五轴数控加工3D 刀具补偿及其后置处理方法
2018-7-17 来源:西安建筑科技大学 机电工程学院 作者:蔡安江,宋仁杰,杜金健,李林
摘要:为解决五轴数控加工过程中,由于刀轴矢量不断变化,刀具补偿方向无法确定引起刀具在三维空间中无法补偿的问题,提出一种基于前置与后置处理的五轴数控加工 3D 刀具补偿方法。针对具备3D 刀具补偿功能的数控系统,推导出五轴数控加工3D 刀具补偿的补偿矢量与补偿后刀位点坐标的矢量计算方程,并基于前置三维软件(UG)的前置处理,建立了控制刀位文件格式的函数,实现了 UG 前置处理在五轴数控加工模块下输出包含切触点在内的刀位文件。根 据 SIE-MENS 840D 数控系统实现3D 刀具补偿的数字控制(NC)指令格式要求,以非正交摆头转台五轴数控机床为例,通过逆向运动学变换提出具体的后置处理方法。基于智能制造软件IMSpost(后处理程序编辑器)平台和所提出的后置处理方法开发了专用后置处理器,自动获取了具有3D 刀具补偿矢量信息的 NC程序,基于仿真软件 VERICUT 平台对不同工况下整体叶轮仿真加工的结果进行对比。结果表明:当刀具因磨损发生尺寸变化时,采用提出的方法和开发的具有3D 刀具补偿功能的后置处理器所获取的 NC程序,可以将加工表面的欠切误差控制在0.1mm 以下,且无过切现象,有效地提高了五轴数控加工的精度和效率,避免了刀具磨损后发生刀具尺寸改变必须返回计算机辅助制造(CAM)系统重新生成刀位文件,以及再次进行后置处理的繁琐过程,验证了所提出的前置处理与后置处理方法的正确性和有效性。
关键词:机械工程;五轴数控加工;3D 刀具补偿;补偿矢量;刀位点坐标;数控系统;后置处理
0、引言
五轴数控加工是实现复杂自由曲面加工的重要方式,已广泛应用于航空航天、兵器、船舶、汽车等制造领域。针对二维轮廓加工,目前数控系统都具备刀具长度和刀具半径补偿的功能,然而在五轴数控加工过程中,由于切触点和刀轴矢量方向均不断变化,刀具半径补偿功能较难实现。目前,众多国内外学者对3D 刀具补偿技术进行了研究。针对具备五轴数控加工3D 刀具补偿功能的数控系统,梁全等分析了前置输出的 CLS文件格式与数控系统接受刀具补偿矢量的指令格式,通过后置处理解决了带刀具补偿矢量的五轴 NC代码编程问题;胡自化等介绍了侧铣加工的半径补偿方法;陈良骥等研究了在 CNC 系统中3D 刀具半径补偿的实现方法;Tung等针对带倾斜回转台的卧式机床,提出了通过后置处理实现三维刀具半径补偿方法。以上方法当刀具尺寸发生变化时均需重新进行后置处理,数控程序重用性差。徐汝峰等针对不具备五轴3D 刀具补偿功能的数控系统,研究了如何通过后置处理来实现3D 刀具半径补偿功能,但未对具备五轴3D 刀具补偿功能的数控系统提出相 关解决方法。目前国内外主要配置的数控系统(如 SIE-MENS 840D 系 统、Fanuc30i系 统 和 Heiden-hain iTNC530系统等)均已具备3D 刀具补偿功能,它们都自定义了接受3D 刀具补偿矢量的 NC 指令格式。