航空发动机主燃机匣智能加工技术有多牛!
2020-2-18 来源:金属加工 作者:赵华卫等
基于自适应控制的发动机主燃机匣加工技术,通过实时监测机床主轴负载变化,并根据负载变化自动调整,实时适应合适的切削参数,使机床保持恒定负载匀速加工,实现主燃机匣的实时监测加工,解决加工效率低和质量不稳定问题。
航空发动机主燃机匣工作条件苛刻,结构复杂、材料加工难度大。受零件材料组织、加工余量和机床冷却等的影响,经常出现刀具破损断裂情况,机床主轴负载剧烈变化,造成零件报废及损害机床。
发动机主燃机匣采用传统方法加工时,由NC程序设定恒定进给量加工,当出现特殊情况(刀具损耗破损、材料组织不均匀余量突变、刀具碰撞零件和冷却系统故障)时,操作人员需手动调整倍率开关调节进给大小,难以准确实时监控,并调整机匣加工过程的进给。传统加工无法将成熟加工经验与科学数据分析相结合,无法实现发动机主燃机匣加工过程的监控及加工参数的实时优化。
发动机主燃机匣加工现引进自适应控制技术。通过控制器硬件与机床NC系统之间的接口连接,实现对机床主轴转速、主轴转矩、进给速度和进给力等切削参数优化控制。可实时动态监控切削参数,并将这些参数存储到数据库中。通过内部智能专家系统监控分析切削过程参数状况,实现单台机床实时监控。内部智能专家系统可实现以下功能:①获取加工中振动、切削力、刀具磨损、材质变化、切削余量突变和冷却系统故障等实际状态信息。②综合分析检测的主轴负载、刀具切削参数。③实时感知预测加工工况。
内部智能专家系统读取库中经验数据和加工信息,分析判断加工状态是否理想,不理想时,动态优化切削参数,优化加工过程。通过调整进给量,将加工过程调节到最优状态,实现加工优化及实时监测,解决燃烧室机匣加工中困扰技术人员的实时监控主轴负载问题。
1.零件结构特点及加工难点
发动机主燃机匣零件结构相当复杂,外形有安装边、加强筋、喷嘴安装座和型槽等特征。机匣材料为GH4169,Ⅱ类锻件,硬度≤277HBW,材料属难加工材料,数控加工难度大,加工中使用整体合金刀具数量非常多。加工过程中出现异常后,需操作人员手动调整、操作人员加工中不能离开设备。当出现刀具磨损断裂、加工余量突变和机床切削液供给不足时,操作人员无法及时发现问题。零件加工周期长,制造成本高,加工时间无法精确统计。操作人员无法解决机床负载变化导致的零件超差及损害机床等问题。发动机主燃机匣零件如图1所示。
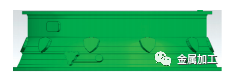
图1燃烧室机匣零件
2.自适应控制加工技术
(1)刀具磨损监测 发动机主燃机匣传统加工方法,一般通过判断刀刃崩裂、零件表面质量、切屑颜色和切削声音等简单方式识别刀具磨损,而在全封闭设备上加工时,无法通过目视观察和声音变化来发现刀具断裂、崩齿和磨损等意外情况的发生。刀具磨损及使用寿命不能有效监控。自适应控制系统能够记录首件加工过程中主轴功率的即时变化,并将其作为后续零件的切削标准。在后续零件的切削过程中一旦出现因刀具磨损造成主轴功率发生较大变化时,控制系统就会自动发出功率异常报警信息,提醒更换刀具,监测刀具磨损。
运用自适应控制技术,加工中可通过主轴过载报警曲线图随时监测刀具磨损状态,如图2所示。图2中纵坐标橙色部分表示刀具磨损时主轴过载随时间变化。蓝色表示刀具切削材料随时间变化。绿色表示切削载荷控制系统启动状态随时间变化。灰色表示主轴旋转状态随时间变化,红色线条表示进给倍率曲线随时间变化,绿色线条表示主轴功率随时间变化。红色三角符号表示警报信息。横坐标表示加工时间。对于任何刀具,当刀具磨损达到“警报”过载极限时,切削载荷控制系统发出警报信息。根据报警信息,系统发出更换刀具、修改切削进给量的指令控制整个切削过程。刀具磨损变化时,无需调整机床倍率及人为干预加工。
