基于分级特征库的机床故障诊断系统设计与实现
2016-10-20 来源:渤海大学 东北大学 中国科学院 作者:苏宪利 郑一麟
摘要:针对机床故障诊断中人工诊断效率低、实时性差、误差大的缺点,研究提出使用分级特征库进行机床故障诊断,该研究将特征分为典型特征和非典型特征两级,在底层汇聚节点完成振动特征提取和典型特征(即A 级特征)机床故障诊断,实现故障现场预警,提高了现场预警的实时性。在控制中心完成对非典型特征(即B 级特征) 综合处理和分析,同时对两级特征数据采用机器学习中SVM算法完成故障特征库的完善和更新,提高了机床故障诊断的准确性。通过实验证明该研究在基于特征库的机床故障诊断领域具有理论研究价值和工程应用价值,提高了数控机床故障诊断的实时性和精确性。
关键词:分级特征;实时预警;故障诊断
0.引言
数控机床是一种自动化程度较高的机械加工设备[1] ,机床故障对机床的使用寿命和产品的加工质量都存在较大影响[2] ,机床故障不能及时得到处理将会导致机床损坏或加工产品的报废,在机床部件发生问题时,将对机床运行产生一定的物理冲击,因此机床运行中的故障主要是通过振动的方式体现出来[3] ,而在机床工作现场的诊断也主要是通过工人对振动的感受进行判断,人工判断的方式存在以下问题:
(1)工人的工作经验是执行判断主要因素,对于机床故障的判断跟工作经验成正比,而这种经验的积累是以机床的伤害为代价。
(2)个人感受中环境因素影响较大,容易造成故障判断的错误或缓慢,导致故障不能及时发现和处理,从而造成产品加工产生次品或机床损坏。
(3)缺少快速的学习机制,影响个人经验增长的因素较多,人工对故障识别和判断的学习过程存在效率较差、速度较慢等缺点。尤其是对新型数控机床,需要大量的时间来进行故障现象的识别和训练。
在故障识别领域目前采用的方法包括模式判别方法和智能故障识别方法,其中模式判别方法包括聚类分析、贝叶斯推断等传统的分类器[4-5] ,智能故障模式识别包括神经网络、支持向量机和模糊理论[4-5] ,其中人工神经网络已在故障诊断领域得到了广泛的应用[4] 。当前研究较多的是神经网络与其它方法结合的模型,包括聚模糊神经网络等[4] 。支持向量机理论通过优化一个泛化误差界限自动生产最优的分类面[6] ,使其具有了更优的泛化性能。
目前研究中故障诊断工作全部在服务器端完成,这种方式的优点是数据运算准确可靠,故障的识别率较高。本研究是为了提高故障诊断的实时性,将故障诊断工作分为两级完成,第一级工作为A 类特征的识别和诊断,将故障特征库中的特征明显、识别可靠性高的特征称为A 类特征,其中A 类特征故障诊断在汇聚节点完成,使得A 类特征的诊断和预警时间缩短,提高A 类特征故障诊断的实时性。第二级工作包括B类特征识别和诊断、特征数据库的更新和完善,该工作在故障诊断服务器端完成,利用服务器端的强大计算资源提高识别的可靠性和准确性。
1.系统总体结构设计
本研究中的故障诊断系统包括了三个部分,振动采集节点、汇聚节点和控制中心(服务器端)三部分,其中振动采集节点和汇聚节点部署在车间、控制中心部署在企业的信息中心,控制中心是故障诊断系统服务器端软件运行的服务器设备。
