主轴动态精度测试与分析
2020-2-28 来源: 大连理工大学 ,精密与特种加工实验室 作者:刘志松,刘阔,王永青,吴嘉锟,况康
摘要: 主轴动态误差对加工精度有至关重要的影响,针对主轴动态误差进行了试验与分析。介绍了主轴动态误差的概念,采用主轴动态误差分析仪对主轴动态误差进行了采集,采集的数据包括主轴径向平均误差、径向异步误差、轴向平均误差、轴向异步误差以及轴向最小间隙。对某型号同类型三台立式加工中心分别进行了多转速情况下的测量,对比并分析了三台立式加工中心的测量结果。在转速为 7 500 r/min 时,三台立式加工中心径向异步误差分别为 70、15、15 μm; 在转速升至 6 000 r / min 之后主轴最小径向间隙均有较大提升。试验结果表明: 主轴动态精度受到机床工况和转速共同影响; 在高速转动情况下,主轴径向最小间隙增大明显; 加工时要根据工况合理安排转速,以保证加工质量。
关键词: 主轴; 动态误差; 径向误差; 轴向误差
0 前言
主轴作为精密加工机床的核心部件,影响着机床加工精度。机床的工作性能和寿命都会受到主轴动态误差的影响。加工工件的圆度、表面粗糙度和平面度都与主轴有关。通过对主轴动态精度进行测试和分析,为进一步提高机床的加工精度,研发改良型号的机床提供数据支持和理论保障。因此,主轴的动态误差测试具有重要意义。
国内外很多学者对主轴动态误差进行了大量的研究。孙艳芬[1]介绍了主轴回转误差的概念及其基本形式,分析了它对加工精度的影响。王莹等人[2]对主轴系统动态误差和热漂移误差进行了测试与分析。朱永生等[3]对主轴动态回转误差进行了实验研究,测试分析了主轴回转误差受转速的影响。许颖等人[4]研究了主轴转速和温升对主轴动态误差的影响。刘阔等人[5]在不同的转速下对主轴的动态误差进行了测试,并对主轴动态误差随转速的变化进行了分析; 包丽等人[6]结合模态对加工中心主轴动态误差进行了研究。靳岚等人[7]同时在两个方向上对主轴的回转误差进行动态测试。
以上研究对于主轴动态误差研究有着很大实用价值,实验往往对单一机床在一种测试方法下对主轴进行动态测试,缺乏对比,没有考虑到安装、工况对主轴精度的影响,不能发现同一类型机床产品主轴动态精度变化的普遍规律。文中对同一批次、同一型号的 3 台立式加工中心,分别对主轴动态误差进行测试。主轴的动态误差测试主要包括径向动态误差、轴向动态误差、最小径向间隙。综合比对、分析 3 台机床数据异同,找出主轴动态误差较大的普遍原因,以提高主轴工作运行的平稳性和加工精度。
1 、主轴动态误差概念及其影响因素
主轴动态误差就是主轴在一定转速工作下的回转误差,机床主轴回转是机床最基本的成型运动,是决定工件圆度的主要因素之一。主轴回转精度可以定义为: 主轴回转线在回转时相对于其平均周线的变动量在误差敏感方向的最大位移[8]。它可以是径向跳动、轴向跳动或摆动,如图 1 所示。一般情况下 3 种误差同时存在,并相互叠加,影响主轴精度。
