高精度数控机床主轴系统热误差的控制方法
2021-1-27 来源:西安交通大学 陕西省智能机器人 等 作者:赵亮 雷默涵 朱星星 王帅 凌正 等
摘要:为了解决高精度数控机床主轴系统热误差的难题,提出了一种主动控制主轴热误差的新方法.根据设计的螺旋盘管冷却器,分析了硅脂厚度对主轴与冷却器间的接触热阻的影响规律,建立了热阻模型.在简化主轴系统模型的基础上,构建了主轴系统的热-流-固有限元模型,并对冷却参数进行了仿真.利用搭建的温度控制系统,对有限元模型进行验证.结果表明,有限元模型能有效预测主轴系统热特性的变化规律,其冷却器的换热效率高,热平衡时间缩短了约68%,热误差减小了约19%.本研究为精密机床主轴热误差控制提供了一种新思路。
关键词:数控机床;主轴系统;温度控制;热误差;热-流-固模型
机床温度变化和温度场分布不均匀引起的热误差是导致精密机床加工精度降低的最主要因素在加工中减小主轴热误差影响的常用办法有误差补偿法和温度控制法.Liu等研究了主轴径向热误差在不同工况下的变化规律,提高了误差模型的预测精度并达到了良好的误差补偿效果.Liu提出了基于岭回归的主轴热误差建模方法。
减少了热敏感点之间共线性对热误差模型的长期预测精度的影响.但是,补偿法的补偿范围和有效性具有一定限制,且鲁棒性较差,对复杂工况的自适应性较弱.此外,热误差补偿实施的过 程具有离散性、非均 匀性,存在温度反馈信号延时等问题,在通用性和稳定性方面存在局限。温度控制法利用冷却液循环带走主轴内部过度累积的热量,使电主轴内部温度分布更均匀,可有效降低主轴的热误差 .Xia等[7]基于分形理论,建立了散热器的三维热流体动力学模型。
分形树形通道净散热器具有压降小、温度场分布均匀、性能系数大等优点.Liu等提出了差异化多回路冷却系统和匹配功率的散热策略以及主动冷却液策略,使主轴温度分布更容易达到均。针对传统的冷却装置,Grama等
提出了一种新的冷却触发模型,对冷压缩机的开关频率和开启时间进行动态控制,可显著减小热变形.上述方法虽然可以有效减少主轴的热误差,但均未考虑主轴达到热平衡的速度和热误差的稳定性问题.为了达到最佳的温度控制效果,需要对在冷却作用下的主轴的热特性进行精确仿真。
本课题组研究了金属粗糙表面接触时的热传导和热阻现象,并基于接触力学建立了模拟主轴内部结构接触的热阻模,提高了主轴热误差的仿真准确性。本文提出了一种主轴主动热误差控制方法,以精密数控坐标镗床的机械主轴为研究对象,设计了一种由螺旋盘管冷却器、液体泵、油液温控箱等组成的外置主轴温度控制系统;综合考虑了螺旋 盘管-硅脂-主轴 接触面间的热传导速率,构建了接触热阻数值模型。
利用有限元方法建立了在冷却作用下主轴的热-流-固耦合仿真模型。该模型可准确反映恒温温控中不同的冷却液温度对主轴温度场和热误差的影响,实现冷却液控制温度的优化,缩短主轴热平衡时间,减小热误差。
1、 螺旋盘管冷却器设计
