西门子802D系统数控机床电动刀架PLC控制
2020-8-5 来源:三门峡职业技术学院 作者:雷楠南
摘 要: 分析了西门子802D系统数控车床电动刀架的换刀控制过程, 系统地研究了电动刀架换刀控制子程序、列出了相关控制接口信号。 以CK6140数控车床为例,编制了四工位电动刀架换刀控制PLC程序。
关键词:西门子; 数控系统; 电动刀架; 换刀控制; PLC程序
一、引 言
数控车床的自动换刀过程通常由 PLC 控制回转刀架来实现,在实际使用过程中回转刀架有两种:电动回转刀架和液压回转刀架。电动回转刀架因为结构简单、易于控制且经济性好等原因,广泛应用于经济型数控车床。液压刀架结构较复杂、但刀具容量大、换刀速度快,且定位准确,所以广泛应用于高档数控车床[1]287-289。电动回转刀架通常由底座、刀架体、驱动电机、蜗轮蜗杆、螺纹升降机构、端面齿牙盘和刀位检测装置等部件组成,刀具可通过刀架体上部的螺钉夹紧于刀架体上,刀架定位利用端面齿牙盘实现[2]231-232。在数控车床上,电动刀架换刀控制通常涉及 CNC 辅助功能 T 指令控制与 PLC 控制,所以换刀控制 PLC 程序设计时主要考虑 CNC 系统信号与 PLC 信号处理。以配置西门子 802D 系统的数控车床为例,因为 PLC 集成在数控系统上,所以编制换刀控制 PLC 程序时,要先分析控制要求,弄清编程涉及的接口信号,然后可参照西门子系统换刀控制子程序编制出合适的换刀控制程序。
二、西门子 802D 系统数控车床电动刀架换刀控制流程
(一)电动刀架换刀控制过程
电动刀架换刀的一般过程为:刀架抬起、刀架转位、刀架定位和刀架锁紧四步[2]231-232。电动刀架换刀控制有两种,手动换刀与自动换刀:手动换刀指的是在手动 JOG 操作方式有效时,按下换刀按键,刀架体转位至下一把刀具;自动换刀,即当 CNC 系统在执行数控加工程序过程中,读入并执行换刀 T 指令时,刀架实现正转换刀的方式。以四工位的电动刀架为例,在自动换刀方式下,CNC 系统读入编程刀号后,首先应判断编程刀号,若编程刀号不为 0、不等于当前刀号且 T 代码正确(T 代码指令刀号范围应为 1 至 4)情况下才能进行换刀。当 T 指令刀具换刀到位后,刀架电机停止转动并延时,延时时间到后刀架电机进行反转锁紧,换刀过程完成。手动换刀时,按下换刀按键,刀架转位至下一把刀具,控制流程较为简单。为便于换刀 PLC 程序设计,绘制出数控车床电动刀架的控制流程如图 1 所示[3]92-95。
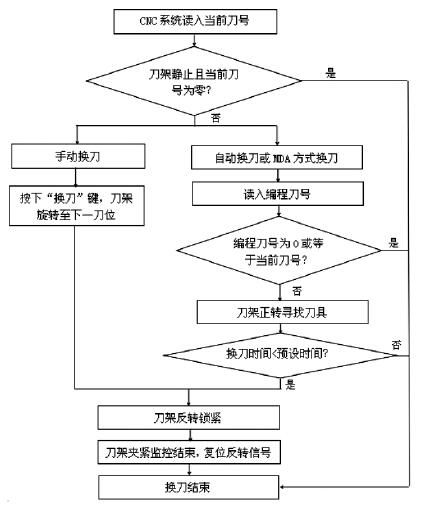
图 1 电动刀架换刀控制流程
(二)西门子 802D 系统电动刀架换刀控制相关信号
