钼合金零件螺纹车削的两种工艺方法
2017-1-10 来源:江南工业集团有限公司 作者:王海云 李文平 彭红 姚春臣 常海 段良
摘要:为解决TZM钼合金件螺纹车削加工中刀具磨损、零件崩裂、掉扣等问题,本文分别采用不同机床和不同加工工艺进行了TZM钼合金件螺纹切削加工对比试验,以及在刀具材料、刀具角度、切削用量等方面的改进试验。通过试验,优选出两种分别适用于普通车床和数控车床较佳的工艺方法。试验结果和生产应用的情况表明,钼合金件螺纹的这两种车削加工工艺方法,都可以使切屑成形好,便于排屑,减少刀具磨损,防止螺纹崩裂、挤伤,从而获得较理想的螺纹加工质量和加工效率。
关键词:钼合金;TZM;螺纹车削;低速车削;高速车削;工艺方法
随着科学技术的发展和产品的更新换代,钼及其钼合金在军工和民用产品中的应用越来越广。但是,这些材料在切削加工中经常发生刀具磨损、零件崩裂等问题,导致产品质量差、生产效率低,特别是钼合金零件的螺纹,过去采用磨削的方法加工,其加工效率太低,难以满足生产需求,
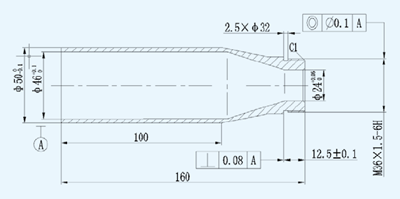
图1 某筒体零件结构外形图
而改用车削加工,则很容易出现崩裂、挤伤等问题,导致报废。因此,钼合金螺纹的加工问题成为当时本单位机械加工中的技术瓶颈。为了解决这一问题,确保产品质量、提高工作效率,降低生产成本,本单位以TZM 钼合金为主,对钼合金零件的螺纹车削工艺及其刀具进行了一些改进试验。
钼的密度为10.22g/cm3,熔点为2625℃,属于稀有高熔点金属[1]。TZM 合金是钼基高温合金中的一种, 含有0.40 ~ 0.60%Ti,0.06 ~ 0.12%Zr,0.01 ~ 0.04%C,属于钼钛锆合金[2]。TZM 合金具有熔点高、强度高、弹性模量高、导电导热性好、抗腐蚀能力强和高温性能好等优点。
1.零件介绍及加工难点
某筒体零件结构外形如图1 所示,材料为TZM棒料, 零件长160mm, 壁厚2mm, 右端外螺纹M36×1.5-6g, 由于材料本身的特点, 该零件在加工过程中主要存在以下几个问题。
1)加工过程中切削刀具磨损严重, 刀具损耗大,成本高;
2)零件容易产生崩裂、掉屑、挤伤、甚至会断裂;
3)零件表面质量差, 螺纹掉扣严重;
4)在以往加工过程中,由于没找到好的刀具材料和最佳切削参数,故一天只能加工少量产品,生产效率低。
2.钼合金螺纹切削试验
为了解决钼合金零件螺纹车削加工难的问题,本文针对TZM 钼合金零件的M36×1.5-6g 外螺纹,分别在普通车床和数控车床上,采用高速和低速切削螺纹两种不同的方法进行了多次切削加工试验。其不同切削加工方法及效果的对比见表1。从表1 可见,在普通车床上车制这种钼合金螺纹时,要低速切削,速度低,切削冲击力小, Vc 控制在20r/min ~ 30r/min,刀具牙型角要小于标准的60 o,选58.5 o ~ 59 o,前角γ 取5 o ~ 10 o,后角α 取10 o ~ 15 o,刀具必须锋利,进给量ap 控制在0.02 ~ 0.04mm。在数控车床上车制这种钼合金螺纹时,要高速切削,采用斜进法(按G72 指令编程),Vc 控制在1500 ~ 1800r/min 之间, 刀具采用肯纳的NT2RKK5010 刀片,进给量控制在0.015 ~ 0.02mm 之间。通过上述多次试验以及后来生产中的实际应用,使本单位掌握了分别适用于普通车床和数控车床的两种不同的TZM 钼合金切削加工工艺。
