DK7732型快走丝电火花线切割机加工工艺的改进
2016-10-28 来源:湖南汽车工程职业学院 作者:谢冬和
摘要:快走丝电火花线切割机加工的凸模,其表面质量和加工精度往往达不到图纸标准要求,需经过抛光及研磨等工序。如果对设备进行适当改造。对切割工艺进行改进,切割的工件就能满足图纸要求,针对在加工中发现的问题,提出了线切割机工艺参数的计算方法。
关键词:快走丝线切割机;工艺改进;计算方法;加工精度
随着模具工业的快速发展,人们对模具产品的表面质量及尺寸精度的要求也越来越高。在快走丝线切割机加工之后,还需对切割件进行抛光及研磨等才能保证模具符合图纸要求,但花费的成本较高,且生产效率也难以满足要求。如果对线切割机进行改造,对使用的线切割工艺进行改进即采用多次切割的工艺方法对模具零件进行加工,这样得到的工件质量及加工精度应能满足图纸要求。多次切割工艺就是第一次切割时采用较大的电参数对工件进行快速切割,快速地切除工件上大部余量,并使工件初步具备图纸要求的外形;第二次切割时使用较小的电参数对工件进行精加工,并留精微余量至第三次切割,保证工件符合图纸要求;第三次切割时使用精规准对工件进行精微加工,以获得较理想的加工表面及加工精度。本文以在快走丝线切割机上加工冷冲凸模为例,讲解如何采用多次切割工艺来提高凸模的加工质量,希望这些方法能对企业的生产具有一定的借签作用。
l. 设备改造
由于使用的是普通快走丝电火花线切割机,其机械构造及配件是按通用标准进行设计和制造的,导致其加工件达不到图纸要求,因此,必须在设备硬件及软件上对其进行升级改造。否则切割的工件质量达不到图纸要求,也不能实施多次切割工艺。
(1)切割中,钼丝因运行速度太快而抖动很严重,钼丝与导电块之间、钼丝与工件之间经常会产生非正常的放电现象而使能量损耗,影响加工的正常进行。
(2)DK7732型快走丝电火花线切割机使用的丝杠为普通丝杠,在进给过程特别是在换向时有误差,导致加工件的精度达不到图纸要求。
(3)加工的次序及要求不同,选择的电参数也不相同,才能保证工件的加工质量及加工精度符合图纸要求,特别在精加工和精微加工阶段,选择的脉宽值不但要求较小,而且变化幅度也不能过大,否则会影响到加工质量及加工精度。
根据对快走丝线切割机加工情况的分析,在对工件使用多次切割工艺之前,应对使用的快走丝线切割机床进行如下改造及调整。
(1)要严格控制机床的刚性、精度和走丝系统的稳定性。刚性差,机床加工的稳定性也差,故在加工前需对机床的传动部件进行改进和调整。采用带预紧力的滚珠丝杠副,此种丝杠副所需的转矩较小,传动时平稳,没有爬行现象,并且此丝杠带有一定的预紧力,消除了丝杠反向转动时的间隙。
(2)储丝筒带动钼丝作正反向高速运转,钼丝在运行中抖动,会造成切割过程的不稳定,而上、下喷水嘴间的钼丝抖动是造成切割不稳定的主要因素,如果将两导轮间的钼丝抖动控制在允许范围内,其切割性能能得到较好的改善。分析发现,喷水嘴(如图1所示)的水口直径达到了13 mm,钼丝的活动范围较大,如果将该喷水嘴的内孑L直径改为0.195 mm的“眼模”陶瓷导丝嘴(如图2所示),这样可以将钼丝的抖动控制在极小范围内,还可消除多次切割中钼丝的定位误差,提高定位精度。但这种陶瓷导丝嘴在安装时要注意保证上、下丝嘴的同轴度,要用校丝器进行严格的校核及调整。
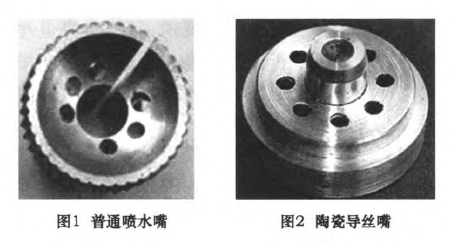
(3)钼丝在高速运行中的抖动还会使钼丝与导电块之间产生非正常放电,这种非正常放电会降低施加在钼丝与工件间的放电能量,从而减缓切割速度。因此,必须对钼丝的受电方式进行改进。从线切割机的加工原理得知,电流通过导电块一钼丝_前端导轮,可以看出,负极线的传输距离较远,传递过程中的能量损耗较大,如果钼丝一旦抖动,在钼丝与导电块之间就会产生细小间隙,进而会产生非正常放电。如果将负极线前移至与导丝轮座相连,导电块只起支承作用,这样可以缩短电流的传输距离及减少传输中的能量损耗,杜绝钼丝与导电块间的非正常放电,改进后的负极受电方式如图3所示。
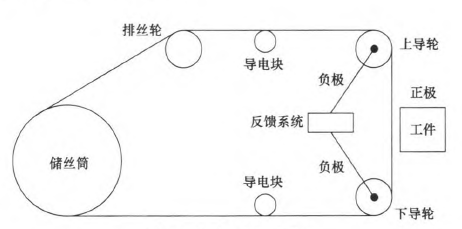
图3负极受电方式改进图
2.加过程及参数计算
在改造过的DK7732型快走丝电火花线切割机上用直径为加.18 mm的钼丝加工如图4所示的凸模工件,工件材料为Crl2,厚度为50 mm。如果采用多次即分3次对工件进行加工,其切割路线如图5所示。第一次沿着1—也_3—巧—汀—固_10一l 1的切割路线,第二次没着11—10—汐q硝q越_÷1的切割路线,第三次沿着1—2_+3—5_7_9_÷10—11的切割路线进行切割。
