基于加工中心的线镗工艺研究与应用
2019-7-18 来源:一汽海马汽车有限公司 作者:周伙英 马小娟
摘 要:研究了基于柔性生产线加工中心的线镗技术,分析了曲轴孔从粗加工到精加工所用到的夹具、刀具,并根据实际加工情况,对发动机缸体曲轴孔的线镗的精加工不断进行研究和持续改进,收效显著,使加工质量和效率都得到了有效提升,从而解决了中、小批量多品种缸体加工的投资大、成本高的问题。
关键词:柔性制造技术;线镗;夹具;刀具;缸体
0 引 言
曲轴孔的作用主要是支撑曲轴,传递从曲轴柄传来的转矩并通过法兰输出,同时吸收活塞运动过程中产生的轴向和侧向力。
由于曲轴孔的加工质量对发动机的工作性能具有极其重大的影响,所以对发动机曲轴孔工艺的要求一般比较严格,包括直径、位置度、圆度、同轴度、各档曲轴孔中心的直线度及表面粗糙度。
为了满足这些要求苛刻的工艺指标,精加工一般采用专机线镗或铰珩两种加工方式。为了降低投资,实现三、四缸发动机的共线生产,海马某型号缸体曲轴孔精加工取消了铰珩,采用加工中心线镗加工工艺,实现机床内机械手自动调刀,质量得到可靠的保证。该曲轴孔整个加工工艺流程为:半圆孔粗加工→瓦盖合装后的两次半精加工→精加工,所有工序都在加工中心上完成。
1 、曲轴孔粗加工
1.1 曲轴孔粗加工夹具
曲轴孔粗加工夹具如图1所示,本工序选择缸体瓦盖结合面和缸孔来定位,以保证缸孔的加工余量均匀及缸孔与结合面的垂直度。工件进入夹具后,导轨下降,缸体瓦盖结合面落在定位支撑上,而后自定心结构下降到指定位置,通过四个缸孔定位,自定心结构定位后中心在同一直线上。
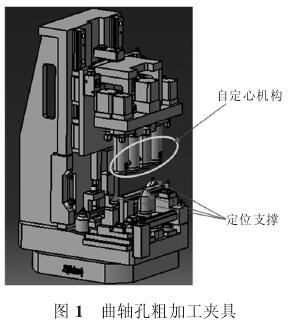
定位完成后,油缸开始动作并压紧缸体。若缸体定位气密检测通过,机床便开始运行加工程序;若气密检测报警,则需重定位夹紧。
1.2 曲轴孔粗加工刀具
曲轴孔粗镗刀如图2所示,刀片分为3组,每组3片,粗加工后曲轴孔留下单边0.85 mm的余量
。
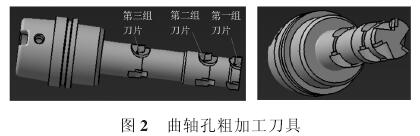
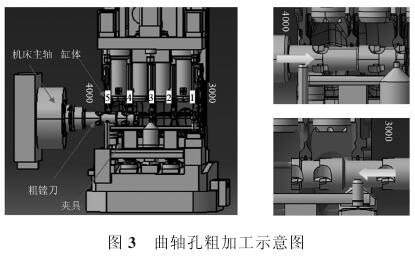
粗镗刀最初使用R0.4刀片,刀具寿命太短,而且加工后的曲轴孔粗糙度较高。经改进,换用
R0.8刀片,试用后粗糙度有明显改善,寿命也有很大提高。
1.3 曲轴孔粗加工
主轴夹紧刀具→刀具进入曲轴孔→镗刀与曲轴孔同轴→粗镗3、4、5档(第一组刀片镗第
3档、第二组镗第4档、第三组镗第5档)→刀具退出→具旋转180°→刀具进入曲轴孔→
镗刀与曲轴孔同轴→粗镗1、2档(第一组刀片镗第2档、第二组镗第1档)→刀具退出,加工过程如图3所示。
2 、曲轴孔线镗
2.1 采用加工中心设备线镗的可行性分析
在大批量生产中,用专机线镗曲轴孔是常见的加工工艺。用CNC替代专机,其难点有两个:
1)夹具设计较为复杂,工序内要实现工件的上升和再次夹紧动作;
2)此工艺是否能满足曲轴孔的表面粗糙度及孔位、孔径,孔的圆度、同轴度的过程能力CPK≥1.33或CP≥1.33的质量要求。
