电火花放电辅助化学加工间隙实验研究
2016-11-22 来源:清华大学机械工程系制造工程研究所 作者:刘光 佟浩 何苏钦 李勇
摘要:面向航空发动机涡轮叶片热障涂层ZrO2陶瓷绝缘材料的加工,开展了不同加工间隙对加工稳定性及效率影响的实验研究。采用CCD 图像在线观测微观接触的对准电极方法,实现了加工间隙测量给定精度可控±1 μm,进而在特定工艺参数下实验研究了加工间隙的评价和优化,利用工件表面离子溅射镀膜和Matlab 图像处理技术实现蚀除量分析,得出了稳定加工时材料最大蚀除量的最佳加工间隙范围,为电火花放电辅助化学加工工艺优化提供了依据。
关键词:放电辅助化学加工;氧化锆陶瓷;加工间隙
氧化锆(ZrO2)陶瓷材料在生物医疗、航空航天、燃气发电等领域具有广泛的应用, 如陶瓷义齿、涡轮叶片热障涂层等。但由于ZrO2陶瓷具有高硬、易脆等特性, 使其在传统机械加工中难以精密成形,且由于热应力、切削力等因素,易产生微裂纹,降低了材料使用寿命[1-2]。目前,氧化锆绝缘陶瓷的非传统加工方法主要有激光加工[3]、超声加工[4]、磨料水力喷射[5]等。然而,激光加工会使材料表面产生热影响、应力集中等而出现微裂纹;超声加工存在工具磨损严重、加工效率低、易产生微裂纹损伤等不足;磨料水力喷射加工用喷嘴需经常更换,且加工精度较低[6-7]。
近年来,有学者采用电火花放电辅助化学加工(apark assisted chemical engraving,SACE)的方法对玻璃、石英等多种绝缘材料进行加工[8-10]。SACE 的材料蚀除原理是在电解液中利用电解原理,在工具电极(阴极)上形成氢气泡,工具电极端部被气泡包裹,使工具电极与电解液分离,在绝缘气泡内瞬间火花放电引导下的电解液内进行蚀除加工,从而实现绝缘材料的加工。该方法无宏观接触力、电极损耗小,且电解液内腐蚀加工原理有望实现材料的无损伤加工。国内外研究已验证了ZrO2陶瓷SACE 加工的可行性,刘永红等研究了不同电解液对ZrO2陶瓷加工效率的影响[11];张有等在钛合金基体的氧化锆陶瓷涂层材料上加工出了直径1.4 mm 的通孔[12];Doloi 等进行了氧化锆陶瓷等绝缘材料的SACE 加工工艺研究,分析了电压、电解液浓度及电极间距等因素对材料去除率的影响[13]。
若要实现SACE 的连续加工, 就需控制工具电极的加工进给,其主要方式有恒力进给和恒速进给两种。恒力进给是通过控制工具电极与工件的接触力,实现工具电极的不断进给;但由于工具电极底部存在液膜,其实质是通过控制接触力来实现微米级的加工间隙;而恒速进给速度过快,会发生电极与工件碰撞,过慢则严重影响加工效率。不论哪种控制方式,目前其合理或最佳加工间隙尚未被阐述清楚,且本研究的前期实验发现,加工间隙对ZrO2陶瓷SACE 加工稳定性和效率具有较大影响。因此,本研究面向航空发动机ZrO2陶瓷热障涂层材料加工,通过开展热障涂层SACE 工艺实验,探索加工间隙对加工结果的影响,进而通过研究加工间隙的测量方法及合理加工间隙的评价方法,得出在特定参数下的SACE 最优加工间隙。
1.加工间隙对SACE 的影响实验
