汽车主模型制造中数控加工中心的选型及应用
2023-10-30 来源: 东风汽车公司技术中心 作者:李庆丰 杨 兴
随着汽车工业不断进步,人们对汽车的审美意识和个性化需求也越来越高,激烈的市场竞争推动着汽车产品的高速发展,汽车模型制作己成为新车型开发中不可缺少的关键环节,是汽车造型设计在效果图的基础上构思进一步完善的过程。汽车模型的制作是多工种、多技能的综合体现 , 在模型制作阶段,制作过程选择高效的数控加工中心不仅能够完成设计质量需求,同时能够高效制作模型,为汽车短周期研发提供有力保障。
一、汽车主模型的种类和制作特点
汽车主模型从早期的效果图开始,经过泡沫体态模型,油泥模型,仿真模型,风动模型,色彩模型,验证模型,验证台架及空间验证模型的效果验证,最终完成汽车造型的定义并批量生产。
1.汽车模型的主要制作类型
1)油泥模型 : 是车身设计中用油泥雕塑的汽车车身模型。1972 年美国通用汽车公司将油泥应用到汽车设计开发模型上。对大多数世界知名车公司而言,制作油泥模型是设计过程中非常重要的一个环节。油泥模型分为造型油泥模型和风洞油泥模型,造型油泥模型完成产品定义 ; 风洞油泥模型完成车辆的风阻测试评定。
2)色彩模型:汽车造型的零件进行色彩定义,对模型的色彩设计及搭配进行评审并做出决策,对不和谐的色彩重新设计或加以改进,使内、外饰色彩达到更佳的效果。
3)验证模型 : 验证汽车实车数据的正确性、有效性和可信性的研究与测试过程。一般包括两个方面 : 一是验证所建模型即是建模者构想中的模型 ; 二是验证所建模型能够反映真实系统的行为特征 ; 有时特指前一种检验。
4)仿真模型 : 是指建立在汽车设计建模后,CAS 经过油泥模型确认后,制作相对应硬质模型进行外观确认和评审,后期根据评审意见进行相应外观的修改和优化。典型汽车模型的制作阶段和周期如图 1 所示。
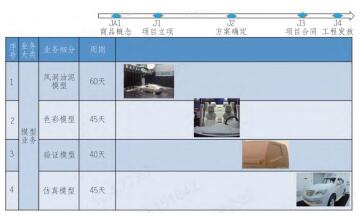
图 1 典型汽车模型的制作阶段和周期
2.汽车模型的主要制作特点
(1)汽车模型材料要求制作加工比例为 1:1,模型外表面材料为糊状可加工树脂,局部部件可用块状树脂或 ABS,树脂密度不得小于 0.6kg/ m3,该材料应具有 :
1)尺寸稳定,对温度和湿度变化不敏感 ;
2)运输过程中表面不易损坏 ;
3)可获得很好的表面精度并可保持不变形 ;
4)模型表面的可加工树脂厚度须保持在30~40mm 左右 ;
(2)汽车模型质量及精度要求
1)数控加工中加工刀具(直径 Φ20mm 球刀)步距应≤ 0.60mm,表面波峰与波谷差值应≤ 0.02mm;
2)模型加工后,铣刀纹要保持连续光顺、过渡平滑、色泽均匀,模型表面不允许有未加工面 ;
3)模型铣削加工后,表面上不得有气孔砂眼、斑状脱落等缺陷 ;
4)模型装配后喷漆前,模型零部件加工尺寸应满足设计数据,尺寸公差 ±0.3mm,模型零部件装配规定的空间位置、间隙和面差,复位基准精度≤ 0.05mm;
5)色彩模型和仿真模型车身表面按甲方提供的造型色彩效果涂装 ; 表面涂装要求 : 刀痕轻微打磨,不保留加工效果,漆膜应均匀、光滑,无流挂、微粒、纤维及桔皮状,不允许有可见的针孔沙眼。验证模型刀痕不允许打磨,保留加工效果,后期模型底灰喷涂处理。
二、汽车模型使用数控加工中心选型的主要参数
针对汽车模型加工技术特点和要求,对数控加工中心(见图 2)的主要参数进行梳理,主要数控加工中心重点参数为 : 数控加工中心床身结构 ; 高速电主轴参数 ; 数控系统 ; 测量系统 ; 使用环境要求。
