PCD刀具加工有色金属的研究
2014-4-15 来源:数控机床市场网 作者:江兆周 张弘弢 董 海李
摘要:本文主要研究 PCD刀具加工有色金属时刃口及后刀面的刃磨质量对切削表面质量的影响。首先对 PCD刀具切削有色金属模型进行了分析研究, 然后分别采用金属结合剂金刚石砂轮、树脂结合剂金刚石砂轮和陶瓷结合剂金刚石砂轮刃磨出三把不同质量的 PCD刀具进行了切削对比试验, 并用扫描电镜对切削表面微观形貌进行了观察分析, 发现加工有色金属时, PCD刀具后刀面与刃口刃磨质量对切削表面质量有着同等重要的影响作用。
关键词:PCD刀具, 刃口, 后刀面, 表面质量
1 引言
聚晶金刚石 (简称 PCD)刀具材料具有高硬度、良好的耐磨性, 并且相对于单晶金刚石还具有各向同性、导电性、可焊接性及经济性等优点, 使其在加工有色金属及难加工非金属材料领域中得到了广泛的应用。
PCD刀具的优良特性使其切削规律与普通刀具的切削规律有所区别, 本文就 PCD刀具加工有色金属进行了探讨研究。
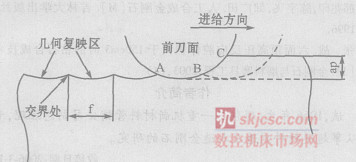
图 1 PCD刀具切削模型
2 PCD刀具切削模型
图 1为 PCD刀具切削模型, 总体看来, 已加工表面的形成过程是刀具 AB段圆弧在工件表面几何复映不断重复的过程; 而对于工件表面单个刀具几何复映区的形成来说, 它首先要经过刀具刃口的挤压, 然后产生弹性恢复, 与刀具后刀面完全相接触 (其接触面域如图 2所示 ), 最终在后刀面给其施加的法向力和摩擦力的作用下发生塑性变形和弹性变形, 流离刀具后刀面形成加工工件表面。
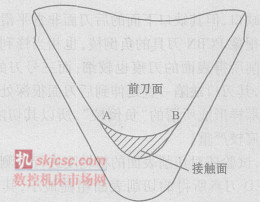
图 2 刀具后刀面与工件接触面域
从上述分析可知, 单个几何复映区内, 已加工表面最终是在与刀具后刀面相互作用下形成的。对于普通刀具, 由于刀具材料的硬度、耐磨性及后刀面光洁度不够, 这种相互作用增大了刀具与工件间的摩擦, 最终是加速了刀具的磨损, 降低了加工表面质量, 而 PCD刀具后刀面一般相当光滑, 且 PCD材料具有高的硬度及耐磨性, 所以 PCD刀具的后刀面对加工工件表面起着熨压的重要作用, 特别是在切削有色金属时, 由于材质较软, 弹塑性较大, 这种熨压作用尤为突出, 所以 PCD刀具的后刀面刃磨质量直接影响着加工工件表面质量。但是, 在工件表面刀具几何复映区的交界处, 加工工件表面与后刀面的接触面积几乎没有, 如图 2所示,工件表面刀具几何复映区的交界处应只与 A、B点刀刃相接触, 而不与后刀面接触, 即 A、B附近处的刀刃质量直接决定了工件上刀具几何复映交界处附近表面的加工质量。
3 切削试验
试验在普通车床 CA6140上进行, 采用三把不同刃磨质量的 PCD刀具进行了切削加工表面质量对比试验。
3 . 1 切削用刀具
试验用三把 PCD刀具的刀坯为英国 DeBeers公司生产的表面已抛光的 010系列, 分别用金属结合剂金刚石砂轮、树脂结合剂金刚石砂轮和陶瓷结合剂金刚石砂轮刃磨而得, 记为一号刀、二号刀、三号刀。其几何参数均为 γ0= 0°、α0= 6°、λs= 0°、Kγ= 45°、Kγ =45°、rε= 0.4mm。
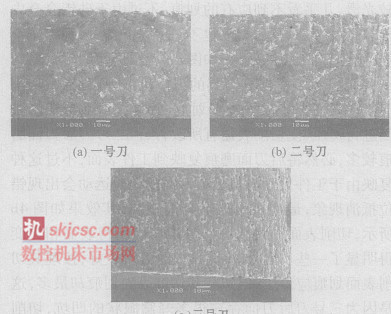
图 3为三把 PCD刀具刃口及后刀面扫描电镜图。
如图 3a所示, 一号刀刃口在右侧靠近刀尖处出现了较大的冲击缺口, 但总体来说一号刀的刃口仍比较平直,而且在三把刀中其后刀面最光滑, 表面质量最好。由图 3b可见, 二号刀后刀面存在较多磨痕, 而且磨痕已经延伸到了刃口, 若从前刀面看, 其刃口呈锯齿状。图3c为三号刀的刃口和后刀面的微观形貌图, 与前两把刀相比, 三号刀的刃口非常平直, 几乎没有缺陷, 质量最好, 而其后刀面虽然也较平整, 但却出现了较多凹坑, 这些凹坑严重破坏了 PCD材料的结构性能, 所以三号刀的后刀面质量最差。
3 . 2 工件材料
本试验采用加工工件为含硅量 10 % 的薄铝管。
薄铝管便于制备样品从而实现对切削加工表面形貌进图 3 切削用刀刃口及后刀面微观形貌行扫描电镜观察。
4 试验结果及分析