铜质的螺旋盘管冷却器具有较高的换热效率,涂抹一定厚度的导热硅脂可以提高其与主轴外壳结合面间的换热效率.在螺旋盘管外包裹隔热层,以阻断由空气对流换热引起的热量传递。螺旋盘管内流体的流动受管壁边界层的作用和由离心力作用产生的二次流(涡对)影响,如图1所示.其中,螺旋盘管单圈直径190mm,管间距12mm,管壁厚0.8mm,内径4.4mm,横截面上的平均流速为3.53m/s.由于二次流的影响,当流体旋转着通过弯管时,流线呈螺旋形。
同时管内摩擦损失增大,螺旋管道中流体从层流向紊流转变的 临界雷诺 数为 6500.螺旋盘管内部流体在离心力诱发下会产生由一对纵向漩涡构成的二次流,导致管壁上产生不均匀的对流换热,即产生不同的局部对流换热系数。
但在层流情形下,螺旋盘管中的二次流可强化其管内冷却液的传热效率.本文选用4号主轴油作为冷却液,其运动黏度为
,瞬时流量为0.1L/s,雷诺数约为 7234。
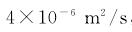
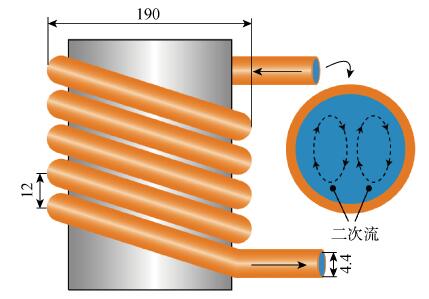
图1 螺旋盘管与二次流 (mm)
2、螺旋盘管-硅脂-主轴系统的热特性仿真
2.1 螺旋盘管-主轴结合面热阻模型
金属固体间通过硅脂进行热传递时,热阻主要来自于硅脂,而硅脂的热阻与其厚度呈正相关的线性关系.螺旋盘管横截面近似圆形,如图2所示。
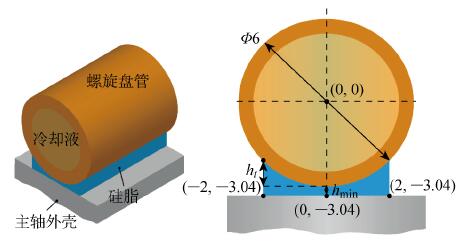
图2 螺旋盘管-硅脂-主轴外壳接触处横截面 (mm)
在整个换热面积上涂抹的硅脂厚度约为2.5mm(经验值),与螺旋盘管接触的宽度约为4mm.其中,hmin为最小硅脂厚度,ht为硅脂厚度.系统外壳表面接触区域较小,受到的法向力约为480N,在整个接触区域内可产生平均的稳定压力。
螺旋盘管与主轴外壳间的硅脂厚度 H =ht+hmin.当x=0时,ht=0,H=hmin.结合面间的硅脂厚度随接触面间压力的增大而减小,受压状态下,hmin值通常在 0.01mm 数量级[15-16],远 小于螺 旋盘管-主轴外壳结合面间多 硅脂区域内的ht值,因此hmin对结合面间的接触热阻影响不大,估计hmin值为0.04mm.硅脂热导率kb=0.58 W/(m·℃),圆心距离主轴表面3.04mm,则

式中:x 为螺旋盘管-硅脂-主轴外壳接触处横截面中横坐标的值.在不考虑脂-固接触热阻的情况下,螺旋盘管与主轴外壳结合面间的热导为

式中:a=-2mm;b=2mm;L 为螺旋盘管管长,取5.97m. 螺旋盘管与主轴外壳表面接触时单位面积内的硅脂热阻

由于螺旋盘管表面粗糙度较小,硅脂与螺旋盘管、主轴外壳结合面的接触热阻(Rc)比Rb小,对总热阻的贡献有限.参考文献中的结果,硅脂与螺旋盘管、主轴壳体间的接触热阻总和的估计值为
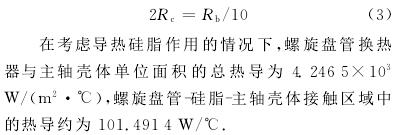
2.2 热-流-固耦合模型建立和仿真计算