在实现电动刀架换刀控制时,西门子数控系统厂家为方便用户使用,专门设计了 PLC 子程序库。在西门子 802D 系统上,涉及电动刀架控制的子程序为 SBR46(TURRET1)[4]148-150。一般情况下,在实际机床使用过程中,用户会根据刀架控制要求对子程序进行修改和完善。但是,不论是基于子程序修改方式或重新编制换刀控制程序,在实现电动刀架控制时所涉及的控制信号及编程地址应保持一致,802D系统涉及换刀控制的信号如表 1 所示。
表 1 802D 系统电动刀架控制信号表
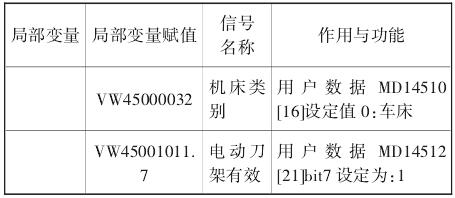
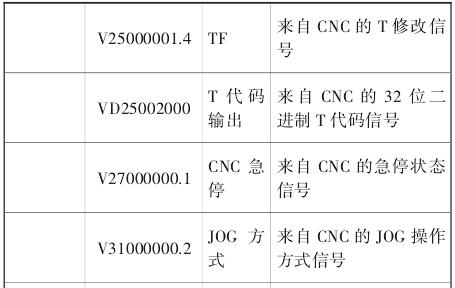
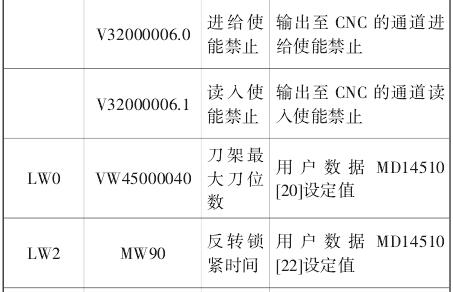
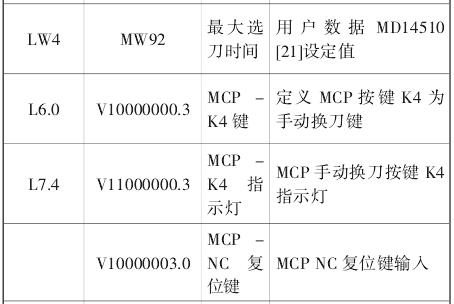
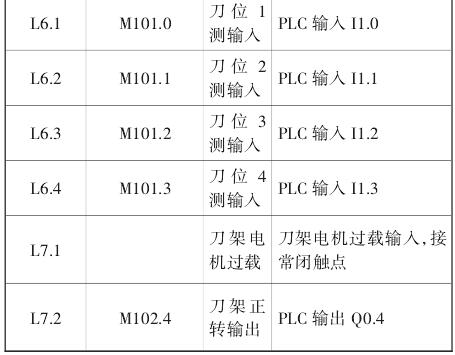
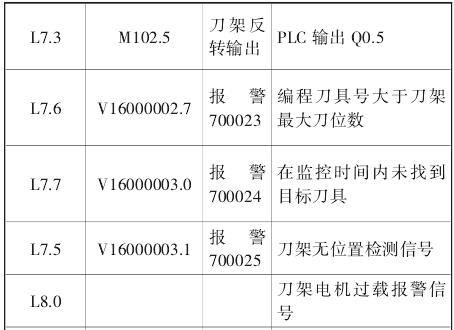
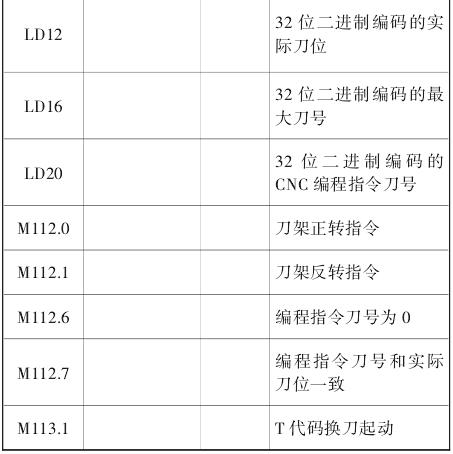
三、电动刀架换刀程序编制
根据前述电动刀架换刀控制流程,下面以CK6140 数控车床电动刀架换刀控制为例,编制换刀控制程序。在编制换刀控制 PLC 程序时,首先应编制刀位检测程序如图 2 所示。在自动换刀过程中,为防止编程 T 代码错误,通常要编制程序读入用户设定的最大刀位数。因此,在图 2 所示第一行程序便是将用户数据 MD14510[20]设定的 16 位二进制格式“最大刀位数”转换成 32 位二进制格式并保存在局部变量 LD16 上。如此处电动刀架为四工位,则最大刀位数设定值为 4。在后续换刀程序中,CNC 系统读入编程 T 代码后,要将 T 代码数值与 LD16 中数值进行比较,只有 T 代码数值小于 LD16 中设定的最大刀位数值时,T 代码才有实际意义。因为刀架为四工位电动刀架,所以编程时只需读入四个刀位信号。由于机床类型为数控车床,所以 CNC 用户数据MD14510[16]应设定为“0”,即变量 VW45000032 值为“0”,该触点接通;若 CNC 用户数据 MD14510[11]bit7 设定 为 “1” 时 , 表 示 电动 刀架 有 效 即 变 量VW45001011.7 值为“1”,该触点接通;由此便可将局部变量 L6.1 至 L6.4 输入的刀位检测信号转换为32 位二进制格式数据存储在 LD12 中。在生产实际中,刀架无论处于某一刀位必有一个位置检测信号。如果刀架处于停止状态则表明刀架无正反转信号输入,即 M112.0、M112.1 为“0”。此时,若刀架无位置检测信号输入,则 LD12 中数值为 0,从而接通局部变量 L7.5,使 CNC 报警变量 V16000003.1 为“1”,显示用户报警 700025:“刀架无位置检测信号”
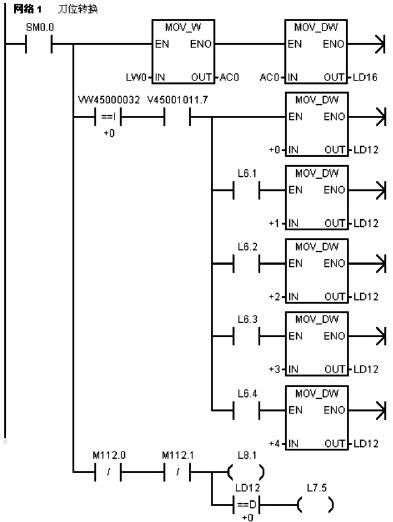