振动采集节点部署在机床特定位置,完成机床振动数据的采集。汇聚节点部署在生产车间内,完成振动数据特征的提取、诊断、实时预警和数据通信。控制中心完成对故障特征数据的深入处理和故障的精确分析诊断,并通过机器学习的方式完成特征库的完善和更新工作。其中振动采集节点与汇聚节点间是通过无线网络进行通信,汇聚节点和控制中心通过以太网进行通信。
机床故障诊断系统结构如图1 所示。
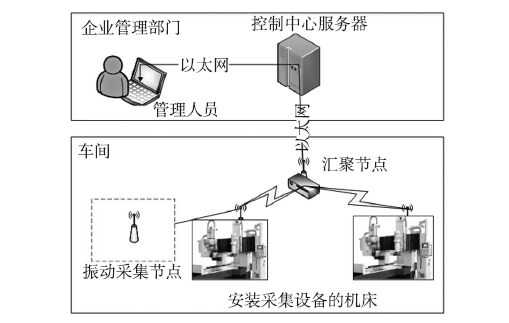
图1 机床故障诊断系统结构
2.分级特征库诊断方法
在传统的研究中,故障特征数据的对比和处理工作全部在控制中心完成,也就是在服务器端完成,在控制中心完成诊断后,将显示预警信息给管理人员或底层预警设备,进行预警和故障处理。这种方式的优势是故障诊断较为准确,它存在的问题是故障诊断缺少实时性,由于所有的故障诊断都经历采集节点、汇聚节点、控制中心诊断后再回传给汇聚节点进行预警,网络通信时间较长,降低了预警的实时性。
为了提高故障诊断的实时性,本系统中设计了分级诊断方法,诊断方法流程如图2 所示。在图2 中诊断方法分为三个步骤:
第一步:特征分类,将特征分类为A,B 两类,A 类故障特征(典型特征)是指只要出现该类特征就一定发生了特定的故障,B 类特征是非典型特征,这类特征需要对振动特征数据进行详细分析处理后才能确定故
障是否发生和产生的原因。
第二步:故障诊断任务分级,汇聚节点完成第一级诊断,实现A 类特征的现场实时预警。控制中心完成第二级诊断。控制中心对汇聚节点上传的振动能量特征进行详细处理,针对B 类特征进行诊断和预警控制输出。
第三步,特征库更新与同步,控制中心通过机器学习svm 方法进行分类描述,通过样本学习实现对特征库的更新和校准,在服务器端对A 类特征库更新后,控制中心发送A 类特征库给汇聚节点,完成汇聚节点A 类特征库的更新和同步。
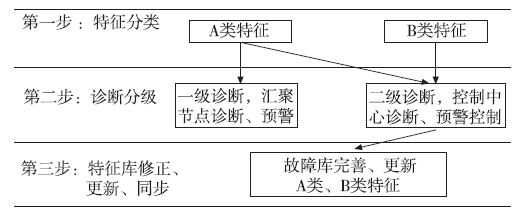
图2 诊断方法流程
一级诊断流程如图3 所示。
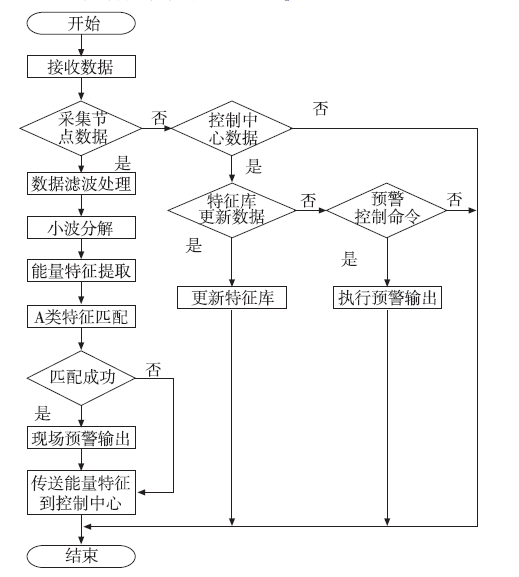
图3 一级诊断流程
在图3 中汇聚节点完成一级诊断工作,汇聚节点为了实现对振动特征的提取,需要对振动信号进行处理,目前采用的方法主要是快速傅里叶变换[3-4] ,该方法的特点是实现简单,可以很快的实现时域到频域的变换,但是FFT 存在缺少时间特征的问题,在FFT 中某一个点的噪声将对整个变换产生影响[3-5] ,因此不适用于对时间和频率同时存在要求的应用。在本系统中为了发现故障的实时特征,采用了小波分解树的方法进行振动信号的处理[6-7] 。小波分解树可以很好的完成信号处理工作,小波分解树工作流程如图4 所示。

图4 小波分解树
在本研究中采用了Mallat 分解算法,该算法的核心思想是通过一对互补的滤波器H 和G,将j +1 尺度下离散序列
分解为j 尺度下的近似系数数列
与细节系数数列
