强国复兴有我:浙江畅尔智能装备股份有限公司
2024-10-10 来源:- 作者:-
【编者按】中华人民共和国成立75年来,随着中国工业化进程不断推进,机床工具工业随之发展壮大,总体水平快速提升,正向着机床工具工业强国的目标迈进。在庆祝新中国75周年华诞之际,中国机床工具工业协会策划组织以“强国复兴有我”为题的主题宣传活动,集中报道机床工具行业及企业取得的成果及未来高质量发展目标规划。
一、企业简介
浙江畅尔智能装备股份有限公司创建于2003年,致力于高端拉床、数控专用机床、机器人集成智能化成套装备的研制,是国家高新技术企业、国家专精特新“小巨人”企业、浙江省“隐形冠军”企业、浙江省“单项冠军”培育企业,曾获浙江省科学技术进步奖一等奖,现为中国机床工具工业协会插拉刨床分会理事长单位。
畅尔市场定位为高端装备进口替代,是国内外汽车零部件制造企业的合作伙伴,为宝马、奔驰、奥迪等汽车零部件精密加工提供智能化成套装备。在新能源汽车领域,为特斯拉、比亚迪等汽配企业提供精密加工装备。在家电领域,为美的、TCL等企业提供自动化装备。
畅尔以攻克国家“卡脖子”技术与解决行业瓶颈难题为目标,为航空发动机、燃气轮机、核工业等零部件制造领域提供国产高性能机床,实现拉床装备核心技术的自主可控和国产化替代。
二、数说企业改革发展成果
在做“专”上,畅尔专注核心业务,深耕细分市场,为大企业、大项目和产业链提供零部件、配套产品和服务,把工匠精神刻在使命里,实现在产品中。
2003年,畅尔拉床进入中国领先的汽车零部件制造企业;2009年,研发的立式内拉床刷新了全球大吨位拉床制造记录,突破大吨位拉床制造共性技术;2012年,开发首台“机器人+”智能化拉床;2016年,打破国外技术垄断,突破汽车卡钳支架智能化加工领域的“卡脖子”难题,获得全球汽配行业前三强企业德国大陆集团的定制化订单,在全球市场上占据一席之地。畅尔先后投入6000多万元科研经费,于2018年成功开发第一代航空发动机等榫槽加工的四轴数控卧式侧拉床,2020年成功开发第二代五轴数控卧式侧拉床,掌握了五轴数控卧式侧拉床以及核心部件技术,填补了航空发动机、燃气轮机等榫槽精密加工制造国产装备空白,弥补了国产涡轮机拉床领域短板。
依靠创新发展,畅尔努力实现中国拉床从低端到高端、从0到1的跨越。
在做“精”上,畅尔推崇精益生产、精细化管理和精准服务。在精益生产方面,建立起一套严格的项目评审机制,合理布局生产计划与排产,实时跟踪各生产维度数据,打通各生产环节,减少不必要的“内耗”,坚持举办技能等级认定工作,让员工学有所成,推动优质制造、绿色制造。在精细化管理上,依托工业互联网,系统构建网络、平台、安全三大功能体系,打造人、机、物全面互联的新型网络基础设施,打破“信息孤岛”,促进集成共享,实现数字化、网络化、智能化、科学化的管理,实现智能制造。在精准服务上,融合项目制管理模式和工匠式生产模式,针对客户需求进行个性化定制与交付,构建全链条的客户支持系统,并推行用户反馈机制不断完善产品设计和服务模式,从生产制造向增值服务领域延伸拓展,实现服务型制造。
目前,畅尔已经掌握了高端拉床产业较为完整的人才链、技术链和产业链,拥有核心工艺技术和自主知识产权。
畅尔依托国家级博士后科研工作站、省级企业研究院、省级企业技术中心、省工程研究中心等创新平台,打造拉削装备团队,科研团队中硕士、博士及中高级职称占比达70%。搭建了国防科工系统劳模工匠创新工作室、浙江省技能大师工作室,培养了一支高技能、精益求精的工匠队伍。
畅尔积累了重大项目科研及“卡脖子”攻关优势,主持承担国家“补短板”、省“尖兵”等省部级项目30余项,刷新并掌握领域内自主可控关键共性技术40多项。已累计授权国家专利200多项,其中发明专利48项,荣获浙江省第一届知识产权奖发明专利奖;参与起草国家标准、行业标准等17项。
三、重大成果及典型案例
1.用于航空发动机等轮盘榫槽加工的数控高速拉床
该成果获得国家“补短板”项目、浙江省重点研发计划项目支持,突破了我国轮盘榫槽加工“卡脖子”难题,入选浙江省装备制造业重点领域首台(套)产品、浙江省先进(未来)技术创新成果。该成果属于航空发动机、燃气轮机等领域压气机盘、涡轮盘榫槽精密拉削加工的关键生产装备,已经在中国航发集团及其配套企业用于轮盘榫槽的精密加工,推动国产化替代。
