精密离心机主轴回转误差测量仿真技术研究
2017-1-10 来源:中国工程物理研究院总体工程研究所 作者:张 荣,牛宝良,凌明祥,王 珏,周继昆
摘要:精密离心机主轴回转误差直接影响精密离心机动态半径的测量、离心加速度输出精度以及精密离心机主轴运行安全性,必须精确测量主轴回转误差参数;介绍一种应用3 个电容测微仪测试并分离主轴回转误差与圆度误差的方法,利用MATLAB 对三只电容测微仪安装角度误差、主轴全周采样点数、测试系统本底噪声对主轴回转误差测试结果影响进行仿真分析,得出采样点数N、测微仪安装角度误差δα、δβ 以及测试系统本底噪声对回转误差分离的影响,基于仿真结果确定了1 0 -6 量级精密离心机主轴回转误差测量的几个工程参数。该方法已应用于某高精度精密离心机主轴回转误差精密测试中,实测表明,转速在300 rpm 内精密离心机纯回转误差测量结果为0.2 5 μm,满足1 0 -6 量级高精度精密离心机的研制指标需求。
关键词:精密离心机;回转误差;圆度误差;三点法;电容测微仪
0.引言
精密离心机空气主轴径向回转误差是影响高精度精密离心机性能的重要因素,主要表现在:1 ) 在利用外基准测量精密离心机动态半径时,主轴径向回转误差将混入动态半径测量值中,回转误差量级较大时,其对动态半径的影响不可忽略,必须对动态半径进行补偿,否则经离心加速度补偿模型[1 ]输出的加速度信号精度无法得到保证;2 ) 主轴径向回转误差直接关系到主轴运行安全,对于空气静浮主轴,气膜厚度通常仅几微米,为保证离心机在各G 值下安全运行,必须对主轴的回转运动误差进行监视,设定主轴回转运动误差限,当主轴回转运动误差接近超限值时,离心机必须停机。因此,为满足高精度精密离心机研制技术指标,对其主轴的回转运动参数必须进行精确测量。针对某1 0 -6 量级精密离心机研制,精密离心机主轴回转误差的精度指标为≤0.5 μm,为完成该参数的高精度测试,笔者提出采用电容测微仪和三点法进行测试,并设计精密测试系统完成了1 0 -6 量级精密离心机主轴回转误差的测试,实测主轴纯回转误差为0.2 5 μm。
1精密离心机主轴回转误差测试方法研究