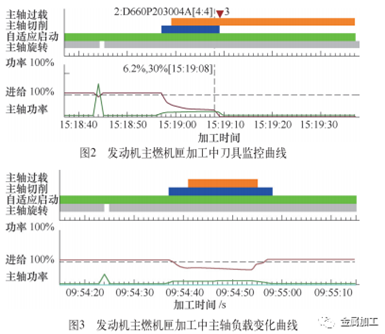
(2)机床主轴负载控制 传统加工方法无法对主轴负载的变化进行直接监控,一般通过主轴声音变化来判断是否正常切削,非正常切削时通过人工调整机床各参数开关控制切削参数,使主轴负载控制在额定范围之内。
自适应控制系统可精确控制整个加工过程中的主轴负载,能根据主轴负载的变化量即时调整切削参数,保证主轴的切削功率维持在一定的范围之内,实现恒速度加工向恒负载加工的转变。加工过程一旦出现刀具破损断裂、刀具切入切出零件、零件材料组织不均匀、零件加工余量突变和机床切削液供冷故障等异常状态时,切削载荷控制系统就会自动将进给速率衰减到合理范围。
图3所示为某发动机主燃机匣加工中的主轴负载变化曲线图,图中纵坐标表示加工时间,横坐标是对主轴过载状态、主轴切削状态、功率及进给随时间变化的描述曲线。随着主轴负载增加,系统自动降低切削速度,当切削速度达到设定的下限值时,系统强行停止设备,并发出报警信息(进给速率小于设定下限,停机,主轴过载保护设置为“立即停止”)。切削载荷控制系统判断主轴负载是否达到主轴承载最大值,当达到最大值时,通过降低进给大小,使切削负荷满足系统中设置的主轴负载安全值。只要主轴负载允许,切削载荷控制系统将进给提高到最大允负荷水平。在保护机床主轴情况下恒负载加工零件。
(3)切削参数优化 传统加工在NC程序中给定了固定的切削参数,设备只能按照给定的参数加工,存在空走刀及进退刀速度慢过程。切削过程不能根据余量大小调整切削参数,造成加工效率低、加工质量不稳定的问题。
自适应控制系统能够将即时切削参数与系统库中理论参数对比,自动补偿NC程序设定的恒定进给,优化切削参数至最合适范围,使整个加工过程的切削参数更加科学优化。使用切削参数优化技术后,燃烧室机匣加工过程更加优化,不仅起到防止刀具碰撞、保护机床的功能,同时也缩短了零件的加工周期。
以φ16R4mm整体硬质合金铣刀切削为例,在应用切削载荷控制系统前毎把刀具只能加工3处喷嘴座,应用后每把刀具可加工5处喷嘴座。刀具寿命明显提升。
传统机匣加工,编程人员根据经验以设备承受最大负载设定加工进给。而实际处于最大载荷时间段只占生产时间很少部分,绝大多数时间机床是处于非饱和加工状态。利用切削参数实时优化技术,使机床加工始终处于饱和状态。在保证设备安全和零件质量前提下,挖据设备利用率。发动机主燃机匣应用切削参数优化前后加工效率提升见表1,表中仅列出部分刀具提升效率。
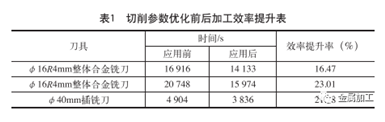
发动机主燃机匣切削参数优化前加工时间为249 727s,优化后所用时间为207 193 s,效率提升率为17.03%。统计时间中不含工件的装夹、找正、对刀、换刀、程序校对和测量等辅助时间,机匣加工时间精确至秒。
3.结语
通过研究,得出以下结论:
(1)实现对主轴负载实时监测 当加工中刀具损耗或破损、材质不均匀、材料硬点、余量突变、刀具碰撞零件和冷却系统故障时,通过优化进给避免了切削冲击主轴,实现了恒速度加工向恒负载加工的转变。
(2)实现刀具磨损监测,保护刀具 解决困扰技术人员的刀具实时监问题,机床在无人监控情况下,可自动采取科学合理的参数、实时适应主轴负荷和切削工况加工零件。
(3)实现零件加工过程实时监控优化,提高了加工效率17% 单台设备零件加工时间精确可控,无人为干顶。整体生产进度可以科学精确规划。并保持最优零件加工状态。
投稿箱:
如果您有机床行业、企业相关新闻稿件发表,或进行资讯合作,欢迎联系本网编辑部, 邮箱:skjcsc@vip.sina.com
如果您有机床行业、企业相关新闻稿件发表,或进行资讯合作,欢迎联系本网编辑部, 邮箱:skjcsc@vip.sina.com
更多相关信息