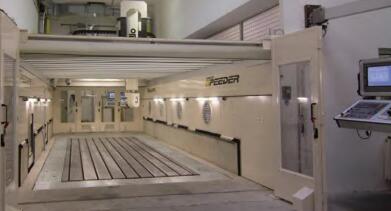
图 2 典型桥式龙门结构加工中心
1. 汽车模型数控加工中心的结构件参数选择
汽车模型的尺寸 : 长度方向约 5000mm; 宽度方向约 1800mm; 高度方向 1600mm。采用立式工作台固定的高架桥龙门5轴5联动数控机床,可配备各种规格五轴头,其结构灵活性使其特别适合加工模型类零件 : 整体大型模型加工(如汽车、船舶、轨道车辆、航天); 飞机结构件 ; 复合材料高速加工。
(1)直线轴参数
根据汽车尺寸参数,结合数控加工的刀具行程,确定数控加工中心的轴行程(见表 1)。
表 1 加工中心的行程参数
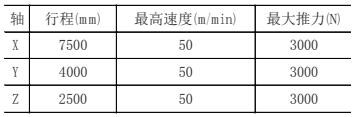
电主轴回转中心到工作台平面的最小距离为250mm 带正压防尘光栅尺的 X-Y-Z 轴定位精度如表 2 所示。
表 2 加工中心的定位精度和重复定位精度
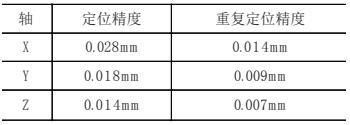
(2)数控加工中心床身结构零件的要求
机床床身结构件的确定 : 为了获得直线轴最佳的动态性能,所有移动部件的设计计算均考虑到重量、刚性和减振等因素。结构件要预先进行有限元分析设计(见图 3),然后借助结构设计的专有软件,分析各轴的频率响应和加工模拟,进一步优化结构设计,从而实现各种的动态响应、精度和刚性的最佳匹配。
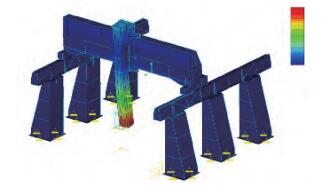
图 3 机床结构设计有限元分析
(3)数控加工中心结构零件的应力处理
结构件采用电焊钢材料。如图 4 所示,结构件在焊接成型后,先进行去除应力热处理。粗加工后、精加工前,进行进一步的消除应力处理,以消除结构件内部的最终残余应力,确保机械部件维持稳定的几何精度。
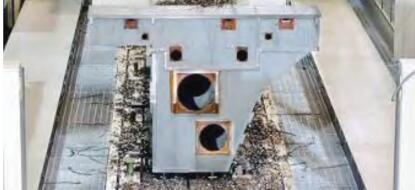
图 4 机床结构应力处理现场示意图
(4)数控加工中心驱动轴的间隙补偿和 A、C 轴结构
驱动轴可以采用直驱伺服电机和齿轮传动方式。直驱方式结构简单、无磨损、噪声低、维护方便。齿轮传动方式响应速度相对滞后,后期调试和维保需要对间隙进行相关补偿工作。
1)齿轮传动的间隙补偿方式机床各轴驱动(背隙补偿)机床所有的伺服轴 (X) (Y) 和 (Z) 都是通过双电机驱动斜齿轮 -齿条传动系统实现的。电子反向间隙补偿是借助数字驱动在两个齿轮间产生一个机械预载(机械耦合)。系统驱动一个齿轮稍稍领先于另一个,由此实现预载。其优势就是不需要任何调整,因为一个齿轮始终领先于另一个,这样就自动弥补了齿轮和齿条间产生的磨损。齿轮传动补偿示意图如图 5 所示。
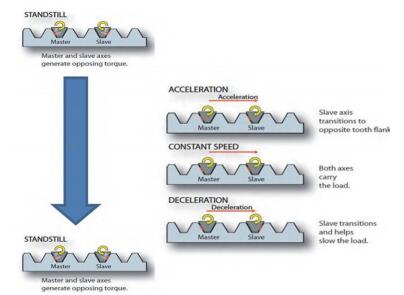
图 5 齿轮传动补偿示意图
2)数控加工中心 A、C 轴结构双轴主轴头 由两个极坐标 A/C 构成,两轴均由力矩电机驱动,以获得最好的动态性能。其非对称结构可确保性能、刚性和重量的最佳组合。主轴一侧包含带气动夹紧系统的 A 轴电机,液压和气动连接,和 A 轴检测。C 轴和 A 轴都可在任何位置气动夹紧定位。C 轴和A 轴电机由恰当匹配的冷却系统进行循环冷却,以确保在任何运行工况,工作稳定。
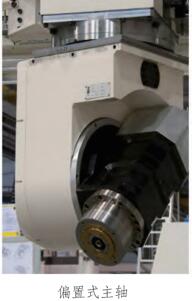
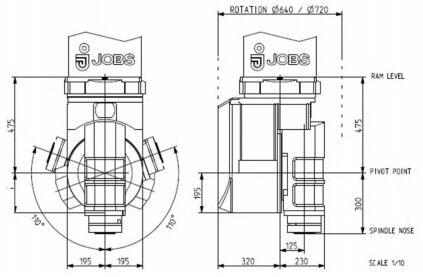
图 6 偏置式主轴示意图
2.高速电主轴的选型
