超大孔径聚晶金刚石拉丝模具单向走丝电火花线切割加工工艺研究
2016-11-10 来源:北京迪蒙吉意超硬材料技术有限公司 作者:康凯敏,曹凤国,桂小波
摘要:基于试验研究,创新性地提出了采用单向走丝电火花线切割机床对超大孔径聚晶金刚石拉丝模具的孔形进行粗加工。以金刚石粒度为25 μm 的直径22 mm、厚度20 mm 的超大孔径聚晶金刚石拉丝模具为例,进行单向走丝电火花线切割加工定径区、压缩区和安全角的工艺研究,得出了加工工艺曲线,确定了最优加工工艺参数,提高了粗加工效率,确保了良好的孔形精度。结果表明:选择脉冲宽度4 μs、脉冲间隔40 μs、峰值电流15 A、走丝速度10 m/min 时,可获得较满意的加工效果。
关键词:聚晶金刚石;超大孔径拉丝模具;单向走丝电火花线切割加工;锥度加工
对传统的钢芯拉丝模具孔形,最早采用机械研磨的加工方法,即用机械传动的方式带动研磨工具(如磨针、磨锥、丝、绳等)作高速运动,利用研磨材料对模具孔形表面产生的磨削作用来加工孔形[1]。但对于聚晶金刚石(PCD)拉丝模具来说,模芯材料PCD 本身具有较高的硬度和抗压强度,且热导率极高、耐磨性较好,用传统的机械加工方法加工孔形时,工时长、效率低、废品率高,很难保证孔形尺寸和表面质量。目前,较多采用电火花、激光及超声波等特种加工方法。电火花放电加工一般用于中、大孔径拉丝模具孔形的粗加工;激光加工适于微孔和小孔拉丝模具的粗加工;超声波加工主要用于拉丝模具的精加工[2]。
目前,国内模具制造厂家对于中、大孔径PCD拉丝模具,主要用电火花成形加工来完成定径区和各角度区域的粗加工, 用超声波研磨进行精加工。这种加工方法不但效率很低, 且由于电极损耗严重,加工出的孔形精度也低,并随着孔径的增大,加工难度越来越大。随着单向走丝电火花线切割技术在模具制作上的应用,采用单向走丝电火花线切割机床进行定径区和角度区域的粗加工成为可能,该机床的优势之一是能进行高精度的锥度加工。利用单向走丝电火花线切割+卧式超声波加工的方式进行超大孔径PCD 拉丝模具的加工,不仅粗加工效率提高了近3 倍,还提高了孔形精度。
本文以金刚石粒度为25 μm 的直径22 mm、厚度20 mm 的超大孔径PCD 拉丝模具为例, 进行单向走丝电火花线切割加工定径区、压缩区和安全角的工艺研究,确定最优加工工艺参数,并介绍了锥度加工方法及工艺技巧。
1. PCD 拉丝模具孔径分类
PCD 拉丝模具孔形结构见图1。按孔径d 的大小可分为微孔(d≤0.1 mm)、小孔(0.1 mm<d≤1.0mm)、中孔(1.0 mm<d≤3.0 mm)、大孔(3.0 mm<d≤10.0 mm)和超大孔(d>10 mm)。孔径大小不同,其加工方法也不尽相同。通常,对于PCD 拉丝模具的孔形加工方式,微孔、小孔采用激光+超声波加工;中孔、大孔采用电火花成形+超声波加工。
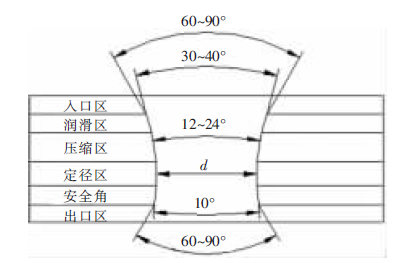
图1 PCD 拉丝模具孔形结构图
2. 超大孔径PCD 拉丝模具线切割加工工艺
