高精密机床主轴回转误差在线测试系统
2016-12-28 来源:中国工程物理研究院总体工程研究所 作者:周继昆, 张荣, 凌明祥, 张毅
摘要:为实现对高精度机床主轴回转误差的在线实时测量,根据机床机械结构特点,采用标准球及外基准测量方法间接对机床主轴径向位移进行测量,并利用三点法误差分离算法将主轴圆度误差与回转误差分离,得到纯回转误差。依据所提出的测试方法,基于PXI 总线数据采集技术建立测试系统硬件部分,并利用PXI 外部时钟同步采集卡实现主轴径向位移信息的等角度同步采样;在LabVIEW 开发环境下,开发在线测试软件,对回转误差进行在线分离。利用该系统对某机床进行在线测试,测试结果表明,测试系统可以在线将机床主轴纯回转误差从径向位移信息中分离出来,并达到较高的测试准确度。
关键词:精密机床;主轴回转误差;在线测试;三点法;标准球;外基准测量
0.引言
主轴回转误差是衡量机床性能的重要指标,也是影响加工准确度的重要因素[1-2]。主轴回转误差是一个二维平面运动位移量,当测量准确度进入亚微米甚至纳米级时,混入测量数据中的形状误差、表面粗糙度就会凸显出来,甚至会掩盖掉主轴微小的回转误差[3],需采用一定的分离方法才能提取回转误差。
常用回转误差分离方法有反向法[4]、多点法[5]、多步法[6]等;其中,三点法误差分离技术相对成熟,且适用于在线回转误差测试[7-8]。目前已有研究都是以机床主轴转速稳定为测试条件,并未考虑在不同转速或转速控制存在一定偏差的情况下在线测试主轴回转误差[1,3,5]。
本文根据三点法回转误差测量分离理论[9-10],设计了固定位移传感器夹具和测试用标准球;基于PXI 总线技术搭建测试系统,利用PXI 外部时钟同步采集卡实现主轴径向运行信息的等角度同步采样;在LabVIEW 开发环境下,开发测试回转误差在线测试软件,并通过现场测试验证该测试系统的正确性和有效性。
1.测试系统机械结构设计
本文测量对象为一台高精密机床,由于机床在设计时并未考虑为主轴回转误差测量预留相关机械接口;因此,首先应根据机床机械结构设计合适的夹具来安装位移传感器以及标准球。
为在线测得机床主轴回转误差,本文采用“标准球+三点外基准非接触式”测试方法对机床主轴运动时的径向运动信息进行测量。首先在机床主轴上安装标准球,机床为一圆柱体,由位于轴心的机床主轴带动旋转。由于无法直接测量主轴径向运行信息,将圆柱体形标准球固定在主轴上,且其轴心线与主轴延长线重合。
本文采用电容测微仪测量主轴径向运动信息,电容测微仪可达到纳米级准确度的位移测量。基于三点法设计的夹具及电容测微仪安装的位置如图1所示。
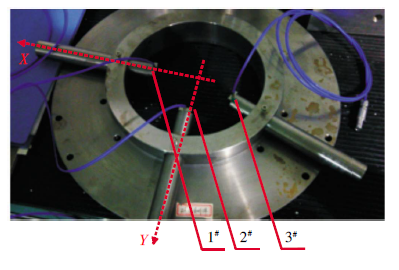
图1 电容测微仪安装效果图
