一种更换砂轮免对刀的内圆磨削方法
2020-7-9 来源:武汉--湖北大学计算机与信息工程学院 作者:陈涛 王辉辉 杨维明 张玲 胡东红
摘要:内圆磨削过程中,砂轮的磨损是不可避免的,特别是对于对小孔径内圆磨而言,砂轮外径小,对工件磨削时,砂轮损耗较快,当砂轮的磨损到达一定程度,磨削工件质量以及效率会大大降低,所以需要修整砂轮,或者更换新砂轮,从而要重新对刀,设置砂轮修整原点和工件坐标原点 ,经过多次调整以后才能磨削出合格工件,可供使用。这个过程即费时间也费工件,为此我们提出了一种内圆磨削更换砂轮免对刀的方法,建立磨削起始位置和磨削终点位置与砂轮直径关系,以及建立当前砂轮直径与砂轮修整量关系,在更换新的砂轮后,直接调用砂轮修整程序,对砂轮进行若干次修整后,即可开始磨削加工工件。
关键词:内圆磨 对刀 砂轮更换
内圆磨床作为一种精密磨削设备,广泛应用于中小孔内圆磨削加工,由于砂轮转速高,砂轮轴刚性比较差,容易产生弯曲形变与振动,导致砂轮工作表面磨粒会因不均匀磨损而失去正确的几何形状[1]。但在砂轮磨削工件过程中,砂轮磨损程度以及自身保持程度是十分重要的,为了保证内圆磨过程中的磨削质量,砂轮要保持良好的表面质量,就需要不断的,均匀地修整砂轮,甚至是更换新的砂轮。由于砂轮尺寸的变化,砂轮和工件的相对位置也会发生变化,机床在重新进给前必须进行砂轮和工件之间位置调整[2]。在本文中,就是通过调整程序中新砂轮直径参数,来调整砂轮磨削的起始和终点位置来对工件进行磨削。
同时在进行内圆磨削时,使用的砂轮存在砂轮切削性很快下降,加工状态发生变动,磨粒在加工表面容易打滑,难以获得足够的砂轮线速度等不利条件,容易造成加工效率下降以及加工精度不稳定[3],因此需要及时的修整砂轮以及更换新砂轮来保证加工质量和效率。可以通过统计每个砂轮加工工件的数量得到砂轮的实际寿命,研究表明:过长的修整间隔并不能提高砂轮的寿命及加工效率,反而会影响加工工件的质量。过长的修整间隔会使砂轮在磨削的过程中自身损耗大幅增加,所以过长的修整间隔反而会降低砂轮的使用寿命[4]。所以在砂轮磨削工件过程中,对加工工件数量进行统计,当磨削的工件达到指定数量时,调用砂轮修整程序对砂轮进行修整,或者对砂轮进行更换。
为了避免内圆磨床频繁的砂轮更换带来的重新对刀工件原点、重新对刀砂轮修整原点和重新试磨工件等繁琐步骤,提出一种更换砂轮面对刀的内圆磨削方法,能够有效地提高了加工效率。
1.更换砂轮免对刀方法简介
该方法在更换新砂轮后,不需要对刀,直接调用砂轮修整程序,对砂轮进行若干次修整后,即可开始磨削加工工件。通过预先设置砂轮修磨工件个数,修磨完指定的个数工件后,可以自动调用砂轮修整程序对砂轮进行修整。若是更换新砂轮,直接修改砂轮直径参数,调用砂轮修整程序进行若干次修整,即可开始磨削加工工件。
2.方法具体内容
2.1建立磨削起始位置和磨削终点位置与砂轮直径关系
首先测量、计算并记录新砂轮直径D0和当前砂轮直径D2,确定磨削起始位置和磨削终点位置的X轴坐标值。金刚笔和工件固定在工作台上,砂轮固定在砂轮架床身上,砂轮能够沿X轴方向上下移动,也可以沿Z轴方向左右移动,砂轮沿X轴靠近金刚笔为X轴负方向,砂轮沿Z轴靠近工件为Z轴正方向,将新砂轮安装在砂轮夹头上,手工操作数控机床,令金刚笔接近砂轮表面并留有安全间隙,记录此时的机床X轴坐标位置X0;如图1所示,1—工件,2—金刚笔,3—砂轮,4—砂轮夹头。将新砂轮安装在砂轮夹头上,手工操作数控机床,令金刚笔接近砂轮表面并留有一定的安全间隙。
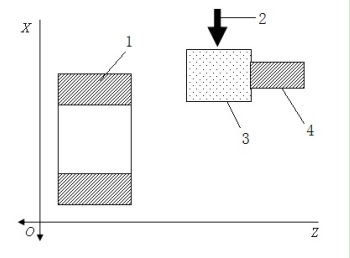
图1 金刚笔接近砂轮表面存在安全间隙的状态图
手工操作数控机床,反复修整砂轮,直到金刚笔饱满可靠地对砂轮进行完全的修整如图2所示,记录此时的机床X轴坐标位置X1,测量并记录此时的砂轮直径D1,记录当前直径D2=D1,由此,计算出新砂轮直径D0,D0含安全间隙,D0为:
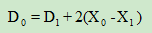
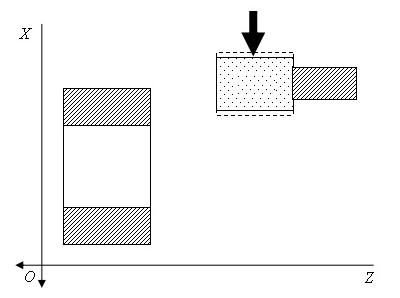
图2金刚笔饱满可靠地对砂轮进行完全修整的状态图
将标准工件,内径尺寸为W1,安装在工作台上,手工操作数控机床,移动砂轮轻触标准工件表面,记录当前机床X轴坐标位置X2;如图3所示。
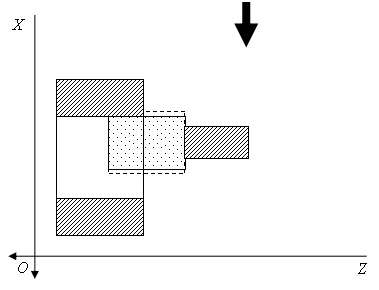
图3移动砂轮轻触标准工件表面的状态图
将毛坯工件安装在工作台上,手工操作数控机床,移动砂轮到毛坯工件表面安全间隙处,记录当前机床X轴坐标位置X3;如图4所示。
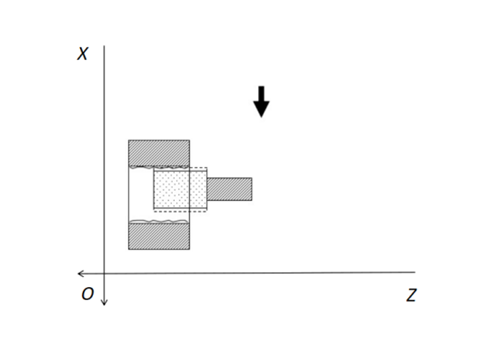
图4移动砂轮到毛坯工件表面安全间隙处的状态图
编制磨削加工程序P1。磨削起始位置X轴坐标值:

