高精度桥式五轴加工中心横梁仿形工艺技术
2023-5-4 来源: 通用技术集团沈阳机床有限责任公司 作者:尚 红 赵普金
摘要 : 现代航空航天等行业对零件精度和质量要求较高,需要加工机床具备高精度、高可靠性和精度保持性。国产设备在高精度和可靠性方面与国外先进技术水平还有一定差距,在航空航天等领域国产设备占有率低,在关键核心技术上还有许多 “卡脖子” 问题急需解决。高精度桥式五轴加工中心主要用于飞机部件骨架表面铣削、钻削加工与装配制孔。其加工能力强,尺寸规格大,定位精度高,兼容高效切削,机床具有五轴联动功能。对机床的关键部件大型横梁导轨直线度仿形加工、装配、测量技术研究,是此类机床精度保持性的核心制造技术之一。本文通过对横梁加工、装配及检测精度的制造工艺技术的实践与总结,详述大型横梁的仿形加工及装配工艺过程。
一、依据有限元分析绘出横梁导轨受力变形曲线
高精度桥式五轴加工中心因横梁两端由桥梁、滑座双支撑横跨工作台的结构特点,中间悬挂滑板、滑枕和五轴头等部件,导致横梁导轨除受自身重力外,还需承载较大的重力及倾覆力矩,实际装配挂梁后由于重力及倾覆力矩作用横梁产生塌腰现象。
1.Ansys静力分析
以装配体的形式建立横梁三维模型,通过有限元对横梁静、动态性能进行分析,依据横梁振动相对变形的振型和幅值,以及机床的工作环境和机床设计的结构力学理论,提出横梁结构及加工的改进建议,从而对横梁进行仿形加工。
建立横梁装配体三维模型,以 X 方向为垂直于横梁向内、Y 方向为平行于横梁向左、Z 方向为垂直于横梁向上为正。依据有限元分析,设计大型横梁 1# 上导轨大面、2# 上导轨立面、3#下导轨大面、4# 下导轨立面仿形曲线图(见图 1)。

图 1 横梁导轨面示意图
2.横梁导轨仿形曲线
装配状态下横梁仅受重力作用,由于受自身重力及悬挂滑板、滑枕等部件的重力导致变形,横梁上下两条直线导轨面中间部位变形最大,最大位置为横梁中间上端部分 , 变形趋势主要为横梁中间部分下沉和绕 Y 方向扭转。横梁受重力和切削力共同作用,受 X/Y/Z 方向切削力情况下的整体和分方向静力变形,最大位置均为横梁中间上端,其中受 X 方向切削力变形明显,主要是因为中部上端受切削力后扭转增大 ; 受 Y 方向切削力变形不大 ; 受 Z 方向切削力变形中部上端变化明显。横梁的最大变形量发生在滑板移动到横梁中间,滑枕移到下极限位置时。加工工艺根据其变形曲线仿形加工,减少滑板、滑枕在横梁上移动时产生的直线度误差。横梁导轨受力变形量仿形曲线图(见图 2)。
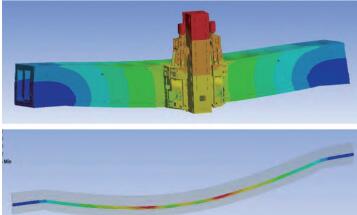
图 2 横梁导轨仿形曲线图
二、横梁仿形加工
从横梁材料硬度、热处理、加工、装配及检测精度入手,通过横梁加工及装配过程直线度等精度检测数据分析,找出横梁导轨面加工曲线及工艺方法满足装配精度要求。
1. 材料及热处理
高精度桥式五轴加工中心大型横梁材料为焊接低合金结构钢 16Mn,零件轮廓尺寸长 × 宽 ×高为 10460×1815×1580mm,净重 25.5 吨,标准材料 16Mn 钢材厚度大于 50~100mm 方,抗拉强度 Rm 为 470~620N/mm2。根据硬度抗拉强度对照表德国标准 DIN50150 查得布氏硬度为143~185HBW。
