高速数控车床主轴变工况温升特性研究
2019-4-12 来源:河北工业大学 沈阳机床 江苏建一机床 作者:韩靖 杨泽青 杨伟东
摘要:为了定量评价和分析高速数控车床在不同运行工况下的主轴温升特性,以某高速数控车床主轴系统为研究对象,在分析主轴系统热源基础上,考虑实际工况参数对主轴系统温升影响,设计了空转条件和切削条件下的工况参数表,利用正交实验法对各工况参数进行组合,然后ANSYSWorkbench15.0进行热稳态分析,得到不同工况下主轴系统的温度场分布情况;在此基础上,采用了多元线性回归的方法建立变工况参数与车床主轴系统达到热平衡时最高温升的预测模型,并对模型进行了验证,结果表明主轴系统温度真实值与预测值的误差在0℃~2.5℃范围内,所以预测模型具有很高的预测精度。此模型为车床主轴系统温升特性评估、工程实践中工艺参数的合理确定和热误差补偿提供依据。
关键词:高速数控车床;变工况;温升;预测模型
主轴系统是数控机床的主要部件,其定位精度和加工精度受其内外温升变化的影响。主轴在运转时,会受到各种工况的影响,将会导致主轴热特性的变化从而影响机床的加工精度和寿命。因此为了确保主轴在运转时的工作精度和寿命,需要对主轴在不同工况下运行时的温升进行预测。国内外学者对影响机床主轴系统热态性能的因素进行了大量研究。Mori-waki等人以UM-200型号数控机床为研究对象,讨论了环境温度和主轴旋转转速对主轴系统热误差的影响并且分别建立了热误差模型,然后利用卷积的算法对机床热误差进行了补偿,使由主轴旋转转速和环境温度而产生的加工误差减少到原来的15%。
Jin Kyung Chio等人应用有限元方法在不同热源和不同对流、接触传热工况下对主轴轴承系统进行了热瞬态分析,通过与各种其他计算方法实验数据相比最大误差只有2μm,即仿真的方法能够很好的预测模型的热行为。张丽秀等人以150MD24Y20电主轴为研究对象,分别讨论了电主轴运行时间、环境温度、冷却液温度三种因素对电主轴外表面温度的影响,并且采用遗传神经网络的方法对电主轴的外部表面温度进行了预测。张良利用有限元法分析了转速、冷却液温度和季节变化3个因素工况对主轴轴向热误差的影响,并且利用多元线性回归法建立了热误差补偿模型,提高了机床的补偿效果。
上述的研究工作主要集中在单一工况或常规工况条件下的热态性能分析,没有考虑实际复杂工况多因素对主轴系统热态性能的影响,针对该问题,本文采用有限元计算法对主轴系统在实际多工况条件下的热态性能进行数值模拟分析,得到多工况条件下主轴系统的温度场分布情况,进而建立工况参数与车床主轴系统温度敏感点温升变化的预测模型,为变工况条件和极限工况条件下的主轴系统温升预测提供依据。
1、高速数控车床主轴系统热稳态分析
1.1热稳态分析理论基础
热稳态分析依据于能量守恒原理的热平衡方程,对于如图1所示的机床主轴一维简化模型,在考虑对流和辐射散热的条件下,单一热源在主轴左侧,热量从左端输入,从右端传出,主轴各点温度T(x,t)按照分布函数公式(1)计算:

式中,[K]为传热矩阵、{T}为节点温度向量、{Q}为节点热流率向量。
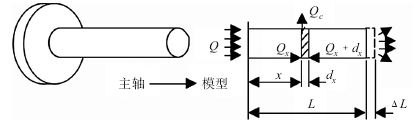
图1 机床主轴一维简化模型
1.2数控车床主轴系统热源分析和计算
在公式(1)中节点热流率向量{Q}主要受主轴受内外热源发热量影响,主轴系统所受热源主要有轴承摩擦热、电动机发热及切削热等。本文以某高速数控车床主轴系统为研究对象,由于此主轴系统采用带传动机构,忽略电机发热对主轴的影响,另外加工过程中大部分切削热被切削液带走,在此忽略切削热对主轴系统的影响。轴承摩擦力矩是引起轴承的发热量主要因素,按公式(2)计算:

式中,Q为轴承发热量(单位:W)、n为轴承转速(单位:r/min)、M为轴承摩擦力矩(单位:N·mm)。
轴承的摩擦力矩包括速度项M0和负荷项M1两项,如公式(3)所示,其中当运动粘度v与转速n的乘积v·n≥2000c St·r/min时,M0按公式(4) 计算;当v·n<2000c St·r/min时,M0按公式(5)计算;负荷项M1按公式(6)计算:
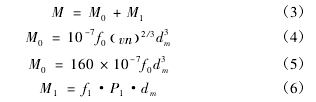
其中,dm为轴承的中径(单位:mm)、f0为与轴承类型和润滑方式有关的经验常数;f1为与轴承类型和所受负荷有关的系数;主轴系统也受切削条件下切削力的影响,切削力又与切削三要素Vc为切削速度(单
位:mm/min)、ap为背吃刀量(单位:mm)、f为进给量有关(单位:mm/r),具体计算与数值的确定参考文献。
2、多工况条件下的主轴系统温升特性模拟
2.1工况条件设计
数控车削加工工艺系统作为复杂的机电系统,加工过程中工况参数(主轴转速、轴承预紧状态、背吃刀量、进给量、进给速度等)直接影响主轴系统的温度场分布,进而制约机床的热定位精度及加工质量。本文以某高速数控车床主轴系统为研究对象,为了分析多工况条件对主轴系统温升变化的影响规律,根据机床选用的轴承标准及参数范围和实际加工条件,分别在空转条件和切削条件下设计工况参数
水平表如表1和表2所示。
表1 空转条件下工况设计表
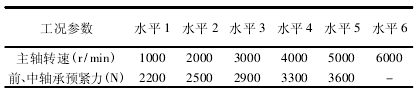
表2 切削条件下工况设计表
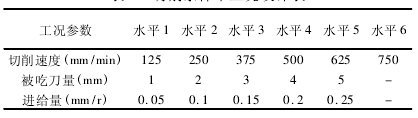
2.2 多工况条件下的主轴系统温升特性分析
空转条件下主要研究主轴转速和前、中轴承预紧力对主轴系统最高温升的影响,利用正交实验分析法对表1中的工况因素进行正交组合,计算不同条件下的生热量,分别对主轴系统进行热稳态分析,图2为空转水平3工况(主轴转速为3000r/min、前中轴承预紧力为2900N)条件下得到的主轴系统整体稳态温度分布图。图3为不同转速对主轴系统温升最高值影响关系图,图4为前、中轴承预紧力对主轴系统温升影响关系图,由图3和图4比较可知,主轴的转速,前、中轴承预紧力对主轴系统的温升变化都有影响,其中主轴转速对主轴系统的温升影响最大,所以在空转条件下主轴转速可以作为对主轴系统温升变化的敏感影响因素。
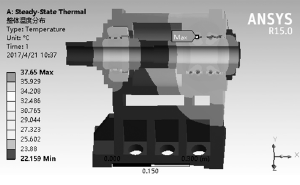
图2 空转水平3工况条件下主轴系统整体稳态温度分布图
切削条件下主要研究切削力对主轴系统温升的影响,而车削加工中切削速度、被吃刀量、进给量的大小直接影响切削力,所以这里主要考虑切削速度、被吃刀量、进给量对主轴温升的影响。根据某高速
数控车床主轴系统的结构和机床参数范围,选择切削速度的范围为125mm/min~750mm/min,被吃刀量的范围为1mm~5mm,进给量的范围为0.05mm/r~0.25 mm/r,利用正交实验分析法对表2中的工况因素进行正交组合,通过有限元分析,得到切削条件多工况下切削速度与主轴系统达到热平衡时最高温升的关系如图5所示、背吃刀量与主轴系统达到热平衡时最高温升的关系如图6所示、进给量与主轴系
统达到热平衡时最高温升的关系如图7所示。
比较图5、图6和图7可知,切削速度、被吃刀量、进给量三个因素对于主轴系统的温升变化都有影响,其中切削速度对主轴系统的温升影响最大,所以在切削条件下切削速度可以作为对主轴系统温升变化
的敏感影响因素。
通过多工况条件下主轴系统热稳态分析可知,空转时主轴转速对主轴系统温升特性变化影响最大,切削条件下切削速度对主轴系统温升变化影响最大,由此在实际加工过程中,为减小热误差对加工精度
的影响可以直接调整主轴转速及切削速度这两个关键工艺参数;为了定量描述不同工艺参数对主轴系统温升影响,需要建立工况参数与主轴系统温升特性的预测模型。
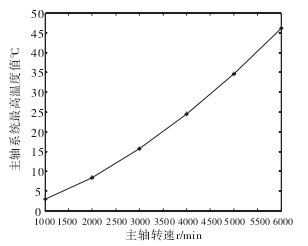
图 3 主轴转速与主轴系统最高温升关系
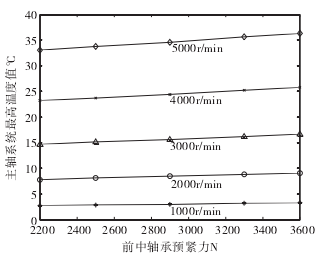
图4前、中轴承预紧力与主轴系统最高温升关系
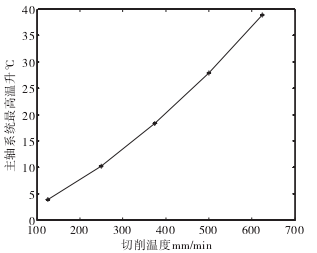
图5切削速度与主轴系统最高温升关系
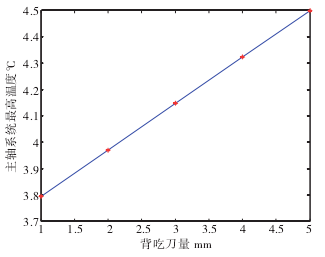
图6被吃刀量与主轴系统最高温升关系