夹具的上升与下降可以通过PLC控制系统与油缸等机械部件实现,夹具设计要保证工件的定位精度。曲轴孔位的精度,由于缸孔未精加工,仅需考虑曲轴孔与设计基准的加工误差。影响因素为工件的定位误差、设备的定位与重复定位的误差,托盘的定位与重复定位误差。依据ISO标准,若机床主轴的定位精度为0.006,重复定位精度为0.003,托盘的定位为5",重复定位精度为2";导套的位置偏差控制在0.003的范围内,若工件的定位误≤0.02,经计算,长度400 mm的曲轴孔,在设备的精度范围内,理论上其位置度将在0.034的区间范围内(可信度≥99.74%)。
再考虑到实际加工刀具的受力情况及原点定位的系统偏差,则加工后工件的位置均值保证在
0.05的偏差范围内则可保证工序能力CPK≥1.33。曲轴孔的圆度与同轴度,则与主轴的远端跳动及整个系统的刚性有关。
因曲轴孔为双材质(轴承盖材质为粉末冶金,缸体材质为铸铁),其表面粗糙度与孔径的工序能力较难保证,对刀具的刚性和刀片的材质有较高的要求。经考证,刀具供应商有类似加工案例,可以作为借鉴。综上,采用CNC线镗技术在当前的技术条件下是可行的,可以进入实施阶段。
2.2 曲轴孔线镗夹具
曲轴孔精加工夹具如图4所示,该工序选择缸体底面及底面两销孔来定位。
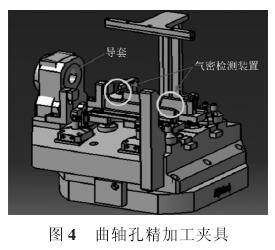
工件进入夹具后,支撑导轨动作,缸体下降到定位支撑处,圆销与菱销上升进入定位销孔,油缸开始动作并夹紧缸体,待缸体定位气密检测通过后,机床开始运行加工程序。
加工曲轴孔时,在镗刀进入曲轴孔前,夹具油缸动作,夹爪松开,支撑导轨动作,缸体上升2.38 mm,待上升气密检测通过后,镗刀偏心进入,镗刀定位后,缸体恢复至初始夹紧状态。加工结束后,之前动作重复一次,镗刀偏心退出。上升气密装置如图5所示,在实际加工中,该气孔容易进入铁屑,造成气密检测报警,影响缸体线正常生产。
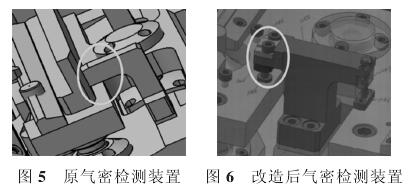
为了解决这个问题,临时措施是经常用水枪冲洗气孔面,后期对夹具进行改造,改造后的气密检测装置如图6所示。
该气密检测位于装置内部,铁屑无法进入,类似的报警问题将不会再出现。
导套是运用于发动机曲轴孔加工的一个精密机床部件。滚动导套的结构、精度、安装、调试、使用、维护及与之相配的直线镗杆的精度、直线镗杆与滚动导套的配合间隙等将直接影响所加工的曲轴孔的粗糙度、圆柱度、同轴度。
本夹具使用GATCO精密滚动导套,由静止外套、与镗杆一起旋转的淬硬并经过磨削的内套、精密轴承、密封件组成。
导套在夹具上的安装定位方式采用导套外径定位,与夹具定位孔的配合选用间隙配合,这样可以避免轴承外圈因温度升高而膨胀影响滚动导套回转精度和寿命,一般要求滚动导套外径与夹具定位孔的内径至少留有0.008 mm的间隙。
2.3 曲轴孔线镗刀具
2.3.1 线镗刀
曲轴孔线镗刀通过刀杆头部的导向键与导套实现固定联接,刀杆材质为重金属,在刀杆上分布着五组半精镗刀片和精镗刀片,如图7所示。
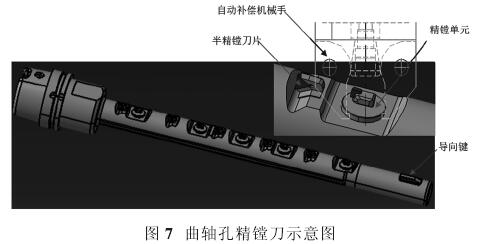
第二次半精镗留下单边0.05~0.06的余量。其中每个精镗单元都可以单独调整,调整精度在直径方向能达到0.002 mm,保证极好的孔径公差。
刀片磨损后在机床数控系统输入孔径数据,可通过自动补偿机械手调节精调单元,调整刀尖高度。自动补偿机械手卡爪上带有金刚石涂层,具有防滑效果。
2.3.1.1 自动补偿装置
在使用过程中,发现机械手调刀的准确性、可靠性不能满足要求。为验证机械手自动调整性能,我们做了调刀试验。
试验方案为:
1)试验前记录每档刀片高度;