,该算法只对信息号的系数序列进行处理,并不涉及到对小波形式的处理[4-6] 。该算法的实现复杂度较低,适用于实时应用的分析,在本系统中将Mallat 分解算法应用于小波分解树,通过迭代的方法实现对信号的分解,在本系统中为了提高信号处理的实时性,采用了一层分解的方法,通过将信号分为高频和低频两部分,对高低频能量特征进行提取,形成能量特征,通过A 类特征库匹配进行故障诊断,发现故障立即实施现场预警,并将预警数据和特征数据传送给控制中心。二级诊断工作流程如图5 所示。



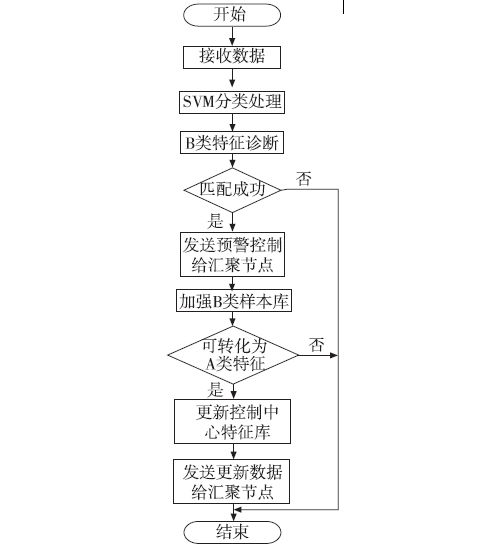
图5 二级诊断工作流程
二级诊断在控制中心完成,如图5 所示控制中心接收到特征数据后,对数据采用svm 算法进行分类和样本学习,根据分类结果对B 类特征进行相似度匹配,诊断出故障后,向汇聚节点发送预警控制,并对B类特征样本库进行强化,当特征库中B 类特征满足A类特征要求时,将该特征转化为A 类特征,并对特征库进行更新,发送新的A 类特征库给汇聚节点,完成特征库的更新和同步。
3.振动数据采集过程
在振动采集中主要采用了振幅、频率和相位三个量值进行描述,其中振幅和频率主要用于机械故障的识别,本系统采用了对振动频率进行采集和处理,实现对机床故障的诊断。
振动数据采集工作是通过采集节点中的三轴加速度传感器实现,在振动特性中振动加速度与振动频率的平方成正比,通过对振动加速度值的运算可以得出振动频率的值。采集节点将采集到的加速度数值传送给汇聚节点,由汇聚节点进行振动特征数据的分析和处理。采集节点工作流程如图6 所示。
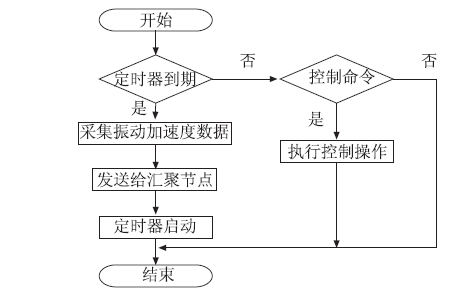
图6 采集节点工作流程
控制中心通过发送控制命令调整采集节点的采集频率和通信方式,采集节点接收汇聚节点转发的控制命令,根据命令执行操作,完成参数调整等工作。
4.控制中心软件实现
控制中心软件系统采用了c#进行开发,采用了C/S 模式,数据库服务器采用了oracle 数据库管理系统[7-8] ,在本系统中设计了三道线程,第一道线程为通信管理线程,该线程完成与汇聚节点的通信工作,完成对特征数据的采集工作。第二道线程为数据处理线程,本线程中采用了SVM 分类方法进行机器学习,对特征数据进行完善。第三道线程为显示线程,完成对操作窗口的输出控制。
在控制中心对特征数据进行分类过程中并不是所有的能量特征都是非常有用的,在本系统中采用了SVM分类方法,对最优特征进行提取,在SVM 算法中为了降低分类器构造的复杂度,本系统中采用了基于决策树的SVM 分类算法,对所有特征进行两类划分,即典型特征A 级特征和非典型特征B 级特征,然后根据特征特点依次进行两类划分,通过这种方法在分类识别过程中提高特征的识别度,加快了特征识别的速度。
控制中心工作过程如下:
(1)接收特征数据,进行数据校验,去除非法数据。
(2)根据特征分类进行样本识别,形成多级树。
(3)根据样本特征进行优化,形成更加精确的特征库。
(4)校准特征类别参数,执行(2)过程。
