Fanuc 加工中心滚珠丝杠在线检测技术
2019-3-27 来源: 上汽通用五菱汽车股份有限公司 作者:蒙旭喜,杨 明,陈 斌
摘 要:Fanuc 31i CNC 加工中心按照工作台往复移动加工零件。丝杠作为关键传动部件,拥有高精度、高传动效率及耐磨性。滚珠丝杠失效会产生机床共振、加工尺寸超差、加工刀痕、工件表面粗糙度不合格问题。利用 SEVRO GUIDE 检测丝杆位置误差,并提取 Q-DAS 数据进行状态识别,可快速判定丝杠磨损程度,及时进行加工精度调整或更换。
丝杠在线检测对同类型的加工中心普遍适用,计算方法基本一致。论文简述滚珠丝杠检测技术、抑制机床振动、加工精度调整、丝杠失效模式分析。目的是为丝杠的状态监控及精度调整提供一种方法,以降低丝杠失效带来的损失和提高加工精度。现场实践表明方法有效。
关键词:加工中心;Servo Guide;丝杠检测;加工精度调整;丝杠失效模式
在发动机制造设备中,加工中心完成 60%的工序,加工中心设备数量占比例 75%. 气缸体
、气缸盖的大部分加工内容是由加工中心完成。按 4 轴联动加工中心计算,一个年产 40 万产能的发动机需 108台 CNC,共用 108 × 3 = 324 根滚珠丝杠。
产品的加工质量取决于工作台的定位的精度,而工作台由滚珠丝杠传动。滚珠丝杠失效后,表现为气缸体缸孔刀痕、气缸盖座圈/导管底孔直径超差等质量问题,易引发批量质量风险。
传统处理方式为,根据经验手动旋转丝杆与螺母副的间隙、或跟踪诊断号 #550-553 半闭环与全闭环误差补偿值大小直接更换丝杠,无法判定滚珠丝杠的磨损状况及程度,存在误判及发现质量隐患的滞后性。
本文利用 Ser-vo Guide 工具监控调整丝杠状态,提取 Q-DAS 数据进行状态识别,可以随时跟踪丝杠磨损程度、调整机床加工精度,解决各类机床共振、加工刀痕、加工超差等问题。如图1 所示。
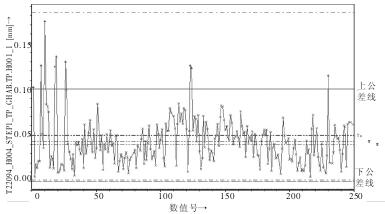
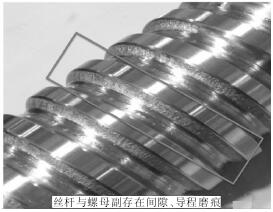
图 1 滚珠丝杠失效加工超差
1 、滚珠丝杠位置误差的产生
机床的每一根轴都是由伺服系统所驱动的,系统的组成是由伺服轴卡、伺服驱动器、伺服电机组成。它的主要作用是由伺服系统接受 NC 所发出的位置指令来驱动电机进行定位控制。加工中心 X、Y、Z 轴由滚珠丝杠传动。通过伺服同步电机实现驱动。加工过程中滚珠丝杠螺母副往复运动不可避免产生反转间隙,较大的反转间隙造成工作台反向移动时,坐标显示移动而实际工作台未移动,使半闭环系统与全闭环系统位置环误差超过参数 #2118 的设定值,机床震动不稳定。
滚珠丝杠磨损越大反向间隙远大,振荡越不稳定。其称为位置误差,位置误差震荡越大,机床越不稳定。此时机床常伴随伺服轴报警。半闭环系统与全闭环系统控制的位置误差增大,常表现为如下报警代码:410 代码:某轴停止中的位置偏差量超过了参数#1829 设定的值,可能该轴的反馈电缆损坏,编码器故障或放大器控制板损坏。
411 代码:某轴移动中的位置偏差量超过了参数#1828 设定的值,可能该轴的反馈电缆损坏,编码器故障或放大器控制板损坏。421 代码:采用双位置反馈功能时,半闭环的反馈误差与全闭环的反馈误差之差值超过了参数 2118设定的值,可能该轴的光栅尺或电机编码器反馈电缆损坏,光栅尺或编码器故障或放大器控制板损坏。
锁定问题方法 1:放大 2118 参数报警值,空运行/手动移轴查看诊断号 550(全闭环)、551(半闭环)数值变化。 方法 2:屏蔽光栅尺循环。此时可快速是否为滚珠丝杠位置误差产生震荡。机床伺服驱动控制通讯方式如图 2 所示。
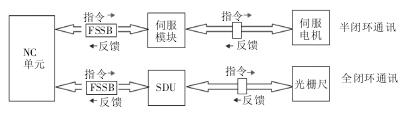
图 2 机床伺服驱动通讯方式如图
2 、位置误差检测方法—Servo Guide
