立式五轴数控机床机电优化方法研究
2021-5-28 来源:沈阳工业大学电气 沈阳菲迪亚数控机床 作者:郭志研 夏加宽 时光
摘要: 根据 VMC 立式五轴数控机床结构及其特点,从机械和电气方面对其进行优化。综合考虑工艺装备、装配工艺、电气控制、PLC 逻辑及先进的五轴精度检测方法,提出一套适用于立式五轴数控机床的机电优化方法。通过对比优化前后的性能,证明了其有效性。该研究对国产高端数控机床产品升级具有理论和现实意义。
关键词: 五轴数控机床; 工艺装备; 机电优化
0 前言
某集团 VMC 系列立式五轴数控机床,是面向航天等领域复杂曲面加工的新一代精密加工设备,该机床采用龙门式框架结构,直线轴为 x、y 和 z; 摇篮式旋转轴为 A、C,如图 1 所示。
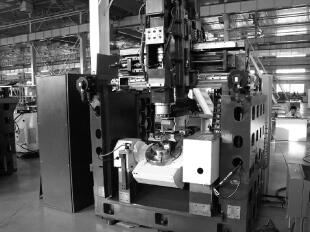
图 1 立式五轴数控机床
为进一步满足零件复杂曲面高效高精加工的技术要求,本文作者通过对现有 VMC 五轴数控机床进行机械、电气全方位优化,使该机床在动静态性能、加工精度和可靠性等方面达到或超过国际先进水平。
1 、机床现存问题概览
( 1) 机械装配方面。
目前,企业在制定装配工艺规范时主要依赖生产经验,装配精度一致性差,可靠性难以保证[1]。对该型号机床采用传统的机械装配工艺进行装配,难以满足五轴数控机床高精度、复杂曲面加工的性能要求。在装配阶段,影响整机产品可靠性的因素 很 多,各 因 素 件 又 具 有 复 杂 的 交 互 关系[2],主要反映在紧固件选型、公差控制等方面。
此外,在装配过程中,缺乏必要的工装检具,致使各项机械检测精度得不到保证且工作效率低。装配工作自由度较大、随意性较高,差异性的装配习惯很难保证产品的一致性,使得机械装配精度处于较低水平。
( 2) 电气控制方面。
机床电气柜布局不合理;内部走线凌乱、缺乏统一标准规划; 机床原始设计时对电磁干扰考虑较少,容易出现不可预期的电磁扰动; 气动、液动单元空间占用较大,不利于后期保养维护; PLC 控制逻辑冗繁混乱,导致机床外设操控性和安全性难以得到保障。
( 3) 五轴联动精度检测方面。
缺乏专业的五轴精度自动化检测手段和设备,现有的人工检测手段和方法比较落后,不适应批量生产。机床中应用的摇篮转台结构在外形尺寸、定位精度、刚性等方面性能不足,并且控制逻辑混乱,导致旋转轴与线性轴五轴联动精度较低、转台易出现错误报警。
2 、立式五轴数控机床机电优化工作
为解决上文中提到的问题,需要对机床进行全面的机电优化,优化工作主要分为 4 个部分: 优化前的对比试验、机械部分的优化、电气部分的优化和HMS 五轴精度测量系统的应用。
2. 1 优化前的对比试验
在机床进行全面机电优化前对其进行全面的精度检测,并与同类国际先进产品的精度允差值进行对比,得到如表 1 所示的数据。
表 1 优化前的精度检测 mm
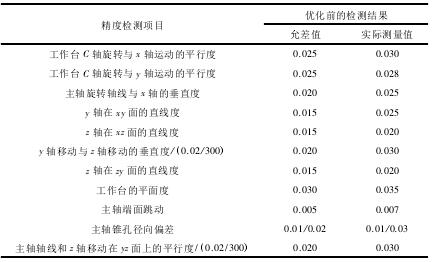