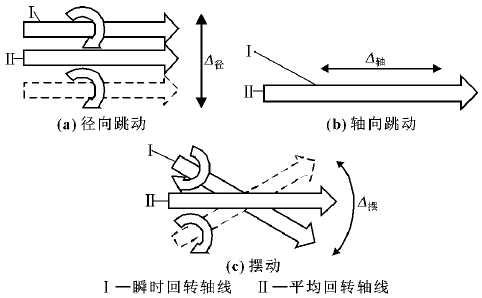
图 1 主轴回转误差
在测量轴向和径向误差时分别测量异步误差和平均误差。平均误差是总误差运动的平均轮廓线,主轴旋转的平均运动轨迹,与转速 “同步”,影响加工工件的圆度; 异步误差是总误差运动对于平均误差运动的偏离,是主轴旋转时随机变动的运动轨迹,影响加工工件表面的粗糙度[3]。
影响主轴回转误差的因素有很多种。机床的主轴是以其主轴颈的前后两个轴承相配合而回转的,因此影响回转精度的重要因素是主轴的精度、轴承的精度和床头箱主轴孔的精度。
2 、主轴动态误差测试
目前测试机床主轴误差的方法主要有静态测试法和动态测试法[9]。立式加工中心主轴最高转速为8 000 r/min,常用的千分表 ( 静态测试法) 测主轴回转误差已经不适用,并且它还无法分离出异步误差和同步误差。文中采用 API 主轴动态误差分析仪对主轴的动态误差进行测试。该测试系统包括电容式传感器、传感器安装架、信号采集器、数据采集及分析软件等。动态误差的采样速率为 256 000/s,可以满足高转速的动态误差采集。
主轴动态误差主要由同步误差和异步误差组成,两者分别影响机床加工件的圆度和表面粗糙度。文中采用的误差分析仪可以将两者区分,更准确地分析主轴动态误差以及其对应的原因。测试现场图如图 2 所示。控制机床转速在 50、100、300、500、750、1 000、1500、2 000、2 500、3 000、3 500、4 000、4 500、5 000、5 500、6 000、6 500、7 000、7 500、8 000 r / min 的情况下,分别测试主轴动态误差,每种转速下测试 3 次。
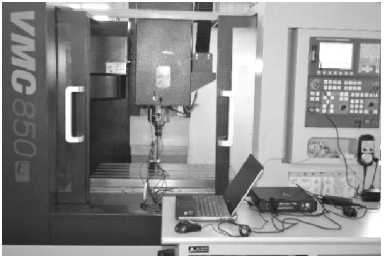
图 2 主轴动态误差测试现场图
3 台被测试的机床采用升速至测试转速→测试→升速至下一测试转速→测试的测试方法; 图 3 为测试方案下机床主轴转速在 300 r/min 时的测试结果。
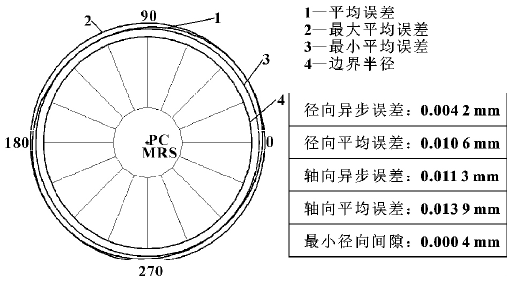
图 3 转速为 300 r/min 时的主轴动态误差
将测试方案中不同转速下,对 3 台立式加工中心的径向异步误差、径向平均误差和最小径向间隙进行统计,3次测量结果取平均值,其结果如图 4—6 所示。
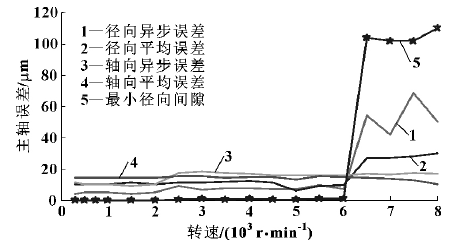
图 4 立式加工中心Ⅰ主轴动态误差测试
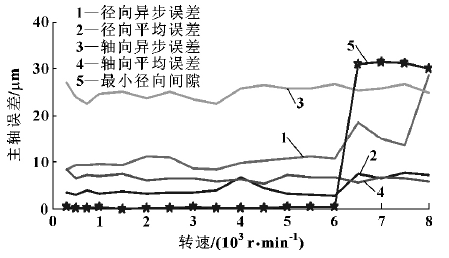
图 5 立式加工中心Ⅱ主轴动态误差测试
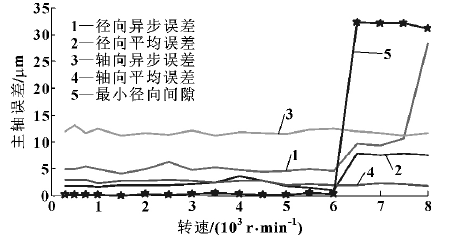
图 6 立式加工中心Ⅲ主轴动态误差测试
3 、数据处理与误差分析
为了方便对比 3 台机床主轴的误差情况,利用 MAT-LAB 绘图,将不同机床同一类型误差绘制在同一张图片中,对比 3 台机床主轴各项误差,分析其可能原因及影响,如图 7—11 所示。
