硬质合金孔加工刀具的技术进展
2014-4-8 来源:数控机床市场网 作者:
摘要: 简要介绍了现代制造技术中常用孔加工刀具的种类、 硬质合金刀具的材料与制备。以钻头为例, 分析了刀具参数、 刃磨、 刃口钝化技术对切削性能的影响, 综述了硬质合金孔加工刀具技术的发展趋势。
关键词: 孔加工; 硬质合金刀具; 技术进展
1 引言
随着机械制造业的不断发展, 尤其是近年来我国汽车、航空、军工、模具等行业的快速发展, 对金属切削加工刀具的需求不断增大, 同时, 对刀具制造质量的要求也大大提高。在机械零件的切削加工中,孔加工占有较大比重, 约占机械零件加工总量的1/ 3[ 1]。硬质合金孔加工刀具因具有高切削速度、高加工效率、高耐用度和高可靠性等显著特点, 获得了越来越广泛的应用。随着数控机床、加工中心等现代加工设备的大量使用, 以及生产的自动化及高效化, 这种趋势将更趋明显。据国外统计资料显示, 在孔加工刀具的总产值中,硬质合金刀具的比例在不断增大。目前, 与工业发达国家相比, 我国硬质合金孔加工刀具在产品质量、刀具结构设计、刀具刃磨技术等方面尚存在较大差距, 制约了我国硬质合金孔加工刀具的发展, 影响了我国硬质合金孔加工刀具产品( 尤其是高端产品) 的市场占有率。因此, 努力提高硬质合金孔加工刀具的设计、制造和刃磨技术,对于提高我国孔加工的质量和效率、增加硬质合金孔加工刀具的国内外市场份额具有重要意义。
2 硬质合金孔加工刀具技术
2. 1 常用的孔加工刀具类型
机械零件上需要加工的孔通常包括直孔、阶梯孔、成型孔、具有特殊要求的孔等各种形式。根据零件的功能不同, 对不同结构的孔有不同的尺寸精度和表面质量要求。在机械加工中, 可以根据孔的结构和技术要求, 采用不同的孔加工方法, 如钻削、铰削、镗削等。常用的孔加工刀具种类如表 1 所示。
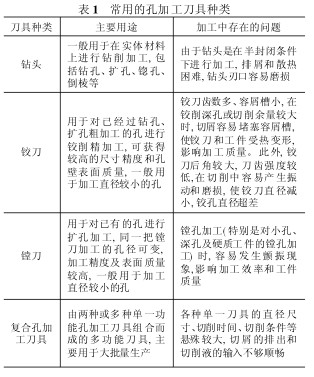
孔加工刀具的共同特点是: 由于受孔径限制, 又是在工件内部加工, 刀具的强度及刚性较差、排屑及冷却润滑困难。因此, 为了提高孔加工的生产效率、加工精度和刀具寿命, 就必须合理选择刀具材料, 采用先进的刀具设计和制造技术。
2. 2 硬质合金刀具材料与制备技术
钻头、铰刀和镗刀的主要材质为高速钢( HSS)和硬质合金(HM) 。高速钢刀具的特点是刃口锋利、韧性好; 硬质合金刀具硬度很高, 但韧性较差。高速钢与整体硬质合金刀具切削效率的比较见图 1。可以看出, 硬质合金刀具在切削速度、加工质量及切削效率上都优于高速钢刀具。
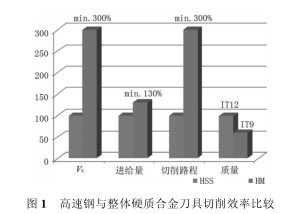
随着电子技术、精密机械工程、微型机械加工和金属成型技术的发展, 传统的硬质合金刀具材料已不能满足加工要求, 细晶粒、超细晶粒硬质合金的使用越来越多。制造超细晶粒及纳米晶粒硬质合金材料的关键是生产出超细粉、纳米粉以及在烧结时防止WC 晶粒长大。美国Nanodyne 公司用喷雾干燥转化工艺大量生产各种规格的WC2Co 混合粉, 其中最小粒度可达 20- 50nm。日本住友和东京钨公司用WO3+ C 直接碳化法生产出粒度 0.1- 0.2μm 的 WC粉。美国Dow 公司用快速还原碳化法大规模、低成本生产粒度0.2μm 的 WC 粉。