基于开放式数控系统平台的空间刀具半径补偿技术实现
2018-8-6 来源:转载 作者:李传军,王立萍,刘 强,雒新宇
摘要:空间刀具半径补偿技术是数控系统实现复杂零件加工的核心技术。在基于曲面直接插补的空间刀具半径补偿中,使用 3 次 B 样条拟合刀位文件中的刀位点、切触点及刀轴矢量来获取刀轨的参数样条表示,实现空间刀具半径补偿功能。通过基于 UG 后置处理的加工轨迹,编制空间刀具半径补偿算法系统软件进行模拟,并在搭建的基于 Twin CAT 的开放式数控系统平台上进行加工验证,满足复杂零件的加工质量要求。此方法为数控系统的空间刀具补偿算法研究提供可行性验证。
关键词:空间刀具半径补偿;曲面直接插补;3 次 B 样条;开放式数控系统平台;仿真验证
1、 引言
刀具补偿技术是数控系统的核心技术之一,空间刀具补偿技术问题的解决对开发新原理数控机床有极其重要的作用。基于曲面直接插补的空间刀具半径补偿与传统的空间刀具半径补偿有很大的不同。传统的空间刀具半径补偿针对的是微小直线段或微小圆弧段的刀具补偿,此时只需要对微段的首末端点计算补偿值即可完成整个微段的刀具半径补偿,此时可以通过给出刀具在首末端点处的切触点作为已知条件来计算补偿量。基于曲面直接插补的空间刀具半径补偿是在实时插补过程中实时计算每个插补点对应的刀具补偿量从而实现刀具半径的实时补偿。而要在插补过程中计算刀具半径补偿量需要一些已知量来辅助计算,如刀具切触点坐标、前倾角和侧倾角等。目前的 CAD/CAM 系统支持输出直线逼近的多轴加工代码,可以得到刀位坐标、刀轴矢量及切触点矢量,尚不支持输出直接使用参数样条的描述形式,因此通过研究空间曲面直接插补算法和刀具轨迹的参数样条拟合,计算实现空间具半径补偿并进行了模拟和实验加工验证得到很好地效果。
2 、刀轨的参数样条拟合
为了实现基于曲面直接插补的空间刀具半径补偿,首先就需要获取刀轨的参数样条表示。通过使用 3 次 B 样条拟合刀位文件中的刀位点、切触点及刀轴矢量,把拟合的结果用微分几何中的参数样条表示。使用 UG 可以获取的使用直线逼近复杂曲线的刀位文件格式为:GOTO/X,Y,Z,I,J,K,U,V,W;其中(X,Y,Z)为刀位点坐标,是绝对坐标值,代表曲面铣削刀具(球形刀、平底铣刀或环形铣刀)的刀具底端中心点或刀具端点切削工件时切触点坐标,其数值为工件坐标系内容;(I,J,K)在 CAM 软件生成刀具轨迹时表示刀具方向单位矢量的位置,具体数值满足 I2+J2+K2=1,表示其空间位置;(U,V,W)为刀具与工件构成的几何模型中刀具与工件的切触点坐标。CAM 软件(UG 等)生成的刀位文件通过提取,可以得到轨迹上的刀位点、(I,J,K) 表示的刀轴方向矢量坐标和通过矢量运算得到的切触点数据,其坐标可以表示为(Oi,Di,Pi),其中 i=0,1,2,…,m。在参数样条曲线的多轴插补中,一般采用双参数样条的形式来确定刀轴矢量,如图 1 所示。
