数控机床在线检测系统的开发与应用
2019-10-14 来源:甘肃机电职业学院 甘肃农业大学技术处 作者:毛文亮 杨小平
摘 要:以 Unigraphics NX 10.0 软件为开发平台,应用 UG/Open GRIP 和 UG/Open Menu Script 二次开发工具,对 MATLAB 2016 和 VERICUT 8.0 软件在 Unigraphics 平台下进行了集成,开发了数控机床在线检测系统。 为验证这一系统的有效性,对在线检测数据与三坐标测量机检测数据进行了对比,结果显示,两者最大误差仅为 0.05 mm。 数控机床在线检测系统的开发,为精密复杂零件的高效数控加工与表面质量信息的获取提供了技术支持。
关键词:机床 在线检测 软件 应用
随着现代制造业智能化、数字化、网络化的发展,精密复杂零件“设计-加工-测量-补偿加工”一体化制造成为了趋势。近年来,国内外学者对此进行了深入研究。 Mou 等[1]开发了一种基于计算机辅助设计 CAD/CAM/CAI 的在机检测系统。 Kramer 等[2]对基于零件表面特征的检测系统进行了研究。 Yoon 等[3]对基于 PC-NC (Personal Computer based Numerical Control) 的 在机检测系统进行了研究。 Kim 等[4]研发了一款将检测路径用 G 代码格式传送给数控机床的在机检测系统。孙志海[5]介绍了基于 CAD 的加工中心在线检测系统的设计。 辛娜[6]研究了加工中心在线检测编程技术。 陈欢等[7]开发了基本体在线检测宏程序。陈明娟[8]研究了基本体在线检测路径。总之,国外的在线检测系统技术相对成熟,价格非常昂贵。国内的在线检测系统检测功能相对比较单一, 无法对复杂零件进行全面精确测量。 因此,开发一套功能全面、价格低廉的数控机床在线检测系统,对精密复杂零件 “加工-检测-补偿加工”一体化制造具有重要意义。
1 、数控机床在线检测系统组成及原理
数控机床在线检测系统主要由测头、数控机床、信号接收装置和计算机组成。在线检测时,在检测系统中导入零件 CAD 模型,选取检测点,生成检测程序,进行仿真校验。仿真校验无误后,计算机通过数控机床通信接口将检测程序传送给数控机床,数控机床驱动测头按检测路径运动,当测头接触到零件后, 发出触发信号,信号被接收装置接收,并传给转换器,转换器把信号处理后传给数控机床控制系统,机床停止运动,测点坐标被保存下来。
然后进行下一点测量,等所有点测量完毕,测点坐标通过通信接口传输给计算机,计算机对检测数据进行后续处理,生成检测报告。数控加工在线检测原理如图 1 所示。
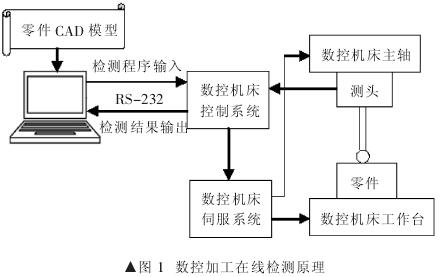
2 、数控机床在线检测系统开发
笔者开发的数控机床在线检测系统是以配置FANUC 0i MC 数控系统的加工中心为执行设备 , 以UG NX10.0 三 维制图软件为平台 , 借 助 UG/OpenGRIP、 UG/Open Menu Scr[9]等 UG 二次开发工具,将矩阵工厂数学软件 MATLAB 2016 和数控加工仿真系统 VERICUT 8.0 集成于 UG 操作环境下, 进行在线检测的一款数控机床在线检测系统。
这一在线检测系统具有检测模型测点选取、检测程序生成、检测仿真、加工中心串口通信、 检测误差补偿计算及数据处理等功能。 主要由 UG、MATLAB 和 VERICUT 三大模块组成。
2.1 检测点信息提取