虽然目前已能在实验室制备出粒度几纳米的 WC 粉及 WC2Co 混合粉, 但由于在烧结过程中 WC 粒子的长大, 还不能生产出粒度 0.1μm 的纳米晶粒硬质合金。为解决这一问题, 可采用快速加热、短时保温等工艺措施, 使WC 粒子来不及长大, 或添加抑制剂阻止 WC 粒子长大。日本住友煤炭开采株式会社研制的 DR. SIN -TER1000 系列电火花等离子烧结设备, 适合开发生产多种新型材料, 包括超细晶粒乃至纳米晶粒硬质合金。韩国Seung I Cha 等人采用 WC- 10Co 纳米复合粉进行了放电等离子烧结制备超细硬质合金材料的研究, 对材料微观结构和机械性能的分析结果表明, 在烧结温度为 1000° 时, 烧结体即可完全致密化, 无需添加抑制剂, 且合金的晶粒尺寸小于300nm, 这是传统烧结工艺无法达到的。
2. 3 硬质合金孔加工刀具参数
在孔加工中, 应用最广泛的加工方式是钻削加工。本文以钻头为例, 说明刀具参数对加工质量和刀具寿命的影响。影响钻头切削性能的因素很多,如钻头的前角、槽型、后角、螺旋角、横刃等, 这里对钻头的槽型及后角进行分析, 说明其对切削性能的影响。
(1) 槽型
钻头的槽型对其容屑、断屑、排屑性能以及刚度、切削稳定性等都有很大的影响。设计硬质合金钻头槽型时, 需要根据不同的被加工材料和表面质量要求, 合理设计槽型结构, 以满足断屑要求。近二十年来, 断屑槽的槽型结构不断改进, 相继开发出了直线刃、折线刃、曲线刃与曲面型、多面型凸起、凹坑型等型面相结合的断屑槽, 槽型曲面越来越复杂, 断屑性能也随之不断提高。例如, 吴新凉等人对几种典型的复合式槽型结构( 包括双槽结构、刀尖部分槽背向前突起及波浪形槽背结构) 进行了断屑试验研究, 结果表明, 复合式断屑槽兼具各种简单槽型的优点, 提高了刀具的断屑性能。龙新延等人建立了切削过程的仿真模型, 分析了刀具断屑槽型参数凸台高度和断屑槽宽深比( Wn/ H) 对切削过程的影响, 证明 Wn/H 的变化对切屑折断的影响较大, 在以小进给量切削加工塑性好的材料时, 可选择凸台高度较大的刀具断屑槽型。
(2) 后角
钻头的后角能减小工件加工表面与主后刀面之间的摩擦力。应根据不同的被加工材料、刀具种类以及刀具直径来选择不同的刀具后角。一般而言,后角随着刀具直径的增大而减小, 加工塑性材料和精加工时应选用较大的后角; 加工脆性材料和粗加工时应选用较小的后角。目前, 国内外硬质合金钻头的后角根据后刀面型式的不同, 分为一个后角和两个后角两种型式。AHNO刀具有限公司针对不同的工件材料来选取后刀面型式: 加工钢件时, 一般采用双弧面型式, 后角取 7°- 12°; 加工铸铁、铝合金时, 采用四平面型式, 第一后角取 6°-10°, 第二后角取 20° 。生产实践证明, 选取合适的后刀面型式, 可以提高刀具的防干涉能力和加工效率。
2. 4 硬质合金刀具的刃磨及刃口钝化
近年来, 随着中、小批量生产对生产效率、自动化程度以及加工中心性能的要求不断提高, 刀具刃磨技术、多轴数控刀具刃磨设备的发展带动了孔加工刀具的发展, 其中最典型的就是, 在机械生产中已应用多年、使用最为广泛的整体结构钻头刃磨技术逐渐成熟, 通过对钻头刃口的修磨和强化, 改善了钻削加工条件。
