冷冲模凹模大直径圆孔磨削加工技术
2017-6-16 来源:南京长江电子信息产业集团有限公司 作者:丁 伟
摘 要: 加工冷冲模凹模的大直径内孔时,因尺寸超过机床行程。普通坐标磨床无法完成加工,因此设计时对凹模相关结构进行调整,同时在保证产品精度的前提下,利用加工中心代替坐标磨完成相关尺寸的加工。
关键词: 加工中心; 磨削; 大直径凹模
冷冲模是冲裁电机定转子硅钢片的重要加工手段。
近年来,市场上越来越多大尺寸的电机芯片也开始要求冷冲模加工。按常识设计,与产品的尺寸相对应,模具的部分重要零件如凹模的尺寸偏大,超过了企业原有的一些机床的行程。同时,用户对产品外形的公差要求依然保持较高的要求。为保证零件的加工,需要在设计加工中进行创新。本文针对大直径定转子模具的凹模加工,通过对模具设计及加工手段进行创新,
充分挖掘企业原有机床的潜力。满足用户对产品的要求。
1 、冷冲模凹模原有设计及加工工艺
冷冲模是利用凸模、凹模的间隙配合,冲出产品的外形尺寸。冲裁直径小于 200 mm 电机定转子硅钢片的凹模通常采用整体设计。因凹模需要一定的硬度,一般是以硬质合金或硬度较高的工具钢为材料加工成一个圆环整体,镶嵌在凹模固定板或固定在下垫板上。内孔常用加工手段为铣削、车削、切割。因生产中凹模材质一般采用硬质合金,材料硬度大于 60HRC,硬度太高无法切削。同时,凹模对成形的尺寸精度及圆度要求达到 ± 0. 003 mm. 因此内孔加工一般分以下2 种情况。
( 1) 对于如导正钉孔或排气孔等 20 mm 以下的小直径圆孔,采用慢走丝 1 次粗切 3 精修的精加工方式将内孔成形在一台机床上一次加工到位。
( 2) 而对于冲裁 20 mm 以上圆孔及直径更大的定转子凹模孔,加工分两步完成。先采用 1 次切割加工圆孔留单面 0. 15 mm 余量,再由坐标磨磨削内孔修正成形尺寸。可以得到较高的尺寸精度、圆度及表面粗糙度。
原因是,慢走丝只有采用多次精修,所加工零件的尺寸及形位公差才能达到较高的精度要求。缺点在于,大直径圆孔采用 1 次粗切 3 精修加工,加工成本过高。而 1 次切割无法达到产品的精度要求。并且加工大尺寸成形时也受慢走丝行程限制,当加工的成形尺寸大于机床行程,则需移位加工。零件可能因多次定位,增加尺寸误差。并且慢走丝切割零件时,是通过放电气化加工区材料,因此零件表面会有一层硬化氧化层,表面粗糙度超过 Ra1. 6 μm,钳工修研工作量比较大。而采用磨削加工,则可以弥补上述缺点。
2 、新产品带来的问题分析
公司承接的产品外形为 590 mm,远超大部分机床的加工行程,公司行程最大的慢走丝 x 向行程为550 mm,y 向行程 350 mm,连内孔粗加工都无法一次切割完成。而坐标磨磨头行程也仅能完成最大 220mm 的内孔加工。这在给加工带来很大的难题。产品的外径大,则凹模内径随之增大。主要难点为以下 2 点:
( 1) 冷冲模冲孔时,凹模需要按产品尺寸放冲裁间隙。当产品直径为 590 mm 时,凹模内径自然也需要大于 590 mm,多数机床都无法满足产品的加工要求. 因以往加工的定转子产品很少有外径大于 200mm。采购机床时,考虑到经济性,企业多数机床的配置行程都在行程 300 mm 以内。坐标磨磨头行程仅为220 mm。
如为产品投资新设备,则将增加企业生产成本。加上大型电机产品的市场相对较小,因此新设备的利用率 不 高。非 常 不 经 济。如外协加工则周期不能保证。
( 2) 凹模直径越大,则加工中产生的变形量也随之加大。加工工艺必须要保证零件的尺寸及形位公差以满足要求。
3 、对模具结构进行科学设计并革新加工工艺
如前文所说,内孔直径较大的凹模成形加工分切割粗加工、磨削精加工两部分。
3. 1 对凹模成形粗加工的解决方案
针对凹模尺寸大,粗加工受慢走丝机床行程限制的问题。在设计时采用多个凹模拼块拼接成一个整体凹模。各拼块尺寸设计为小于慢走丝机床工作行程。粗加工时,各块独立加工,各拼块成形切割时留单面0. 2 mm 余量,并同时将销孔 1 次粗切 3 精修加工到位,便于装配时定位。最后,将凹模拼块在模座上进行固定,磨削内孔去除加工余量。