检测点信息是检测系统获取检测零件表面数据信息的主要依据。主要指曲面检测点的三维坐标、检测点相对于检测曲面的法向矢量、 检测点相对于检测曲面的切向矢量等[10]。 数控机床在线检测时,首先要对检测曲面检测点的数据信息进行提取,为实现上述功能,在二次开发中, 笔者用 UG/Open GRIP 以 NURBS 曲面在 U、V 两个方向的节点矢量, 均匀划分采样网格,设步长,生成节点,以节点作为曲面检测点。 检测点确定后,定义 surf 为曲面变量,pt(200)为测点变量,fxl(3)为检测点相对检测曲面的法向矢量 ,qxlu (3) 为检测点相对检测曲面的 U 向切向矢量,qxlv(3)为检测点相对于检测曲面的 V 向切向矢量。 编写检测点信息读取程序,调用函数 IDENT,选取检测曲面和检测点,保存变量,用 FETCH 和 READ 命令读取检测点三维坐标。调用函数 SPARF,取检测点 U、V 参数值。调用函数 SNORF, 求取检测点相对于检测曲面的法向矢量。调用函数 SDDUF, 求取检测曲面在 U 向的切向矢量。调用函数 SDDVF, 求取检测曲面在 V 向的切向矢量。调用函数 IF、JUMP 循环语句,重复上述操作,待检测曲面所有检测点的三维坐标、法向矢量、切向矢量信息获取后,用 PRINT 语句以 *.txt 格式输出到列表,
检测曲面检测点数据信息提取完毕。
2.2 检测路径规划及 NC 代码的生成
曲面检测点数据信息提取后, 利用软件 MATLAB2016 读取检测点信息 ,按照测头沿检测点法向矢量检测的原则、规划三轴联动加工中心在线检测路径。在线检测路径规划完成后, 根据建立的三轴联动加工中心运动模型,编制后置处理程序,生成 NC 检测代码,并把 NC 检测代码传输给加工中心,加工中心驱动测头按照规划的检测路径运动, 就可以实现加工中心对零件的在线检测。 为实现上述功能,在二次开发中,笔者对编制的 MATLAB 2016 源程序进行了打包处理,并以 *.dll 的文件格式进行了保存。
在 UG10.0 环境下,通过 UG/Open Menu Script 开放的端口函数, 用 *.men文件对编制的 MATLAB 2016 源程序 *.dll 文件进行了调用,使 MATLAB 2016 与 UG10.0 在程序调用和数据信息转换间实现了对接[11]。
2.3 检测仿真
为避免干涉, 在线检测前需要调用 VERICUT8.0对检测路径进行仿真。为实现上述功能,通过新建系统环境变量, 增设 VERICUT8.0 程序运行图标, 实现了UG10.0 与VIRECUT8.0 的无缝连接 。 具体操作过程为:在电脑属性中打开系统属性对话框,选择高级,新建 系 统 变 量 CGTECH_INSTALL, 输 入 变 量 值 D:\Program Files\vericut 8.0\VERICUT, 点击确定 ; 新建系统变量 CGTECH_PRODUCTS,输入变量值 D:\ProgramFiles\vericut 8.0\VERICUT\windows64, 点击确定 ; 新建系统变量 LSERVOPTS, 输 入 变 量 值 -s "C\ProgramData\CGTech\license\cgtech.lf",点击确定 ; 新建系统变量 LSHOST, 输入变量值 GYZX6-PC, 点击确定; 新建变量UGII_VENDOR_DIR, 输入变量值 D:\Program Files\vericut8.0\VERICUT\windows64\nx\NX10\english,点击确定。 通过新建上述系统变量,并赋值,就使 UG10.0 与VIRECUT8.0 实现了对接。新建系统环境变量如图 2 所示。