3.普通车床低速车削螺纹工艺
这种工艺适用于在普通车床上车削TZM 钼合金
表1 TZM 钼合金螺纹的不同切削加工方法及效果的对比
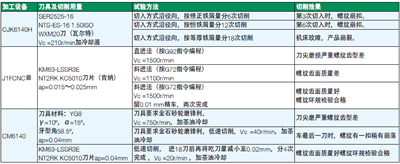
3.1 刀具材料和形状
车钼合金材料上的螺纹用 YG 类硬质合金,一般选用YG8、YG6X 焊接螺纹车刀。车刀的形状被直接复制到工件上,因此刀具的形状制作是否准确很重要,若采用粗车和精车分别加工,可得到较理想的表面粗糙度和精度。粗车刀的牙型角常取58.5 ~ 59° , 比精车刀的牙型角要小1 ~ 1.5° ,用粗车刀车至牙深, 然后用精车刀车光螺纹2 个侧面,既保护刀尖又省时。刃磨粗车螺纹刀时, 不需刻意磨小刀尖角, 只需在开始车刀前角时适当加大前角, 这样既能达到排屑顺利的目的, 又可减小牙型角。但前角加大, 楔角减小后, 车刀的强度就会降低, 所以后角要适当减小, 这样可弥补车刀强度的不足。粗车刀前角可以取大些 ( 5 ~ 10 ° ),其刀刃锋利,便于排屑和减少切削阻力,切削轻快。精车刀,则必须保证前刀面和水平面平行,即径向前角为 0°,以保证牙形角正确。
3.2 切削用量
螺纹加工要求主轴转速和刀具进给速度之间保持严格的速比关系。即主轴每转一转,刀具应均匀地移动一个导程的距离。刀具切削部分在螺纹加工时的工作条件非常恶劣,不仅切削力大,而且摩擦剧烈,发热严重,刀具材料本身对切削线速度也有一定的限制。螺纹加工主轴转速 Vc 控制在 20 ~ 40r/min 即可,进刀量控制在0.02-0.04mm,可以分粗车、精车多次切削完成同一螺纹的加工。
4.数控车床高速车削螺纹工艺
这种工艺适用于在数控车床上车削TZM 钼合金螺纹。
4.1 螺纹数控车削加工分析
由于数控机床本身有速度控制、位置控制和精度控制等方面的特点,故数控机床螺纹加工方式与传统螺纹加工方式相比,在加工精度、加工效率等方面都具有明显的优势。
1)直进法:螺纹车刀X 向间歇进给至牙深处。采用此种方法加工钼合金螺纹时,螺纹车刀的三面都参与切削,导致加工排屑困难,切削力和切削热增加,刀尖磨损严重,当进刀量过大时,还可能产生扎刀和爆刀现象。这种方法在数控车床上采用指令G92 来实现。很显然,这种方法不可取。
2)斜进法:螺纹车刀沿牙型角方向斜向间歇进给至牙深处。
采用此种方法加工螺纹时,螺纹车刀始终只有一
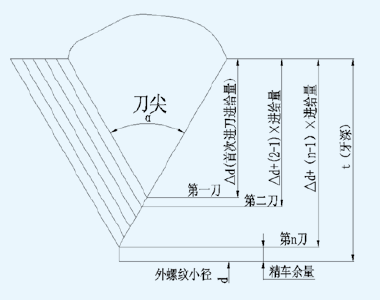
图2 斜进法的螺纹循环加工吃刀深度分布情况
个侧刃参加切削,从而使排屑比较顺利,刀尖的受力和受热情况有所改善,在车削时不易引起扎刀现象。这种方法在数控车床上采用指令G76 来实现进刀方式。G76 通过多次螺纹粗车、精车完成规定牙高(总切深)的螺纹加工,如果定义的螺纹角度不为零,螺纹粗车的切入点由螺纹牙顶,逐步移至螺纹牙底,使得相邻两牙螺纹夹角为规定的螺纹角度,可实现单侧刀刃螺纹切削,吃刀量逐渐减小,有利于保护刀具,提高螺纹精度。
4.2 G76 指令车削螺纹编程技巧