目前,对于1 0 -5 及以下量级精密离心机研制, 由于量级低,主轴回转误差的量值大小对精密离心机输出加速度精度影响不明显,而主轴运行安全性监测是主要的,常采用在主轴截面上安装两只[2 3 ]正交的电容传感器测量主轴转动一周测微仪输出最大值与最小值,这种测量无法测试出纯主轴回转误差运动极值。对于1 0 -6 及以上量级的精密离心机研制,必须考虑主轴安全性以及主轴运动误差对动态半径的贡献,采用双测微仪法测试无法满足测试要求,必须采用新的测试手段。
1.1主轴回转误差测试的难点
主轴回转误差测试难点在于通常主轴圆度误差和回转误差同时混杂于测试结果中, 并且圆度误差往往比回转误差大得多,测试纯回转误差较难,解决方法有两种:一种是借助于安装在主轴上的标准球, 采用电容非接触式或电感接触式测试标准球的径向跳动量, 此时忽略标准球圆度误差, 采用正交双测微仪合成李萨如[4 ]图获得主轴回转误差, 但该法仅适用便于安装标准球的场合, 同时标准球的安装还存在偏心误差,必须在测量结果中进行一次谐波分离去偏心误差; 对不便安装标准球的测试, 如本项目中的精密离心机主轴, 采用在主轴外沿安装测微仪测试, 测试结果包括了主轴回转差和圆度误差两类信号,必须通过测试方法从结果中分离出圆度误差信号,得到真实的回转误差信号, 故信号分离算法是关键。目前基本的圆度误差分离方法有反向法[5 ]、多点法[6 ]、多步法[7 ]等, 多点法分两点法、三点法、四点法等。
表1 [8 ]是几类误差分离方法精度统计, 通常各方法应用在不同的测试场合,但对于回转误差的总体分离精度均可控制在1 0 %以内,这为本项目中空气主轴的回转误差的测试奠定了基础。从技术实现难易程度、成本等综合考虑选择在项目中应用三点法测试主轴回转误差。
表1 回转误差与圆度误差分离方法及误差表

1.2 三点法主轴回转误差分离测试原理
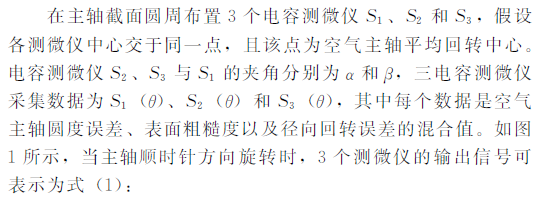
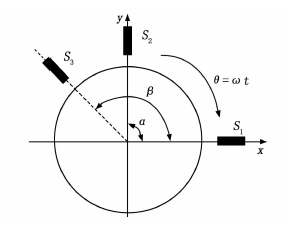
图1 三点法主轴回转误差分离测试示意图
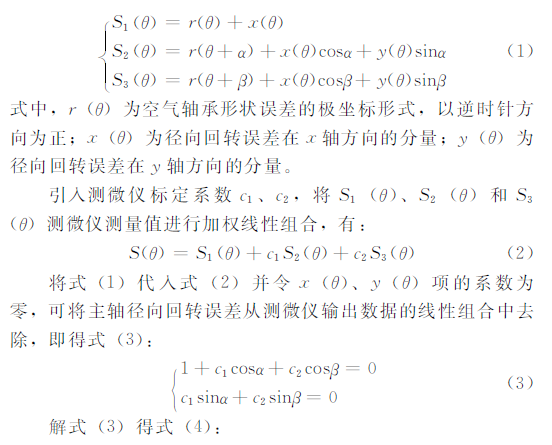
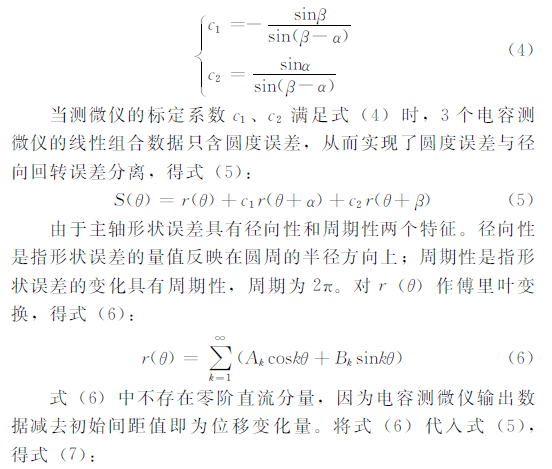
