汽车制动主缸体加工工艺改进设计
2022-6-23 来源: 长春科技学院 作者:刘振利
汽车制动主缸体是汽车制动系统中的重要安全部件,柱塞式主缸体(以下简称主缸体)是其中的一种。目前主缸体的加工方式大体分为两种 :一种是采用高端多轴数控设备以工序集中的方式加工,但设备昂贵,投入高,调整时间较长,虽是今后加工方式发展的方向,但普及还需要一定时间 ; 另一种是采用中端数控设备,部分工序集中的生产线方式加工,产线布局灵活,设备成本投入较低,目前在大部分企业仍在应用,但工序的安排和加工方式上存在不合理的地方,有改善的空间,比如,安装孔的加工、避免装夹压痕等方面。
1. 生产加工过程与常见问题
企业在工序的安排和对加工过程改进仍在不断地完善中。在这里主要针对该种加工方式中存在的不足进行加工工艺的改进。主缸体的生产加工过程,通常采用生产线的加工方式,工序一般划分为 5 步(见表 1)。
表 1 主缸体加工工艺流程
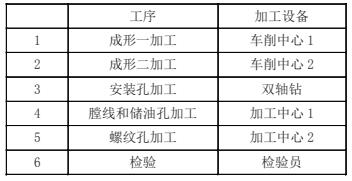
安装孔工序是其中的一道工序(安装孔和加工设备见图 1)。实际生产中,由于主缸体型号较多,生产过程中需要经常进行不同型号的主缸体切换,当更换不同型号的主缸体时,每道工序都要进行夹具的切换调整。不同工序的调整时间不同,如果切换调整过程中某道工序的调整时间过长就会影响到下一道工序的调整,或造成整条生产线处于停滞状态。
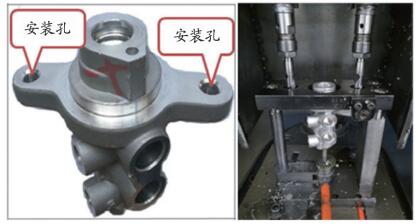
图 1
之前,安装孔工序在切换主缸体进行调整时,产生的废品数量过多,每次的废品数量平均在 7件左右,每条生产线每年产生调整废品近 300 件,造成了很大的浪费。同时,切换主缸体时调整效率低,每次的调整时间在 30~60min 不等,并且加工过程主缸体质量不稳定,经常会影响到下道工序的加工。
因此,针对这种情况,有必要分析问题的原因,对该工序的加工进行必要的改进设计。
2. 原因分析
在主缸体安装孔的加工过程中,采用的设备是台式双轴钻,夹具使用的是手动连杆夹紧方式,它的调整步骤见表 2。
表 2

出现问题的主要原因是 : 由于不同型号主缸体的安装孔间距不一致,在调整时首先要更换夹具上板,夹具上板面有和主缸体安装孔孔距相应的两个导向孔,再手动调整双轴钻的两个轴之间的离,使双轴钻的轴距和上板面导向孔的间距位置相互重合。但是,在调整两个轴和夹具的位置时(前后左右调整),都是手动调整,没有精确的定位,所以很难保证一次调整好两者的位置,需要多次重复 3~5 步骤,调一次,试切一次,尺寸不合格就产生 1 件废品,调整的次数越多产生的废品就越多,调整时间也就越长,造成很大的浪费。
同时,双轴钻刚性不足,夹具夹紧结构的不稳定,在生产加工时很容易造成尺寸超差,影响下道工序的加工。因此,主要问题是 : 调整过程费时,精度差 ; 双轴钻刚性不足(参见图 2)。
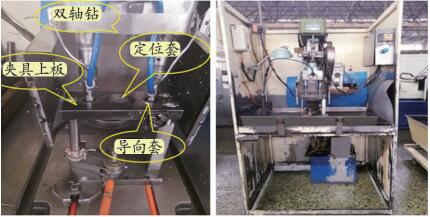
图 2
针对上述问题,安装孔工序原有的夹具和加工机床(双轴钻床)不再适合安装孔加工,考虑到精益生产和优化生产线布局,改进方案为 : 设计一套可同时加工安装孔和膛线加工夹具,并取消双轴钻设备。