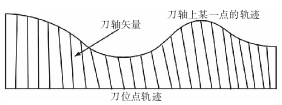
图 1 双参数样条
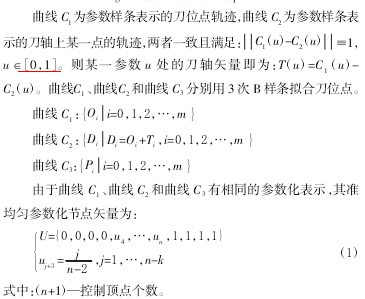
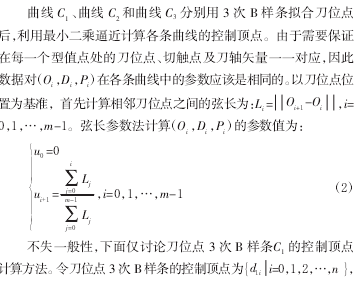
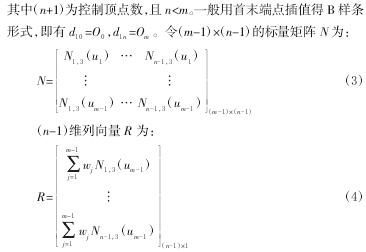
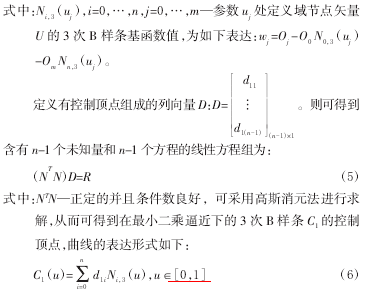
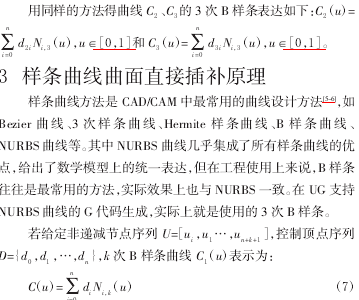
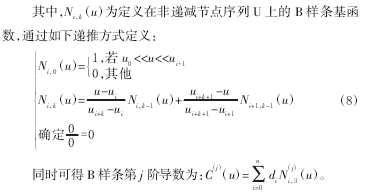
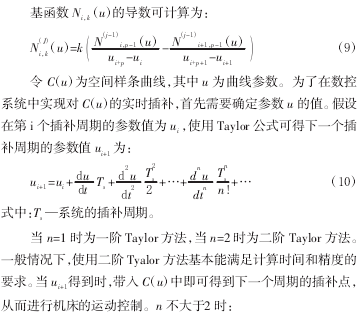
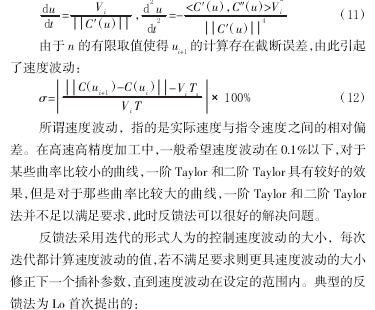
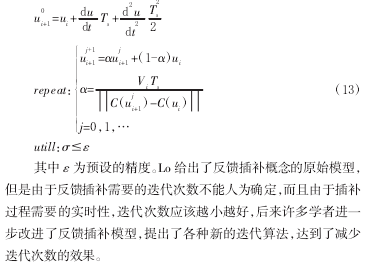
4 、基于曲面直接插补的刀具半径补偿原理
插补得到的插补点还不能直接输出给伺服系统进行位置控制。通常刀具半径补偿指的是在插补之前根据刀具信息对轨迹进行偏置,由数控系统的插补器对偏置后的曲线进行插补,这叫做插补前刀补。未来数控系统通过各种传感装置能在线实时获取刀具信息,因此在实时插补过程中同时进行刀具半径补偿成为可能。插补前刀具半径补偿只能根据预设的刀具信息进行刀具半径补偿,如果在加工过程中刀具由于磨损或者其他原因导致刀具几何信息发生改变(虽然非常微小),就可能造成加工质量的下降。插补后刀补,即在插补点生成之后根据刀具的几何信息进行刀补。这样做的好处是能实时根据刀具信息进行刀具补偿,从而考虑刀具加工磨损情况,提高加工质量。通过第 1 部分我们得到刀轨的参数曲线形式 C1、C2和 C3。首先通过第 2 部分中的插补算法获取第 i 个插补周期的插补参数,此时可以得到第 i 个插补周期中的刀位点、刀轴矢量及切触点为:
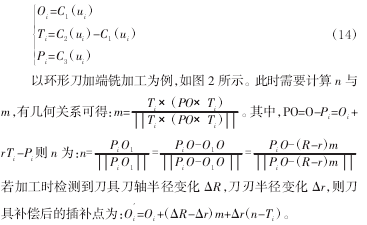
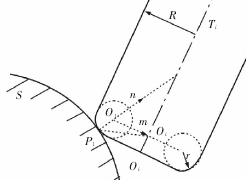
图 2 环形刀加端铣加工
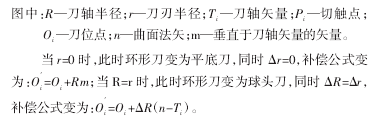
5、 仿真分析与加工验证