但 CAM 软件(如 CATIA、UG 等)生成的刀位文件经过后置处理得到的 NC指令并不符合这些数控系统实现3D刀具补偿功能所 定义的指令格式。基于上述不足,本文针对具备五轴数控加工3D刀具补偿功能的数控系统,研究其基本原理及后置处理方法,解决如何生成具有 3D 刀具补偿矢量信息的 NC程序,实现五轴数控加工3D 刀具补偿。
1、3D刀具补偿的基本原理
由于刀轴矢量不变,二维刀具半径补偿的实质只是将切触点的坐标按其表面 的法向矢量 进行偏置,再对刀具中心点编程;而在 3D 刀具补偿中,由于刀轴矢量不断变化,刀位点的补偿矢量与二维刀具半径补偿不同,是通过切触点表面的法向矢量、刀具方向和刀具几何尺寸计算得出。下文分别对五轴数控加工中常用的端铣刀、球头铣刀和环形铣刀进行矢量分析,计算得出3D 刀具补偿的补偿矢量及补偿后的刀位点坐标,见下页图1。图 中:P 为 切 触 点,OP(x,y,z)为 刀 具 中 心点,即 刀 位 点,OC为 刀 心 点,O1为 刃 口 圆 心,P(px,py,pz)为切触点,R 为刀具半径,r、r1均为刃口半径,n(nx,ny,nz)为 切 触 点 表 面 的 法 向 矢 量,l(lx,ly,lz)为刀轴矢量,m(mx,my,mz)为垂直于刀轴方向的矢量,v(vx,vy,vz)为补偿矢量,以上矢量均为单位矢量,k为路径切线。
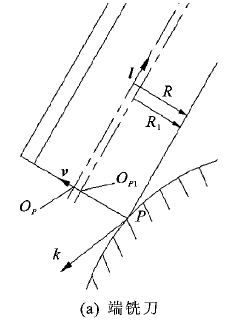
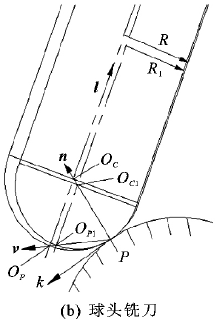
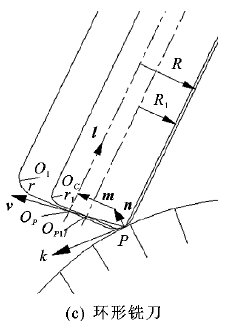
图1 3D刀具补偿模型
1.1 端铣刀的补偿矢量及补偿后的刀位点坐标计算
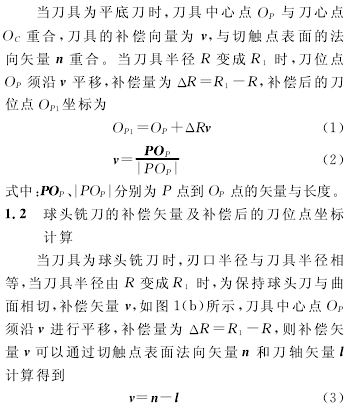
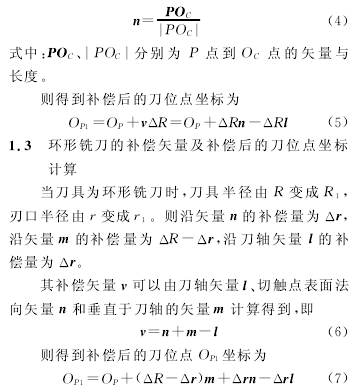
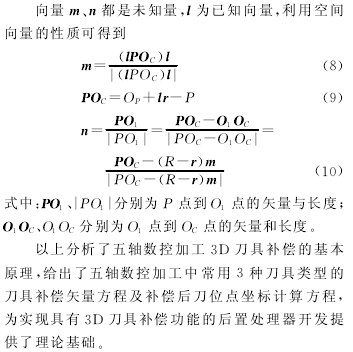
2、五轴数控加工3D 刀具补偿后置处理的实现
2.1 UG刀位文件及数控系统3D
刀具补偿 NC 格式分析
五轴数控加工3D 刀具补偿是在实际加工刀具尺寸发生变化的情况下,让原规划的刀具中心点沿着补偿矢量方向进行一定的偏置,从而保证切触点位置的正 确。基于 UG 前 置处理生 成 刀 路 轨 迹时,为满足五轴数控加工 3D 刀具补偿矢量计算所需要的刀位信息,需要对 UG 控制刀位文件格式的函数进行修改,使生成的CLS 文件包含切触点坐标。UG 前置处理控制刀位文件格式的函数主要针对 CLS文件中的关键字输出进行控制,如 GOTO、FEEDAT、RAPID 等。
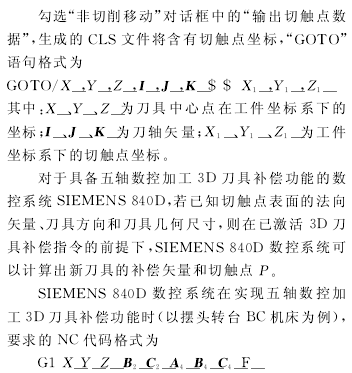
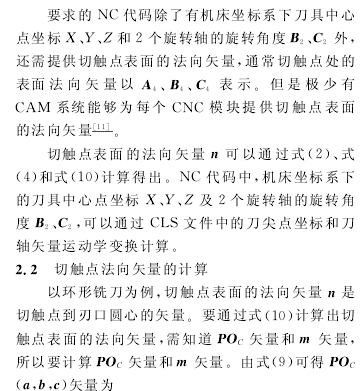
