加工中心实践教学安全体系的构建与实施
2018-5-21 来源:转载 作者:王 成,刘孝赵
【摘要】以苏州经贸职业技术学院在自身发展及机电一体化专业多年实践教学经验为例,讲述了加工中心实训教学中教学管理、教学方法等多方面的管理、教学经验与技术手段,通过这些方法使得在加工中心实践教学的安全体系的建设上取得了显著的效果。
关键词:安全体系;教学管理;工艺改良;刀具;编程
1、引言
安全文明生产是操作者和设备安全的根本保证,是考核企事业单位在安全管理体系的重要指标,它直接影响着操作者安全、产品质量和生产效率的提高。在高等职业学院的实践教学中就要教好学生这一重要知识。我院机加工实训车间从教学管理、技术改进、教学方法创新等多方面着手,长期致力于加工中心安全教学工作的不断创新,取得了很好的效果。以下作者就数控加工中心安全体系方面的构建与实施作如下探讨。
2 、严格教学管理制度、提高学生安全意识
对于本院机电系工科类专业,尤其是机床操作的实训安全是教学管理的重点问题,对于如何有效地提高安全性,我们在实训管理制度和学生思想上进行了必要的规范及引导。
学院本着以学生安全为本的原则,机电系机加工实训车间严格执行规章制度,同时采用多形式、多方法对学生在实训中的安全进行耐心的讲解。使学生明白安全文明生产在实训和工作中的重要意义以及事故发生后的危害性和重要性。
本校数控专业学生数控机床操作上都是初学,在刚接触到机床时对于机床上的很多按钮有很高的探知欲,总想试着去按一下什么按键,针对这种学生的心理状态,实训教师会耐心的向学生讲解要严格按照教学进程和指导教师的步骤去操作的必要性。定期以班级为主体,开展“安全操作,规范自我”的主题班会,使学生发表各自在实训中应该要注意的安全问题及自身感悟。此外,还邀请企业一线工程师前来讲授真实的工作环境及企业规范,组织学生参观企业的生产车间,使学生意识到生产安全的重要性,为以后的工作打下安全基础。通过多种安全教育措施,提高了学生的安全意识,在实践教学操作过程中都以学院“加工中心操作规程”来严格要求自己,极大地提高了实训的安全。
3 、通过工艺的改良提高安全性
合理制定零件的加工工艺是进行数控加工的一项基础性的重要工作,在加工中所有工艺参数必须在零件的数控加工程序中准确地体现,这就要求加工程序要有极高的正确性和合理性,同时在对图形进行数学处理和编程时要力求准确无误,否则就可能酿成重大安全事故。针对此项分析了有可能产生的事故的原因和避免措施。
3.1 刀具选择方面
刀具合理选择是工艺的一部分,正确选择合适的刀具决定着是否能够安全切削、是否能够提高加工效率、是否能够节省成本。
(1)对于不同的加工材料应选用不同的刀具,对于我院学生来说都是初学者,为节约成本保证安全,在单步的实践操作时选用塑料工件,刀具采用普通高速钢铣刀。训练一段时间后工件换成铝材,而此时刀具选用稍好点的高速钢铣刀。在后期学生单独操作时,为保证加工精度及表面质量,刀具采用有色金属专用切削刀具。
(2)在刀具直径上应满足零件加工要求的前提下尽可能选择直径大的铣刀。如刀具半径比凹圆弧半径大将轮廓加工不到位,与刀具半径补偿号内的值发生干涉,机床将报警或产生过切,导致工件无法加工,如图 1 所示。如刀具直径选择过小,不仅影响加工效率,有可能致使刀具的折断,出现加工事故。故所选刀具半径+精加工余量零件过渡圆角R。
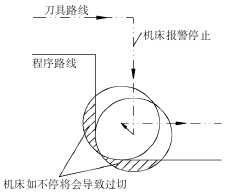
图1 过切现象
3.2 在程序编制上的安全措施
设定“安全指令”:以FANUC 0i Mate-MD操作系统为例,编程时在程序头设定“安全指令”有利于将前一个程序执行后某些未取消的指令进行复位,可有地避免因续效指令未取消而带来的错误,出现安全隐患。安全指令是:G94 G90 G17 G21 G15 G69 G80G40,例如上个程序执行 G68(坐标系旋转指令)后未取消,则现在就会因坐标系旋转后无法定位,导致坐标系错误发生事故。又如上个操作人员执行了 G95(每转进给量)指令未及时取消,在执行该程序时会出现进给速度很快的现象(参数设定与以往一样F100),非常容易出现撞刀事故。实践证明,在学生编程时加入了“安全指令”后,可有效地提高了加工程序的正确性,降低事故的发生。
铣削内腔时的分段执行:对于初学者来说,对于刀具轨迹不是很清楚,往往将两个程序语句段写在一起,导致撞刀的事故。以 FANUC-0i 系统,如图 2 所示为例,如程序写成:G0 X0 Y0 Z100.的话,则Z轴与X、Y轴同时运动,走刀路线斜向运动发生碰撞,如图 2a 所示。如改成:G0 Z100; G0 X0 Y0;两个程序段的话,走刀路线先走Z轴向上运动到100mm位置后,再进行回X、Y轴原点,如图2b所示,这样就会避免碰撞事故.