图 7 3 台加工中心主轴径向异步误差比较
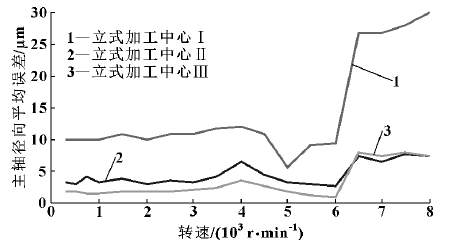
图 8 3 台加工中心主轴径向平均误差比较
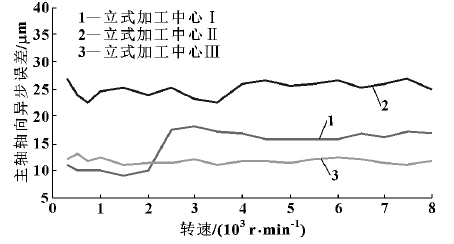
图 9 3 台加工中心主轴轴向异步误差比较
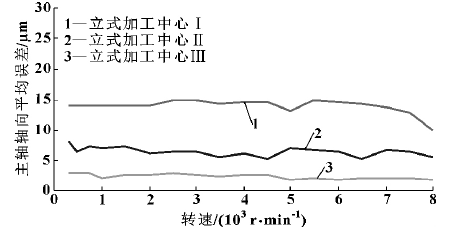
图 10 3 台加工中心主轴轴向平均误差比较
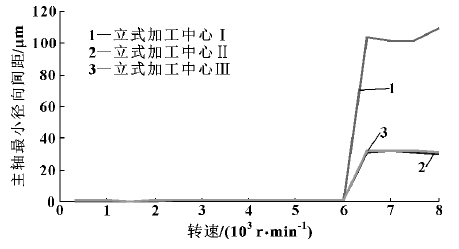
图 11 3 台加工中心主轴最小径向间隙误差比较
从以上图表中对比发现: 同一型号、批次的机床主轴误差存在较大差异。以转速 7 500 r/min 情况下的径向误差为例,立式加工中心Ⅰ的径向异步误差为 70 μm,而立式加工中心Ⅱ和立式加工中心Ⅲ的径向异步误差都在 15 μm 左右,相差了约 5 倍。
3 台立式加工中心的径向误差存在较大差异,不仅表现在个别转速下的误差区别,而且在总体变化趋势上也有不同之处。如转速为 6 000 r/min 之后,立式加工中心Ⅰ的径向误差有了较大的升高,而另外 2 台立式加工中心的径向异步误差提升并不明显。这说明,同一型号的机床由于安装、工况等因素的不同,径向精度会有较大区别,变化规律也不一样。良好的安装、工况可以提升主轴的径向精度,进而可以提高加工精度。
轴向精度方面,三者在不同转速下的误差以及变化趋势方面比较接近、一致,说明轴向的误差对于转速、安装、工况等影响因素不太敏感,精度保持相对稳定。当然 3 台机床也有总体表现出一致的趋势时,在转速升至 6 000 r/min 之前,主轴最小径向间隙表现一致;而在转速升至 6 000 r/min 之后,有着较大的提升。这有可能是转速提高带来温升使得主轴的轴承与主轴发生了膨胀,而两者热膨胀系数不一致,导致了间隙的增大。
4 、结束语
文中对多转速下主轴的动态误差进行了测试,测试了多台机床,并对 3 台立式加工中心测得的数据进行了详细对比。采用动态误差仪分别测试了加工中心主轴的径向平均误差、径向异步误差、轴向平均误差、轴向异步误差以及最小径向间隙,列出了测试的数据曲线。通过对多次测量数据平均值作图,对比分析了 3 台机床的误差异同。同种类型、型号的机床径向误差可能会有较大的差别,变化规律也不尽一致; 轴向误差三者接近。
并给出了可能的原因,机床在型号、批次一致的情况下,还要受到安装和工况的影响。另外转速升至 6 000 r/min之后,径向误差均有不同程度的增大。测量方案及结果对今后主轴动态误差测试、分析具有较强的参考价值。
投稿箱:
如果您有机床行业、企业相关新闻稿件发表,或进行资讯合作,欢迎联系本网编辑部, 邮箱:skjcsc@vip.sina.com
如果您有机床行业、企业相关新闻稿件发表,或进行资讯合作,欢迎联系本网编辑部, 邮箱:skjcsc@vip.sina.com