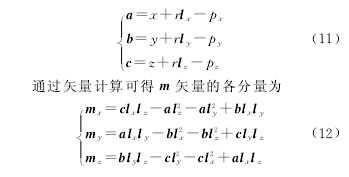
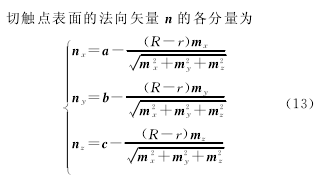
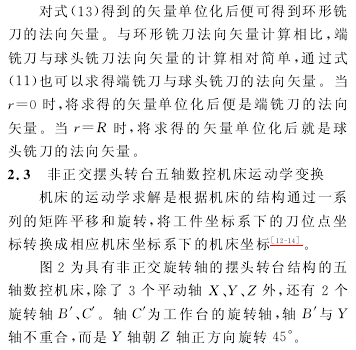
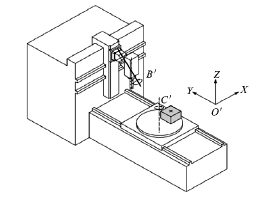
图2 非正交摆头转台结构
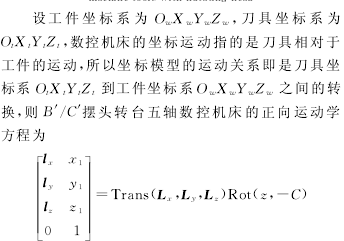
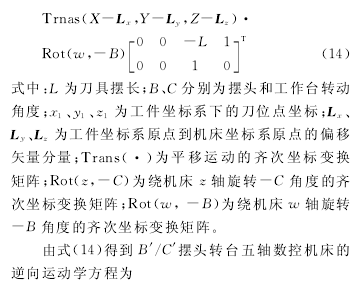
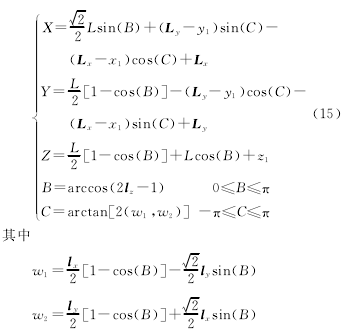
通过建立非正交摆头转台五轴数控机床各运动轴坐标与刀位数据之间的关系,基于逆向运动学求解方法,可以得到非正交摆头转台五轴数控机床平动轴坐标与转动轴坐标。
3、3D刀具补偿后置处理器的开发
基于IMSpost(后 处 理 程 序 编 辑 器)开 发 具 有3D 刀具补偿功能的后置处理器,需根据非正交摆头转台 类 五 轴 数 控 机 床 结 构 和 配 置 的 SIEMENS840D 数控系统程序格式进行设置、修改、子程序调用及宏程序编制等。宏程序编制实现后置处理的主要任务除刀位文件信息的读取、机床运动学变换求解、进给速度的校验、非线性运动误差校验外,还应完成切触点处表面法向矢量的求解。SIEMENS 840D 数控系统自定义了五轴数 控加工时实现3D 刀具的补偿指令,即刀具长度补偿指 令 为 TRAORI 和 半 径 补 偿 功 能 的 命 令 为CUT3DF。为实现3D 刀具补偿功能,在调用3D 刀具补偿指令后,除需知道机床坐标系下刀具中心点坐标和2个旋转轴的旋转角度外,还需提供切触点处表面的法向矢量。当刀具尺寸发生变化,把变化量添加到数控系统刀具补偿量里,SIEMENS 840D数控系统就可根据具有3D 刀具补偿格式的 NC 代码自动进 行 补 偿,从 而 提 高 了 数 控 加 工 程 序 的 重用性。以球头铣刀为例,利用IMSpost平台的宏命令功能,基于后置处理算法,主要通过在 GOTO/* 宏命令中编译宏程序实现刀具中心点坐标和旋转角度的输出;基于五轴数控加工 3D 刀具补偿矢量的矢量算法,可在 NORMAL/* 宏命令编译宏程序中实现切触点处表面法向矢量输出。NORMAL/* 宏命令中具体的代码如图3所示。

图3 编辑 NORMAL/* 宏命令
4、仿真加工验证试验
为验证本文方法的有效性,以整体叶轮为例,基于 UG 的前置处理,生成含切触点坐标的整体叶轮CLS文件。通过基于IMSpost开发的后置处理器生成具有3D 刀具补偿矢量的 NC程序,在某航空企业生产使用的基于 VERICUT 构建的 DMU 210FD虚拟仿真加工系统中进行了验证。仿真加工验证主要对整体叶轮叶片在3种工况下的加工结果进行比较。
(1)采用刀具半径及刀具切削部分的半径均为R=3mm的球头铣刀(生 成 刀 路 轨 迹 所 使 用 的 刀具),仿真加工结果如下页图4所示。