3只电容测微仪按照一定的角度固定在夹具上,且电容测微仪到夹具圆心的位置可调;其中,电容测微仪的量程均为250μm,最小分辨力为0.01μm,绝对误差≤±0.05%。采用外基准测量的方法对主轴径向运动信息进行测量,其中1# 电容测微仪与2# 电容测微仪之间的夹角为90°,1# 电容测微仪与3# 电容测微仪之间的夹角为157°,并按图中虚线箭头所示建立直角坐标系。则3 只电容测微仪输出的位置信息可表示为
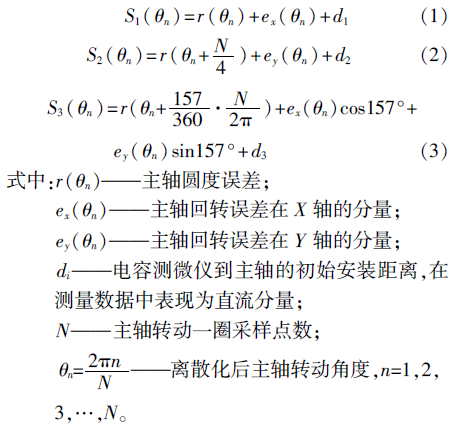
去掉式(1)~式(3)中的直流分量,再利用三点法误差分离算法即可求出主轴回转误差。
2.测试系统软硬件设计
2.1 测试系统硬件设计
由式(1)~式(3)可以看出,为在机床不同转速下在线分离主轴回转误差,必须在主轴转动过程中对主轴径向运动信息进行等角度采样;这样才能保证在不同转速下,每圈对主轴径向运动信息的采样点数一致。为此,本文将机床主轴光栅A 脉冲信号k 次分频后作为数据采集时钟信号,由于光栅A 脉冲频率的高低与主轴转速对应;因此,即使在机床转速存在一定偏差的情况下也可以保证每圈采样的点数相同。同时,利用光栅Z 脉冲作为采样起始触发信号,即可保证每次采样的初相位一致。测试系统硬件结构如图2 所示,将光栅的Z 脉
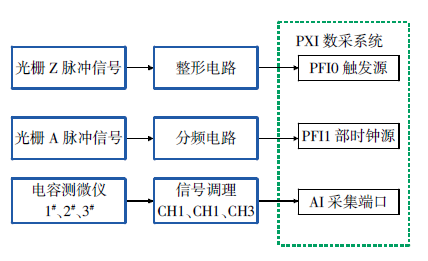
图2 硬件结构图
冲信号通过整形电路变换为建立时间和保持时间均满足触发脉冲要求的信号,送入PXI 多功能同步数采卡的PFI0 外部触发源输入口,作为测试任务的信号采集起点时刻。同时,将光栅的A 相脉冲信号经k 次分频后送入数采卡的PFI1 作为采样时钟,其中分频系数k 由每圈采集的点数确定。3 只电容测微仪的输出信号经调理后送入采集卡AI 端口。
2.2 测试系统软件设计
利用三点法进行主轴回转误差测试的软件设计,主要解决数据采集、预处理、误差分离算法具体实现等问题,主要功能模块与流程设计如图3 所示。
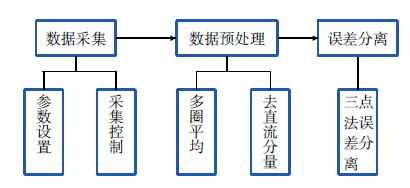
图3 软件功能模块与数据流
图中,参数设置主要包括每圈采样点数N、采样圈数M、采样模式等。采集控制主要包括数据采集任务与计数器计数任务的同步控制、数据采集与数据存储的线程运行控制,确保测试时系统稳定不丢失采样点。数据缓存是在程序中开辟动态内存,并通过多线程的合理设计,将多帧数据按时序缓存,为后续数据分析奠定基础。
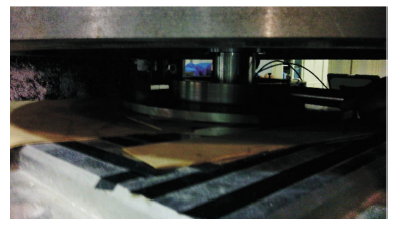
图4 安装后的夹具