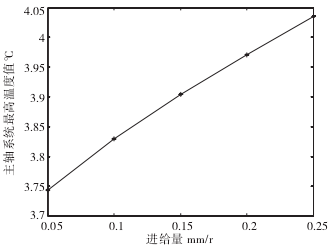
图7进给量与主轴系统最高温升关系
3、工况参数与主轴最高温升预测模型的建立与分析
根据高速数控车床选用的轴承标准、参数范围和实际加工条件,这里选择主轴转速、轴承预紧力、切削速度、进给量、被吃刀量5个工况参数为自变量,主轴系统达到热平衡时的最高温升为因变量。利用
正交实验分析法对表1和表2中的工况因素进行正交组合,通过有限元分析得到在不同的主轴转速、轴承预紧力、切削速度、进给量、被吃刀量下主轴系统的温升,用MATLAB对空转条件下得到的温升数据和工况因素数据进行多元线性回归分析,得到空转条件下主轴系统达到热平衡时最高温升与主轴转速、轴承预紧力的预测模型1如公式(7)所示。

其中,T(k)为主轴系统达到热平衡时的最高温升值;X1()k为主轴转速;X2()k为前、中轴承预紧力。
同样用MATLAB对切削条件下得到的温升数据和工况因素数据进行多元线性回归分析,可得到切削条件下主轴系统达到热平衡时最高温升与切削速度、被吃刀量、进给量的预测模型2如公式(8)所示:

其中,T(k)为主轴系统达到热平衡时的最高温升值;X1()k为切削速度;X2()k为被吃刀量;X3()k为进给量。
为了验证空转条件下预测模型1和切削条件下预测模型2的精度,分别将空转条件下的后6组数据带入预测模型公式(6)中,切削条件下的后6组数据的预测模型公式(7)中,并与实际的仿真值作比较,结果
如图8、图9所示,两个模型的预测结果如表3所示
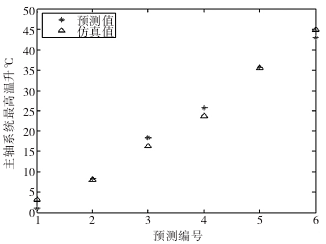
图8 空转工况下仿真值与预测值的比较
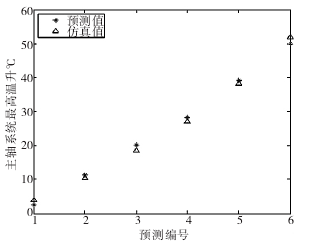
图9 切削工况下仿真值与预测值的比较
表 3 模型的预测结果分析
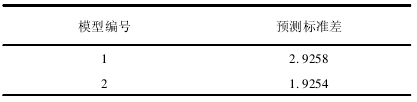
由图8和表3可知,由空转工况下的预测模型得出的主轴系统的温度最高值与仿真模型1得出的温度最高值的误差值在2.5℃范围内,且模型1的预测标准差为2.9258。由图9和表3可知,由切削工况下的预测模型得出的主轴系统的温度最高值与仿真模型2得出的温度最高值的误差值在1.5℃范围内,且模型2的预测标准差为1.9254。由以上分析可知空转工况和切削工况的预测模型都具有较高的精度,在上
述建立模型的工况中不仅包括常规工况同时也包括破坏性工况,所以建立的模型更符合实际条件,准确度也更高,所以可以对实验中很难获得的某些极限工况或破坏性工况下的主轴系统最高温升特性进行预测和分析。
4、结论
为了定量评价和分析高速数控车床在不同运行工况下的主轴温升特性,在分析主轴系统热源和散热基础上,设计了空转条件和切削条件下的工况参数表,利用正交实验法对各工况参数进行组合,然后运用有限元软件进行热态性能分析,得出以下结论:
(1)通过对某高速数控车床主轴系统在变空转工况下温升特性分析,发现主轴转速、前、中轴承预紧力均对主轴系统最高温升呈大致线性增长影响趋势,其中主轴转速对主轴系统的最高温升变化影响最大
,作为其敏感影响因素。
(2)通过对某高速数控车床主轴系统在变切削工况下温升特性分析,发现切削速度、被吃刀量、进给量三因素均对主轴系统最高温升呈大致线性工程实践中工艺参数的合理确定和热误差补偿提供依据增长
影响趋势,其中切削速度对主轴系统的最高温升影响最大,可作为其敏感影响因素。
(3)由多工况条件下的仿真数据建立了空转条件下和切削条件下的工艺参数与主轴系统最高温升之间的预测模型,并对模型精度进行验证,结果表明模型1的标准差为2.9258、模型2的标准差为1.9254,说明其具有较高的预测精度,可以为工程实践中工艺参数的合理确定和热误差补偿提供依据。
投稿箱:
如果您有机床行业、企业相关新闻稿件发表,或进行资讯合作,欢迎联系本网编辑部, 邮箱:skjcsc@vip.sina.com
如果您有机床行业、企业相关新闻稿件发表,或进行资讯合作,欢迎联系本网编辑部, 邮箱:skjcsc@vip.sina.com
更多相关信息