该成果攻克了榫槽高效精密拉削的多刀具、多工位、多参数复合加工工艺,研制了集成多个数控轴的C形摇篮机构,开发了刀具快速定位、就位及远程智能运维技术等。该成果核心技术自主可控,拥有国家专利20余项,具有高刚性和稳定性、高精度和精度保持性、智能化和柔性化等特点。
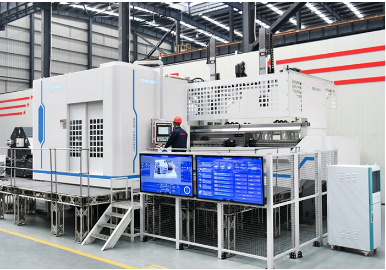
用于航空发动机等轮盘榫槽加工的数控高速拉床
2.多机器人协同汽车制动钳加工自动化生产线
该成果属高端装备制造领域,为汽车工业黑灯工厂提供“机器换人”成套解决方案,获得浙江省重大科技专项支持。产品集工件准确定位、精密拉削成形、铣钻攻丝、在线检测、多机器人协同于一体,主要用于汽车关键零部件制动钳支架的高速、精密、全自动化加工,经鉴定,技术达到国际先进水平,曾获2020年度中国机床工具工业协会自主创新十佳产品、装备制造业重点领域首台(套)产品、中国机械工业科技奖、浙江省知识产权奖发明专利奖二等奖、浙江制造精品等。
该成果进驻汽配企业德国Continental集团(跨国性企业集团,全球500强),经用户使用反馈,一致认为本成果较国外进口设备,具备制造周期短、性价比高、附加值高、市场竞争优势明显等特点,属于高质量、高档次的高端装备。该成果已经为宝马、奔驰、奥迪、特斯拉等高档轿车零部件制造配套加工,国内占据一定市场份额,并出口欧美地区。
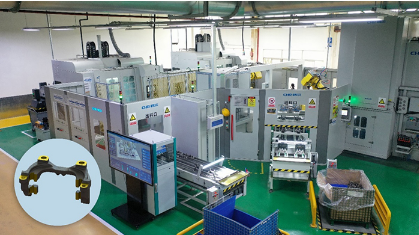
多机器人协同汽车制动钳加工自动化生产线
3.深槽加工数控立式内拉床
该成果用于家电行业零部件的精密加工,可实现超过常规键槽深度≥10倍深槽工件三工位同步一次性精密拉削成形,如空调压缩机气缸滑片槽加工。该产品拥有完全自主知识产权,具有拉削速度快、精度高、可靠性强等特点,已进驻全球空调转子压缩机生产企业美芝集团,供应给美的、TCL等知名企业。该成果荣获2023年度中国机床工具工业协会产品质量十佳、浙江省装备制造业重点领域首台套产品、浙江机械工业科学技术奖二等奖、浙江省先进(未来)技术创新成果等。
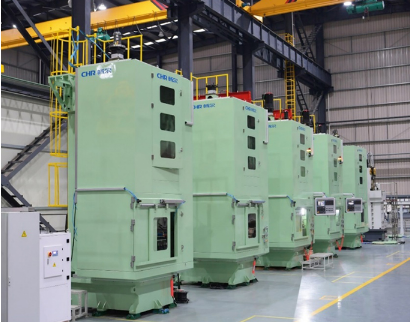
深槽加工数控立式内拉床
4.高精度数控分度转台
“高负载精密数控分度转台”主要用于航空航天、核工业等精密加工的高端数控拉床,产品融合了机械式锁紧及定位技术、高负载精度分度技术及精密检测技术,可承载≥20T单边重载切削力及扭矩力,满足复杂型面零件的精确定位及分度,定位精度≤8",重复定位精度≤6",项目在高档拉床核心装置中属于补短板、填空白产品。目前已在在航空发动机、燃气轮机等轮盘加工高档数控机床进行推广应用。
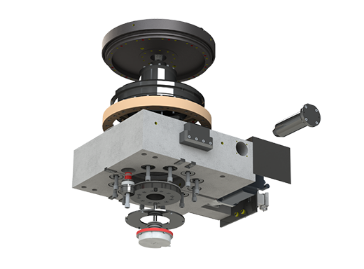
高精度数控分度转台
四、发展新质生产力
畅尔装备围绕客户价值链和产品生命链的提升,以研发设计数字化为“龙头”,以“智能运营数字化”为基础,打造数据驱动、智能引领的数字化技术核心竞争力,以机器人+、智能化、数字化的发展变革进驻中高端市场,实现企业跨越式发展的同时带动行业转型升级。
2013年,畅尔装备开发出“机器人+拉床”的创新案例,研制了基于机器人操作的智能化拉床,为汽车零部件企业提供了自动化拉削加工的样板案例。之后,又率先在国内同行业推广集成“机器人+高端拉床+数控专用机床”的高端制造模式,开发了可集工件准确定位、精密拉削成形、铣钻攻丝、在线检测、多机器人协同于一体的汽车制动钳高速精密加工全自动生产线,奠定了畅尔装备在汽车零部件精密拉削领域的高端化路径。
近年来,畅尔装备基于研发、生产、营销、管理等各环节,加强ERP、CRM、PDM、MES等信息建设投入,搭建产品全生命周期网络,聚力推动数字化、信息化产品研发。将数控技术及工业机器人应用技术渗透并运用到主导产品中,开发了工业机器人集成技术、远程监控系统、嵌入式控制系统、在线监测技术等,基于物联网+,在拉削装备上搭建物联网操作平台,实时远程监控机床状态,使产品逐步向智能化、数字化转变。通过这一数字化转型,产品技术含量得到了大幅提高,不断满足客户高效率、自动化、智能化的生产加工需求,也使产品的附加值大大提升,推动企业持续、健康、高质量发展。
(来源:畅尔装备 责编:梅峰)
投稿箱:
如果您有机床行业、企业相关新闻稿件发表,或进行资讯合作,欢迎联系本网编辑部, 邮箱:skjcsc@vip.sina.com
如果您有机床行业、企业相关新闻稿件发表,或进行资讯合作,欢迎联系本网编辑部, 邮箱:skjcsc@vip.sina.com
更多相关信息