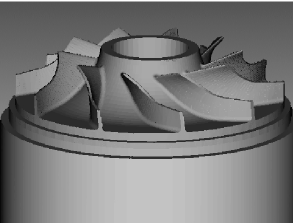
图4 R=3mm 球头铣刀仿真加工结果
(2)采用刀具半径 R=3 mm、刀具切削部分的半径r=2.5mm 的球头铣刀,用来表示刀具更换或磨损后的刀具。仿真加工结果如下页图5所示。
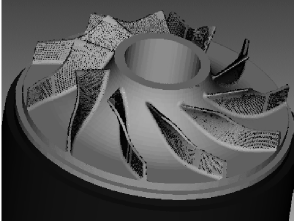
图5 R=3mm,r=2.5mm 球头铣刀仿真加工结果
(3)采用刀具半径 R=3 mm、刀具切削部分的半径r=2.5mm 的球头铣刀,设置刀具长度补偿值和刀具半径补偿值均为0.5mm,同时激活3D 刀具补偿指令。仿真加工结果如图6所示。
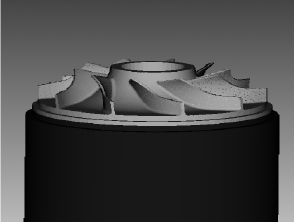
图6 R=3mm,r=2.5mm 的球头铣刀带补偿的仿真加工结果
由图5可以看出,当刀具尺寸发生变化时,叶片表面有明显的欠切,且欠切误差都在0.1mm 以上,但无过切现象。由图6 可以看出,在激活 3D 刀具补偿指令的情况下,即使刀具尺寸发生变化,工件的加工表面并没有出现过切和欠切现象。对比图4和图6可知,本文提出的 3D 刀具补偿及其后置处理方法有效.
5、结语
(1)研究了五轴数控加工 3D 刀具补偿的基本原理,针对3种常用类型刀具分别推导出五轴数控加工3D 刀具补偿的补偿矢量与补偿后刀位点坐标矢量计算方程,为实现五轴数控加工具有 3D 刀具补偿功能的后置处理器开发提供了理论基础。
(2)基于 UG 的前置处理,建立了控制刀位文件格式的函数,实现了在五轴数控加工模块下可输出包含切触点在内的刀位文件,解决了五轴数控加工3D 刀具补偿后置处理所需的刀位信息问题,为具有3D 刀具补偿功能的后置处理器的开发奠定了技术基础。
(3)以非正交摆头转台五轴数控机床为例,基于SIEMENS 840D 数控系统实现3D 刀具补偿的 NC指令格式要求和逆运动学原理,提出了实现五轴数控加工3D 刀具补偿功能的后置处理方法,并基于IMSpost平台开发了专用后置处理器。
(4)实例加工仿真结果验证了本文方法的正确性和有效性。该方法 可以实现 五 轴数控加 工具有3D 刀具补偿,避免了刀具磨损后发生刀具尺寸改变必须返回 CAM 系统,重新生成刀位文件和再次进行后置处理的繁琐过程,从而缩短零件总加工时间,提高数控加工程序的可重用性,具有较强的实际应用价值。
(5)进一步研究可考虑基于图像处理方法,研究如何对加工中刀具的磨损量进行实时监测,并结合五轴数控加工3D 刀具补偿算法,对实时磨损引起的刀具尺寸变化情况进行实时3D刀具补偿。
投稿箱:
如果您有机床行业、企业相关新闻稿件发表,或进行资讯合作,欢迎联系本网编辑部, 邮箱:skjcsc@vip.sina.com
如果您有机床行业、企业相关新闻稿件发表,或进行资讯合作,欢迎联系本网编辑部, 邮箱:skjcsc@vip.sina.com
更多相关信息