在G76 螺纹切削循环中,螺纹刀以斜进的方式进行螺纹切削,总的螺纹深度(牙高)一般以递减方式分配。第一次切削时,背吃刀量为△ d,约为牙高的12%,第二次切削深度△ f,选择较小的进给量(0.015 ~ 0.025mm),第n 次的切削深度为△ d+(n-1)△ f,每次循环的背吃刀量为△ f,最后精车0.01 mm左右, 分两次光整。螺纹单刃切削如图2 所示。
G76 指令编程如下:
T44 ;
M3 ;
GO X50 Z0 ;
G76 P02 0060 Q25 R10 ;
G76 X30.5 Z27 R0 P750 Q100 F1.5 ;
G0 Z30
5.工件和刀具装夹
5.1 工件的装夹
TZM 合金材质很脆,夹持零件时,力度要适中,受力均匀,用力过大或稍不注意,则导致其加工过程中出现裂纹。车削时,应采用软爪卡盘, TZM 合金零件可选用扇形爪,可增大与工件接触面积而使工件受力均匀,车削软爪的直径最好与被装夹工件直径一致,或大或小,都不能保证装夹精度,一般卡爪车削直径比工件直径大0.1 ~ 0.15mm。
除了工件安装要牢固、平稳, 还要考虑工件本身的刚性。刚性不足,则不能承受车削时的切削力,产生过大的挠度,改变了车刀与工件的中心高度,工件被抬高了,形成切削深度突增,会出现扎刀现象,此时应把工件装夹牢固,可使用尾座顶尖等,以增加工件刚性。
5.2 刀具安装
在安装螺纹车刀时,要尽量减少伸出长度,防止刀杆刚性不足而产生振动。刀杆要垂直于主轴方向,保证牙型准确对称。理论上螺纹车刀安装高度要与回转轴线等高,过高或过低都会出现扎刀现象,安装过高,吃刀到一定深度时,后刀面会顶住工件,增大摩擦力,甚至把工件顶弯,造成扎刀;安装过低,则切屑不易排出,车刀径向力的方向是工件中心,加上横进丝杠与螺母间隙的影响,致使吃刀深度不断自动趋向加深,从而把工件顶起,出现扎刀现象。加工过程中,粗车、半精车时理想的刀尖位置是比工件中心略高 0.1 ~ 0.3 mm ,精车时则应力求使刀尖和螺纹中心等高。
6.应用效果
上述两种工艺方法,分别解决了在普通车床和在数控车床上加工TZM 钼合金螺纹的崩裂、掉屑、挤伤、掉扣等质量问题,现都已应用于产品生产。用普通车床加工TZM 钼合金螺纹,生产效率远比磨削加工螺纹高,而数控车床加工的效率则更高,由于既可以用普通车床加工,又可以用数控车床加工,更便于生产管理人员安排生产,确保了产品加工任务按期完成。图2 斜进法的螺纹循环加工吃刀深度分布情况
上述两种工艺方法,还可以推广应用于钼和其它某合金螺纹的加工。
7.结束语
TZM 钼合金螺纹的不同切削加工机床和不同加工工艺对比试验结果说明,普通车床低速螺纹车削工艺方法和数控车床高速斜进式螺纹车削工艺方法,都可以使切屑成形好,便于排屑,减少刀具磨损,防止螺纹崩裂、挤伤,从而确保和提高螺纹加工质量。生产应用的情况说明,上述两种钼合金车削加工方法,解决了TZM 钼合金螺纹车削加工的技术和质量问题,而且加工效率比磨削高,又便于安排生产,有利于加快生产进度。
投稿箱:
如果您有机床行业、企业相关新闻稿件发表,或进行资讯合作,欢迎联系本网编辑部, 邮箱:skjcsc@vip.sina.com
如果您有机床行业、企业相关新闻稿件发表,或进行资讯合作,欢迎联系本网编辑部, 邮箱:skjcsc@vip.sina.com