双线梯形螺纹加工方案设计
2018-6-20 来源:广东广州市增城区职业技术学校 作者:杨华贵
摘要:在车床上加工梯形螺纹,有一定的技术难度,不能很好地保证螺纹的表面粗糙度,也达不到加工的要求。本文通过运用数控车床进行加工双线梯形螺纹,提出实用、安全、可行的加工方案,运用宏程序编程,解决在数控车床上加工梯形螺纹的技术难度,提高生产效率。
关键词:梯形螺纹,加工方案,分层切削,宏程序
0、 前言
在现在制造业中,梯形螺纹以其精确的传动得到广泛的应用。而在普通车床加工梯形螺纹的过程中,遇到较大的技术难关:因切削深度大,梯形螺纹刀受到螺纹参数的影响而使得刀头宽度较小,所以刀具刚性较差,寿命较短;与加工普通三角螺纹相比,其导程大、牙型高度高、切除余量大、切削抗力大、螺纹精度难控制等。因此,在数控车削双线梯形螺纹时,需精细的计算和优化的加工工艺,方能解决其精度和生产效率的问题。
1 、加工工艺
加工工艺是在加工过程中利用制造技术手段,是以完成零件加工为目的一种加工方案。其手段主要是在机床运作的情况下,运用夹具、刀具、量具及测量技术等合理随机的组合,去完成零件加工的一种过程。而这个过程就是加工工艺。在数控车床完成零件加工的过程,称之为数控车削加工工艺。数控车削加工工艺由一个或多个加工工序组成,其中包括机床的选择、零件图样的分析、程序的编写及对机床的巧妙操作等。
下面通过在数控车床上加工梯形螺纹的实例,为其设计出合理的加工方案,解决技术难题,提高精度与生产效率。车削的梯形螺纹工件如图 1 所示,材料为 45 号钢。
2、 设计加工方案
2.1 零件图样分析
数控车削加工的素材是工件,零件图样的完整性是加工方案制定的重要前提。在进行零件图样分析时,特别要重点关注以下几方面:
1) 分析尺寸标注。分析零件图尺寸的关键一步是标注是否齐全、标准与清楚。严谨的尺寸标注是数控加工工艺的制定的一个因素,影响着产品的质量与生产时间。图 1 所示的尺寸标注齐全、标准、直观,可满足数控车削编程的加工要求。
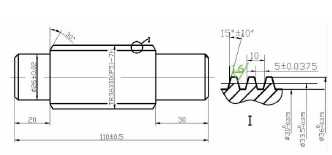
图 1 梯形螺纹工件图样
2) 分析公差、精度要求。公差要求是机械加工的重要部分,产品是否有效是由公差精度决定的。因此在使用数控机床加工零件时要考虑两个因素:一是考虑数控机床的精度是否达标,二是考虑如何优化加工工艺。两因素确保零件精度是否可以达到图样要求。
3) 分析工件结构。影响数控加工方案制定的设计制造 > Design & Manufacture36重要因素就是零件的结构,其复杂程度决定加工效率的高低。经过详细分析零件图样,确定理想的加工方案,明确每道加工工序及注意事项。例如根据零件的结构选择合适装夹工具,完成一个工序的加工。根据以上分析,我们选用了法拉克数控系统数控车床 FANUC 0i-TD,它可以满足零件精度要求。图样尺寸标注合理,满足数控编程加工要求;为防止加工螺纹时,工件往卡盘方向移动,我们采取两顶尖同夹加工的办法,即在三爪里面加放一自制顶尖,如图 2 所示。
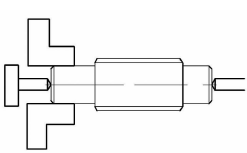
图 2 装夹图样
2.2 刀具选择
为提高加工效率,选择高速进行粗车加工。由于总的切削深度大,刀具尺寸又受到梯形螺纹几何尺寸的限制,所以在刀具选择的时候要注意选用车刀的材料和其角度,以保证螺纹车刀车削时与工件螺纹的牙形相吻合。车刀的角度一定满足粗、精的要求,特别是螺纹精车刀,其刀刃刃磨的准确性,刀具的耐磨性和车刀相对于工件理论安装位置的精确性,都会直接影响牙形轮廓,而产生误差。
1) 刀具角度参数确定。根据零件图纸中梯形螺纹的条件,运用螺旋角计算公式:

确定刀具的螺旋角 5.05°。因此左侧后角大于5.05°,就不会涉螺纹线,因此确定为 6~8°;右侧后角约为 2°,可提高刀具刚性。同时刀具前角取为 6~8°,一方面方便排屑,增加刀具寿命;另一方面增强刀具更加锋利程度又利于断屑 (如图3所示)。
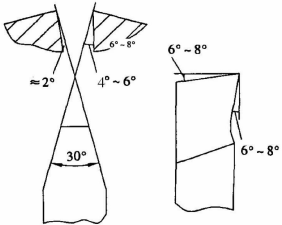
图 3 梯形螺纹刀角度参数
再根据梯形螺纹的尺寸标注,结合公式计算其相关参数如下 (单位均为 mm):
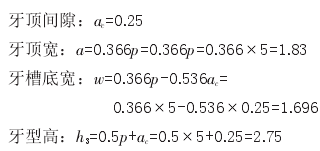
结合零件材料、刀具的几何角度及梯形螺纹的相关参数,我们选用超硬白钢刀,通过数控线切割加工刀具刀头宽约为 0.8 mm。