在主轴回转误差的动态测试过程中,测试数据主要包括测试系统硬件本身引入的随机误差和主轴的表面粗糙度引起的误差,这两种误差虽然很小,但却会影响最终系统的测试准确度,不能忽视。对此,采用多圈数据平均消除随机误差,然后去掉信号中的直流分量即可得到主轴径向运动信息。最后利用三点法误差分离算法计算回转误差。所有模块都在LabVIEW 环境下编程实现。
3.实验结果分析
将图1 所示夹具套在标准球外,如图4 所示,然后调节电容测微仪到标准球的初始距离(一般在电容测微仪量程的50%左右),安装完成后即可对机床主轴回转误差进行在线测试。
分别在30r/min 和60r/min 的转速下,对机床的回转误差进行在线测试。设每只电容测微仪每圈采
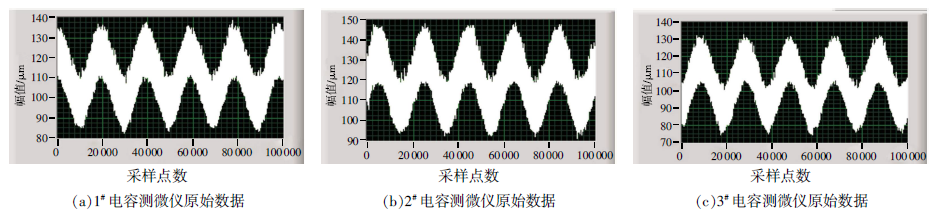
图5 主轴原始回转曲线
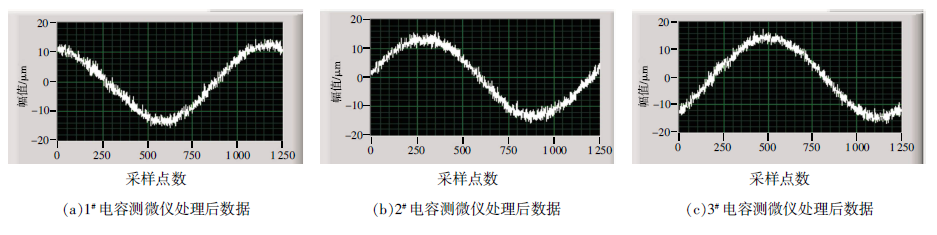
图6 原始曲线经处理后数据
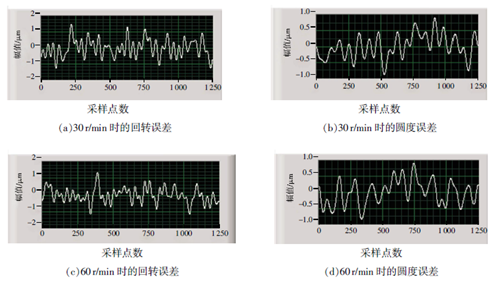
图7 分离后的回转误差与圆度误差
集的点数为1250、每次测量时采集5 圈主轴回转数据, 在30r/min 转速下电容测微仪所测主轴原始径向运动信息如图5 所示。从图中可以看出,原始信号中包含由于安装偏心差带来的一阶谐波和随机噪声
带来的高次谐波,采用多圈点对点平均的方法可以有效消除随机噪声的干扰[10]。实际每圈采样点数为20 000 个,这是由现场电池干扰造成的;为了得到每圈1250 个点的主轴运动信息,在原始数据中每隔7 个点提取一个有效数据点,然后对5 圈数据点对点平均,再除去数据中的直流分量后得到如图6所示的波形。
从图可以看出,经过处理后的数据较为平滑,其一阶谐波分量较大,为安装标准球时的偏心差。根据文献[1],主轴的回转误差和圆度误差主要集中在主轴运动信息的2~50 次谐波;因此,进行三点法误差分离前,先利用傅里叶变换方法将一次谐波和50 次以上谐波滤除,再利用三点法误差分离算法[9-10]分离后的圆度误差和回转误差如图7 所示。由图可知,该机床的回转误差在±1.5 μm 以内,标准球圆度误差在±1μm以内,不同转速下得到的结果基本一致,且测试结果与机床指标相符。
4.结束语
本文针对机床主轴回转误差的高准确度在线测试问题,设计了测量所需的标准球和夹具,基于LabVIEW和PXI 总线搭建了测试系统,设计了系统的软硬件。通过现场测试,本文设计的回转误差测试系统达到了在线亚微米级测试,测试数据准确可靠。
投稿箱:
如果您有机床行业、企业相关新闻稿件发表,或进行资讯合作,欢迎联系本网编辑部, 邮箱:skjcsc@vip.sina.com
如果您有机床行业、企业相关新闻稿件发表,或进行资讯合作,欢迎联系本网编辑部, 邮箱:skjcsc@vip.sina.com
更多相关信息