实验采用AQ360 单向走丝电火花线切割机床,电极丝为直径0.2 mm 的黄铜丝, 加工介质为去离子水,加工方式为浸没式加工。利用单向走丝线切割机床切割拉丝模具时,需事先加工穿丝孔。实验用机床数据库虽然提供了加工PCD 的参考加工参数,但实际切割中,该参数不适合超大孔径PCD 拉丝模具的切割。超大孔径PCD拉丝模具的特点是孔径大、工件厚度大、材料粒度大,其切割工艺要求为:表面粗糙度均匀,孔形精度高,切割时间长,且切割过程不允许断丝,这些要求增加了线切割的加工难度。若在切割过程中发生断丝,在断丝部位会出现凹槽或凸棱,将给后续的超声研磨加工增加相当大的工作量, 既浪费磨料,时间和成本均增加,还影响模具精度。因此,有必要对超大孔径PCD 拉丝模具的线切割工艺进行研究,对脉冲宽度、脉冲间隔、峰值电流、伺服参考电压等电参数和其他非电参数进行分析及适当的调整,选择最佳的工艺参数,以提高切割速度和加工质量。
2.1 电参数对切割速度及表面质量的影响
2.1.1 脉冲宽度
脉冲宽度是单个脉冲能量的决定因素之一。脉冲宽度过小,脉冲能量不够,几乎无法加工PCD 材料。当脉冲宽度增加时,单个脉冲放电能量增加,切割速度也随之增加。图2 是超大孔径PCD 拉丝模具的切割速度随脉冲宽度变化的曲线。当脉冲宽度增大到一定值时,切割速度将不再与脉冲宽度呈正比增长关系,甚至还会随着脉冲宽度的增加而下降[3]。这主要是由于PCD 材料的导热率高,放电脉冲能量通过工件散发而损失,反而削弱了蚀除作用。电蚀产物的抛出作用不会随着脉冲宽度的增加而显著提高,使短路几率增大,加工变得不稳定,切割速度减小,甚至造成断丝。另外,由于单脉冲能量的增大会使电极丝振动加强, 从而增大表面粗糙度值,降低表面质量。
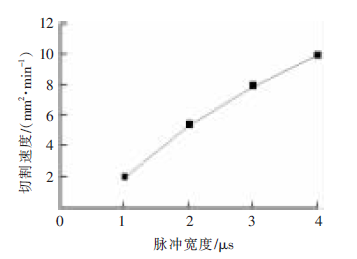
图2 切割速度随脉冲宽度变化的曲线
脉冲宽度过大,单个脉冲能量过大,金刚石颗粒被冲击或局部碎化脱落,或整体脱落,在加工表面将留下较大的凹陷,因此加工表面粗糙度值大[4]。金刚石粒度越大,留下的凹陷就越大,表面越粗糙,将给后续的研磨精加工增加难度。此外,还有可能使正常的脉冲放电状态转变为瞬间电弧放电状态,烧坏工件(图3a),或造成断丝现象时常发生。正常切割时的表面见图3b。超大孔径PCD 拉丝模具厚度大、排屑条件差,因此,线切割加工时一般不采用增加脉冲宽度的方法来提高切割速度,而普遍采用窄脉冲宽度、高峰值电流。
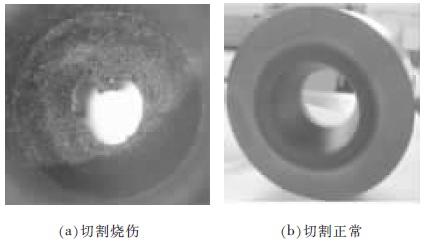
图3 切割烧伤与切割正常表面状况
2.1.2 脉冲间隔
脉冲间隔对超大孔径PCD 拉丝模具切割速度的影响较大,对表面粗糙度的影响较小。图4 是切割速度随脉冲间隔变化的曲线。脉冲间隔增大,脉冲空载百分率提高,加工稳定性提高,极间不易产生拉弧现象,但切割速度降低明显。脉冲间隔减小,会使脉冲放电频率增加,平均加工电流增大,切割速度提高;但脉冲间隔过小,会使放电间隙中的电蚀产物来不及排出,加工状态变得不稳定,影响切割速度的提高, 甚至会产生电弧放电烧断电极丝,使加工无法继续进行。因此,在工作液恢复极间绝缘性的条件下,可适当减小脉冲间隔,使单位时间内的放电次数增多,从而提高切割速度。