ERRC 表示驱动装置的误差值,因 ERRC=进给速度/位置增益,故当进给一定时,ERRC 理论上一定。由于丝杠、螺母副、轴承磨损,导致驱动装置构件间约束发生变化,系统定位时,为达到准确定位,必须不断进行调整,从而体现为机床某轴驱动装置振动。机床位置增益设定值越高,相同进给速度下,ERRC 值越小,但同时要求机床驱动装置刚度和约束越高。
当机床驱动装置刚度和约束无法与机床位置增益匹配时,振动发生。ERRC 曲线可作为表征丝杠状态的一个指标。ERRC 监控方法如图 3 所示。
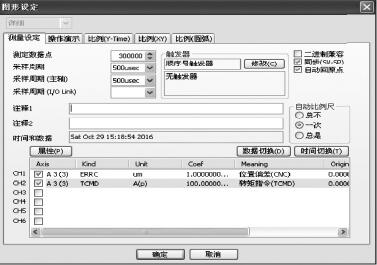
图 3 图形设置
通过对同一台机床在同一进给不同 1825(位置增益)值下的监控,可发现位置增益越小机床 ERRC越大,但由于同时降低机床定位的敏感度,机床振动降低,ERRC 曲线的振幅降低。因此,可通过对驱动装置的 ERRC 曲线进行定期收集,建立数据库,通过大量数据的分析,对不同工位的驱动装置状态进行评估,以制定有效的预测性维修。如图 4 所示的正常丝杠 ERRC,通过检测对比T0001 刀具在加工时的 Z 轴位置偏差(ERRC)曲线,97 000~100 000 ms、101 000~105 500 ms 无震荡,误差值波动范围将近 2~3 μm(正常范围 25 μm 以下)。该机床 Z 轴丝杠正常。
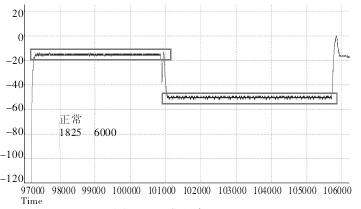
图 4 正常丝杠 ERRC
如图 5 所示的故障丝杠 ERRC,检测对比 T0001刀具在加工时的 Z 轴位置偏差(ERRC)曲线,75 550~ 79 500 ms、80 000~84 500 ms 震荡,误差值波动范围将近 56 ~ 57 μm. 该机床
Z 轴丝杠异常。判定丝杠、螺母副、轴承磨损。此时机床可能会产生共振、加工刀痕、加工超差等问题。
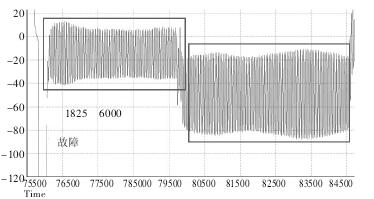
图 5 故障丝杠 ERRC
3、 误差计算及加工精度调整
FANUC SEVRO GUIDE 首先测量位置误差大小,再通过对系统内部参数进行调整重置:一是抑制设备异常震动 (#1825/#1828/#2118/2021 位置环、速度环增益进行调整),通过在线测量机床响应频率来手动调整;二是调整机床加工精度 (系统功能的调整),通过观察畸形零件来调整。
抑制机床震动是基础,调整加工精度是进一步发挥机床性能,可以实现伺服轴丝杠测量、自动调整功能及调整引导功能。
3.1 滚珠丝杠位置误差计算
滚珠丝杠传动中位置误差的计算及相关参数调整。No2021:负载惯量,其值决定速度增益。速度增益=[No2021+256/256] ×100No1825:位置环增益,单位 0.01/S 误差量(P)= [进给速度/60×位置增益] ×1/检测单位No1826:快速指令的到位宽度。No1827:切削指令的到位宽度。到位:定位结束。系统根据移动指令和反馈指令的差值的多少,来确定是否定位结束。位置偏差值存放在误差寄存器中,其值可以通过诊断 DGN300 读出。
No1828:移动中的误差极限值,当误差寄存器数值超过其值,ALM411 报警。No1829:静止时的误差极限值,当误差寄存器数值超过其值,ALM410 报警。
3.2 Servo Guide 调整原则
(1)提高位置增益,可以改善系统的定位及加工精度,调整量以不使系统产生振动与过冲为前提,同时所有的差补轴的增益需保持一致。
(2)提高速度增益,可以改善电机的速度响应,提高加速能力,但过高的速度增益会使机床产生振动。
(3)当振动出现时,可以在降低速度及位置增益之前使用转矩指令滤波器进行调整,如因机床的机械刚性等原因不能产生效果后,可降低速度及位置增益。
转矩指令滤波器:将输出的转矩指令中包含的高于设定频率的共振频率对应的转距指令滤掉,以降低振动。
3.3 加工精度调整方法(ERRC)
调整机床加工精度方法应该从两方面着手:控制系统方面和驱动方面。系统方面使用 AIAPC 或AICC. 驱动方面主要通过调整伺服位置环增益(PRM1825速度环增益(PRM 2021)参数来实现,使之越宽越好。