3. 2 对凹模内孔磨削的解决方案
磨削加工的优点在于凹模经过粗加工,应力已经得到释放,而磨削零件时加工区温度相对低,产生的应力变形很小,因此凹模形腔通过磨削可以得到较高的圆度,而且磨削后零件表面粗糙度好,可以减少甚至不需要进行后期抛光处理。因此精加工依然采用磨削。
由小凹模拼块组成大凹模,解决了粗加工时的机床限制。然而磨削仍然需要在组装成整体后加工。而单位现有的坐标磨床行程是无法满足要求的。而无论是大行程的坐标磨或立式内圆磨价格都比较高,临时采购也不现实。如果外协加工,外协费用太高,也会对模具成本带来不利的影响,并且周期难以保证。因此必须找出可行的代替方案。
坐标磨机床的磨削机构能完成三种运动: 砂轮的高速自转( 主运动) 、行星运动( 砂轮回转轴线的圆周运动) 及砂轮沿机床主轴轴线方向的直线往复运动。坐标磨磨削内孔就是利用砂轮在圆孔内进行轴向往复行星运动,对内孔进行加工( 如图 1) 。
前面提到坐标磨采用上下螺旋沿凹模形腔进行磨削。而这种加工方式,其实在加工中心上也有类似的模式。我厂的加工中心就可以做到螺旋下刀的走刀路径。并且加工中心的 X,Y 向加工行程可以达到2 000mm × 800 mm。行程上可以满足 590 mm 内圆的加工。因此需要将加工中心与坐标磨的一些基础数据进行对比、换算。通过对比性能数据,判定是否可以给加工中心设计专用刀柄安装上砂轮,并利用加工中心磨削凹模。
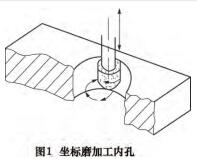
坐标磨主轴转速范围一般在 4 500 ~ 45 000r /min,砂轮直径一般为需要加工孔内径的 80% ~90% 。不过当内孔直径大于 50 mm,砂轮直径上限一般为 40 mm。
用坐标磨磨削硬度高的材料时,砂轮的线速度为25 m / s。而加工中心的主轴转速虽然没有坐标磨主轴转速高,然而最高也可达 10 000 r /min线速度的计算公式为:
V = πDN /1000V 为砂轮线速度,m / s; D 为砂轮外径,mm; N 为砂轮转速 r /min。通过计 算,可 以 得 知,当加工中心主轴转速为6 000 r /min 时,采用 80 mm 的砂轮可以得到相应的线速度。
最后,加工中心的加工精度也可以达到 ± 0. 003mm。能够满足产品的精度要求。因此,决定利用加工中心代替坐标磨完成内孔的磨削工作。
4 、创新方案的注意事项
加工中心代替坐标磨也需要注意到磨削时砂轮与工件摩擦会产生细微颗粒。如在加工过程中不加处理,一旦细微颗粒进入加工中心的运动部件,就会对加工中心运动部件产生磨损,降低加工中心的加工精度及寿命。因此在主轴上方固定一吸尘管,尽量收集细微颗粒,以减少对加工中心机床的不利影响。
加工中心也缺乏数控坐标磨机床对砂轮的磨损进行自动补偿的功能,因此加工中要注意多对砂轮及圆孔内径进行测量并及时在程序中进行补偿。
5 、改进后产生的效益
改进设计及工艺后,加工出的产品满足了产品的性能要求。利用上述设计及加工方式,将模具的加工难度控制在用厂内设备可以完成的水平,又可以保证产品的生产周期可控。为承接相应高附加值的模具走出了成功的路子,也为企业增加了新的利润增长点。从成本上说,仅需自制一套专用刀柄,避免了设备投资给企业增加固定资产负担。仅避免设备采置一项,就可以为企业减少几百万元的支出,如一台一般立式内圆磨需要 150 万元,一台进口数控坐标磨床需要 500万元。
6、 结语
大直径定转子模具因为尺寸大,对加工设备要求高,国内能设计生产相应模具厂家少,利润也比普通冲裁模利润大。通过对凹模结构的调整,并利用加工中心磨削内孔完成此类模具的生产,有利于提升国内模具的技术水平。为同类产品的生产研发打下良好的基础。
投稿箱:
如果您有机床行业、企业相关新闻稿件发表,或进行资讯合作,欢迎联系本网编辑部, 邮箱:skjcsc@vip.sina.com
如果您有机床行业、企业相关新闻稿件发表,或进行资讯合作,欢迎联系本网编辑部, 邮箱:skjcsc@vip.sina.com