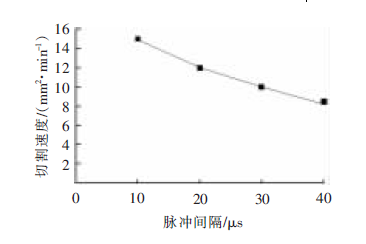
图4 切割速度随脉冲间隔变化的曲线
实际加工时,应根据超大孔径PCD 拉丝模具的厚度选取合理的脉冲间隔。脉冲宽度不能过小,否则压力冲液很难充分进入工件中间部位,不利于电蚀产物的排出,易断丝。因此,应选择较大的脉冲间隔加工,以保持加工的稳定性。
2.1.3 峰值电流
对于PCD 材料, 尤其是超大孔径PCD 拉丝模具的切割,应采用大脉冲能量、大峰值电流,否则能量太小,无法切割。与脉冲宽度的影响相似,随着峰值电流的增加,单个脉冲能量增大,切割速度提高,而表面粗糙度值却变大;同时,加工间隙大,也使加工精度降低。切割速度随峰值电流变化的曲线见图5。提高脉冲峰值电流可按比例提高单个脉冲的放电能量,单向走丝线切割加工在其他参数保持不变的情况下,提高单个脉冲能量就意味着提高切割加工的速度。但如同脉冲宽度和脉冲间隔的影响一样,峰值电流的提高也应在一定的范围内。若峰值电流过大,在冲液状况没有改善的情况下,切缝内排屑不畅,切割速度会减慢,并可能引起断丝。
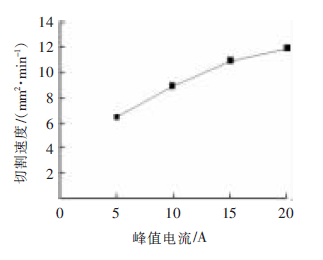
图5 切割速度随峰值电流变化的曲线
2.1.4 伺服参考电压
伺服参考电压是预先设定的用以控制电极丝前进和后退的标准电压。当平均加工电压高于该值时,电极丝前进;低于该值时,电极丝后退。切割PCD 时需杜绝发生断丝,因此切割超大孔径PCD 拉丝模具时,适当增加伺服参考电压的设定值,可增大电极丝和工件间的间隙,有利于排屑,使加工稳定,不易造成断丝。
2.1.5 伺服进给速度
切割PCD 材料时的伺服进给速度与切割普通材料不同,不允许伺服进给速度超过加工速度(即过进给)。因为当伺服进给速度超过加工速度后,对于普通材料会出现频繁的短路现象,同时增大了断丝的可能性; 而对于PCD 材料是直接将电极丝划断,影响了加工速度。因此,切割超大孔径PCD 拉丝模具时,伺服进给速度应略低于加工速度(即欠进给),以避免断丝。
2.1.6 开路电压
在正常情况下,提高开路电压会使切割速度显著提高,这是因为电压的提高必然使脉冲峰值电流和加工平均电流都提高,单个脉冲能量加大,对提高切割速度有利,但表面粗糙度值却变大;同时,加工间隙大,也使加工精度降低。切割加工超大孔径PCD 拉丝模具时,开路电压一般在100 V 左右。
2.2 非电参数对切割速度及表面质量的影响
2.2.1 走丝速度
走丝速度对切割速度有一定的影响。提高走丝速度,电蚀产物的排出速度也会加快,这将减少产生二次放电的几率,提高加工稳定性,从而提高切割速度。但走丝速度过快,将使电极丝振动加大,表面粗糙度变差,降低表面加工质量,也会造成电极丝的浪费;走丝速度过慢,会使电极丝上某一点可能产生多次放电,易造成断丝。因此,结合超大孔径PCD 拉丝模具定径区、压缩区和安全角的不同切割厚度,适当地调节走丝速度在9~10 m/min 为宜。