通过对比发现,在优化前的一些机床精度检测关键项目上,该机床距国际先进水平机床产品的精度允差值存在一定超差。机械精度和控制系统无直接关系,如果机械本身的精度不足,则任何先进检测和控制系统都很难发挥其应有的作用
[3]。
因此,判断该机床在机械的装配过程中存在一定缺陷,可以通过优化来进行机械精度的提升,以期在精度上达到或超越同类国际先进机床的水平。
2. 2 机械部分的优化
VMC 立式五轴数控机床机械部分的优化主要包括以下几个方面: 工艺装备的改进、装配工艺优化和高性能转台的应用及优化。
2. 2. 1 工艺装备的改进
原 VMC 机床装配过程中,适配的工装夹具较少,对机床装配、精度测量等方面有较大影响。因此,对现有工装夹具进行优化并提出新工装的制作方案和使用方法,新制作了丝杠表座、直线导轨弯板、z 向托板等十余种适配于此机床的新型工装,如图 2—4 所示; 改进了轴承孔检棒等现有工装,如图 5 所示。
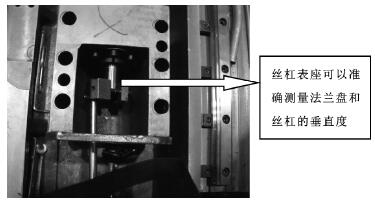
图 2 丝杠表座
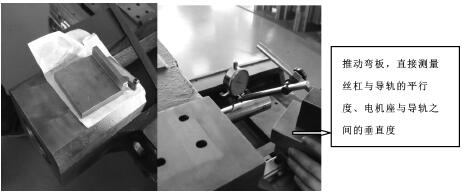
图 3 直线导轨弯板
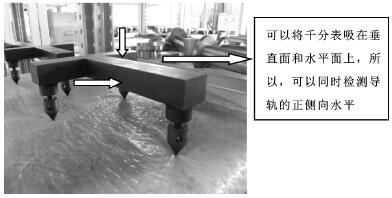
图 4 z 向托板
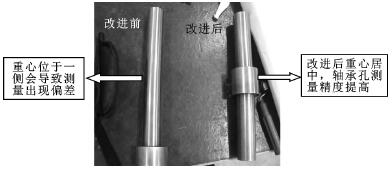
图 5 轴承孔检棒
2. 2. 2 机床装配工艺优化
装配工艺水平直接决定了数控机床的机械精度、刚性和稳定性。考虑到优化前装配中存在的各种问题,提出了如下优化方案:
( 1) 将电机座的底面磨薄,加装调整垫并以此为基准,确保电机与地面的平行度。
( 2) 固定直线导轨的螺栓,加装碟形垫片,以增加螺钉的刚性。
( 3) 测量立柱 ( y 轴) 两侧的正向、侧向、合向精度、合向扭曲,以提高测量精度。
( 4) 简化气动柜的结构。
将 A/C 轴的夹紧松开方式变为气动,减小液压站的负荷,从而使液压站的体积大大减小。
( 5) 对各伺服轴的导轨滑块加装调整垫,通过研磨调整垫来控制导轨的各项精度。
采用以上优化方案,机床的刚性、可靠性以及各项精度 得 到 提 升,优 化 后 的 精 度 检 测 结 果 如 表 2所示。
表 2 优化后的精度检测 mm
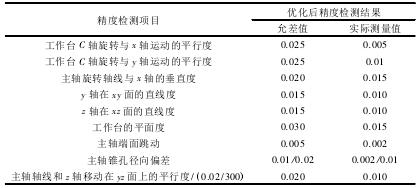
2. 2. 3 高性能转台的应用及优化
VMC 机床标配台湾旭阳转台,在刚性、控制精度和稳定性方面略有不足,且控制该转台的 PLC 逻辑不够合理,容易造成机床加工过程中出现过载、通信故障报警等问题。为了全面提高转台性能,选用意大利 LCM 高性能转台,如图 6 所示。
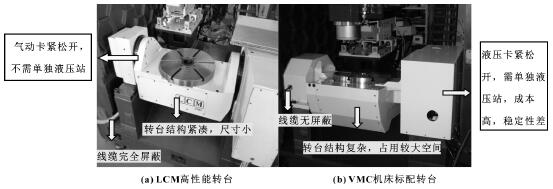
图 6 2 种转台的应用现场
图中左侧为LCM 高性能转台,右侧为 VMC 机床原标配的转台。LCM 转台具有刚性好、 响应快、 性能稳定等优点,并且在五轴加工领域被广泛应用。对控制转台动作的PLC 逻辑进行全面优化,优化前后对比如表 3 所示。
表 3 转台优化前后对比
