浅谈薄壁零件的加工
2016-7-26 来源:航宇救生装备有限公司工装分公司 作者:崔健
摘要:文章以典型薄壁零件在三轴机床上的加工为例,探讨薄壁件在数控铣加工过程中存在的易变形、工件尺寸及表面粗糙度不易控制等技术问题,对加工难点要点进行分析,给出了工艺路线和加工方案,通过优化、完善夹具及装夹方法,优化加工参数,优化加工工艺从而有效解决薄壁件的加工精度和批量加工的尺寸稳定的难题,为其它同类薄壁零件的加工提供借鉴。
关键词:薄壁;装夹;工艺方法;加工参数;变形
1、概述
在数控加工中,薄壁零件因其自身具有重量轻,节约材料,结构紧凑等特点在航空航天、通讯、国防等各个领域产品中得到了越来越广泛的应用,而薄壁零件因其壁薄、刚性差、易变形加工困难也成了同时需要面对的棘手问题,由于薄壁零件自身的特点,在实际加工中不易达到设计的形位公差要求,其加工工艺较为繁复,编程、加工需要注意的细节较多,实际操作较为复杂。作者针对这类薄壁零件以曾经加工过的一批零件为例介绍薄壁件的加工方法、夹具使用、刀具选用、参数选择及编程要点等。此零件使用MasterCAM 9.1编程,在FANUC 系统三轴机床上加工完成。数控加工薄壁零件时,零件因刚度不足引起的加工变形成为影响尺寸精度的主要矛盾。为了提高零件尺寸的稳定性,对于薄壁零件的加工必须从工艺安排、夹具设计、设备选择、刀具选择、加工参数选择、程序编制等方面进行综合考虑,以解决零件在反复装夹后保证零件的加工精度的问题。下面通过具体实例来介绍薄壁件的加工。
2、实例零件加工
2.1 示例零件特点
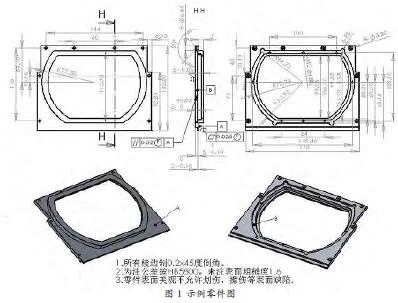
实例零件(如图1)为不久前加工的某型号产品光学系统的前镜头板,共45 件,材料为LY12 铝板,下料尺寸为185mm*130mm*15mm,转入本工序时已经经过粗加工及时效工序,粗加工后余量为单面1.5mm, 零件变形较大约为1mm -1.8mm。
从图1 中可以看出,零件形状并不复杂,多为平面、台阶,但零件外形尺寸较大,由于中部为D 形空腔,其有效截面积很小,并且截面面积变化较大不均匀。对于数控加工来说,此零件的尺寸公差较大,除注意选择合适的加工参数外,在编程上基本没有什么难度。加工最困难的是相对于A 基准的平面度0.025mm、平行度0.02mm。零件由多个台阶组成加工任何一面都有可能因为零件变形造成平面度超差,由于工件较薄,刚性较差,所有面都需要加工,工步多,一般情况下这样的零件仅控制平面度就比较困难,而此零件需要在多次装夹后来控制两面平行就更加困难。
2.2 加工工艺分析
通过对工件结构及其加工难点的分析,根据零件特点,制定加工工艺流程。此零件由于尺寸公差较大其加工难点主要的就是解决零件变形问题,而解决零件变形主要在于解决三点问题,第一解决零件应力释放问题,第二解决装夹问题,第三解决切削力问题。
2.2.1 零件应力的释放
一般情况下零件释放应力有两种途径,即时效和加工释放。时效包括自然时效和人工时效,而时效本身的特点决定了其不适于在精加工过程中进行,而且零件已经经过人工时效,所以在这里不讨论时效应力释放问题。
对于应力的加工释放其实就是通过不断的分层次加工使其应力得到重新分布并达到平衡进而控制变形。通过实验可以知道,对于易变形件的加工可以通过多次的均匀小余量切削使其变形逐渐减小直至达到加工要求。
因此加工分为三大步:粗加工、半精加工、精加工。
2.2.2 装夹问题
