件及多种零件(如斜齿轮、叶片等)的加工领域[1]。锥度工件特别是大锥度(≥±5°)工件切割时,由于受多种因素(尤其是电极丝采用导轮定位产生的各种结构误差)的影响,加上大锥度切割时工作液不能很好地包裹住电极丝且不能随着电极丝沿倾斜方向进入加工区域,其加工精度和表面粗糙度比直体加工时差很多,切割过程中断丝概率也较高,因此对于锥度零件的多次切割特别是大锥度零件的多次切割显得更加困难。
1 、现有大锥度切割存在的问题及处理方法
1.1 现有大锥度结构
现有大锥度切割的HSWEDM 通常由普通四连杆摆动式大锥度线架实现,如图1所示[2]。导轮在四连杆带动下可以在U 方向进行平移及在V 方向进行偏摆。采用导轮对电极丝进行定位存在以下问题:首先会产生锥度切割时电极丝的交切误差,如图2所示。锥度切割过程中,当进行U 向平移时,电极丝在导轮上的切点将从直体切割时的A、C点转变成锥度切割时的B、D 点,这就形成了实际电极丝位置和理论电极丝位置的误差,即交切误差b(图2)。交切误差随着切割锥度的增大和导轮直径的增大而加大。虽然交切误差可以通过插补计算的误差补偿进行修正,但由于大锥度切割时电极丝的空间位置的不稳定和不确定性,误差补偿大多数情况下反而适得其反。因此,如需要进行精密的大锥度切割时,必须首先保持电极丝空间位置的一致性和稳定性,采用导丝器对电极丝进行限位是行之有效的方法。其次,采用导轮对电极丝进行定位时,喷水嘴为避免与
电极丝在U 方向平移时形成干涉,通常做成沿U方向长槽式的多出水孔喷嘴,如图3所示。此时对电极丝的冷却无法保证工作液从喷嘴喷出后包裹住电极丝,且对电极丝产生扰动,如图4所示。所以该方式对加工区域的冷却效果很差,影响切割精度和表面质量。
图1 现有四连杆摆动式大锥度线架
图2 导轮定位U 向交切误差示意图
图3 长槽式喷水板结构
图4 U 向平移时电极丝单边“水幕”现象
1.2 现有大锥度切割工作液扰动分析
线切割加工的工作液都具有一定的黏度[3],在电极丝走丝时,就会因电极丝的运动而产生剪切流动,这种流动的根源在于流层间的黏性摩擦作用[4]。稳定切割过程中,理想条件下工作液能够均匀包裹住电极丝,如图5所示。加工过程中为使极间蚀除产物能够及时排除,需要保证放电间隙工作液具有较大流量[5]。流量大时,由于工
作液重力及水流的喷射压力作用,工作液自身流向为垂直于工作台面方向,而锥度切割时,电极丝倾斜一定的角度,工作液流向不平行于电极丝,因此对电极丝产生扰动。正向走丝(电极丝由上向下走丝)时,电极丝对工作液的剪切力垂直方向分力与工作液自身重力及工作液喷射压力同向,电极丝倾斜一定角度时,由于电极丝对工作液的剪切力作用,工作液在电极丝一侧产生“水幕”(图6a),对电极丝产生扰动,使加工不稳定,加工时采集的放电脉冲波形如图7a所示。电极丝反向走丝(电极丝由下向上走丝)时,剪切力垂直方向分力与工作液自身重力及水流喷射压力反向,避免了“水幕”现象产生,如图6b所示,工作液对电极丝的干扰较小,脉冲波形如图7b所示。
图5 理想条件下工作液包裹电极丝
根据流体动量定律:系统内的流体动量的时间变化率等于作用在系统上的外力矢量和[6],即
图6 电极丝不同走向时工作液扰动情况
图7 锥度切割电极丝正反向走丝时脉冲波形(界面图)量和。