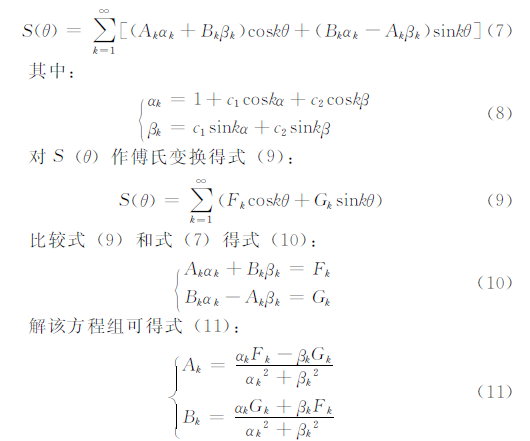
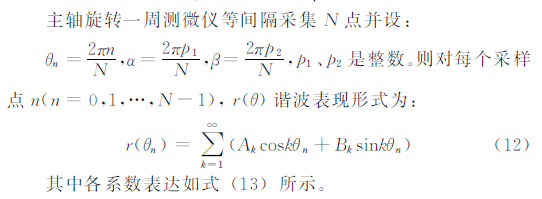
由式(1 3)可知,采样点数N 、测微仪安装角度误差以及谐波分析阶次均会给分离精度带来影响,故须根据谐波分析阶次与分离精度要求确定三测微仪安装角度; 根据ISO 标准,当被测零件圆度误差的谐波次数大于22 ~45 阶后,可将其归结为零件表面粗糙度和波度[9 ],本项目参考ISO 标准, 设定主轴圆度误差谐波上限为45 阶,45 阶以上的谐波成分将作为表面粗糙度与波纹度处理。圆度误差分离完成后,则回转误差也即得到分离。
2.主轴回转误差分离测试影响因素的仿真分析
精密离心机主轴回转误差测试实际设计时,需确定主轴全周采样点数N 、三测微仪安装角度误差以及测试系统本底噪声对回转误差分离结果的影响程度, 为此在MATLAB 下
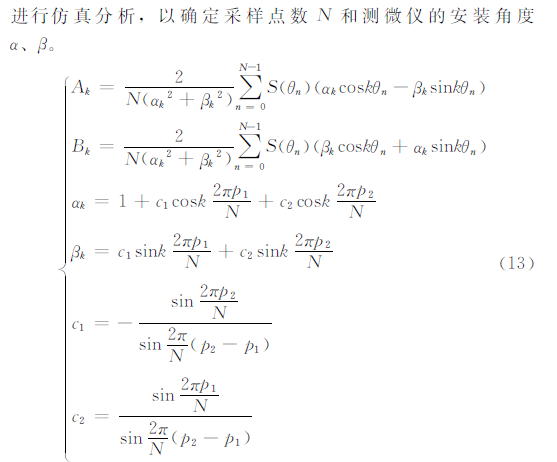
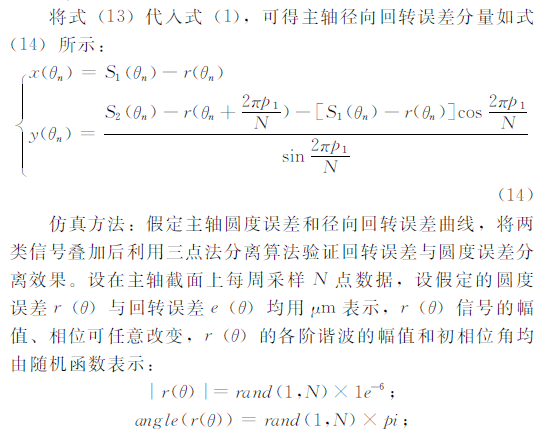
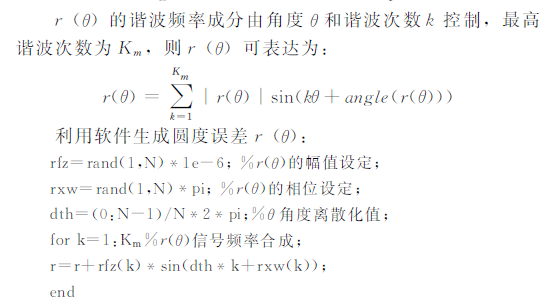
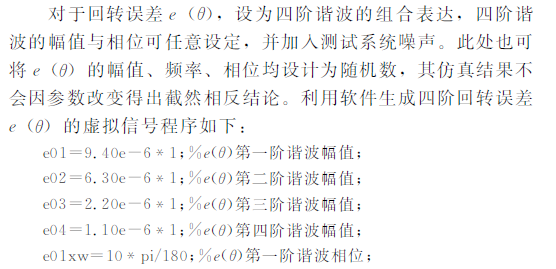
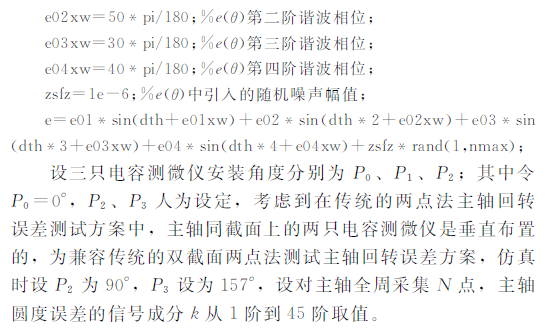
2.1采样点数N 对回转误差测试影响仿真
分别设定N =1 28,N =5 1 2 进行仿真,回转误差与圆度误差的分离结果如图2 ~图5 所示。
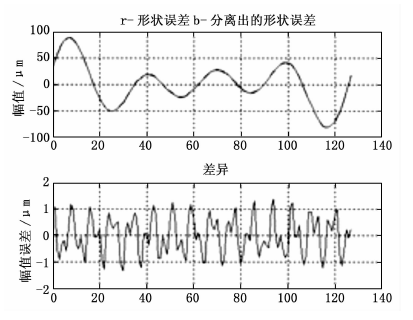
图2 N =1 2 8 时圆度误差设定与分离结果
从仿真结果看,N 值越大,回转误差与圆度误差的分离精度越高,适当选择N 值可使圆度误差分离信号的误差达1 0 -1 3 量级。本项目中N 取1 600 点。
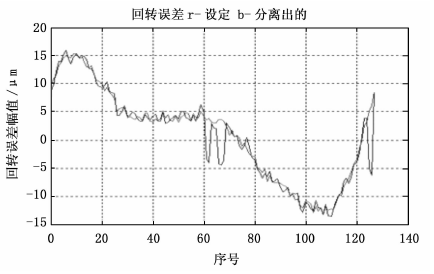
图3 N =1 2 8 时回转误差设定与分离结果
2.2 测微仪安装角度对回转误差测试影响仿真
