加工中心圆度误差的原因分析及调整方法
2021-7-30 来源: 中国航发西安动力控制科技有限公司 作者: 弋博
摘要:针对加工中心在加工过程中经常出现的因圆度误差而导致零件超差现象,为避免此类问题出现,分析了圆度误差引起的原因,以及在实际机床加工过程中如何抑制此类问题,以确保零件加工精度需求。
关键词:加工中心;圆度误差;原因分析;调整
圆度误差是指在回转体同一横截面内被测物体实际圆对理想圆的变动量。数控机床在长期使用过程中,滚珠丝杠、导轨及轴承或多或少存在一定程度的磨损,同时,由于保养不到位、缺少润滑及大吃刀量等因素会加剧机械部件磨损,造成数控设备几何精度加速劣化,这些都是引起圆度误差的因素。数控系统动态响应不稳定,伺服优化不完善,也会影响数控机床的圆度误差。
一般在机床实际应用过程中,可以通过球杆仪或设备自带圆度测试功能对加工设备进行圆度误差检测。Siemens 840Dsl数控系统圆度测试功能可以在不需要零件试切的情况下,通过数控程序模拟加工,配合数控系统强大的计算能力和位置反馈功能,测量出机床实际与理论的圆度误差,通过对圆度测试得出的不同图形进行分析,可以得出不误差产生的原因及此类误差的调整方法。一般引起圆度误差的主要原因有插补轴反向间隙大、反向跃冲、伺服不匹配、两插补轴不垂直及机床振动等。下面以Siemens 840Dsl数控系统为例进行说明。
1. 反向间隙误差
机床反向间隙误差是指机床某一轴在运动过程中,从正向运动变为反向运动时,在一定角度内,尽管驱动电动机带动丝杠已经反转,但工作台还要等丝杠和螺母间隙消除后才能反向运动,这个间隙就是机床轴的反向间隙,一般反映在丝杠的螺旋角度上,在半闭环数控系统中,轴在反向运动时指令值和实际运动量之间的差值即为该轴的反向间隙误差值。
(1)反向间隙对圆度误差的影响 反向间隙的存在会影响机床的定位精度和重复定位精度,降低数控机床加工精度,在加工中心铣圆过程中会造成圆度误差。当Y轴在反向运动过程中,由于反向间隙的存在,会造成Y轴反向后滞后于X轴进行插补运动,铣圆加工会出现如图1所示结果。
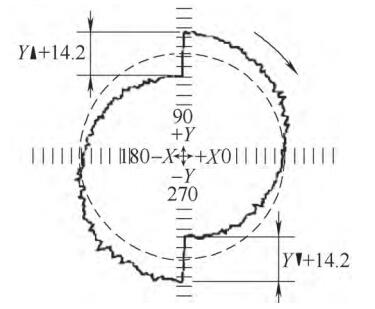
图1 反向间隙造成的圆度误差
(2) 反向间隙测量与调整 影响机床轴反向间隙误差的因素多种多样,从驱动电动机到运动部件之间所有的机械联接件都会存在间隙,电动机对丝杠的联轴结是否松动、滚珠丝杠制造误差、丝杠预紧是否过紧或过松、丝母与运动部件联接是否紧固,都是造成机床轴反向间隙的原因。对于机械部分无法消除的间隙,需要在数控系统中对反向间隙进行补偿。
如图2所示,进行反向间隙测量,用一磁性表座固定一个位置,千分表表头压在要测量轴的工作台上一固定位置,千分表刻度调零,相同方向继续移动进给轴一定距离,反向移动轴到初始位置,读取千分表的差值A,同样测量7次后得出的平均值即为该轴的反向间隙误差,即A=(A1+A2+A3+A4+A5+A6+A7)/7。把测量计算出的值A写入对应轴的数MD32450中,可以消除此轴的反向间隙。通过对轴反向间隙的补偿,可以有效提高进给轴的精度,以保证插补运动的精度,有效改善圆度误差。
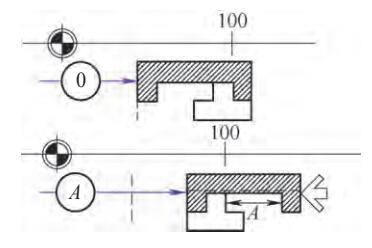
图2 反向间隙测量
2. 机床进给轴振动
数控机床加工时产生的振动,不仅会影响机床的动态精度,还会降低被加工零件的轮廓精度,增大表面粗糙度值,振动剧烈时甚至会影响刀具和机床的使用寿命。
(1)振动产生原因及对圆度误差的影响 数控机床进给系统产生振动主要有三方面原因:一是运动部件之间润滑不好,移动部件所受的摩擦阻力增大,容易造成进给轴的爬行和振动;二是给系统驱动装置到移动部件之间机械传动链的整体刚度不好;三是在闭环数控系统中,由于位置环、速度环及电流环增益设置过大及加速度等参数设定不合理而引起系统振荡。在数控机床应用过程中,造成振动的原因通常综合性的,应逐一排查。如图3所示,当机床进给轴振动时,刀具和工件会发生周期性的跳动,工件已加工表面会随机床振动出现频率相同的条纹,工件轮廓精度和表面粗糙度会受到影响。