(1) 刃磨
金属切削刀具的刃磨既是刀具制造中的最后一道工序, 也是刀具重磨最重要的工序。刀具刃磨决定了刀具切削部分的形状及其几何精度, 是保证刀具切削性能和产品质量的关键。
一汽解放汽车厂引进数控万能工具磨床对刀具进行刃磨, 该机床采用五轴数控系统, 对钻头的切削刃部进行铲磨, 通过改进钻头的钻尖几何角度, 尝试提高钻头使用寿命, 经过多次试验后发现, 在锋角为130° 左右时加工平稳性最好, 加工工件的数量和质量明显提高。在对钻头横刃进行处理时, 采用大量切除方式铲磨横刃, 缩短横刃宽度, 使钻心的横刃与主切削刃接近十字交叉, 减小了钻削中的轴向力和转矩。郭延文等人将钻头后刀面刃磨成双曲面,形成 S 型横刃, 与锥面麻花钻相比, 这种钻型的轴向力平均下降了24%, 扭矩平均下降了 25%, 钻孔的定心性和刀具耐用度都得到了改善。
(2) 刃口钝化
经普通砂轮或金刚石砂轮刃磨形成的刀具刃口, 存在不同程度的微观缺口。通过对刀具刃口进行钝化, 能有效提高刃口强度、刀具寿命和切削过程的稳定性。现代高速加工和自动化机床对刀具的切削性能和稳定性提出了更高要求, 特别是涂层刀具,在涂层之前必须经过刃口钝化处理, 才能保证涂层的牢固性和使用寿命。K. D. Bouzaki 等人采用有限元仿真与试验相结合的方法, 分析了刀具刃口钝化半径对涂层刀具寿命的影响。Yung- Chang Yen 等人采用有限元仿真方法, 研究了刀具刃口半径对切削力、切削温度等加工要素的影响。刘月萍通过有限元仿真与试验相结合的方法, 研究了铣削钛合金Ti6Al4V 刀具的不同刃口钝化结构及表面质量完整性。刃口钝化技术是提高刀具寿命、减少刀具消耗的有效措施, 在经济性和技术性两方面都行之有效。
3 硬质合金孔加工刀具的发展趋势
3. 1 硬质合金刀具材料
随着机械加工技术的不断发展, 对孔加工的要求日益提高, 特别是在大批量的孔加工中, 为了获得高精度的孔轴配合, 对孔的尺寸精度、几何形状及表面粗糙度提出了更高要求, 而传统的硬质合金刀具材料已难以满足大批量、高精度、高效率生产的需要。纳米硬质合金刀具是能够适应这种需要的一种精密孔加工刀具。但是, 由于生产工艺不成熟、价格昂贵以及烧结过程中纳米晶粒容易疯长等原因, 迄今世界上还没有一家公司能实现粒度 100nm 硬质合金材料的工业化规模生产。因此, 今后还需要进一步研究纳米硬质合金材料的工业化生产与应用。此外, 国内在结合剂以 Ni 代 Co 上的研究主要集中在矿用硬质合金方面, 在硬质合金刀具材料方面还没有开发出正式牌号, 因此, 还需要对材料的高温性能、耐磨性以及抗崩刃性等一系列问题进行深入、系统的研究。
3. 2 刀具涂层技术
由于孔加工技术的快速发展, 涂层硬质合金钻头、 铰刀等孔加工刀具的使用量大幅增加, 此外, 随着对刀具重磨要求的提高, 越来越多的重磨刀具需要进行重新涂层, 使涂层技术的应用有了更广阔的前景。由于单一涂层材料难以满足提高刀具综合性能的要求, 因此涂层成份将趋于多元化、复合化。德国Guhring 公司和瑞士Vilab 公司联合开发了MOVIC 涂覆技术( 类似于表面处理技术) , 制备出的涂层主要由二硫化锰材料构成, 具有很好的润滑性能( 不粘结) , 该技术正在继续开发和推广运用之中。