式(1)中,等号左边表示系统内的流体动量,等号右边表示作用在系统上的外力矢量和。假设流体断面速度为常数,v1、v2分别为两断面速度。
由于封闭系统中,流体单位时间内流量Q恒定,所以各方向动量方程为
大锥度切割实验中,取单位时间工作液质量为δm,初始速度取为v1,其方向垂直于工作台面(图8中Y 方向),到达电极丝时工作液速度可视为与电极丝速度相等,v2方向与电极丝方向平行,如图8所示。图8中,Fx、Fy分别为电极丝对工作液的剪切力在X、Y 方向上的投影。将上述条件代入式(2)可得
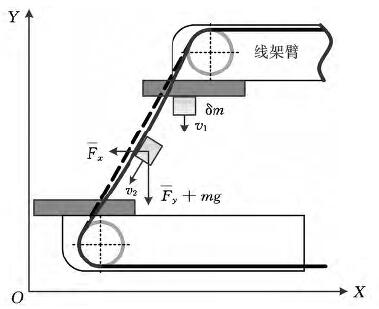
图8 单位质量工作液速度及受力模型
线切割加工过程中,电极丝可以抽象为两端支撑的弦 ,其两端受张紧力T 作用,如图9所示。由牛顿第三运动定律可知,F′x=Fx、F′y=Fy,即在电极丝正向走丝时,工作液在电极丝径向方向存在一定作用力F′,使得锥度切割时,电极丝正向走丝时偏离理论位置,从而严重影响工件表面质量。
图9 电极丝受力情况
2 、六连杆大锥度随动导丝及喷水机构原理
针对现有的HSWEDM 在切割大锥度工件时电极丝定位和喷水装置不能实现随动导丝及喷水的问题,设计了一种六连杆大锥度随动导丝及喷水机构,其原理如图10所示[8]。
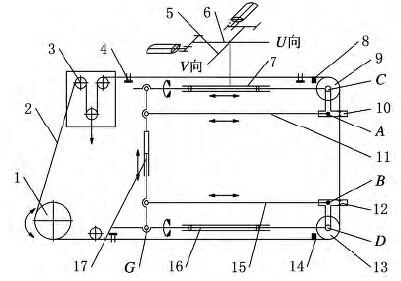
1.丝筒 2.电极丝 3.恒张力机构 4.宝石叉 5.V 向丝杠 6.U 向丝杠 7.上直线轴 8.上进电块 9.上导轮 10.上导丝器 11.上连杆 12.下导丝器 13.下导轮 14.下进电块 15.下连杆 16.下直线轴 17.套筒连杆
图10 六连杆大锥度随动导丝及喷水机构结构示意图
六连杆大锥度随动导丝及喷水机构U 向传动过程如下:在U 向电机的传动下,通过齿轮、丝杠6带动上直线轴7前后运动。此时整个上直线轴7和下连杆15的前后旋转中心为下线臂后端点G。当上直线轴7前伸或后退时,上连杆11向前或向后运动,通过转动点A带动上导丝器10绕旋转中心点C顺时针或逆时针旋转,如图11所示,与此同时下连杆15在套筒连杆17的带动下也会向前运动并通过转动点B带动下导丝器12绕旋转中心点D 顺时针或逆时针旋转。这样的运动可以保证上下导丝器转动一个角度,使得导丝器内的硬质定位块V形槽与电极丝始终重合。上连杆11与下连杆15的距离在运动过程中必然会产生伸长和缩短变化,这些变化可以由套筒连杆17自动伸长和缩短来补偿。U向的定位原理如图12所示。在运动过程中电极丝的伸长量由恒张力机构3进行补偿,走丝系统的进电由上下进电块8、14完成。
图11 锥度头U 向运动时随动喷水导丝器运动图
图12 U 向定位原理图
设计的六连杆大锥度随动导丝及喷水机构由于电极丝方向始终与导丝器中的V形槽重合,设计于导丝器上的喷水嘴喷出的工作液始终能包裹住电极丝并随电极丝进入加工区,因此能起到很好的洗涤、冷却和消电离作用[9],对加工精度、切割效率和表面质量的提高起到积极作用。其机构装置与加工过程如图13与图14所示。
图13 随动导丝及喷水机构实物装置
图14 随动导丝及喷水机构加工现场
3 、随动喷水及导丝加工工艺试验
分别采用现有大锥度机构与设计的随动导丝及喷水机构进行锥度切割试验。试验条件如表1所示。
表1 试验条件
3.1 工件表面质量影响