实验系统见图1,主要包括主轴机构(定位精度为±0.5 μm)、脉冲电源、金属钨工具电极、大尺寸石墨辅助电极(电极浸入电解液的表面积至少为工具电极的100 倍以上[14])。实验采用正极性加工方式,即工具电极为阴极,辅助电极为阳极。实验主要参数见表1。
主轴采用恒速进给方式,对ZrO2陶瓷工件进行逐层扫描恒速进给加工实验,SACE 扫描路径见图2。为了减少侧壁放电的概率并提供气膜形成的氛围,工具电极浸入电解液液面约2 mm。实验过程监测及结果见图3。实验发现电极与工件之间的间隙大小对加工稳定性、效率具有显著
表1 SACE 实验工艺参数
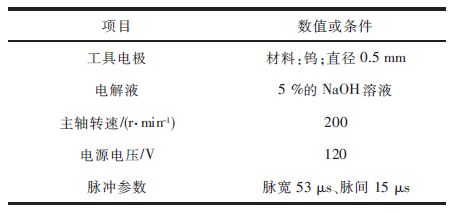
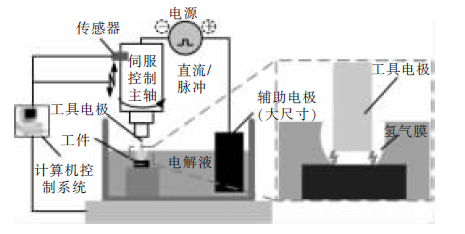
图1 SACE 实验系统示意图
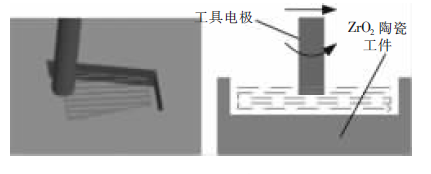
图2 SACE 扫描路径规划
影响。当工具电极与工件表面的间隙过大时,火花放电的瞬间作用在工件表面的爆炸力弱,不足以达到蚀除材料的目的(图3a);当工具电极与工件表面的间隙过小甚至互相接触时,对气膜形态产生了影响,且易产生拉弧现象,这种因电弧放电产生的高温高热将使工具电极与工件表面均出现不同程度的烧伤破坏(图3b)。因此,确定SACE 最佳加工间隙对ZrO2陶瓷稳定加工具有重要意义。
2.加工间隙测量方法
为研究SACE 最佳加工间隙, 首先要实现微米级加工间隙的测量和给定。本研究前期借鉴电接触测量原理,考虑到ZrO2陶瓷作为绝缘工件,故采用在工件表面放置标准厚度金属片作为辅助,以满足电接触回路形成的条件,从而通过工具电极电接触辅助金属片来获知工具电极与工件之间的相对位置,拟测量并给定加工间隙。
然而,应用中发现该方法的间隙测量精度无法达到要求,其误差分析见图4。分析可知,间隙测量误差主要来源于标准片变形Δ1和工件表面微观不平度Δ2。由于本研究采用等离子喷涂法制备ZrO2陶
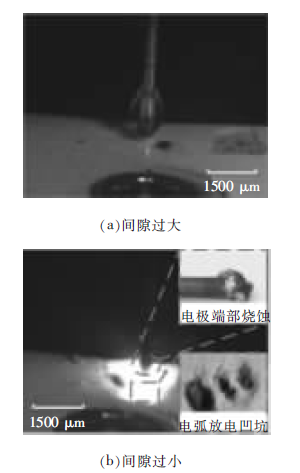
图3 不同间隙的SACE 放电现象对比
瓷热障涂层工件,该方法的工艺特点是工件材料表面会呈现微观不平形貌。实验中,当采用厚0.2 mm的辅助标准片时,位置误差甚至达到100~200 μm,已超出预设加工间隙所需的测量精度。因此,为了精确测定加工间隙,实验采用分辨率为500 万像素的工业数字摄像机,并利用主轴装置的高运动分辨率(0.5 μm),通过在线观测工具电极与工件微观瞬间接触状态,确定工具电极与工件的相对位置。
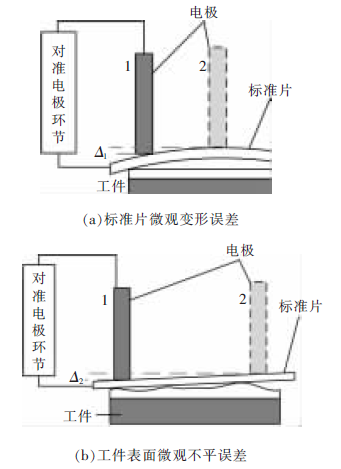
图4 辅助金属片对准电极方法的误差示意图
如图5 所示,电极先接近工件表面,并以每步0.5 μm 的进给量逐次进给, 当接触瞬间CCD 图像观测到接触状态微观变化,即认为电极与工件接触(图5b);然后,电极回退,直至微观接触变化恢复(图5a),可保证h1和h2在±1 μm 之间,即实现可控的测量精度达±1 μm。这样,就能精确确定工具电极与工件表面的接触点位置,再控制电极的回退量即可给定加工间隙。由于工件表面微观不平,故每个位置的实验将重复上述步骤。