为了验证基于曲面直接插补的刀具补偿算法在实际加工中的效果,以某一航空发动机叶片曲面的一段加工路径为例进行仿真分析与验证。示例五轴加工代码中截取的一段叶片加工刀具轨迹,其中生成刀位文件时使用的为直径为10mm 的球头刀,如图 3 所示。曲线 1 为切触点轨迹,即加工刀具切削被加工叶片曲面的轨迹。曲线 2 为刀位点轨迹,及数控系统中插补器需要插补的曲线。曲线3 为刀轴上某一点的轨迹。曲线 4 为刀轴矢量。首先根据第 1 部分给出的刀轨参数样条拟合方法得到曲线 1、曲线 2 和曲线 3 的参数样条表示 C1(u)、C2(u)和 C3(u)。仿真时令插补周期 Ts=1m s,进给速度为 F=100m m /s,使用 MATLAB 编写仿真程序,应用第 2部分中给出的 Taylor 二阶方法进行插补,最终得到 667 个插补点。插补过程中的速度波动,如图 4 所示。

图 3 基于曲面直接插补的刀具补偿算法验证
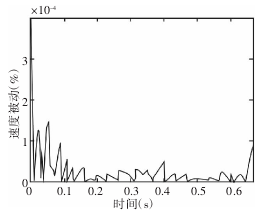
图 4 插补过程中的速度波动
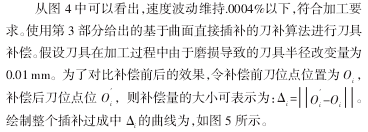
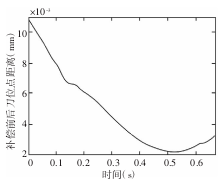
图 5 补偿前后刀位点距离
由图 5 可以看出,补偿前后刀位点距离最大可达 10.83μm,这在叶片曲面的高精度加工中,基于曲面直接插补的刀具半径补偿是对数控加工精度提高是非常有效的。在基于 Twin CAT 开放式数控系统平台上,编制直线与直线,直线与圆弧的刀具补偿功能程序并加工,如图 6 所示。
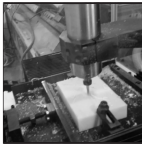
图 6 开放式数控系统加工平台
6 、结语
以数控系统空间刀具半径补偿为研究对象,利用刀具矢量和方向矢量,在基于曲面直接插补的空间刀具半径补偿中,通过使用 3 次 B 样条拟合刀位文件中的刀位点、切触点及刀轴矢量来获取刀轨的参数样条表示,实现了空间刀具半径补偿,并在搭建的基于 Twin CAT 的开放式数控系统平台上进行算法仿真和加工验证,能满足加工质量要求。为数控系统的空间刀具补偿算法研究提供可行性验证。下一步研究方向:进一步改进刀具补偿算法模型,并结合曲面直接插补理论“一步式”插补前提下,对插补过程中的实时刀具补偿优化,分析误差原因和寻找减少误差的方法,使其更加与工程实际相一致。
来源:(1.承德石油高等专科学校,河北 承德 067000;2.中国农业大学 工学院,北京 100083;3.北京航空航天大学 机械工程及自动化学院,北京 100191)
投稿箱:
如果您有机床行业、企业相关新闻稿件发表,或进行资讯合作,欢迎联系本网编辑部, 邮箱:skjcsc@vip.sina.com
如果您有机床行业、企业相关新闻稿件发表,或进行资讯合作,欢迎联系本网编辑部, 邮箱:skjcsc@vip.sina.com
更多相关信息