大型零件材料为焊接件的由于焊接引起焊件不均匀的温度分布,焊缝金属的热胀冷缩等因造成焊接残余应力,零件在机加工之后其内部易残存应力,所有这些内应力都必须消除。消除残余应力最通用的方法是去应力退火,即将零件放在热处理炉内加热到一定温度 (Ac1 以下 ) 和保温一定时间,利用材料在高温下屈服极限的降低,使内应力高的地方产生塑性流动,弹性变形逐渐减少,塑性变形逐渐增加而使应力降低。焊接件去应力退火加热温度为 500~550℃,保温时间为 2~4h,炉冷至 300℃以下出炉空冷,消除加工应力退火加热温度为 400~550℃,保温时间为 2~4h,炉冷或空冷。横梁去应力退火对零件精度保持有重要作用,零件质量稳定性较好,因此大型横梁应二次以上去应力热处理即毛坯焊接
后及粗加工后去应力退火。
依据标准并结合实际应用绘出热处理温度 -时间工艺曲线图(见图 3)。热处理工艺规程 :大型焊接横梁装炉底部垫平,入炉温度不大于300℃,加热升温速度不大于 100℃ /h,加热至500~550℃保持温度 4h,后随炉冷却至 300℃以下,出炉空冷。
2. 横梁加工工艺
大型横梁加工工艺流程 : 毛坯( 焊接16Mn)- 毛坯去应力退火 - 划 - 粗铣 - 时效处理(二次去应力退火)- 半精铣(放置 48h)-精铣(仿形加工)- 摇钻 - 钳序(清理)- 油漆。大型横梁在加工前应划线,照顾支撑面及直线导轨面壁厚均匀,回字内腔壁厚均匀且成矩形。粗铣选用大型龙门铣床,用可调垫铁,以导轨面为粗加工基准,铣背面做为导轨面粗铣加工基准面,粗铣序横梁直线导轨向上,铣出导轨形状,去除机械加工余量,提前发现毛坯缺陷等。横梁粗加工后要进行二次时效,去除残余应力退火。半精铣选择大型数控龙门镗铣床,为避免大型横梁吊装、翻转产生变形,大型横梁应在此序以装配状态加工,以导轨面为装置面,精铣横梁支撑面做装置面,除直线导轨、光栅尺、齿条基准面
留量外,其余防护、管路及电气元件等结合面、螺纹孔均加工完成,保证零件相关尺寸精度。
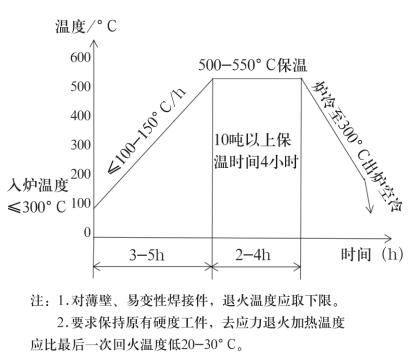
图 3 温度 - 时间工艺曲线图
关键工序精铣序,选择精密龙门五面加工中心,先以导轨面为装置面,精铣横梁支撑面做装置面,保证支撑面平面度不大于 0.05mm。再以装配状态支撑面为装置面,将四块垫铁按横梁支撑面内侧基面位置固定于方箱座上,自铣垫铁钞平,横梁放置于四块钞平垫铁上,按导轨大面找正 0.02mm,检测各垫铁与横梁支撑基面间是否有缝隙,将 4 个 0.1mm 等厚铜皮放于垫铁上,横梁落下后,抽动铜皮不动,可以进行加工(见图 4)。用直角头精铣齿条安装正、侧面,检测正面和侧面直线度,通过数据曲线分析机床实际精度。按设计仿形曲线图及机床实际精度综合修正值编程,按程序再次加工齿条安装正、侧面验证曲线,加工后检测。检测直线度与导轨设计仿形曲线一致后,仿形加工上下导轨大面、立面,同时精铣齿条面、光栅尺面等安装基面,精铣时压板松开不夹紧。
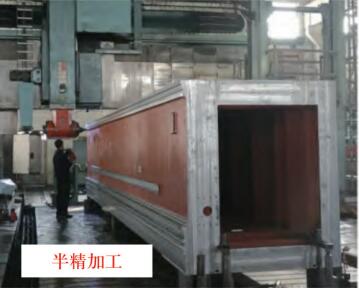
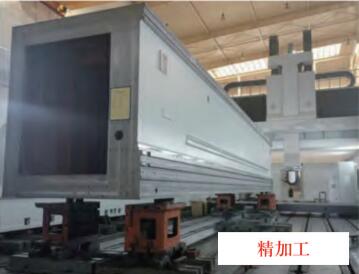
图 4 横梁加工示意图