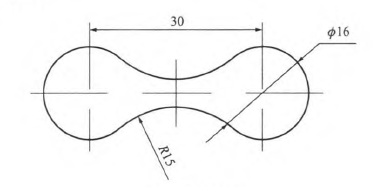
图4凸模工件
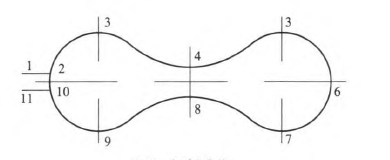
图5切割路线
由于所切割的凸模工件属于内切割,为了在线切割机上实现3次切割,必须保留一段支撑段(图中2_10),可以在切割后的切缝中塞入薄铜片,卡住凸模件不致于往下掉,然后再按同样的加工工艺对2—10段分别进行3次切割,以保证凸模的加工质量。
2.1 第一次切割时的工艺参数
由于第一次切割的主要目的是稳定快速切割,尽可能快地切除工件上的余量,并使工件初步具备图纸的形状,其参数的选用要求如下。
(1)脉冲参数。为了尽快将余量快速切除,应选用较大能量的脉冲电参数,并且要求在加工中逐步增大电流数值,控制电流的上升率不要过大,以获得更好的切割效果,因此脉冲电流的峰值选择在32 A,加工电流控制在3.2 A,脉宽选为42¨s,加工后的表面粗糙度可达3.2¨m。
(2)切割中钼丝补偿量门拘计算。切割中钼丝补偿量的计算公式为

式中∥为补偿量,mm;8为第一次切割时的平均放电间隙,mm;d为电极丝直径,mm;△为第二次切割预留的加工余量,mm;s为精修余量,mm。在采用大能量电脉冲参数(脉冲电流的峰值较大)进行加工的情况下,钼丝与工件间的放电间隙6约为0.ol一0.02 mm,而留下精修余量s甚微,而加工余量△取决于工件加工后的表面粗糙度值的要求,表面粗糙度值越小,留下的加工余量就越小。本案加工时,按第一次加工控制表面粗糙度值约为R。=3.2斗m,取加工余量△=0.05 mm,这样补偿量.厂约为0.16 mm。
(3)走丝方式。利用储丝筒带动钼丝作往复运动,钼丝的运行速度通过变频控制器控制在10 m/s左右。太快,钼丝的抖动严重,切割稳定性差;过慢,切割效率较低,达不到快速切割的目的。
2.2第二次切割时的工艺参数
第二次切割的主要目的是修光第一次的加工面并确保其尺寸精度,因此,其工艺参数的选择应有所不同。
(1)脉冲参数。要达到修光的目的,必须采用较小的电脉冲能量,而降低脉冲能量的主要方法是减小脉宽,但脉宽选得太小,会影响线切割机的加工速度,在兼顾加工质量及切割速度的情况下,将脉宽选择为16斗s,脉冲电流的峰值为22 A,加工电流控制在1.2A,加工后的表面粗糙度可达1.6 Ixm。
(2)切割中钼丝补偿量^由于第二次切割的目的是精加工,此时的放电间隙比第一次的更小,应控制在0.006~0.008 mm,留给第三次加工的余量更小,仅有几个微米。因此,第二次切割时的钼丝补偿量/约为0.11 mm(钼丝半径0.09 mm+电极丝补偿量0.008 mm+预留量0.0l mm)。
(3)走丝方式。由于是以降低走丝速度的方式来实现修光的目的,但钼丝仍会在工件的加工面上留下一道道的切割条纹,因此可采用短行程切割的方法,将丝速速度控制在一定范围内,这样可在第二次切割后基本消除第一次切割留下的条纹,表面粗糙度控制在R。≤1.6 Ixm,走丝速度控制在4 m/s。
2.3第三次切割时的工艺参数
由于第三次切割属于精微加工,是对第二次加工的表面进行精修,保证工件的表面粗糙度值和尺寸精度符合要求,其脉冲电参数的选择要求如下。
(1)脉冲电参数。在兼顾加工速度及加工质量的情况下,选择脉宽4¨s,脉冲电流的峰值为10 A,加工电流控制在0.5 A,加工后的表面粗糙度值可达0.4 LLm。
(2)切割中钼丝的补偿量.厂。因第三次切割属于精微抛光加工,其放电间隙要很小才能保证工件的尺寸精度和加工质量,其放电间隙控制在0.004—0.006mm,钼丝的补偿量.厂为0.095 mm(钼丝半径0.09 mm+电极丝补偿量0.005 mm)。
(3)走丝方式。为了提高运丝平稳性及保证加工面质量,将丝速控制在2.5 m/s左右,并且采用短距离往复运丝来排除钼丝与工件间的电蚀产物。
3. 结语
通过对冷冲凸模的加工发现,只要对快走丝电火花线切割机床进行适当改造,采用改进后的切割工艺来提高其表面质量及加工精度是完全可行的,这种工艺方法可以作为生产企业借签,但在加工过程中特别要注意的是钼丝补偿量的计算,不同的材料其补偿量有所不同。补偿间隙过大,不但会影响工件的尺寸精度及表面粗糙度,而且会给后续的加工带来困难。
投稿箱:
如果您有机床行业、企业相关新闻稿件发表,或进行资讯合作,欢迎联系本网编辑部, 邮箱:skjcsc@vip.sina.com
如果您有机床行业、企业相关新闻稿件发表,或进行资讯合作,欢迎联系本网编辑部, 邮箱:skjcsc@vip.sina.com
更多相关信息