图 2 刀位转换控制 PLC 梯形图程序设计
当数控车床通过编程 T 代码指令实现自动换刀时,可编制如图 3 所示 PLC 程序。在西门子 802D系统上,当 CNC 读入编程 T 代码指令时,其译码数值存储于变量 VD25002000。同时,来自 CNC 的 T代码修改信号 TF 选通,即变量 V25000001.4 为“1”。利用该触点接通的上升沿信号可将编程指令中的32 位二进制 T 代码刀号读入并输出到 LD20。若编程 T 代码数值小于用户设定的最大刀位数,即 LD20数值小于刀架刀位设定值 LD16,则表示编程指令中指定的刀号正确,通过取反指令使“编程刀具号大于刀架最大刀位数”信号 L7.6 为“0”;接着,要进一步判断 LD20 中的 T 代码数值是否为“0”;若为“0”则“编程刀号为 0”信号 M112.6 为“1”,由于实际生产中无 0 号刀,所以电动刀架无换刀动作。最后,再利用一致性判别指令判断存储于 LD20 中的编程指令T 代码数值与 LD12 中的实际刀位 T 代码数值是否相等,若相等则表示编程刀位到达,即“编程刀号与实际到位一致”信号 M112.7 为“1”,无需换刀。由此可见,只有当 LD20 中的 T 代码数值小于刀架刀位设定值 LD16,且 LD20 中的 T 代码数值不为“0”,电动刀架才具备换刀条件。
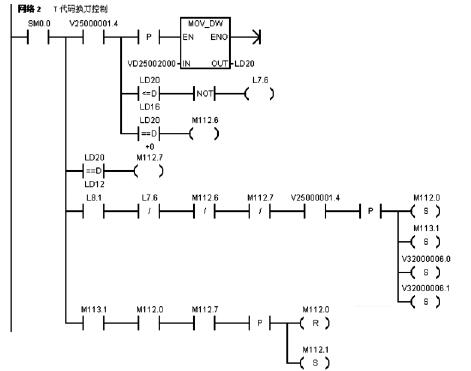
图 3 自动换刀控制 PLC 梯形图程序设计
当电动刀架满足换刀条件、执行自动换刀时,应编制 PLC 程序实现刀架正转换刀与反转锁紧控制如图 3 所示后续程序。由于换刀前,刀架处于停止状态,所以“刀架停止”信号 L8.1 为“1”;当 LD20 中的T 代码数值小于刀架刀位设定值 LD16,且 LD20 中的 T 代码数值不为“0”时,则 L7.6 信号为“0”、M112.6 为“0”;若 LD20 中的编程指令 T 代码与LD12 中的实际刀位 T 代码不相等,则 M112.7 信号为“0”;此时,如果 T 代码修改信号 TF 选通时V25000001.4 为“1”,可利用上升沿信号置位“刀架正转”信号 M112.0 和“T 代码自动换刀起动”信号M113.1,实现刀架回转换刀。刀架回转换刀时,应禁止下一程序段的读入和进给,使 CNC 进入辅助功能执行等待状态,所以编程时必须使 CNC 进给禁止使能 信 号 V32000006.0、 读入使能禁止信 号V32000006.1 置位为“1”。当换刀结束时,即 LD20 中的编程指令 T 代码与 LD16 中的实际刀位 T 代码相等,则表示编程的刀位到达,“编程刀号与实际到位一致”信号 M112.7 变为“1”,利用最后一行程序执行上升沿信号,复位“刀架正转”信号 M112.0,同时置位“刀架反转”信号 M112.1,使刀架反转锁紧。