大型横梁精加工设备采用沈阳机床自制的龙门桥式五轴加工中心 GMC50200u, 用A/C 五轴头(刀柄 HSK-A63)直角定位精铣仿形曲线,设备精度具备 X/Y/Z 定位精度0.02/0.015/0.01mm,重复定位精度0.008mm。加工刀具 : 大面精铣用方肩面铣刀 Φ63(Z=5),立面精铣整体硬质合金立铣刀 Φ20(Z=3),液压夹紧刀柄,切削参数均为转速 S=1000r/min, 进给 F=285mm/min。
三、横梁装配
高精度桥式五轴加工中心与横梁相关的几何精度有:G3 项Y轴轴线运动的直线度 : ① 在YZ 垂直平面内 ; ② 在XY水平平面内允差值 :0.014/1000mm;0.035/7000mm。G4项Y轴移动的角度偏差 : ① 在 YZ垂直平面内 ( 俯 仰 ); ② 在 XZ 垂直平面内(倾斜); ③在 XY 水平面内(偏摆)允差值:0.015/1000mm;0.04/7000mm。
1. 横梁装配工艺
横梁装配工艺流程 : 横梁精加工后入装配 -单件直线度检测 - 线轨装配 -- 安装线轨后直线度检测 - 齿条装配 - 光栅尺装配 -Y 轴驱动装配 -安装液压管路 - 电气接线 - 安装行程开关确定 Y轴行程 -Y 轴总装直线度检测(加修或刮研调整)-角度偏差检测(加修或刮研调整)- 防护安装。通常,龙门式数控机床为保证装配后的 Y 轴运动的直线度,工艺方法根据设计变形曲线图进行仿形加工,但因设备精度、环境温度、材料硬度等诸多因素影响,实际铣削仿形曲线往往会随之发生变化。横梁精加工后转部装,为减少环境温度偏差造成的直线度误差,横梁进部装在安装直线导轨前、后应复检导轨正、侧向直线度,对于直线导轨横梁部装检测有两种姿态即平放或立放检测。平放即直线导轨大面向上,用自准直仪检测
直线度,根据直线度计算软件得出上下导轨正、侧向曲线值,应用于小型批量型龙门式数控镗铣床横梁。大型横梁采用立放即装配状态,用激光校准仪检测导轨直线度,检测数值与设计曲线值对比,不合格转加工车间加修,合格转总装挂箱检测。
总装挂箱后实测 Y 轴移动直线度,滑枕处于最下端,用激光校准仪通过专用支板具与滑枕结合置于滑枕上,200mm 步长采数,分别得出 YZ垂直平面内正向直线度,XY 水平平面内侧向直线度。用电子水平仪置于与滑枕连接支架具上,500mm 步长采数,移动滑板 Y 轴由负向正,得ZX 垂直面内角偏和 YZ 垂直面内角偏。用自准直仪移动滑板 Y 轴由负向正,得在 XY 水平面内角偏。通过总装挂箱后实测 Y 轴运动直线度及角度偏差,分析直线度及角度偏差是否满足几何精度允差值,如与要求不符合装配分析直线度及角偏数值及曲线图形,计算实际曲线修正值并编制程序加修,或装配采取刮研方法,达到整机几何精度的验收要求。
2. 横梁装配刮研
横梁在总装精度检测后为减少其加修过程中的变形,装配采取刮研方法进行精度调整。高精度桥式五轴加工中心大型横梁直线导轨呈对称式设计,依据仿形曲线并结合实际,装配仿形曲线导轨直线度检测精度在 YZ 垂直面内下导轨大面直线度为 0.01~0.02mm,导轨中部凹,上导轨大面直线度为 0.025~0.03mm,导轨中部凹。在 XY 水平面内上、下导轨立面直线度为0.1~0.13mm,导轨中部上凹下凸,上下导轨平行度 0.02mm。仿形加工后,部装安装直线导轨,用电子水平仪检测导轨直线度,对比理论曲线 : │实测值 - 理论值│≤ 50μm,导轨直线度基本符合设计曲线允差范围。