具体使用时,打开 UG10.0 进入加工环 境 , 在工具条上单击 VERICUT8.0 图标 , 进 入VERICUT8.0 界面 , 就可以对检测路径进行仿真 、 优化。
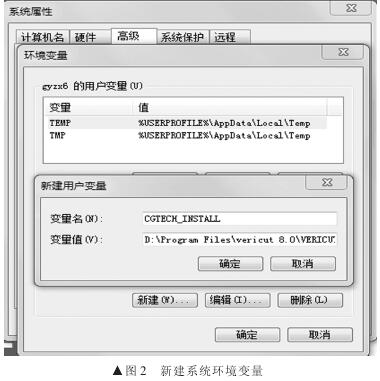
3 、试验验证
为验证基于 UG NX 10.0 二次开发的数控机床在线检测系统的可行性和有效性, 笔者在三轴数控机床上进行了试验验证。 具体过程为,在 UG NX 10.0 中创建检测零件 CAD 模型,用 UG/Open GRIP 选取检测曲面,确定检测点,调用相应函数,提取检测点坐标矢量信息,并保存。 检测零件曲面测点分布如图 3 所示。 检测 点 信 息 提 取 后 , 在 UG10.0 环 境 下 调 用 MATLAB2016 软件,读取检测点三维坐标 、法向矢量、切向矢量信息,自动规划检测路径,路径规划好后,设置测头半径、进给率、定位距离,后置处理程序生成在线检测 NC代码,保存到指定文件夹路径位置。
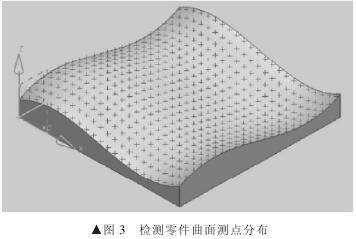
在 UG NX 10.0 环境下启动软件 VERICUT8.0, 根据加工中心和检测零件模型,读取在线检测 NC 代码,在线检测过程进行仿真, 仿真无误后, 将在线检测 NC 代码导入加工中心,加工中心驱动测头对零件进行在线检测,加工中心接收到的检测程序如图 4 所示。
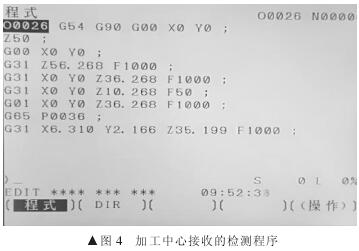
试验中, 笔者对检测零件曲面上五个测点的在线检测数据与三坐标测量机检测数据进行了对比, 结果显示,基于 UG NX 10.0 二次开发的数控机床在线检测系统检测数据与三坐标测量机检测数据的最大误差为0.05 mm。 考虑到检测零件二次装夹定位中产生的测量系统误差的存在,笔者认为基于 UG NX 10.0 二次开发的数控机床在线检测系统是可行有效的。
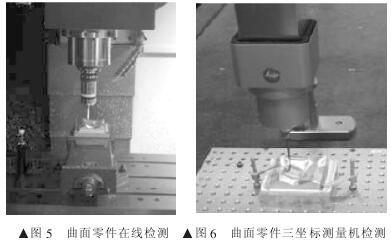
曲面零件在线检测如图 5 所示, 曲面零件三坐标测量机检测如图6 所示, 曲面零件五个测点的在线检测数据与三坐标测量机检测数据的比较见表 1。
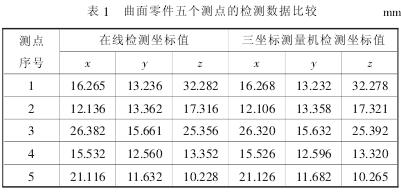
4 、结束语
通 过 UG/Open GRIP、UG/Open Menu Script 等UG 二 次 开 发 工 具 , 将 软 件 MATLAB 2016 和VERICUT8.0 与 UG NX 10.0 软件进行了有效集成 ,在UG NX 10.0 环境下,通过 MATLAB 2016、VERICUT8.0与 UG NX 10.0 之间的数据信息转换,实现了加工中心对加工零件的在线检测, 有效提高了精密复杂零件数控加工质量和效率,也为精密复杂零件“加工-检测-补偿加工”一体化制造提供了参考依据。
投稿箱:
如果您有机床行业、企业相关新闻稿件发表,或进行资讯合作,欢迎联系本网编辑部, 邮箱:skjcsc@vip.sina.com
如果您有机床行业、企业相关新闻稿件发表,或进行资讯合作,欢迎联系本网编辑部, 邮箱:skjcsc@vip.sina.com