基于螺旋盘管冷却器和主轴的部件型号、结构设计、结构尺寸以及运行工况,对内部生热率、换热边界条件等进行计算.其中,轴承生热率、主轴外表面与空气之间的对流换热系数、主轴内部金属部件结合部(如轴承与轴心以及主轴套之间)的接触热导等边界条件的计算采用课题组已有方法.利用有限元方法,对安装螺旋盘管冷却器的主轴进行瞬态的热-流-固耦合仿 真.模 型 建立过程主要包括:在三维建模软件 Creo中建立主轴三维实体模型(不包括螺栓、螺孔、凹槽、圆角和倒角等对主轴系统热特性影响较小的微细结构);将模型导入 ANSYS中进行网格划分;选择热-流-固耦合分析单元;加载边界条件;求解;进行结果后处理.瞬态的热-流-固耦合仿真结果包括各瞬态时间点(t)的盘管内冷却液温度分布、主轴温度(T)场和变形(ε)场。
仿真工况包括:主轴转速选择精密镗床实际加工中的典型转速(1 000r/min),环境温度设定为恒温实验室实际温度(19℃),仿真结果如图3所示.结果表明,冷却液温度 为 16 ℃ 时冷却效果明显。
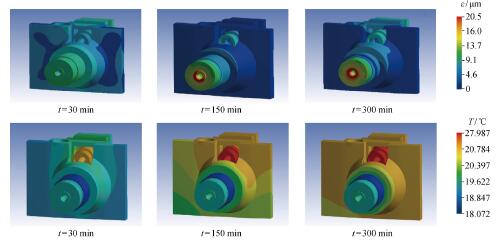
图3 冷却液温度为16℃时的热特性仿真
3 、实验验证
3.1 冷却系统设计和实验装置
主轴冷却控制系统总体架构如图4所示.系统的冷却工质选用4号主轴油,冷却循环从油温控制箱开始,工质经循环泵增压,经涡轮流量计和控制阀控制流量后输出至螺旋盘管换热器,用于主轴冷却,最后回流至温控箱,实现循环冷却。为了监控系统的工作状态,在螺旋盘管进出口的位置设置温度传感器和压力传感器,在主轴被冷却的位置设置温度传感器。
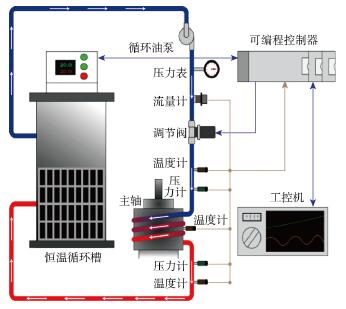
图4 温控系统整体设计
在精密坐标镗床实验平台上进行主轴的恒温主动冷却控制实验,验证温度控制的效果.实验在恒温车间进行,环境温度为 19 ℃,主 轴 恒 定 转 速 设 为1000r/min.电涡流位移传感器测量主轴的伸长量:温度传感器吸附在主轴外表面,分别布置在主轴前端法兰(T1),主轴壳体前端上方(T2)和下方(T4),主轴壳体前端侧方(T3和 T5),主轴壳体后端上方(T6)和下方(T8),主轴壳体后端侧方(T7和 T9),如图5所示。
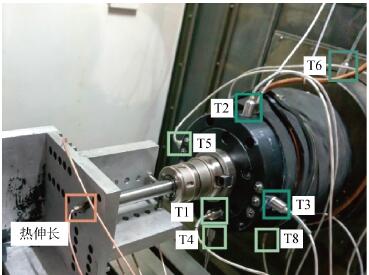
图5 主轴特征温度和热误差测量
3.2 主轴热-流-固模型的实验验证
实施温度控制之前需要建立准确的有限元仿真模型,并作为冷却参数选择的依据.在冷却液温度分别为20℃和16℃时,对比主轴的热误差和经模糊聚类辨识的热敏感点(T2、T3、T6)温度的瞬态热-流-固仿真结果与实验测量值,如图6所示.对于20℃ 恒温冷却的螺旋盘管-主轴系统,实验中 T6的温度在约 130min后上升趋势 显著减缓,在 200min后趋于平稳;T2、T3的温度在130min左右逐渐趋于平稳.仿真中 T6的温度在100min之前上升趋势明显,在100min之后上升趋势减缓并逐渐趋于平稳.对于16℃恒温冷却的系统,实验中 T2、T3的温度在0~25min范围内持续下降,25min后上升,并在150min后逐渐平稳;T6的温度与 T2、T3的温度同时下降,随后上升至200min左右在逐渐平稳.主轴热平衡时的温度随冷却液温度的降低而有所降低。
