高强度精密螺栓加工方法优化
2019-4-11 来源:中车戚墅堰机车有限公司 作者:刘剑峰
摘 要: 本文主要从设备的合理选择、刀具的选用、先进加工方法的引进等方面,详细阐述了高强度精密螺栓的加工方法分析和优化的过程,为类似产品的加工,提供参照办法。
关键词: 精密螺栓; 优化加工; 断屑; 车削; 滚压
1、产品结构特性和技术要求
高强度精密螺栓是某公司加工的主要零部件,其主要特点是:等级高、强度高、精度要求高。下面以典型的高强度精密螺栓—气缸盖螺栓(见图1)为例,分析产品的结构特性及技术要求。
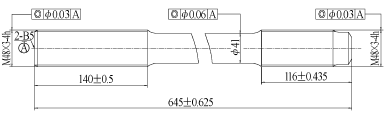
图1 气缸盖螺栓
气缸盖螺栓是柴油机上的一个关键零部件,其作用是将气缸盖牢固地固定在机体上,在柴油机运行过程中承受较大的拉力和扭矩,因此对产品的加工精度要求非常高,主要体现在以下2个方面:
(1) 产品的材料为18Cr2Ni4WA,是一种高强度合金结构钢,经过调质后有较高的强度和韧性(抗拉强度不小于1 175 MPa,屈服强度不小于1 029MPa,伸长率不小于10%,收缩率不小于45%)。
(2) 产品的加工精度要求高:①产品的形位公差要求较高,其螺栓螺纹及杆身的同轴度要求分别为0.03 mm和0.06 mm;②产品的两端螺纹等级要求高,均为M48×3-4 h。
2、产品加工工艺分析
通过对产品结构和技术要求的分析,找出该螺栓加工的难点:
(1) 该螺栓的两端螺纹及中间杆身的同轴度要求高,而且该螺栓的长度较长,为645 mm,杆身直径为41 mm,长径比接近16∶1,刚性较差,加工较为困难。
(2) 该螺栓两端均为M48×3-4 h的螺纹,螺纹等级要求高,采用传统的加工方法,很难保证螺纹精度。
(3) 该螺栓批量大,每台机体需48根气缸盖螺栓,采用传统的加工方法加工效率低、生产周期长,无法满足生产需求。
3、优化加工方法解析
3.1 以车代磨
传统的加工方法,为保证工件的精度,一般采用磨削的方式加工螺栓的杆身及两端螺纹档。由于以前螺栓批量小,该加工方式的缺点没有完全呈现出来,但随着螺栓的大批量生产,该加工方式已无法满足生产需求,必须采用新的加工方法,提高生产效率。
通过对螺栓技术要求分析,结合公司现有设备,计划采用车削方式代替磨削方式加工螺栓的杆身。通过前期试验发现车削加工存在2个问题:螺栓同轴度和表面粗糙度出现超差,无法满足设计要求。
针对上面问题,分析其产生原因并进行攻关。
(1) 螺栓同轴度超差。
原因分析:螺栓刚性差,加工时容易产生振动;公司现有数控车床,长时间车削长度小于500 mm的产品,导致机床导轨前后段磨损情况不同。
解决方案:首先合理选择加工刀具,半精车时采用负型刀,提高加工效率,降低生产成本。精车时采用正型刀,减小刀具切削阻力,同时优化切削参数,通过不断试验,合理选择吃刀量、进给速度,避免刀具与工件产生共振,有效控制工件加工过程中的振动。其次请求设备维修部门对机床导轨进行铲刮,保证机床导轨整体的平整度,提高机床的加工精度。
(2) 螺栓表面粗糙度差。
原因分析:螺栓材料热处理后韧性好,车削加工时不容易断屑,铁屑缠绕在螺栓杆身上,拉伤螺栓表面;车削过程中工件振动,工件表面存在振纹,影响表面粗糙度。
解决方案:为了提高零件加工的断屑性,首先与刀具供应商协商合理选择加工刀具的断屑槽形状,同时优化切削参数,合理选择吃刀量增加切削进给,提高断屑能力。其次,自制断屑块(见图2),将断屑块固定在刀具下端,改变铁屑的流向与长度,保证加工过程中的良好断屑。同时为有效消除车削振纹,须先调整车床主轴中心线与尾座中心线同轴,并与车床大导轨平行,允差应小于0.02 mm;刀具选择上注意选择75°~90°主偏角的车削刀具,使其加工工件时产生的径向切削力最小,而让刀片刃口产生的轴向力最大,并减小切削深度,增大进给量。