2.3 切削方式选择
目前,在车床上加工梯形螺纹用得比较多的方法主要有三种,分别是直进法、斜进法和分层左右切削法。
直进法加工梯形螺纹对刀具要求比较高,在加工时刀具刀刃三面参与切削,切削力大,排屑难,散热条件差,刀具寿命短,甚至还会扎刀,影响加工质量与生产效率。直进法一般适合导程较小的梯形螺纹加工。
斜进法虽然克服了直进法的缺点,但随着梯形螺纹牙高的增加,刀具的斜进刀量不断变小,精度难以控制,同时随着进刀深度的增加,左右赶刀亦趋于频繁,精度亦更难控制。
分层左右切削法拥有直进法和斜进法的优点,加工时减小了刀刃的切削力,增长刀具的寿命,左右加工进刀量易把控,精度得以保证,在加工大导程梯形螺纹时,选择分层左右切削法是一种较为理想的加工方式。
根据图样所示,优先选择分层左右切削法以确保大导程梯形螺纹的精度及生产效率。
2.4 数控程序编写
在一般的加工中,人们往往运用 G76 进行编写程序,因为 G76 一段简单的程序段就可以加工完成一个梯形螺纹,尽管其在加工过程中,刀具会斜进法走刀,但却无法完成螺纹的精度要求。为达精度要求及提高生产效率,运用宏程序进行编程虽然较G76 编程稍为复杂,但能解决技术难关,大大提高生产效率。加工梯形螺纹的宏程序如下:
T0303;(调用螺纹刀并进行刀具补偿)
#1=36:(螺纹直径赋值)
#2=5;(螺纹螺距赋值)
#3=10;(螺纹导程赋值)
#4=#3/#2;(螺纹线数计算)
#5=0.25;(螺纹顶隙赋值)
#6=2*#3;(升速进刀段距离计算)
#7=-70;(螺纹加工长度赋值)
#8=0;(X 方向加工深度变量赋初值)
#12=0.8;(螺纹刀头宽度赋值)
N10 #9= 0;(X 方向深度进刀次数)
N20 #10= 0.5;(Z 向每刀移动量赋值)
#11=0;(z 方向进刀量累计变量赋值)
#9=#9+1:(切深进刀累加计数)
IF[#2GT5]THEN [#14=1.5];
#8=#14*SQRT[#9];(每层切深计算)
IF[#8]GE[2*[0.5*#2+#5]] ;
THEN#8=[#2*[0.5*#2+#5]];(切深判别)
N30#13=0.634*#2-#8*[0.268*#2+0.536*#5]/[0.5*
#2+#5]-#12-0.2;(每层槽宽计算)
IF[#11GE#13]THEN[#11=#13];(判断本层槽宽)
G01 X[#1+5] Z[#6+#11]F350;(螺纹起刀点定位)
092 X[#l-#8] Z[#7]F[#3];
#11= #11+#10;
IF[#11LT[#13+#10]] GOTO 30;(本层槽宽加工完成条件转移)
IF[#8LT[2*[0.5*#2+#5]] GOTO 20;(总切深加工完成判别)
G01X[#1+5] Z[#6+0.1]F350;(精加工左牙侧刀具时刀具起点定位)
G92X[#1-#8] Z[#7]F[#3];(精加工左牙侧)
G01X[#1+5]Z[#6-#11-0.1] F350;(精加工右牙侧刀具时刀具起点定位)
G92X[#1- #8]Z[#7]F[#3];(精加工右牙侧)
#6=#6+#2;
IF[#4LT2]GOT0 10;
IF[#4EQ2]GOTO 40;
N40 GOO X100 Z100;
M30.
根据以上方案,在数控车床运用宏程序加工出来的梯形螺纹精度高,牙型角、梯形螺纹的大、中、小径都完全符合零件图样的尺寸要求,比简单运用数控车螺纹指令加工出来的梯形螺纹分线精度高,同时螺纹两侧的粗糙度也达到要求,加工效率可提高一倍。
3、 结束语
通过对双线梯形螺纹加工方案的设计,对图纸进行分析,选择了符合梯形螺纹精度的数控车床,确定了“两顶一夹”的装夹方式,防止加工工件被加工时向后移动的可能;选用了超硬白钢刀具,利用分层左右切削的优点来确保加工时的安全可靠;运用宏程序加工优化模块化,实现不同规格梯形螺纹的复杂粗加工和精加工,大大提高了加工梯形螺纹的加工速度,保证了梯形螺纹的精度,解决数控车切削梯形螺纹的技术难关。
投稿箱:
如果您有机床行业、企业相关新闻稿件发表,或进行资讯合作,欢迎联系本网编辑部, 邮箱:skjcsc@vip.sina.com
如果您有机床行业、企业相关新闻稿件发表,或进行资讯合作,欢迎联系本网编辑部, 邮箱:skjcsc@vip.sina.com
更多相关信息