由于零件壁薄不易定位、装夹,很容易变形,如果采用通用夹具来装夹工件和切削加工,将难以控制零件的变形,很难达到技术要求,提高了装夹和加工难度。而由于零件毛坯的变形较大所以第一步只能使用通用夹具重新建立粗基准,建立基准后此零件多数工步将采用夹具装夹。由零件的特点可知其形状变形主要为平面弯曲、扭曲,对薄壁外周边影响较小,所以夹具将采用零件外周边定位方式,粗加工时零件压紧使用小压板轻压,半精加工时切削力相对较小视情况可使用小压板手拧轻压或在夹具底面加固体油脂使其产生粘滞力带紧零件,精加工时由于切削力极小可以不使用压板压紧,而使用夹具小配合间隙时产生的阻尼力夹紧零件。
2.2.3 切削力问题
由于高速加工的切削力小,对加工刚性较差零件减少了变形。高速加工的切削热小,零件不会由于温升导致翘曲或膨胀变形。高速加工的切削震动小,保证了较好的加工状态,降低了零件装夹压紧力,减小了变形。高速加工刀具与工件间的摩擦小,切削破坏层变薄,残余应力小,从而降低变形。所以切削时为防止切削力过大将采用高速小吃刀高速加工所以发热及磨损很小可以忽略,仅仅要注意冷却润滑方式以防止切削瘤的产生。所以解决切削力问题主要在于选择合适刀具及合理的切削参数。
2.2.3.1 刀具的选择。切削时为防止切削力过大讲采用高速小吃刀加工,所以需要采用耐磨比较好的刀具,且为了切削稳定使用四刃刀具,这里选用聚晶氮化硼涂层的30 度四刃整体硬质合金立铣刀。粗加工考虑切削效率及切削稳定选用直径6mm 立铣刀,半精加工时由于进刀量及切深减小为降低抗力及振动选用直径5mm 立铣刀,精加工时进一步降低切削力及考虑最小凹角问题选用直径4mm 立铣刀。(钻孔攻丝参数在此不做说明)
2.2.3.2 切削参数的选择。切削参数的合理选用,对切削过程的稳定性,刀具的耐用度等有很重要的作用。为了减低切削力在机床允许的情况下将使用高速切削,高速切削最大的优势并不在于速度、进给速度的提高所导致的效率提高,而是由于采用了更高的切削速度和进给速度,允许采用较小的切削用量进行加工。由于切削用量的降低切削力和切削热随之下降,工艺系统变形减小,可以避免铣削颤振。由机械制造原理可知任何的刀具刃口都不可能做成绝对的尖部,都存在刃口圆弧,在切削时由于圆弧的存在其切削力分为几个方向,如图2 所示。

图2 切削分力
由图2 中可以看出,当刀具切削时由于刃口圆弧的存在切削力将有三个分力,当切深h 远大于刃口圆弧半径R 时,C 向力大于B向力,刀具将会将零件抬离夹具,而当切深h 小于等于刃口圆弧半径R 时,C 向力小于B 向力,刀具将会将零件压紧夹具。据此在零件精加工及修光时一般选择的切深等于刃口圆弧半径此时切削最稳定,震动最小,切削力最小。由于有刀具的压紧力所以精加工及修光时可以不压紧零件仅靠夹具的摩擦力加工,要注意的仅仅是防止零件底面不贴合夹具引起震动。
根据刀具厂商提供的参数范围选用较高速度,具体参数如表1。
表1 铣刀切削参数
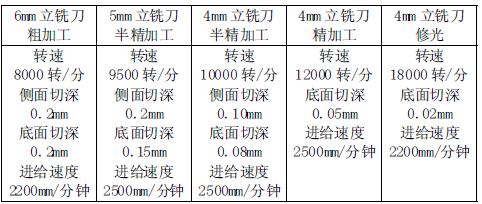
转速及进给可根据实际切削情况用倍率旋钮调整。侧面切深指使用侧齿切削时的轴向切削深度,底面切深指使用底齿切削时的轴向切削深度,一般情况下侧齿的切削宽度不大于刀具直径的十五分之一一般取直径的二十分之一,底齿切削宽度不大于直径的四分之三一般取直径的三分之二到直径的一半。
2.2.3.3 冷却润滑。由于零件为铝件且刀具采用高速小吃刀加工所以发热及磨损很小,所以仅需要注意防止积削瘤的产生。积屑瘤延伸到刃外,使得实际切削厚度增大,影响尺寸准确性。积屑瘤周期性增大脱落,可随切屑排出或残留在已加工面形成鳞片状毛刺增大已加工表面粗糙度。积屑瘤未脱落时,起保护刀刃和减小前刀面磨损的作用,脱落时可能粘连刀具材料一起剥落而加快刀具失效影响刀具耐用度。在粗加工和半精加工时可采用油气雾冷却润滑,以避免积削瘤的产生。精加工时由于切削量很小,且为了夹具清理方便可以单用汽冷。注意气压避免压力过大将零件吹动,调整至吹走切削即可。