总装挂箱并安装五轴头后Y 轴移动用激光校准仪检测导轨直线度及用电子水平仪检测角偏,装配记录检测数值并分析。为减少横梁反修周转变形,装配采用刮研横梁上下导轨大面及立面方法,使用电动或手动刮刀,通过刮研导轨大面和立面,提高 Y 轴移动的直线度及角偏精度。刮研方法,刮研前根据总装检测数值及图形,先确定刮研位置及范围、刮研量、刮研次数。按 200mm 一段划线做好标记,导轨面刮研应边刮研边检测,每次刮研严格控制刮研量,不许刮过量,每刮一次需用专用研具检验接触率 ,当刮研直线导轨两端时,假导轨面也需要刮研,保证假导轨与导轨对接处平整,不能出现台阶。刮研完成后,安装直线导轨检验几何精度,若不合,再一次进行刮研,直至合格为止。
四、横梁直线度检测方法
导轨直线度现有四种检测方法 : 平尺拉表法、自准直仪(平行光管)、水平仪、激光校准仪。平尺拉表法因为受平尺长度影响,只能检测横梁局部的直线度,所以不采用。一般情况下,横梁直线度检测用自准直仪,通过专用桥板长200mm 置于直线导轨大面及立面上,检测平数随导轨长度增加而增多,记录数据后通过输入计算机直线度计算程序软件,生成图形曲线。框式水平仪一般用于调整横梁水平,因检测直线度效率低及读数误差大,现已很少使用。大型横梁直线度检测,为提高检测精度及检测效率购置高精度的电子水平仪、激光校准仪、直线度镜组,并根据检测方法设计专用的滑块连接板、平行检具、等高块等。电子水平仪因无读数误差、数据可传输、可通过软件计算生成曲线图,操作简单等优
点,为工艺方法广泛推广使用。
五、结束语
通过对大型横梁仿形加工及装配的实践,提出横梁设计及工艺优化的建议。
(1)横梁结构直线导轨应采用上下导轨侧基准在下导轨形状平移式分布,不应如床身直线导轨形状对称式分布(见图 5)。优点在于 : ①侧基准在下可作为直线导轨的支撑面,通过预变形仿形加工凸形补偿导轨因重力塌腰 ; ②平移式侧基准面因中凸式仿形加工,立铣刀为切出式切削,切削力小,切削精度及效率高,相反如果对称式分布其中一条侧基准为切入式吃刀,切削力变大,切削精度受影响 ; ③平移式侧基准对于大型横梁立式装配有利。大型横梁为避免吊装、翻转的变形,部装采用装配状态安装直线导轨、齿条、光栅尺,直线导轨侧压块安装方便且侧顶力均匀。相反如果对称式分布其中一条侧基准在上,导轨仿形为凹形,侧压块在锁紧固定时,需要较大的力,导致直线导轨侧基准因受力不均而变形,影响装配精度。④平移式侧基准对于装配刮研有力。因侧基准为平行中凸,装配刮研只刮高点,操作相对容易且准确快捷。而对称式分布两条侧基准仿形为上凹下凸式,凹面刮研量大且困难。
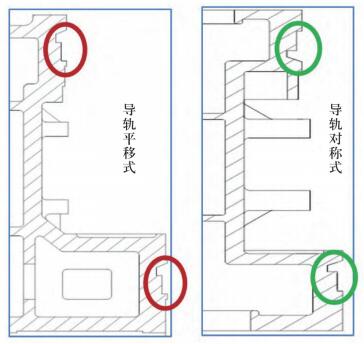
图 5 横梁直线导轨分布
(2)大型横梁超重超大,因结构优化横梁外观差别较大。铸件横梁上下导轨阶梯平移式布局、焊接横梁背板整板煨弯式设计、大型焊接横梁回字腔整板筋加强型设计等,大型横梁因吊装翻转困难且容易变形,建议横梁半精加工、精加工按装配状态自然装夹,保持加工及装配基准统一。
投稿箱:
如果您有机床行业、企业相关新闻稿件发表,或进行资讯合作,欢迎联系本网编辑部, 邮箱:skjcsc@vip.sina.com
如果您有机床行业、企业相关新闻稿件发表,或进行资讯合作,欢迎联系本网编辑部, 邮箱:skjcsc@vip.sina.com
更多相关信息