2.2.2 电极丝张力
电极丝张力在加工过程中应保持恒定, 它与PCD 厚度密切相关,PCD 越厚, 所需电极丝张力应越大。如果张力较小,电极丝的跨距较大,除了其振幅大以外,还会在加工过程中受放电爆炸力的作用而弯曲变形或抖动,造成腰鼓形状,且会降低模具的切割精度和表面粗糙度等级。电极丝的张力越大,加工时丝的振动幅度越小,加工变得稳定,尺寸精度高,表面质量好。但电极丝张力过大,在加工过程中易造成断丝,使加工无法继续。因此,在切割超大孔径PCD 拉丝模具的压缩区和安全角时,丝张力应比切割定径区适当增加10~20,确保角度的精度。
2.2.3 喷流压力
喷流的压力及流量直接影响线切割的加工速度和模具表面质量。为了将加工过程中产生的电蚀产物迅速排出,采用强喷流,且PCD 厚度越大,所需的喷流压力越大, 以便带走更多的热量及蚀除物,避免二次放电的发生,且不易断丝,切割速度提高。但喷流压力过高,造成电极丝抖动,反而降低了切割速度,同时造成加工精度及表面质量的降低。与电极丝张力调节一样, 在切割压缩区和安全角时,喷流压力应比切割定径区适当增加5~10 Hz (变频器频率),以确保角度的精度。
此外,实验用机床数据库中的加工条件给出了另外2 个有益参数,可通过调整其数值对脉冲的持续加工和加工稳定性进行控制。
(1)高压遮断
在通常的控制电路中增加遮断电路和高压电路,以对放电中单个脉冲的持续加工进行良好的控制。H 值越大,电压越高;R 和P 值越大,电阻值越小,能量越大。
(2)MAO
调整加工稳定性的参数,通过M 值对加工状态进行判断。若加工状态不稳定,脉冲间隔将根据设定的A 值倍率伸展, 脉冲宽度将被设定的O 值取代,从而提高加工稳定性。M 值越大,进行加工稳定性判断的频次越多,影响切割速度;A 值越大,伸展倍率越大,加工越稳定,但切割速度会降低;O 值越小,加工越稳定。通过以上一系列的实验,摸索出了加工超大孔
径PCD 拉丝模具的工艺参数(表1)。
表1 加工超大孔径PCD 拉丝模具工艺参数
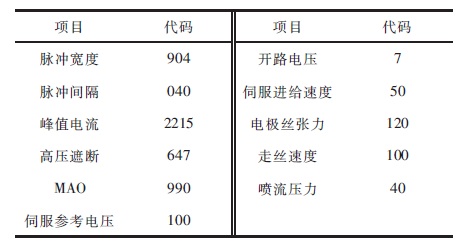
注:表中参数值均以实验用机床加工条件代码表示。
2.3 锥度加工的原理及技巧
通过单向走丝线切割机床的锥度切割功能可精确加工压缩区和安全角,这为高效率、高质量加工超大孔径PCD 拉丝模具部分区域的角度提供了精度保障。
2.3.1 锥度加工原理
数控单向走丝线切割机床的上、下导丝器两点形成一条直线,下导丝器中心轴线不动,上导丝器通过步进电机驱动U、V 轴的移动,使电极丝与垂直线偏移角度, 并与X、Y 轴按轨迹运动实现锥度加工。图6 是锥度加工示意图,U、V 轴移动距离越大,产生的锥度就越大,实验用放电加工机的U、V 轴最大移动距离为80 mm。在进行角度区域加工时,应注意U、V 轴的行程是否会超出机床的限定范围。
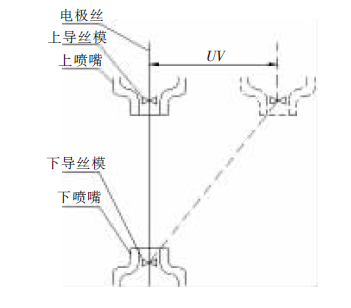
图6 U、V 运动示意图
2.3.2 锥度加工程序及加工设定