磨削终点位置X轴坐标值:
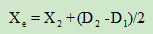
运行该程序,对毛坯工件进行试磨加工;测量磨削加工后的工件直径,记为W2,根据实际磨削加工的尺寸与标准工件的尺寸W1的差,将公式(3)中磨削工件时的X轴终点坐标Xe调整为Xe’:

完成了磨削加工程序P1的设定和磨削尺寸调整,建立了磨削起始位置和磨削终点位置的X轴坐标值与当前砂轮直径D2之间的关系;建立当前砂轮直径与砂轮修整量关系,设定砂轮修整程序P2,并在砂轮修整完成后,将加工工件计数清零;设定内圆磨磨削加工主程序P3,使其能够实现调用磨削加工程序P1,修改加剩余加工工件数N,剩余加工工件计数N为零,则调用砂轮修整程序P2;更换新砂轮后,不用对刀,人工将当前砂轮直径D2修改为新砂轮直径D0,然后直接调用砂轮修整程序P2若干次;然后,直接开始磨削加工工件。
2.2建立当前砂轮直径与砂轮修整量关系
设置砂轮修整起始位置为机床X轴坐标
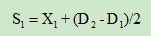
砂轮修整的终点位置为机床X轴坐标

其中为砂轮修整量;
设定砂轮修整程序P2,使其能够实现:若当前砂轮直径D2小于预先设定的砂轮最小直径D3,则提示更换新砂轮;否则,令机床由砂轮修整起始位置X轴坐标开始,修整砂轮至砂轮修整终点位置X轴坐标;修改当前砂轮直径
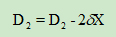
设置当前砂轮可加工工件数N=m,其中m代表每加工m个工件,修整一次砂轮;N代表剩余加工工件数,每加工一个工件,N的值减1,当N减到0,则自动调用砂轮修整程序P2。
2.3内圆磨削主程序设置及更换新砂轮设置
内圆磨削主程序P3中包括在装上毛坯工件,调用磨削加工程序P1,提示操作人员取下加工好的工件,装上毛坯工件;N=N-1;若N>0,直接调用磨削加工程序P1加工工件;否则,调用砂轮修整程序P2,然后再调用磨削加工程序P1。
若安装新砂轮,则将当前砂轮直径D2修改为新砂轮直径D0,
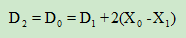
多次调用砂轮修整程序P2,直到金刚笔饱满地对砂轮进行修整;执行内圆磨加工主程序P3,对工件加工。
3.结语
(1)砂轮经过多次修整后,修磨效果和安全性会逐渐降低,需要合理的设置一个砂轮最小直径。同时在需要设置合适的砂轮修整间隔,保证砂轮的磨削质量以及使用寿命。
(2)最开始测量砂轮直径时,砂轮可能不圆导致无法准确测量出砂轮直径,但是可以确定金刚笔修整后的砂轮直径,从而反推出新砂轮直径(包含安全间隙)。
(3)避免每次更换新砂轮后,修整新砂轮、重新对刀工件原点、重新对刀砂轮修整原点和重新试磨工件等繁琐步骤,有效地提高了加工效率。
(4)更换新砂轮后,只需把当前砂轮直径修改为新砂轮直径,调用砂轮修整程序,对砂轮进行若干次修整,即可直接磨削加工工件,提高了加工效率。
参考文献
[1]赵飞, 李焕锋, 沙杰,等. 功率监控在精密内圆磨床砂轮修整系统中的应用[J]. 机械工程师, 2013, 000(001):8-10.
[2]周军. 自动内圆磨床砂轮的修整和补偿[J]. 磨床与磨削, 1997, 000(003):43-44.
[3]新谷裕之, 潘广银. 内圆磨削砂轮整形与修整[J]. 磨床技术, 1998, 000(002):32-36.
[4]陈卫东, 涂俊群. 压缩机内圆磨CBN砂轮修整间隔对工件质量及砂轮寿命的影响[C]. 中国超硬材料技术发展论坛. 2015.
投稿箱:
如果您有机床行业、企业相关新闻稿件发表,或进行资讯合作,欢迎联系本网编辑部, 邮箱:skjcsc@vip.sina.com
如果您有机床行业、企业相关新闻稿件发表,或进行资讯合作,欢迎联系本网编辑部, 邮箱:skjcsc@vip.sina.com
更多相关信息