组合机床生产线加工及上下料控制系统的设计
2015-2-23 来源:常熟理工学院电气与自动化学院 作者:刘燕,周航
摘 要:根据自动化生产线中工件加工的要求,设计了一种组合机床生产线自动加工及上下料控制系统。该系统以西门子S7-200PLC控制器为核心,结合步进电机、高分辨率伺服电机以及位置传感器等元件的检测定位,实现了工件的上料、装卸、下料和加工等工序的自动连续生产。该系统经现场调试运行,能满足生产线高效率、高质量的自动化加工需要。
0 、引言
自动化生产线是依照所设定的工艺过程,将生产和加工各过程组合起来,完成上料、装卸、下料和加工等工序的自动测量、自动控制和连续生产。加工的产品或零件在生产线各工位的工艺操作和辅助工作以及工序间的输送等均能自动进行,生产线具有较高的自动化程度。本文将探究自动化生产线加工及上下料控制系统的电气部分设计。针对其中圆柱形工件的加工工艺以及控制要求设计硬件、软件等电路,以满足组合机床生产线高效率、高质量的自动化加工需要。
1 、组合机床加工生产线的结构
组合机床加工自动化生产线包含5个部分,分别为机械手横轴、机械手竖轴、上料架、机床加工和回料仓。自动加工及上下料控制系统工作流程为:当自动给料架上放入工件后,给料架自动将工件输送到机械手所处的抓取位置。机械手从给料架中取出工件移动到机床卡盘上,工件到位后,三相电机启动对工件进行加工。加工完成后,机械手将工件抓起并放入到旋转气缸中,工件到位后,对其进行再加工,再加工完成的工件由机械手从旋转气缸取出,放入到回料仓中,至此一个工件的循环加工过程完成。在加工运行过程中如果按下停止按钮,在完成将工件放回料仓的动作后机械手寻零复位,系统停止运行,报警灯亮。各部分的检测与驱动部分如图1所示。
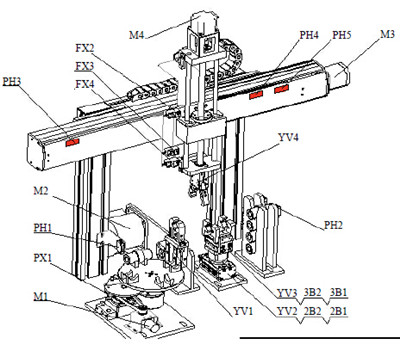
图1 组合机床结构图模型
1)机械手横轴由伺服电机M3带动,控制机械手在水平方向上的移动。位置传感器PH3(左限位)和PH5(右限位)确定机械手水平方向上的移动范围。位置传感器PH4则用来确定水平方向上的参考零点位置。
2)机械手竖轴由步进电机M4带动,控制机械手在垂直方向上的移动。位置传感器PX4(上限位)和PX2(下限位)确定机械手垂直方向上的移动范围。位置传感器PX3则用来确定垂直方向上的参考零点位置。机械手爪的夹紧与松开由电磁阀YV4的得失电控制。机械手爪为CAAP MHY系列气缸。
3)直流电机M1通过皮带带动上料架转动。位置传感器PX1检测料仓位置,位置传感器PH1检测物料位置。
4) 加工机床由机床卡盘和旋转气缸组成,电磁阀YV1控制机床卡盘动作;电磁阀YV2、YV3K控制旋转气缸动作;三相异步电机M2完成机床加工动作。
5)位置传感器PH2检测物料回仓。
2 、组合机床生产线控制系统设计