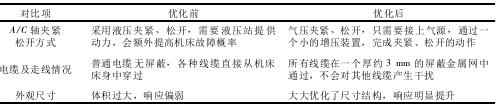
2. 3 电气部分的优化情况
VMC 机床电气部分的优化,主要包含以下几个方面: 电器柜的优化与设计、PLC 逻辑的优化以及HMS 测量系统在五轴精度检测中的应用。
2. 3. 1 电气柜的设计
重新对 VMC 机床的电气柜进行设计,新设计的电气柜如图 7 所示。
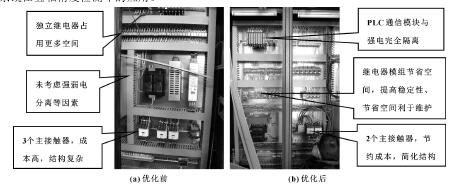
图 7 电器柜优化前后对比
主要进行了以下改进:
( 1) 强弱电分开,减小了电磁干扰。
( 2) 将电气图纸进行标准化处理,为保证机床未来进入欧美市场,将原有的中文图纸丰富为符合CE 标准的中英文对照图纸。
( 3) 优化电气柜结构,将控制星角转换的接触器由 3个减小为 2 个,节省了电气元件,节约了成本,简化了电路结构。
( 4) 将继电器组改为继电器模块,减小了占用空间,节约成本; 将电气柜内的元件全部换为符合CE 标准的零部件。
2. 3. 2 PLC 逻辑优化
通过优化完善 PLC 的逻辑,根据气动液压结构的改变,增加了更多的逻辑互锁保护,如表 4 所示。
表 4 PLC 逻辑优化前后对比

2. 3. 3 HMS 系统在五轴精度检测中的应用
HMS ( Head measure system) 是某公司开发的五轴精度自动检测工具[4],如图 8 所示。
相较于传统的手动五轴精度检 测 ( 千分表配合 球头 检棒人工测量) ,HMS 具有以下优点:
( 1) 手动五轴精度测量依靠人工控制,对操作员技术水平要求高; 而采用 HMS 系统测量五轴精度,是由系统控制来自动完成的,只需要对操作人员进行适当培训即可。
( 2) 手动测量准备、测量时间长,易产生随机误差,效率低; 采用 HMS 系统测量速度快,每测量完一项精度,系统自动纠正误差,可靠性高。
( 3) 手动测量只能寻找 A/C 轴旋转中心,不能对 A/C 轴进行旋转轴的螺距补偿。五轴机床做复杂曲面加工,需要对旋转轴的误差进行控制,HMS 系统可以对 A/C 轴进行旋转轴的螺距补偿。
( 4) 手动测量时,当转台旋转角度较大时,千分表的误差会加大,而 HMS 系统的 3 个空间传感器不会受到转台角度的影响,使其精度始终保持稳定。
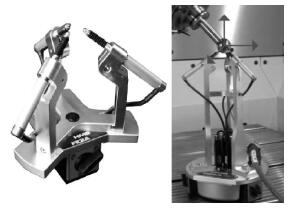
图 8 HMS 系统
3 、结束语
对现有 VMC 立式五轴数控机床进行机械、电气方面的优化,从装配工艺、电气控制以及零部件选配等方面改进机床的各项性能指标、提升制造水平、提高 VMC 立式五轴数控机床的市场竞力。同时,在工作中摸索总结出一套应用于五轴数控机床产品的机电优化方法,为企业高精尖产品的技术升级提供了指导。
投稿箱:
如果您有机床行业、企业相关新闻稿件发表,或进行资讯合作,欢迎联系本网编辑部, 邮箱:skjcsc@vip.sina.com
如果您有机床行业、企业相关新闻稿件发表,或进行资讯合作,欢迎联系本网编辑部, 邮箱:skjcsc@vip.sina.com
更多相关信息