具体方法是 : 把安装孔工序移到现有加工中心设备上,现有加工中心设备是指膛线和储油孔加工工序所使用的加工中心设备,因为这台加工中心设备上加工膛线的工序和安装孔工序装夹加工方式非常相似,完全可以把膛线、安装孔这两道工序合并在一起,一次装夹完成原来两道工序的加工。而且,原有膛线和储油孔工序的加工节拍相比其它工序较短,可以充分利用该工序的节拍,而不影响整个生产线的加工节拍(见图 3)。
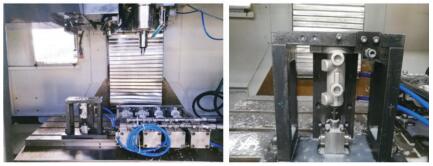
图 3
4. 实施效果
针对原有安装孔调整存在的问题采取了重新设计夹具的改进方式,该套夹具具有如下特点 :
(1)采用气缸夹紧代替原有手动夹紧方式,夹紧准确稳定。
(2)为了减少夹具高度,气缸夹紧没有采用气缸直接夹紧,而是设计了拨叉杠杆机构,设计巧妙合理。
(3)主缸定位套采用由下往上安装的设计,减少主缸体和定位套接触面,更好的避免接触面之间由于垫屑而产生的表面压痕。
(4)夹具上板采用让刀槽和排屑槽设计,一是使夹具上板的通用性大幅提高(不再需要更换上板),二是排屑更顺畅。
具体原理和方案为(见图 4): 在更换调整主缸体时,将相应尺寸的定位套 5 由下往上装入上板 1 中,手持主缸体 2 装入夹具上板 1内,安装孔的法兰面与定位套 5 下端面接触,安装孔 3 外端与定位销 4 接触,限制主缸体轴向转动。然后,扳动气缸 15 的气源开关,气缸 15 推动气缸推杆 14 向下运动,通过销子 13 带动拨叉连杆 12 绕着销子 11 转动,拨叉连杆 12 另一端通过销子 10 带动滑动轴 9 在内套 8 中移动,滑动轴 9 带动与其螺纹连接的顶尖 6 向上运动,顶尖6 顶到主缸体下端中心孔内,将主缸体夹紧。
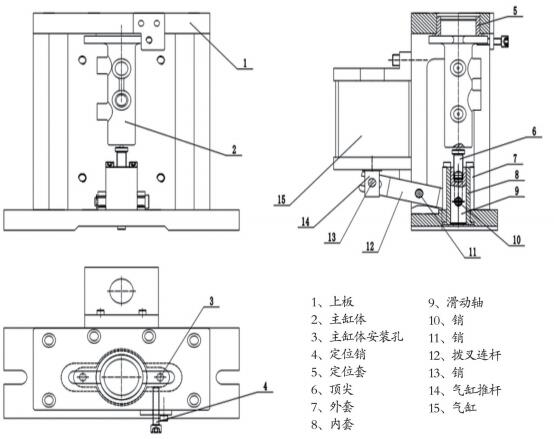
图 4
上板 1 有让刀槽,将加工两个安装孔 3 位置让开,加工刀具在数控程序控制下完成两个安装孔的加工。
取消双轴钻设备,把膛线、安装孔这两道工序合并在一起后,充分利用了加工中心设备,而不影响整个生产线的加工节拍。采用了数控编程方式,调整方便快捷,提高调整效率 80% 以上 ;减少了一道工序操作,并取消了原来工序繁琐的调试工作,操作者劳动强度降低 ; 取消了安装孔工序加工设备,缩短生产线,便于管理和精益生产线的布局。
该方法主要应用于汽车制动主缸体安装孔、膛线、竖孔等加工和工序的优化,以及其它行业主缸体在垂直方向装夹和加工方面的使用,可以提高主缸体装夹的稳定性,控制加工精度,减轻劳动强度等。同时减少设备更新的投入资金,减少设备能源损耗和提高产品的良品率和企业的产能,在主缸体的生产中得到了推广应用。
投稿箱:
如果您有机床行业、企业相关新闻稿件发表,或进行资讯合作,欢迎联系本网编辑部, 邮箱:skjcsc@vip.sina.com
如果您有机床行业、企业相关新闻稿件发表,或进行资讯合作,欢迎联系本网编辑部, 邮箱:skjcsc@vip.sina.com
更多相关信息