自动化生产线的控制系统由检测传感元件、控制元件和执行元件等部分组成。检测传感元件多为位置传感器,用来检测运行过程中工件的具体位置,并将检测到的信号传送给系统控制器;系统控制器采用PLC控制,对接收到的信号进行转换处理,并将处理完成的信号输出至执行元件。执行元件接收到控制信号后完成加工控制的具体动作。本系统中用到的控制元件还包含步进驱动器、伺服驱动器、变频器、继电器和电磁阀。执行元件有步进电机、伺服电机、三相异步电机、气缸和报警灯等。组合机床生产线总体控制方案如图2所示。
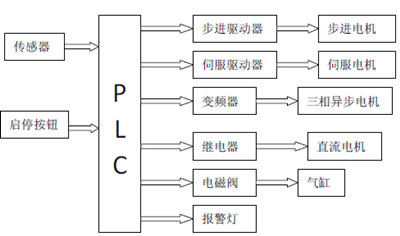
图2 控制方案图
步进电机驱动器接收PLC控制器输出的脉冲及方向信号驱动步进电机转动,并带动机械手水平移动。伺服电机驱动器接收PLC控制器输出的脉冲及方向信号,驱动伺服电机转动带动机械手竖轴移动。变频器根据PLC I/O口输出的状态,控制三相异步电机的启动和 停止。PLC的I/O输出控制继电器的通断,由继电器控制直流电机的启停,进而带动上料架转动。电磁阀的由PLC I/O口控制,以控制气缸的动作(夹紧与松开)。位置传感器用于检测机械手在横轴或竖轴的移动位置以及工件在控制过程中所处的位置,检测到信号后,转换为开关量输入PLC。根据控制所需I/O点数,PLC选用S7-200系列224XP,外加一个EM 223扩展模块。PLC的I/O分配如表1所示。
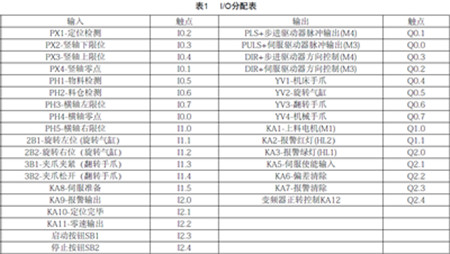
2.1 伺服驱动系统的控制
自动化生产线横轴移动及位置检测精度要求比较高,用伺服电机实现传动定位控制。图3为伺服驱动器接线图。选用合信伺服驱动器E10匹配伺服电机CTSD M16-B2012-M100。伺服驱动器E10的DI数字输入信号有伺服使能、解除报警、顺/逆时针行程限位、齿轮比切换、脉冲输入禁止、零速锁定、位置偏差清除等;DO输出有伺服准备好、报警输出、定位完成、零速检测输出等。在位置控制模式时调整电子齿轮比可以设置单位指令脉冲对应的电机速度以及位移量。假设编码器分辨率为10000,则每转所需脉冲数计算公为:
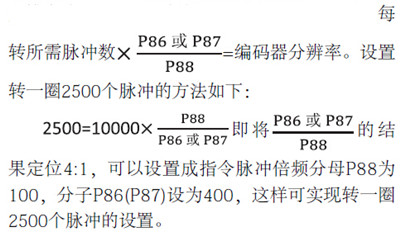
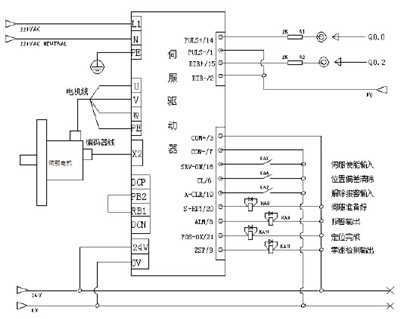
图3 伺服控制系统接线图
由图3可知,通过编码器线将伺服驱动器与伺服电机进行连接。伺服电机接收来自驱动器的电压信号并转化为相应的转矩量和转速值驱动控制对象。旋转编码器检测出伺服电机的转数,并将角位移转换成脉冲值,通过内置的高数计数器统计编码器发出的脉冲数,从而判断机械手在横轴水平运动过程中所处的位置。通过改变控制脉冲数的大小,就可控制伺服电机转动的角位移,从而控制机械手在横轴方向上的水平移动距离,实现机械手在横轴上的精确定位。
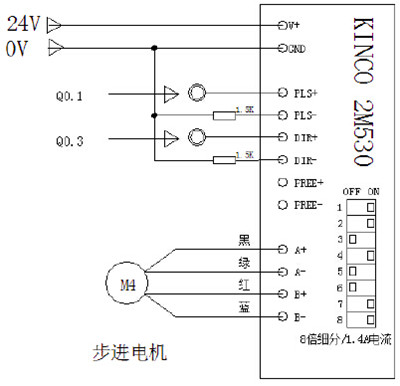
图4 步进控制系统接线图
2.2 步进驱动系统的控制