图3 轴振动引起的圆度误差
(2)进给轴振动抑制的方法 在数控机床中,机电系统不匹配通常会引起机床轴的振动,动优化的目的就是让机电系统达到最佳的匹配,从而获得最优、最稳定的动态性能。如图4所示,机床轴的伺服驱动包含三个反馈回路,即位置环、速度环和电流环。当进给轴发生振动现象时,首先要检查机械系统是否据有良好的润滑,传动链是否具有足够的刚度;其次要根据机械维修情况对伺服电动机进一步优化,可通过调整位置环增益参数MD32200及速度环增益参数1407进行手动优化,直到伺服轴不
振,运动平稳。
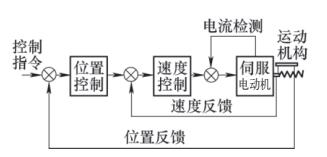
图4 伺服系统框图
3. 插补轴伺服增益不匹配
加工中心在运行一个圆的周期上,各轴运行的距离应完全相同。如果出现铣削加工的圆变成椭圆的情况,如图5所示,则说明两轴在插补运动过程中长轴超前于短轴。对于已使用过多年的机床而言,首先要检修机床插补轴的机械结构,传动装置是否松动,磨损是否严重,检查丝杠、轴承的预紧进行消隙调整,对反向间隙进行补偿,排除以上问题后需对两插补轴的增益进行重新调整,确保两插补轴的加速参数MD32300及位置环增益MD32200保持一致。 图5 增益不一致造成出现椭圆。
4. 反向跃冲
反向跃冲是指当机床某一个轴在做反方向运动时,轴从负的速度加速到正的速度时,该轴速度通过0的时候,摩擦力的状态由静摩擦力变为动摩擦力,所需的力比正常运动时要大,造成在换向处由于摩擦力的状态发生改变而出现短时的黏性停顿现象。
(1)反向跃冲误差对圆度误差的影响 在加工中心铣圆过程中,当轴在过象限时,轴的速度方向改变,轴从零速起动,摩擦力状态随之改变,必然存在反向跃冲。当两插补轴中一个轴已经达到最大值而另一个轴的速度却为0,这样将会有一个很短时间的停滞,从而产生轮廓误差。如图6所示,圆在过象限的地方有4个尖角,这就是由静态摩擦引起的反向跃冲误差。
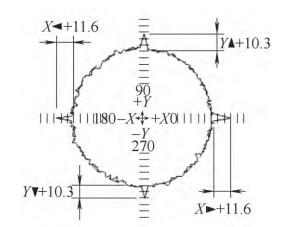
图6 反向跃冲误差造成的圆度误差
(2)反向跃冲的调整方法 反向跃冲存在的主因是摩擦力状态的改变,所以在出现反向跃冲时,应当给插补轴加上摩擦补偿,在西门子数控系统中,摩擦补偿是由摩擦补偿值MD32520和摩擦补偿时间常数MD32540决定的。对于反向跃冲的调整,首先设置MD32500=1(摩擦补偿有效),再调整跃冲轴对应的摩擦补偿值MD32520和摩擦补偿时间常数MD32540,两个参数值的大小调整对象限点影响可参考图7进行,直到过象限尖点被消除。需要注意的是设置的补偿值不宜过大,当MD32520>150mm/
min、MD32540>0.015s时,就应当首先检查机械传动是否良好,速度环增益及积分时间是否合理,过大的静摩擦补偿可能会对表面质量产生负面影响。
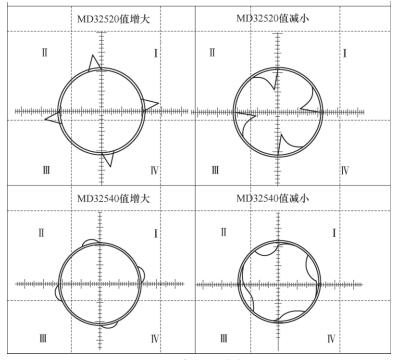
图7 摩擦补偿参考
5. 结语
数控机床是一个完整的有机整体,机械、电气及液压的控制存在相互联系和相互影响。因此,在分析解决圆度误差影响的因素时,应有整体概念和经验,进行多方面检测、分析和诊断,直至找出故障根源。
投稿箱:
如果您有机床行业、企业相关新闻稿件发表,或进行资讯合作,欢迎联系本网编辑部, 邮箱:skjcsc@vip.sina.com
如果您有机床行业、企业相关新闻稿件发表,或进行资讯合作,欢迎联系本网编辑部, 邮箱:skjcsc@vip.sina.com
更多相关信息