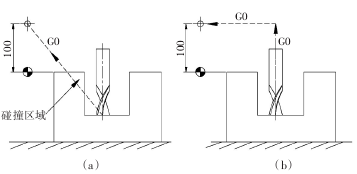
图2 内轮廓铣削碰撞实例
a——错误 b——正确
加工程序的检查:在程序编制完成后,对程序进行必要的检查可有效地降低机床的报警率,提高安全性能,主要对程序中的 Z 轴运动及 G0 的指令进行排查式收索。可有效地避免因误输入引起的撞刀事故。
3.3 工件及刀具装夹
铣刀在安装时夹持部分应适当,刀刃的伸出距离不能过长也不能过短,如过长,则夹持面积降低,所受力偶加大,刀具在加工过程中,容易变形或折断,容易产生安全事故。如过短,在加工过程中刀具在扭矩的作用下刀刃部分会损坏夹持套的内壁表面,或在切削中可能因为工件的加工深度问题,致使发生碰撞事故,如图3所示。
故铣刀在装夹时应根据图纸的深度要求和保证工具安全的前提下,铣刀端部距离刀柄底端部尽可能短,以保证刀具在加工时的强度,降低切削时的变形量,提高刀具使用寿命,从而提高安全性。
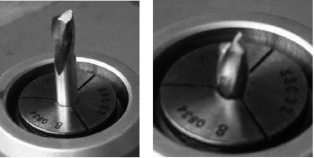
图3 铣刀安装
a——装刀过长 b——装刀过短
3.4 刀具对刀及对刀检测
刀具在X、Y方向用试切法对刀时,应及时将刀具抬至工件上方,以避免刀具与工件横向碰撞,如图4所示,进给速度上应用手轮控制,当将要碰到工件时将倍率旋钮调至X10或X1位置,如图5所示,以避免因速度过快导致刀具的快速切削,致使刀具折断或影响其寿命。
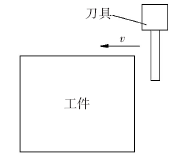
图4 横向碰撞
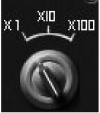
图5 进给倍率
以往学生在对完刀之后,就迫切地去执行程序,以为加工程序没有问题就不会出事,但往往因为忽略对刀检测从而导致撞刀事故,实训教师在根据自身教学经验,教学中加入对刀检查程序,这样对完一把刀就用程序进行检查,有问题及时解决,从而避免了由于对刀出现的事故。以FANUC 0i操作系统机床对刀检查程序如下:
O1;
T1M6;
G90G54G0G43Z100.H01;
M30;
以 1 号刀为例,将快速倍率旋钮调至 0 速度—运行程序—打开快速倍率—程序继续运行,程序运行中可目测刀具与工件坐标系Z轴的距离情况,如偏差过大立即停止。当程序运行结束后,用等高量块测量距离就可以判断对刀是否正确。
3.5 机床空运行及图形模拟
在所有工作都调试好,运用机床的图形模拟功能对该程序进行加工前的最后检查工作,将坐标系的Z轴调高100mm进行机床空运行,在程序运行中除了观察真实刀具的轨迹外,还可查看机床显示的图形形状,可有效地防止事故的发生。
3.6 常态下旋钮所处位置
有时操作人员或他人不小心或无意之间碰上面板上的启动按钮,导致正在装夹常态下“功能旋钮”放在“编辑”位置上和“进给倍率”放在最小进给位置上,如图6所示,可避免因他人误操作或不小心碰到机床时导致的机床运动,从而避免意外的发生,提高安全性。
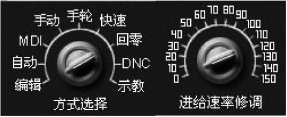
图6 常态旋钮位置
4 、小结
学院机加工实训车间建立了以上安全体系后,极大的提高了加工中心实践课程的安全性,在加工中心实训上一直保持零事故率,大大降低了实训耗材,节省了成本,每年为社会输送了一定数量的高技能应用型人才。实践证明:利用科学的管理和教学方法以及通过技术手段建立的安全体系有效地解决了学生在加工中心实训方面有可能出现的安全隐患,确保了学生在加工中心实训中的安全,取得了良好的效果。
来源:苏州经贸职业技术学院机电系,江苏省光伏风电控制工程技术研发中心
投稿箱:
如果您有机床行业、企业相关新闻稿件发表,或进行资讯合作,欢迎联系本网编辑部, 邮箱:skjcsc@vip.sina.com
如果您有机床行业、企业相关新闻稿件发表,或进行资讯合作,欢迎联系本网编辑部, 邮箱:skjcsc@vip.sina.com