自动化生产线的竖轴移动及位置检测采用步进电机控制,接线如图4所示。采用2M530步进驱动器,并选择与之配套的两相步进电机Kinco,其步距角为1.8度,额定电压为24V,相电流3A。步进电机的A+、A-、B+、B-四个驱动信号分别通过信号线由步进电机驱动器控制。控制步进驱动器的脉冲数和脉冲频率来控制步进电机的角位移量和转动速度,实现机械手在垂直方向上的准确定位和调速。2M530步进驱动器采用双极型恒流驱动方式,当驱动电流小于3.5A时,它可以驱动任何两相双极型步进电机。通过调整DIP开关,改变对电机驱动输出的相电流,实现与不同规格步进电机的配合使用。采用专用电机驱动控制芯片,具有最高可达256/200的细分功能,细分可以通过DIP开关设定,保证提供最好的运行平稳性能。如8细分的驱动方式下步进电机驱动器接收200×8=1600个脉冲信号步进电机转动一圈。
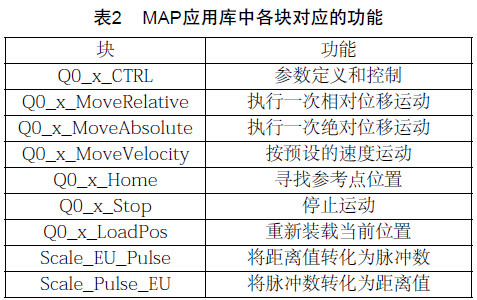
3 、软件程序设计
按照自动加工工艺要求设计其软件程序,控制流程如图5所示。
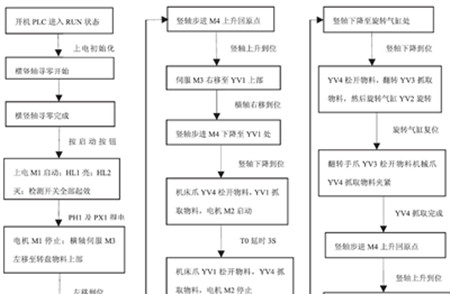
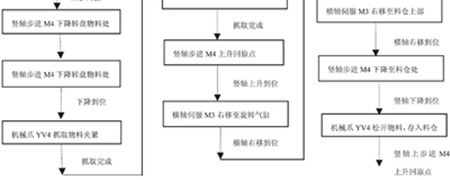
图5 生产线软件控制流程图
S7-200提供了脉宽调制(PWM)、脉冲串输出(PTO)、EM253位控模块三种方式的开环运动控制。本次设计中采用S7-200本体PTO提供的应用库MAP SERV Q0.0和MAP SERV Q0.1分别用于Q0.0与Q0.1脉冲串输出控制伺服电机和步进电机,实现组合机床横轴与纵轴的定位控制。应用库MAP如图6所示,其中各个块的功能如表2所示,这些程序块全部基于S7-200内置的PTO输出,通过相应的程序块设置完成组合机床横轴和纵轴的运动控制功能。选择MAP应用库来输出脉冲具有以下优点:
1)只要知道距离值就可以利用MAP应用库中的对应的功能块直接转换成脉冲数,避免了大量繁琐的计算。
2)由于MAP库中有参数定义、寻找参考点位置、停止运动、将距离值转换为脉冲数等对应的功能块,所以在程序的编写时只需直接调用所需的块,修改对应的参数即可。这样为编程人员节省了大量的时间,并且当在调试的过程中遇到问题时,只需修改对应功能块参数即可。
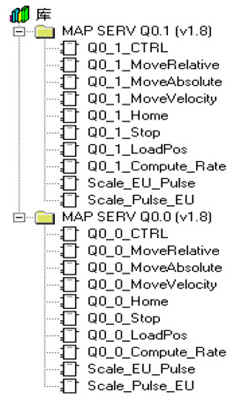
图6 MAP SERV应用库
4 、结束语
根据生产线组合机床加工的要求,结合工件加工工艺设计了一种针对生产线自动加工及上下料的控制系统。该系统基于PLC控制能实现工件的上料、装卸、下料和加工等工序的自动连续生产,运行可靠。该系统投入到实际生产,大大降低了劳动强度,提高了工作效率,具有很好的实际应用价值。
投稿箱:
如果您有机床行业、企业相关新闻稿件发表,或进行资讯合作,欢迎联系本网编辑部, 邮箱:skjcsc@vip.sina.com
如果您有机床行业、企业相关新闻稿件发表,或进行资讯合作,欢迎联系本网编辑部, 邮箱:skjcsc@vip.sina.com
更多相关信息