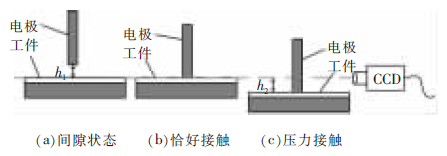
图5 CCD 图像观测对准电极方法示意图
3.加工间隙优化实验
给定不同的加工间隙并保持一段时间, 进行ZrO2陶瓷的SACE 加工实验,通过评价材料去除率和加工过程的放电稳定性,可得出最佳加工间隙范围。由于白色ZrO2陶瓷工件表面不便观测材料去除效果, 故对工件表面采用离子溅射金靶的方式镀膜,使工件表面与基体材料呈现色差,加工后工件表层材料剥离,可与未加工部分形成明显对比。因纳米级厚度镀膜瞬间即可剥离,故忽略其对实验效果的影响。
实验沿用表1 所示的加工参数,通过设定不同加工间隙δ 进行分组实验,每次实验保持加工时间5 min。实验结果见图6,观测发现:当加工间隙δ 为150 μm 时,加工痕迹微小;随着δ 逐渐减小,加工痕迹越来越明显;当δ 进一步减小时,加工进入稳定阶段,加工痕迹增大;当δ 小于某一间隙值时,开始出现明显的电弧放电现象, 工件表面出现过热烧蚀,使SACE 不能稳定进行。
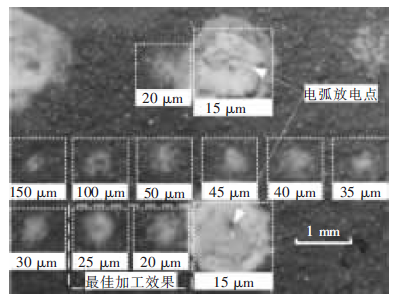
图6 不同加工间隙δ 对应SACE 加工结果
根据加工过程和实验结果可认为,在正常稳定放电情况下,材料去除量最大时的加工间隙为最佳加工间隙。因为实验去除的工件材料为不规则形状,为便于对比评价材料蚀除量大小,通过图形处理方法对比加工位置的蚀除面积大小。本研究采用Matlab 软件对各组实验结果进行图像分析处理,对比反显图像灰度值0~2 范围内的像素(图7),得出不同间隙时材料去除面积的对比情况(图8),即像值越高,材料去除面积越大。从图8 可看出,加工间隙δ 为20~25 μm 时,工件材料蚀除量最大,即为该加工条件下的SACE 最佳加工间隙。利用该方法,可评价并得到给定工艺条件下的最佳加工间隙。
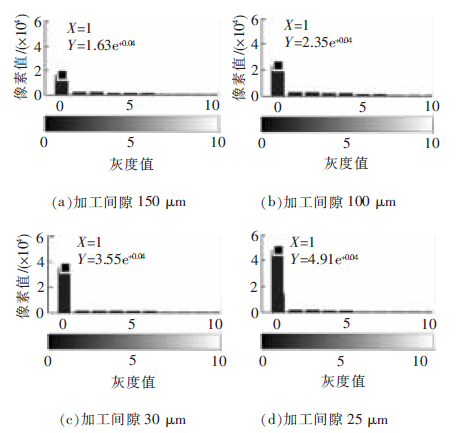
图7 不同加工间隙的实验结果灰度图

图8 各组SACE 加工点像素值对比
4.结论
为优化ZrO2陶瓷的放电辅助化学加工(SACE)工艺,探索了加工间隙对工艺过程的影响,开展了加工间隙测量评价及最佳间隙实验研究,得到如下结论:
(1)当加工间隙过大时,虽然可在电极端部气泡内放电,但作用于工件上的放电能量过小,难以去除工件材料;加工间隙过小时,易产生电弧放电现象,损伤工具电极和工件。
(2)辅助标准片的电接触对准电极方法会产生较大的间隙测量误差(达到100~200 μm),因此采用分辨率为500 万像素的数字摄像机在线观测工具电极与工件微观瞬间接触变形的对准电极方法,实现了加工间隙在线测量,且给定大小的精度可控达±1 μm。
(3)借助Matlab 图像分析方法评价加工去除面积, 在本实验条件下优化得到了正常放电情况下(避免电弧放电) 蚀除面积最大时的最佳加工间隙为20~25 μm。
投稿箱:
如果您有机床行业、企业相关新闻稿件发表,或进行资讯合作,欢迎联系本网编辑部, 邮箱:skjcsc@vip.sina.com
如果您有机床行业、企业相关新闻稿件发表,或进行资讯合作,欢迎联系本网编辑部, 邮箱:skjcsc@vip.sina.com
更多相关信息