设三只测微仪理论安装角度分别为0°,α=90°,β=1 5 7°。工程设计时因测微仪装配误差使各安装角度存在误差,以第一只测微仪安装位置为参考,第二只与第三只测微仪相对于第一只测微仪的安装夹角存在偏差δα、δβ, 仿真δα、δβ 对回转误差分离结果的影响。考虑到离心机最高转速为300 rpm 的工程实际,设测微仪安装偏差角δα、δβ 控制在±1°范围内,在输入信号和采样点数N =1 024 不变时,开展如表2 仿真分析,给出代表性的仿真结果如图6 ~图9 所示。
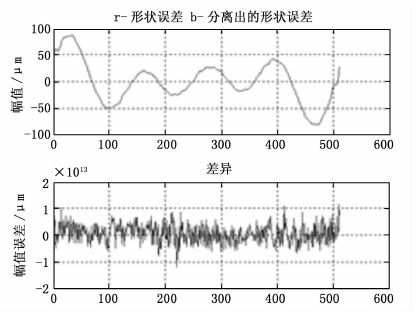
图4 N =5 1 2 时圆度误差设定与分离结果
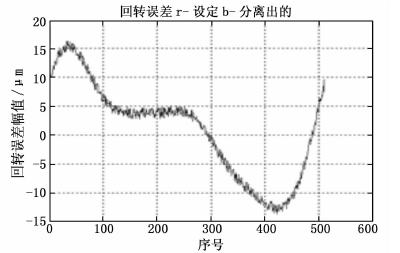
图5 N =5 1 2 时回转误差设定与分离结果
表2 仿真测试测微仪安装角度偏差δα、δβ 表 c°
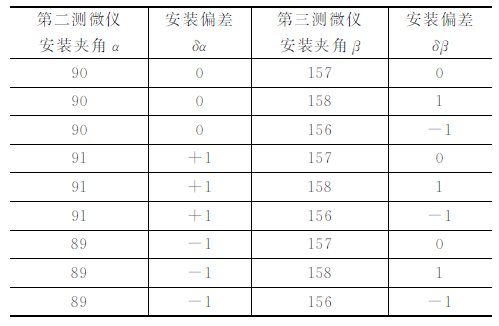
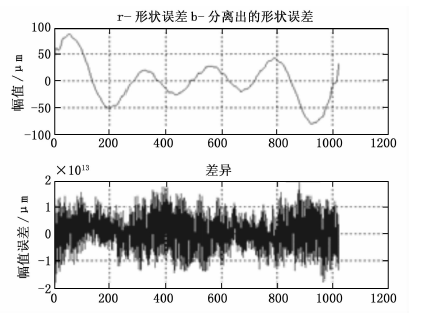
图6 α=90°,β=1 5 8°圆度误差设定与分离结果
仿真表明,在实际安装夹角α、β 偏离理想安装夹角± 1°时,安装夹角的偏差δα、δβ 对主轴圆度误差与径向回转误差
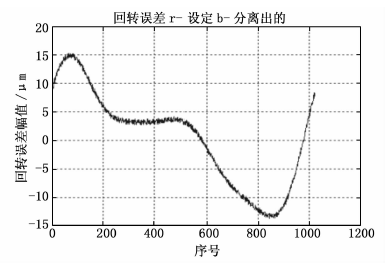
图7 α=90°,β=1 5 8°回转误差设定与分离结果
分离有一定影响,但影响较小,圆度误差分离误差量级通常在1 0 -1 3 以上,可忽略。其中,仅在α=90°、β=1 5 6°时圆度误差的分离误差达到了0.03 μm 左右, 这是由于安装夹角引起的分离过程谐波抑制,多次仿真发现,这种谐波抑制现象引起的分离误差最大均控制在0.05 μm 以下, 这对于本项目的主轴径向回转误差分离影响较小可忽略。因此,在实际测微仪安装
时可适度降低安装精度,允许一定安装角度偏差,并可根据角偏差的不确定度评估出主轴圆度误差和径向回转误差的分离不确定度。
投稿箱:
如果您有机床行业、企业相关新闻稿件发表,或进行资讯合作,欢迎联系本网编辑部, 邮箱:skjcsc@vip.sina.com
如果您有机床行业、企业相关新闻稿件发表,或进行资讯合作,欢迎联系本网编辑部, 邮箱:skjcsc@vip.sina.com
更多相关信息