2)通过机械手自动调刀机构将孔径调大或调小2~6 μm;
3)自动调刀后,测量并记录各档刀片高度(表1),看其是否变化及其变化量。
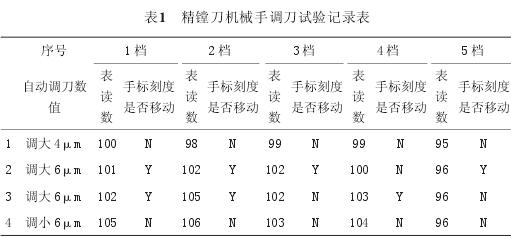
从表1可知,机械手自动调刀不成功率为65%。对精镗单元依据数据进行持续改进,经过多次验证,发现改进后的精镗单元通过机械手调整的数值比实际输入值小2μm, 按照此规律,目前已能用机械手自动调刀。
2.3.1.2 线镗的精镗刀片
线镗刀首次实验刀片为SPCE731 UK20, 是非涂层硬质合金刀片,在用各种组合参数试切削后,曲轴孔的表面粗糙度为Rz12~18 μm,达不到图样要求。
通过更改刀片材质 , 选用一款金属陶瓷刀片PCE731 VC610。此次变更刀片材质后,表面粗糙度上有较大的改善,能到达Rz8~10 μm,但孔径减小很快,刀片抗磨损能力较差。
再次改善,选用SPCE732 VC610和Ti Al N物理涂层的SPCE732 VC610两种方案。
试切削后,发现只是增大圆角方案SPEC732 VC610刀片的抗磨损能力没有明显增强,而加了涂层的刀片,虽在抗磨损方面有了很大的提升,但是粗糙度有所提高。而后又将涂层后的刀片做顶面抛光处理,使刀尖变得更圆滑,来降低加工粗糙度,结果还是不理想。
随后,我们对线镗刀的刀片材质进行了另外一种方案的验证,即更换现有的硬质合金刀片材料为CBN刀片材料,选用型号为SPHN050204-T01015。然后,进行了新刀片的验证工作,该刀片总共试验3次,第一次总加工件数为152件;第二次总加工件数为246件,平均加工29件调
一次刀;第三次总加工件数为250件,平均加工27件调一次刀。
本次试验来看,在粗糙度的控制方面CBN刀片明显优于硬质合金刀片,单刃均加工寿命能够突破210件,调刀频次也可满足生产要求。经过不断地摸索与改进,目前该刀片平均每刃加工件数可达260件。
2.3.2 曲轴孔线镗
主轴夹紧刀具→刀具进入曲轴孔→刀头进入导向套→夹具托盘下降→夹紧工件→镗刀与曲轴孔同轴→半精镗曲轴孔(五档同步)→精镗曲轴孔(拉镗顺序:5档→2档→3档→4档→1档)→夹具放松→工件上升→镗刀退出,加工过程如图8所示。
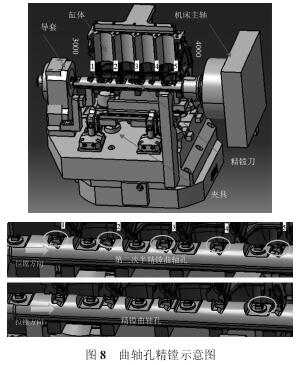
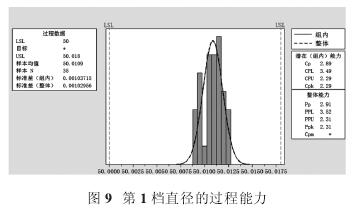
经过机床与刀具的多次实验调整,第1档与第2档的各项数据稳定,达到Cpk≥1.33的要求,如图9选取第1档的直径数据。但第3档的直径只达到Cpk=1.0。
针对该问题,我们将继续在刀片的材质、调刀的稳定性等方面做进一步的改善。此状态可以进入量产,但需加大工件的抽检频次,并对数据做持续的监控。
3 、结 语
本文研究并实践基于加工中心的线镗工艺,通过对线镗夹具的设计、刀具和刀片的改进,实现了多品种共线的生产模式,经实践验证,中、小批量生产质量较为稳定。鉴于缸体曲轴孔的重要性,在今后生产过程中还需对曲轴孔的粗、精加工进行紧密跟踪,通过不断摸索与改进,使其达到最佳状态。
投稿箱:
如果您有机床行业、企业相关新闻稿件发表,或进行资讯合作,欢迎联系本网编辑部, 邮箱:skjcsc@vip.sina.com
如果您有机床行业、企业相关新闻稿件发表,或进行资讯合作,欢迎联系本网编辑部, 邮箱:skjcsc@vip.sina.com
更多相关信息