试验切割材料为厚20mm 的Cr12,切割形状为20mm×20mm锥度±20°的四方锥体,试验参数如表2所示。
表2 切割电参数
不同喷液条件下工件表面质量如图15~图17所示。现有喷液方式下工件表面粗糙度Ra=4.976μm,随动喷液方式下工件表面粗糙度Ra=3.284μm。
图15 工作液带入量不足时工件表面形成烧伤
图16 工作液扰动时工件表面凹凸不平
图17 随动喷液加工时工件表面平整
由图15~图17可知,现有大锥度喷液方式工作液带入量不稳定,当加工区域工作液不足时,极间蚀除产物没有及时排出,导致工件表面得不到及时冷却而出现烧伤;当工作液流量较大时,锥度加工中其喷射方向和电极丝走向角度时刻变化,工作液对电极丝的扰动力发生变化,导致工件表面形成凹凸不平的表面;而随动喷水在保证加工区域洗涤性能的同时减小了对电极丝的扰动力,工件表面平整均匀。
3.2 工件精度影响
试验切割材料为厚20mm 的Cr12,切割形状为底径20mm、锥度±20°的圆锥体。试验参数同表2。切割工件精度如表3所示。
表3 不同机构切割工件圆度误差值μm
随动导丝及喷水机构切割大锥度工件时电极丝始终垂直穿过导丝器,由导轮跳动和工作液扰动形成的扰动产生的振动通过导丝器的阻尼作用减弱消除[10],电极丝空间稳定性和一致性得到保证,零件加工精度相对现有机构有所提高。
3.3 大锥度多次切割影响
试验切割材料为厚40mm 的Cr12,切割形状为底径40mm、锥度±20°的圆锥体。试验参数如表4所示。
表4 多次切割电参数
多次切割工件表面纹理如图18所示。两种机构切割工件表面粗糙度和精度如表5、表6所示。
(a)现有机构多次切割工件表面纹理 (b)随动机构多次切割工件表面纹理
图18 不同大锥度机构切割工件表面
表5 两种机构切割工件表面粗糙度 Ra μm
表6 两种机构切割工件圆度误差值 μm
多次切割过程中,一次切割是双面对称余量加工,此时电极丝是在一个封闭的环境中进行切割加工的,对电极丝振动的阻尼作用较大,同时有利于电极丝在切缝中的稳定[11];而第二次切割是单边余量加工,加工时作用在电极丝上的放电力是不对称的,电极丝两侧的阻尼状态也不一样,此时切缝对电极丝振幅的约束作用大大减弱,如图19所示[12]。现有机构大锥度多次切割,由于没有能够保持电极丝空间位置及稳定性的机构,加上工作液对电极丝的扰动力,电极丝振动影响加大,多次切割工件表面效果很差。
图19 多次切割放电与单次切割放电的区别
随动导丝及喷水机构大锥度切割过程中工作液喷射方向始终与电极丝平行,且导丝器减小了电极丝的振动,多次切割过程中能够保持电极丝空间位置的稳定性,使多次切割电极丝重复定位精度提高,能够实现多次切割,大大提高了工件表面质量及精度。
4、 结语
本文通过对现有电火花大锥度切割机构与随动导丝及喷水大锥度切割机构的分析,讨论了现有大锥度机构存在问题,并提出相应的解决措施;通过对比试验验证了随动导丝及喷水机构结构的合理性。设计的随动导丝及喷水机构能够保证工作液的洗涤性能,在稳定电极丝空间位置作用的同时可减小对电极丝的扰动和干涉作用,大大提高了电火花大锥度切割工件的表面质量及精度。
如果您有机床行业、企业相关新闻稿件发表,或进行资讯合作,欢迎联系本网编辑部, 邮箱:skjcsc@vip.sina.com