3.3.1 控制系统调整方法
首先设定控制系统和驱动方面的参数。这些参数对于提高机床性能非常重要,建议按照以下的说明进行设定。以系统是 0i-B/C 为例设定 AICC 以下参数。
No1620=100———各轴快速进给直线型加减速时间常数 T1;No1621=8———各轴快速进给铃型加减速时间常数 T2:
No1732 =100———基于圆弧半径进给速度下限值;No1768=16———AIAPC 模式下插补后加减速时间常数;
No1770=10000———AIAPC 模式下插补前加减速最大进给速度;
No1771=200———AIAPC 模式下插补前直线型加减速到达最大进给速度的时间;
No1772=48———AIAPC 模式下插补前钟型加减速时间常数;
No 1602#6#3 =1,0———先行控制下插补后加减速为直线型(当使用插补前钟型加减速时设定)
3.3.2 驱动方面调整方法
手动设定降低位置增益参数 1825,同时增大移动过程误差值参数 1828,可以改善丝杠定位产生振动,对带有圆弧插补、曲线、倒角等加工差补轴的增益需保持一致。
有参数调整应以不影响加工精度、调整量为前提。手动设定完以上参数之后,系统的性能应有一定的提高。如果调整位置环增益还达不到精度要求,只能其他因素考虑:机床的机械传动部
分,进给量、进刀方式、刀具、程序、夹具零部件、机构松动、传感装置误感应、工件本身问题
、速度、冷却方式、传动机构共振等。
这些因素都会对加工质量过程产生影响。以故障机床 ERRC 为例,调整后如下图 6、图 7 所示。
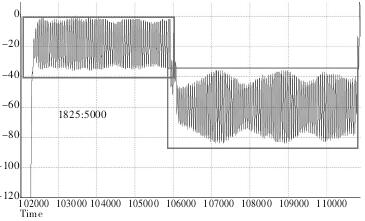
图 6 调整 1 丝杠 ERRC
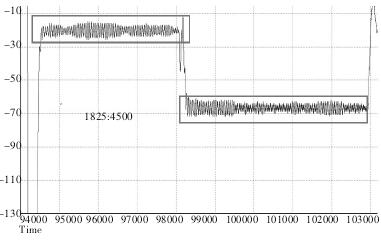
图 7 调整 2 丝杠 ERRC
修改参数1 825 = 5 000/4 500 后,检测对比T0001 刀具在加工时的 Z 轴位置偏差(ERRC)曲线无震荡,误差值波动范围将近 0≤25 μm. 该机床 Z 轴移动位置误差正常、加工正常、抑制机床震动。
4 、滚珠丝杠失效状态识别
滚珠丝杠由于长期的运行产生磨损间隙,将直接影响加工中心的传动精度及刚性。一般现象为反向间隙大、定位精度不稳定、机床产生震动、螺母副卡滞、进给爬行等。系统及参数调整已经超过调整量,加工精度不能满足要求时基本可以判定该丝杠已失效。
以下图 Servo Guide 位置偏差(ERRC)曲线检测、Q-DAS 数据状态识别为例说明(见图 8
)
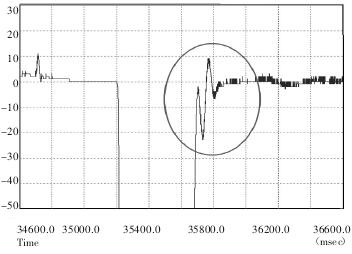
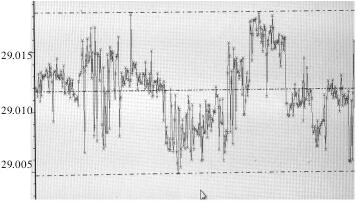
图 8 丝杠失效 ERRC
对比 T0001 加工 Z 轴 Q-ADS 数据上下波动不稳定、位置偏差(ERRC)曲线震荡严重,
Z 轴加工过程 400ms 震荡,误差值波动范围将近 60 μm. 而这个震荡有可能导致机床共振
、加工尺寸超差、加工刀痕、工件表面粗糙度不合格问题。
通过对比可确认该滚珠丝杠严重磨损,需更换处理。
5 、结束语
通过 Fanuc 加工中心滚珠丝杠在线检测技术,测量判别位置误差的产生方式,使用 Q-DAS
数据进行状态识别,建立 Servo Guide PDM 数据。计算当前位置误差,进行加工精度调整,解决加工中心机床振动、提高加工精度、快速识别滚珠丝杠失效模式,从而推进汽车发动机加工中心大批量生产过程的自动化、网联化及稳定性。
投稿箱:
如果您有机床行业、企业相关新闻稿件发表,或进行资讯合作,欢迎联系本网编辑部, 邮箱:skjcsc@vip.sina.com
如果您有机床行业、企业相关新闻稿件发表,或进行资讯合作,欢迎联系本网编辑部, 邮箱:skjcsc@vip.sina.com
更多相关信息