电主轴 ELECTROSPINDLE 24000 rpm(D.02.96JF): 该型号主轴是模型加工中特别配置的高速电主轴,由专门的冷却回路保持恒温。换刀时,主轴锥孔压缩空气吹气保护。高速电主轴的选型参考如表 3 所示,主轴功率扭矩图如图 7所示。
表 3 高速电主轴的选型参考
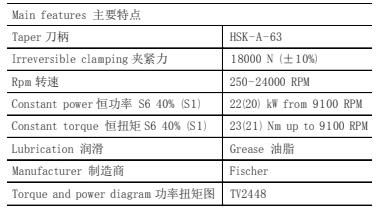
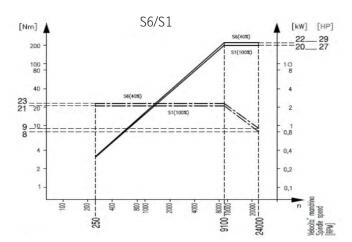
图 7 主轴功率扭矩图
3.数控系统的选型
五轴数控加工系统综合性能较好的型号是 :FANUC31I; HEIDENHAIN iTNC 640; 西门子 840D。以海德汉系统为例,海德汉 iTNC640HSCI 数控系统和同型号驱动原件能够最大限度发挥出机床机械和所配驱动的特性。模型五轴加工需要数控系统提供相应的功能 :
①海德汉实时操作系统,显示 PDF 文件。图纸,工艺指令直接在数控系统中打开 ;
② iTNC 6400 中直接访问互联网,内置浏览器 ;
③在 iTNC 640 中能直接打开多种文件格式且能用相应编辑器编辑,部分格式文件 ;
④文本文件(.txt,.ini); 图形文件(.gif,.bmp,.jpg,.png); 表(.xls,.csv); 网 页文件(.html);
⑤标准化的操作系统对话框显示格式 ;
⑥设置防火墙,提供更高数据安全性。
4.汽车模型数控加工中心测量系统的选型
加工中心的测量系统分为工件测量系统和刀具测量系统,为数控加工的模型质量和数控切削参数提供数据支撑。
(1)工件测量系统的选型
接触式测头能够在加工过程中和加工结束后自动检测工件,从而可以更精确地控制工件精度,显著提升加工精度及生产效率。可实现以下功能 : 工件 / 夹具预定位 ; 测量监测加工去除量 ; 加工过程中检验 ; 加工结束后尺寸核验。接触式测头采用无线传输,可自动更换夹持刀柄,检测系统管理软件可从机床程序内自动调加载程序。RENISHAW RMP60 接触式测头HSK-A-63 刀柄 包含海德汉检测循环 (D.10.24.H)。标配探针直径 φ6 mm,长度 50mm。
(2)刀具测量系统的选型
激光对刀系统可以精确可靠地完成以下任务 : 刀具长度 ; 刀具半径 ; 刀具破损检测可以直接由数控系统加载并管理对测量值的自动补偿。最小检测长度 120mm,最大检测直径 300mm。测量系统附件包含 : 激光单元固定到机床上的支架 ; 信号处理系统 ; 管理软件 ; 用于修改和补偿的特殊软件循环。
5.汽车模型数控加工中心使用的环境要求
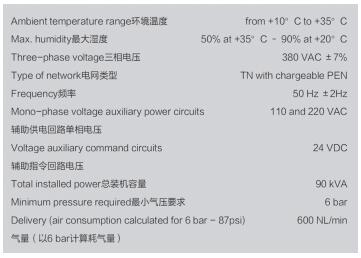
三、结束语
随着技术和装备的引进不断的提升,国内模型制作水平已经缩小了与国际模型先进地区的差距。作为模型制作的核心装备,除了在数控加工装备选型上参数不断细化外,必须正确定位汽车模型的加工类型和范围,这样才能选定出适合企业需求的设备型号。同时从技术水平上和管理水平突破,使得汽车模型实现短周期、高质量、低成本的目标。东风技术中心在 2017 年使用高速加工中心后,累计完成模型 52 台,机床开动率保持 58%,完成 12 类车型的开发,为东风自主品牌研发提供了有力的保障。
投稿箱:
如果您有机床行业、企业相关新闻稿件发表,或进行资讯合作,欢迎联系本网编辑部, 邮箱:skjcsc@vip.sina.com
如果您有机床行业、企业相关新闻稿件发表,或进行资讯合作,欢迎联系本网编辑部, 邮箱:skjcsc@vip.sina.com
更多相关信息