本切割实验属于固定锥度加工,上、下表面具有相同的表面形状———圆形,编程较简单。 锥度加工需根据生成的程序进行相关的设定,涉及锥度加工的设定参数主要包括主程序面(编程平面,也是精度尺寸在工件上的位置) 到工作台面的距离TP、从程序面(工件上另一个有尺寸要求的面)到工作台面的距离TN 及角度的方向。这3 个参数需正确设定,否则会影响拉丝模具的尺寸、角度所在的位置和角度精度。
2.3.3 喷嘴的干涉检查
在进行角度切割时,需事先通过加工预演来确定喷嘴与电极丝是否发生干涉。如发生干涉,会造成与实际要求的加工角度不符,可更换规格大的喷嘴或将喷嘴取下。但取下喷嘴会使喷流起不到相应的作用,排屑不通畅会造成断丝。
2.3.4 锥度加工技巧
在切割压缩区和安全角时,均带有不同大小的锥度,由于高压冲液不能有效地冲入切缝,电蚀产物不能有效排出,易造成断丝。且带有锥度区域的切割速度与无锥度区域的切割速度相比要低得多,锥度越大,切割速度越低。适当减小脉冲宽度,降低脉冲能量,可避免发生断丝。此外,应尽可能保证上、下喷嘴贴近工件表面,改善喷液状态,并检查上、下喷嘴,确保其完好无损。锥度加工前,需使用找正器找正电极丝的垂直度(0.01 mm),如果电极丝垂直度误差较大,将导致超大孔径PCD 拉丝模具的角度区域在各个方向的锥度不一致,降低角度的精度[5-6]。
3. 结论
(1)随着脉冲宽度的增加,切割速度呈非线性增加,一般选择脉冲宽度3~4 μs 区间时,可获得良好的表面质量及合理的加工速度。脉冲间隔对切割速度影响较大,为确保加工的稳定性,应选取较大的脉冲间隔,一般35~40 μs 为宜。随着峰值电流的增加,切割速度增加,但表面粗糙度变差,也应在一定范围内合理选取, 避免电流太大而烧伤工件、太小则无法切割PCD 材料,因此选15 A 左右为宜。适当增加伺服参考电压,以增加电极和工件之间的放电间隙,使加工稳定。伺服进给速度不能超过加工速度,否则易造成断丝,欠进给状态较合适。其他非电参数的选取均以加工稳定、防止断丝为主要前提条件,因为切割超大孔径PCD 拉丝模具时不允许断丝,断丝处留下的凹槽和凸棱会给后续的研磨加工增加相当大的工作量,浪费时间和成本。
(2)采用单向走丝电火花线切割进行超大孔径PCD 拉丝模具的定径区、压缩区和安全角的粗加工,达到了预期要求,实现了更好的工艺效果,提高粗加工效率近3 倍。一次装夹,各个区域尺寸的同轴度得到了保证。尺寸余量更小,减少了原工序复杂的整形工序,降低了废品率。切割后的内芯可制作小孔径拉丝模具的原始坯料, 比EDM 套料尺寸直径大1~2 mm,提高一个组距。
(3)以粒度为25 μm 的超大孔径PCD 拉丝模具为例, 进行单向走丝电火花线切割加工工艺研究,对于不同粒度的PCD 性能有一定的差别,在切割时,工艺参数选择也应区别对待。
投稿箱:
如果您有机床行业、企业相关新闻稿件发表,或进行资讯合作,欢迎联系本网编辑部, 邮箱:skjcsc@vip.sina.com
如果您有机床行业、企业相关新闻稿件发表,或进行资讯合作,欢迎联系本网编辑部, 邮箱:skjcsc@vip.sina.com