成都工具研究所开发的 Ti-C-N-O-Al 和Ti-C-N-B 两个系列共三种高性能多元复合涂层, 具有较好的复合机械性能和优良的切削性能。豪泽技术涂层进一步发展了其高功率脉冲磁控溅射技术(HIPIMS 和 HIPIMS+ ), 为改善涂层刀具的精度提供了更多机会。今后的发展趋势是, 通过工艺、材料和结构创新, 进一步改进各类涂层的性能, 如将多弧工艺与溅射工艺相结合, 优化涂层结构, 开发多层涂层以提高其韧性和结合力, 添加合金元素(如铬、锆、钒、硼、铪、硅等), 提高涂层的硬度、韧性、化学稳定性、润滑性等, 同时努力开发纳米多层涂层。
3. 3 刀具表面微观质量
随着现代刀具制造技术的发展, 对刀具表面质量的要求越来越高, 要求刀具的刃口及排屑槽表面非常光滑。提高刀具磨削质量, 减少排屑槽表面的细小裂纹, 能有效减少应力集中, 防止在加工过程中发生崩刃。同时, 排屑槽表面越光滑, 切屑流动就越顺畅, 切屑的温升也越低, 刀具就可以采用较高的切削速度, 并能提高刀具寿命。由于孔加工刀具( 特别是深孔钻) 在加工中排屑比较困难, 因此要求刀具排屑槽具有较高的表面微观质量, 使切屑能快速排出,从而提高孔加工的精度。国外利用磨料超声振动研磨技术, 来提高刀具排屑槽的表面光洁度, 当排屑槽表面粗糙度值达到 R a0.08- 0.02μm 时, 可以获得很高的孔加工精度, 还能将切削效率提高 10% , 国内也将致力于这方面技术的研究与开发。
4 难加工材料刀具技术
为了满足机械产品向高性能、多功能、高质量的方向发展, 以及产品结构轻量化、零件尺寸微型化的需求, 具有高硬度、高韧性和高耐磨性的难加工材料(如钛合金、镍基合金、超耐热合金、陶瓷等) 的使用越来越多。能否高效加工这些材料, 直接关系到我国汽车、航空航天、能源等重要工业部门的发展和制造业的整体水平的提升, 也是对切削加工技术的最大挑战。在难加工材料的孔加工中, 切削轴向力大,钻头等刀具磨损剧烈、易产生较大挠曲, 导致钻孔偏斜, 影响钻孔精度。因此, 需要大力发展具有优异耐磨性和较低摩擦系数的硬质合金刀具材料, 选择与难加工材料特点相适应的前角、后角、切入角等刀具几何形状, 并对刃尖进行适当钝化处理, 以提高切削性能、延长刀具寿命。
5 结语
孔加工是机械加工中不可或缺、应用广泛的基础加工技术, 对产品的质量、成本等具有重要影响。
随着产品的小型化和高性能化, 对孔加工技术的要求越来越高, 为了充分发挥数控加工、高效加工、自动化加工等现代加工技术的优势, 孔加工刀具必须满足高切削速度、大进给量、大切深、刀具寿命长等苛刻要求。硬质合金孔加工刀具因具有高速度、高效率、高寿命、高可靠性等优势, 正取代高速钢刀具,成为孔加工的主流刀具。随着硬质合金材料细化、涂层技术的发展, 以及刀具表面微观质量的提高, 孔加工的质量和效率将会进一步提高。
投稿箱:
如果您有机床行业、企业相关新闻稿件发表,或进行资讯合作,欢迎联系本网编辑部, 邮箱:skjcsc@vip.sina.com
如果您有机床行业、企业相关新闻稿件发表,或进行资讯合作,欢迎联系本网编辑部, 邮箱:skjcsc@vip.sina.com
更多相关信息