反转锁紧时间 LW2 时,T14 常开触点接通便可复位“刀架反转”信号 M112.1、“T 代码换刀起动”信号M113.1;同时,要结束辅助功能控制,进行下一程序段的读入和进给,就必须复位进给禁止使能信号V32000006.0 和读入使能禁止信号 V32000006.1。此外,当“T 代码换刀起动”信号 M113.1 为“1”,且“刀架正转”信号 M112.0 为“1”时,可接通定时器 T15用于监控最大选刀时间。若刀架正转换刀过程时间超过用户数据 MD14510 [21] 设定的最大换刀时间LW4,定时器 T15 常开触点接通便可复位“刀架正转”信号 M112.0,停止刀架转动;并置位 L7.7 并使报警变量 V16000003.0 为“1”,使 CNC 显示 700024报警:“在监控时间内未找到目标刀具”。
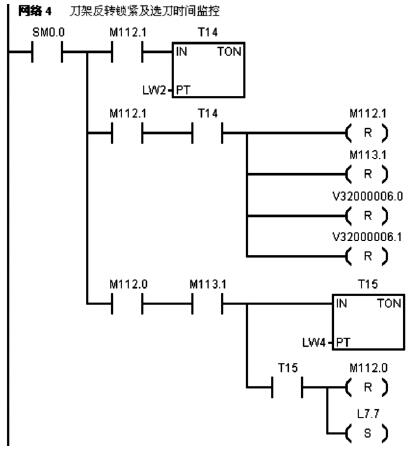
图 4 手动换刀控制 PLC 梯形图程序设计
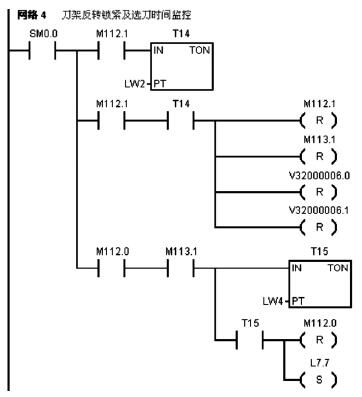
图 5 刀架反转锁紧及选刀时间监控 PLC 梯形图程序设计
数控车床采用手动换刀方式时,可编制手动换刀控制 PLC 程序如图 4 所示。只要将 CNC 操作方式选择在 JOG 方式,则变量 V31000000.2 信号为“1”。由于换刀起动前,刀架处于停止状态,所以“刀架停止”信号 L8.1 为“1”。当按下机床操作面板上的换刀按键 K4 时,L6.0 信号为“1”。利用该信号的上升沿可置位“刀架正转”信号 M112.0 为“1”,起动刀架回转;松开换刀按键时,L6.0 信号为“0”,利用该信号的下降沿可置位“刀架反转”信号 M112.1 为“1”,使刀架反转锁紧;同时复位“刀架正转”信号M112.0 为“0”,清除刀架正转信号。
电动刀架在换刀过程中,为了保证刀架选刀及锁紧正确,通常设计刀架反转锁紧及最大选刀时间监控 PLC 程序如图 5 所示。不论是自动换刀还是手动换刀,只要“刀架反转”锁紧信号 M112.1 为“1”,首先会接通反转锁紧时间控制定时器 T14;当定时器 T14 定时时间达到用户数据 MD14510[22]设定的反转锁紧时间 LW2 时,T14 常开触点接通便可复位“刀架反转”信号 M112.1、“T 代码换刀起动”信号M113.1;同时,要结束辅助功能控制,进行下一程序段的读入和进给,就必须复位进给禁止使能信号V32000006.0 和读入使能禁止信号 V32000006.1。此外,当“T 代码换刀起动”信号 M113.1 为“1”,且“刀架正转”信号 M112.0 为“1”时,可接通定时器 T15用于监控最大选刀时间。若刀架正转换刀过程时间超过用户数据 MD14510 [21] 设定的最大换刀时间LW4,定时器 T15 常开触点接通便可复位“刀架正转”信号 M112.0,停止刀架转动;并置位 L7.7 并使报警变量 V16000003.0 为“1”,使 CNC 显示 700024报警:“在监控时间内未找到目标刀具”。如图 6 所示 PLC 程序为电动刀架控制信号输出程序。