图 4为三把 PCD刀具切削铝管所得切削表面形貌图, 三把刀切削铝管时切削用量均为 v=53.5m /min ; f= 0.1mm /r ; ap= 0.1mm。由于铝管直径较小以及受机床性能限制, 所以切削速度选得比较低。
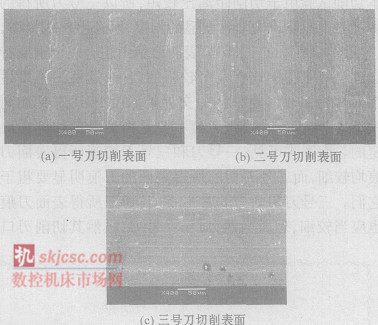
图 4 加工工件表面扫描电镜图
由图可见, 在一个刀具几何复映区内, 一号刀所得切削表面相当光滑, 几乎看不到划痕; 二号刀所得切削表面的划痕则较为明显; 三号刀所得切削表面的划痕则非常明显。由 PCD刀具的切削模型可知, 工件表面单个刀具几何复映区的形成首先要经过刀具刃口的挤压, 对于一号刀, 其刀尖处存在较大缺口, 可能在切削表面留下较大划痕, 但 PCD刀具的后刀面对切削表面有熨压作用, 一号 PCD刀具的后刀面表面质量好, 光洁度高, 所以较软的铝工件表面经其熨压后, 表面变得较光滑, 几乎看不到应有的划痕, 不过由于硅铝合金中Si粒子的存在, 且后刀面也不是完全光滑, 因此熨压不能达到完全理想的效果, 如图 4a所示仍隐约可以看到一些划痕。二号 PCD刀具的刃口呈锯齿状, 因此切削时工件表面必然留下较多划痕, 接着后刀面对切削表面进行熨压, 使切削表面有所改善, 但二号刀后刀面磨痕较多, 必然将后刀面磨痕复映到工件表面, 不过这种复映由于工件表面与刀具后刀面的相对运动会出现错位抵消现象, 最终表面也不会很糟糕, 其效果如图4b所示, 切削表面的划痕与一号刀切削所得表面相比变得明显了一些。三号 PCD刀具的刃口较好, 按理其切削表面划痕应最少, 但实际其切削表面划痕却最多,这是因为三号刀后刀面存在很多蜂窝眼状的凹坑, 切削时, 加工工件表面材料在后刀面熨压作用下发生弹塑性变形, 由于加工工件材料铝较软, 必然使其在塑性流动过程中被强行压入后刀面的凹坑中, 发生机械镶嵌作用, 这些镶嵌材料经过不断的挤压后将变得很硬,并在突出后刀面形成微刃划伤切削加工表面, 最终这些镶嵌材料可能会带着部分刀具材料脱落, 同样这些脱落颗粒也将划伤加工工件表面或嵌入在切削表面上, 本切削试验由于切削距离比较短, 所以三号刀所得的切削表面只是出现非常明显的划痕, 而未出现残留物。
图 4所示的三张切削表面形貌图还有一个重要特点就是每张图中均有几个较粗的刀痕, 这些刀痕发生在刀具相邻几何复映区的交界处。由 PCD刀具切削模型的分析可知, 这些刀痕主要是由刀具的切削刃决定的。由图 4可见, 一号刀和三号刀切削所得表面刀痕均较细, 而二号刀切削所得表面的刀痕明显要粗于它们。三号刀切削刃非常平直, 其切削所得表面刀痕也应当较细, 理所当然; 对于一号刀, 虽然其切削刃口存在一些缺口, 但其缺口下面的后刀面非常平滑, 所以这些缺口很像 PCBN刀具的负倒棱, 也相当锋利, 因而一号刀切削所得表面的刀痕也较细; 而三号刀的刃口呈锯齿状, 其刃口缺陷一直延伸到后刀面很深处, 不能像二号刀那样形成所谓的 ?负倒棱?, 所以其切削所得表面的刀痕较严重。
另外, 试验还对切削表面的粗糙度进行了测量, 发现一号 PCD刀具所得的切削表面粗糙最小, 其 Ra为0.9122μm, 而二号和三号 PCD刀具所得切削表面的粗糙度则大小相当, 它们的 Ra分别为 0.9769μm 和0.9755μm。由此可见, 刀具几何复映区交界处的刀痕及复映区内的划痕综合决定了加工工件表面的粗糙度。虽然二号 PCD刀具所得切削表面的划痕较三号刀要轻微, 但其切削刀痕较严重, 最终二号刀和三号刀一样, 其切削表面的粗糙度都不理想。
5 结论
PCD刀具加工有色金属时刀具刃口及后刀面质量对加工工件表面质量有着同等重要的影响作用, 它们共同决定了切削表面的质量。刃口质量越高, 在工件表面刀具几何复映区交界处留下的刀痕则越细, 切削表面质量越高; 后刀面质量越高, 在工件表面刀具几何复映区内留下的划痕就越少, 切削表面质量越高。
投稿箱:
如果您有机床行业、企业相关新闻稿件发表,或进行资讯合作,欢迎联系本网编辑部, 邮箱:skjcsc@vip.sina.com
如果您有机床行业、企业相关新闻稿件发表,或进行资讯合作,欢迎联系本网编辑部, 邮箱:skjcsc@vip.sina.com