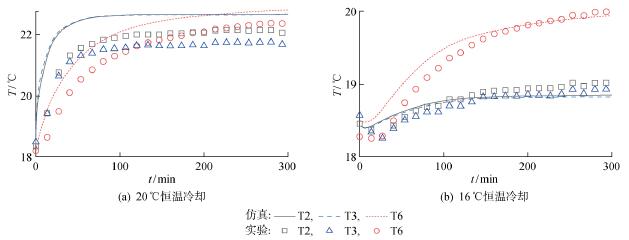
图6 主轴温度的仿真-实验对照
恒温20℃和16℃冷却时主轴热误差测量和仿真结果如图 7所示.热误差在 50min 之前快速增加,在50min之后增加速度渐缓,并在150min之后达到平稳状态.仿真得到的热误差大小和变化趋势与实验结果吻合。
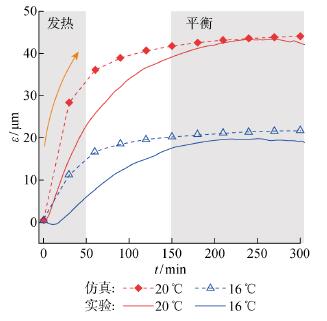
图7 主轴热误差的仿真-实验对照
3.3 温控效果的实验验证
在无外加冷却的条件下,主轴系统从静置状态开机,恒定转速为 1000r/min,测试得到的温度-热误差曲线如图8所示.其中,变速箱由机床自带的独立油冷机冷却,控制周期较长,温度波动比其他位置稍大.主轴最高温度 (24.1 ℃)出现在主轴中段上方,主轴最大伸长量为 53.4μm,热平衡时间约为492min.恒温控制的实验结果如图9所示。
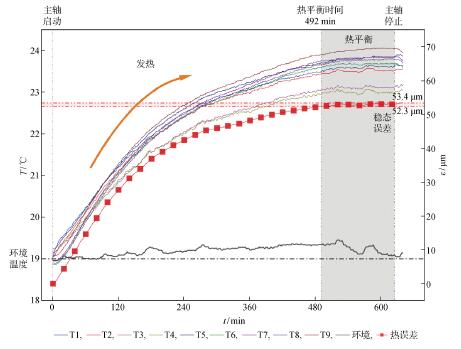
图8 温度-热误差曲线
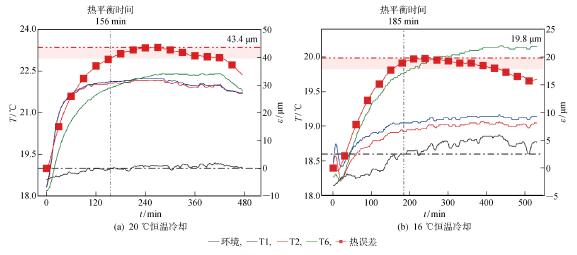
图9 恒温控制实验
其中,油箱的温度分别设置为20℃和16℃.从图中可知,恒温20℃冷却时测点的最高温度为22.4℃,主轴的最大伸长43.4μm,热平衡时间约为156min.与无外加冷却的工况相比,主轴的最大伸长量减少了10μm,即热误差减小了约 19%;热 平 衡 时 间 缩 短 了 336min,缩短了约68%.结果表明:基于螺旋盘管的主轴冷却控制方法可以缩短机床的预热时间并有效减小热误差,且控制温度越低,热误差的最大值越小.但是,降低控制温度会延长系统达到热平衡的时间,从而不利于精度的提高,并且还会导致平衡时温度稳定性下降,制冷功率和能耗增加.在实际加工过程中,热误差的稳定性比其最大值更加重要.并且,较为稳定的热误差可以通过补偿等方法消除.因此,与16℃相比,20℃是更加理想的恒温冷却控制温度。
4 、结语
本文针对精密数控机床主轴系统热误差的问题,提出了一种基于螺旋盘管的外置主轴热误差抑制方法。分析了螺旋盘管与主轴外壳接触面间的硅脂厚度对热传导的影响,计算得到了结合面间的热传导率。通过综合考虑主轴部件生热、换热等边界条件,建立了螺旋盘管-主轴系统的瞬态热-流-固耦合模型。
该模型能够准确预测螺旋盘管冷却器作用下的主轴热特性,并且可以作为选择冷却液温度的依据。理想的恒温冷却控制温度为20℃,当螺旋盘管冷却器内冷却液的流动状态为层流时,冷却器的换热效率高:与无外加冷却工况相比,达到热平衡的时间缩短了约68%,热误差减小了约19%.该方法成本低,效率高,无需建立热误差模型,具有普适性。
投稿箱:
如果您有机床行业、企业相关新闻稿件发表,或进行资讯合作,欢迎联系本网编辑部, 邮箱:skjcsc@vip.sina.com
如果您有机床行业、企业相关新闻稿件发表,或进行资讯合作,欢迎联系本网编辑部, 邮箱:skjcsc@vip.sina.com