在本系统中为了保证数据通信的可靠性采用了TCP 的连接方式,每一个汇聚节点通过tcp 完成与控制中心的连接,由于本研究中汇聚节点数量为10 个,每个汇聚节点采集数据量较大,tcp 工作方式可以保证数据传输稳定性和可靠性。
本系统在结构上完全采用了mvc 的软件编程模式,设计了模型层、视图层和控制层,其中模型层完成数据处理和数据库的访问工作,视图层完成软件界面输出工作,控制层完成功能调用工作。控制中心系统软件运行界面如图7 所示。
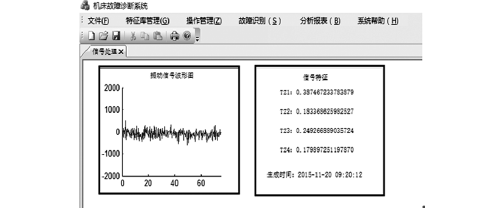
图7 诊断系统运行图
5.实际应用
在本系统应用中采用了根据诊断需求在机床特定位置固定振动采集节点完成振动数据的采集,本系统的测试环境为沈阳机床厂生产的Z3050X16 摇臂钻床,系统采集节点工作位置如图8 所示。
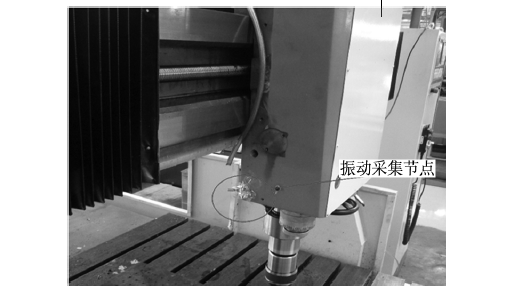
图8 系统测试环境
系统测试条件如下:
(1)每台钻床安装1 个振动采集节点,每5 台钻床使用两个汇聚节点。
(2)汇聚节点通过以太网与企业控制中心连接。
(3)汇聚节点使用大功率声光输出装置。
(4)系统测试时间为45 天,每天工作12 小时。
为了对本系统的运行效果进行分析,测试中采用了两种工作方法,第一种方法为原始的工作模式,所有的故障诊断工作均在控制中心完成,汇聚节点仅完成特征数据处理和转发功能。第二种方法为本研究中提出的方法,在汇聚节点完成一级诊断,在控制中心完成二级诊断。测试中通过在机床上部署一个振动采集节点,在车间部署了两个汇聚节点(一个汇聚节点为原始工作方式,另一个汇聚节点为一级诊断工作方式),一个采集节点同时为两个汇聚节点提供数据。经过45 天的连续工作,对故障时延数据进行汇总和分析,两种方法的预警时延对比如图9 所示。
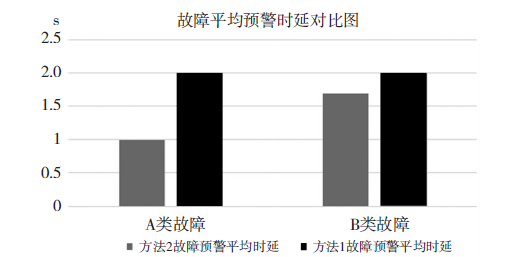
图9 故障预警平均时延对比
方法1 即原始工作方法中故障平均预警时延为2 秒钟,方法2 即本文提出的方法中,A 类故障预警平均时延为1 秒钟,B 类故障平均预警时延为1.7 秒钟。对于A 类故障时延缩短了50%,B 类故障时延缩短了15%,本测试中初始的A、B 类特征比例为1:1,随着系统的运行,特征库中的A 类特征比例将远大于B 类特征,系统的平均故障预警时延将接近于1 秒,实验证明了本系统对提高故障诊断的实时性具有明显的提升效果。
6.结论
本系统设计了基于分级特征库的机床故障诊断系统,实现在汇聚节点对典型故障特征的快速识别和现场实时预警,实现控制中心对非典型故障和典型故障预警和分析,采用机器学习的方法实现对特征数据库的完善和更新,提高了数控机床故障诊断的实时性和可靠性。通过在机床集团的应用,证实了本系统提高了机床故障预警的实时性和诊断的准确型,因此本系统的研究具有理论研究价值和工程应用价值。
投稿箱:
如果您有机床行业、企业相关新闻稿件发表,或进行资讯合作,欢迎联系本网编辑部, 邮箱:skjcsc@vip.sina.com
如果您有机床行业、企业相关新闻稿件发表,或进行资讯合作,欢迎联系本网编辑部, 邮箱:skjcsc@vip.sina.com
更多相关信息