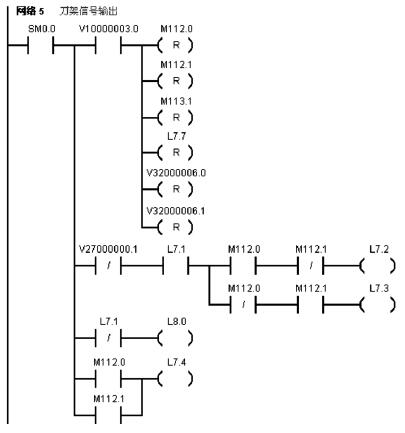
图6 刀架输出信号PLC 梯形图程序设计
在电动刀架换刀过程中,若按下机床操作面板 MCP 上的 NC 复位按键,则 V10000003.0 信号为“1”,可直接复位“刀架正转”信号 M112.0、“刀架反转”信号 M112.1、“T 代码换刀起动”信号 M113.1、报警 信 号 L7.7, 以 及 复 位 进 给 禁 止 使 能 信 号V32000006.0 和读入使能禁止信号 V32000006.1。当松开急停按钮且刀架电机不发生过载情况下,急停状态信号 V27000000.1 为“0”、“刀架电机过载输入”信号 L7.1 为“1”;若“刀架正转”信号 M112.0 为“1”、“刀架反转”信号 M112.1 为“0”,则“正转输出”信号L7.2 为“1”;同 理,若“ 刀架 反 转 ”信号 M112.1 为“1”、“刀架正转”信号 M112.0 为“0”,则“反转输出”信号 L7.3 为“1”;程序中串联 M112.0、M112.1 的常闭触点用于正反转输出的互锁控制。当按下急停按钮时,急停状态信号 V27000000.1 为“1”;或刀架电机发生过载情况时,“过载输入”信号 L7.1 为“0”。当发生急停或刀架电机过载任意一种情况时,均可断开正反转信号输出。此外,刀架电机过载时,“过载输入”信号 L7.1 为“0”,可利用 L7.1 的常闭触点接通 L8.0,输出刀架电机过载报警信号。刀架正反转信号正常情况下,可接通 L7.4,作为换刀按键 K4 指示灯输出信号。电动刀架换刀控制 PLC 程序一般由上述几部分组成,用户编程时可根据控制要求自行编写,也可基于西门子系统提供的子程序进行修改以达到控制目的。
四、结语
文中详细分析了数控车床电动刀架的换刀控制流程,并以西门子 802D 系统为例介绍了电动刀架换刀控制相关接口信号。然后,以 CK6140 数控车床四工位电动刀架换刀控制为例,介绍了换刀控制PLC 程序编制方法。目前,西门子数控系统 PLC 编程技术资料相对较少、程序编制复杂且较难理解,通过完整的换刀程序编制及说明,一方面可为编程人员提供参考,另一方面在涉及到换刀控制系统故障时,可帮助数控维修人员识读相应 PLC 程序,迅速判断故障点,排除故障。
投稿箱:
如果您有机床行业、企业相关新闻稿件发表,或进行资讯合作,欢迎联系本网编辑部, 邮箱:skjcsc@vip.sina.com
如果您有机床行业、企业相关新闻稿件发表,或进行资讯合作,欢迎联系本网编辑部, 邮箱:skjcsc@vip.sina.com
更多相关信息