图2 自制断屑块
通过攻关解决了车削存在的问题,保证了产品质量。为验证车削加工杆身与磨削加工杆身加工效率的不同,选取相同数量的螺栓,分别采用2种方式进行加工,并对产品的加工时间进行统计,其平均加工时间如表1所示。
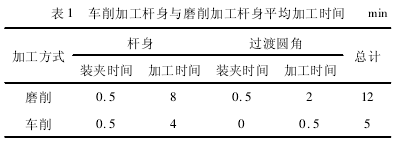
通过平均加工时间对比发现,车削杆身较磨削杆身的加工时间节约了约60%,加工效率提高。
3.2 滚压加工螺纹
螺栓两端的螺纹要求高,原加工方法是采用普通车床车削螺纹,车削效率低,同时由于螺纹长度较长,车削时容易产生振刀,螺纹表面粗糙度差,加之螺栓材料强度高、韧性好,刀具磨损快,螺纹尺寸不稳定。同时该螺栓组装时需要进行拉伸试验,由于车削螺纹强度低,拉伸时螺纹容易变形,导致螺母无法装配。
通过对螺纹加工性能的分析,结合公司现有螺纹加工设备和先进的螺纹加工方法,计划采用滚压的方式加工螺纹。为了验证滚压方案的可行性,首先对螺纹滚压力进行计算。
螺纹滚压力F简易计算公式:

通过查阅相关资料得出相关参数的数值:材料布氏硬度:HB296~350选上限值HB350、螺栓材料系数Z=4、材料延伸率A=10%、螺纹螺距P=3、螺栓有效长度为L:116~140 mm,选长端140 mm。
参考压力计算:

考虑1.2~1.5倍的保有量,滚压所需提供滚压力F1=1.2×F=57.36 Tnos、F2=1.5×F=71.7Tnos,而公司现有63 Tnos的滚丝机,满足滚压要求,滚压方案可行。
螺纹滚压是一种不去除材料的成型工艺,即用成型的滚压模具使工件产生塑性变形以获得螺纹的加工方法,见图3。
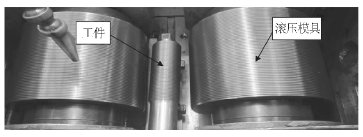
图3 螺纹滚压加工
通过对2种螺纹加工方式进行对比,滚压制作螺纹的优点突出。
(1) 滚压制作螺纹精度高。
滚压制作螺纹时,螺纹的精度主要取决于滚压坯的尺寸精度与滚压模具的精度。由于每批次螺栓的原材料及热处理存在差异,导致螺栓滚压时延伸量不同,影响螺栓的精度,因此每批次螺栓滚压坯的尺寸,是通过试滚确定的,即每次螺栓批量加工滚压坯前,先试加工几根,然后滚压,确定滚压精度后,再批量加工,有效保证螺纹滚压坯的尺寸精度。同时,对采购的滚压模具,进行合格性验证,严格控制滚压模具的精度,加之滚压模具的使用寿命远大于车削刀具的使用寿命,因此滚压制作螺栓的加工精度高、稳定性好。
(2) 滚压制作螺纹加工效率高。
螺栓的滚压是一种一次成型工艺,无须多次进刀,因此加工时间较车削短。同时滚压加工螺纹时,螺栓的固定装夹较车削简单方便,节约了大量的固定、装夹时间。为验证车削螺纹与滚压螺纹加工效率的差异,选择相同数量的螺栓,分别采用2种方式进行加工,平均加工时间统计如表2所示。

通过加工时间对比发现,滚压制作螺栓的加工效率较车削提高了2倍。
(3) 滚压制作螺纹强度高、表面粗糙度好。
滚压制作螺纹是一种无屑螺纹成型工艺,是通过滚压模具挤压坯料,使其发生塑性变形,按滚压模具的形状形成螺纹。
滚压制作螺纹与车削螺纹微粒流之间的区别如图3所示。可以明显地看出,滚压螺纹部分,材料出现塑性变形,使表层组织冷硬化和晶粒变细,形成残余的应力层,产生额外的拉伸强度,提高了螺纹的强度和硬度。同时滚压技术也是一种压力光整加工,利用金属在常温状态的冷塑性特点,利用滚压模具对工件表面施加一定的压力,使工件表层金属产生塑性流动,减小工件表面的凹凸峰谷之间的落差,从而达到较高的表面粗糙度。
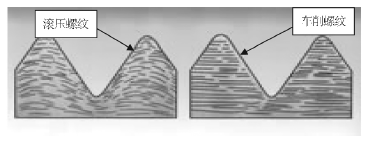
图4 滚压制作螺纹与车削螺纹微粒流之间的区别
(4) 滚压制作螺纹生产成本低。
滚压制作螺纹,采用不去除材料的方式加工螺纹,螺纹滚压前尺寸一般为螺纹的中径尺寸,而螺纹车削前的尺寸,一般为螺纹的大径尺寸,因此滚压制作螺纹比车削螺纹所需的坯料的尺寸小,对于大批量生产来说,这是一个很可观的数字,降低了生产的成本。
4、结束语
本文通过车削、磨削及滚压3种加工方式的优缺点对比,结合高强度精密螺栓的结构特性和技术要求,采用了以车代磨、以滚代车的加工方法,对高强度精密螺栓的加工方法进行了优化、改进,提高了螺栓的产品质量和加工效率。然而,随着加工刀具、设备及加工技术的不断进步,产品的加工方法也必须及时地优化、改进。
投稿箱:
如果您有机床行业、企业相关新闻稿件发表,或进行资讯合作,欢迎联系本网编辑部, 邮箱:skjcsc@vip.sina.com
如果您有机床行业、企业相关新闻稿件发表,或进行资讯合作,欢迎联系本网编辑部, 邮箱:skjcsc@vip.sina.com
更多相关信息