2.2.4 确定加工工艺
在解决零件变形主要三点问题,零件应力释放、装夹、切削力之后确定加工工艺流程。如表2 所示。
表2零件加工流程
(零件已加工完成期间经过的实验工艺调整过程简略)
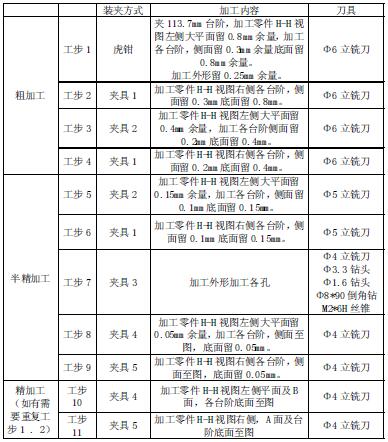
2.3 零件的加工
下面工艺流程详细说明加工及编程:加工分为三大步:粗加工、半精加工、精加工。整个加工步骤除孔加工外每两个工步为一组,分别加工零件两面。
2.3.1 粗加工
粗加工分为四个工步。第一工步使用机用精密平口钳夹持H-H视图右侧台阶面,以零件A 面定位于钳口,并在工作台加装辅助定位器,夹紧力要小,轻夹。第二工步由于外形基准及平面基准已经创建完毕,为防止虎钳装夹变形大则使用夹具装夹(如图4:夹具一),夹具侧面多数空开小面积定位以免零件变形不好放入,由于零件有变形底面不能很好贴合,所以夹具使用小压板轻压,加工期间需换压一次。第一第二工步由于零件变形,其粗基准不好,所以本工步主要是为了重建基准,只要大部分面见光,加工完成后平面变形不大于0.5mm 即可。路径编程尽量使用外形铣削注意进退刀,使用直径6mm 铣刀。
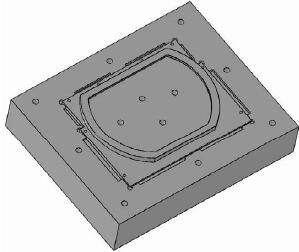
图3 夹具一(零件安装在夹具上)
第三,第四工步进一步提高零件平面度及两面平行度,使其不大于0.2mm。其中第三步使用夹具二,如图4:夹具二。路径编程尽量使用外形铣削注意进退刀,使用直径6mm 铣刀。
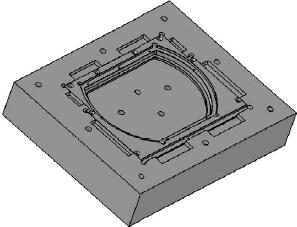
图4 夹具二(零件安装在夹具上)
2.3.2 半精加工
半精加工分为五个工步。第五第六工步进一步提高零件平面度及两面平行度,使其不大于0.1mm。由于需要进一步降低切削力所以选用5mm 立铣刀加工。路径编程尽量使用外形铣削注意进退刀,使用直径5mm 铣刀。
第七工步为重建精确外形基准,且由于平面变形已经较小,且外形较薄变形对外形尺寸的影响也变小所以在这里外形尺寸133.5mm*170mm 至图。为降低振动使用4mm 立铣刀,使用夹具三(如图5:夹具三),夹具使用A 面及113.7mm 处台阶定位精加工外形至图,同时将孔加工完成。
路径编程尽量使用外形铣削注意进退刀,使用直径4mm 铣刀。(钻孔攻丝参数在此不做说明)
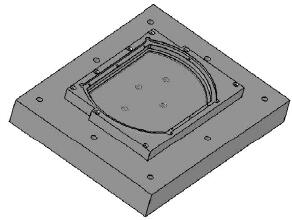
图5 夹具三(零件安装在夹具上)
第八第九工步进一步提高零件平面度及两面平行度,使其必须小于0.05mm。由于需要进一步降低切削力所以选用4mm 立铣刀加工。且由于平面变形已经较小,变形对型腔尺寸的影响也变小所以在这两步所有侧面尺寸至图。并且由于零件外形已经精加工,所以改用夹具四、夹具五(如图6:夹具四、图7:夹具五),并且此时压紧力要非常轻。路径编程尽量使用外形铣削注意进退刀,使用直径4mm 铣刀。

图6 夹具四(零件安装在夹具上)
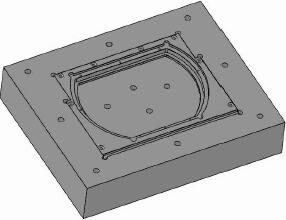
图7 夹具五(零件安装在夹具上)
2.3.3 精加工
精加工分为两个工步。第十、第十一工步进一步提高零件平面度及两面平行度,使其不大于0.02mm 达到图纸要求,且深度尺寸尽量偏上差为部分零件返修留余量,并且要添加最后纹路修光步骤。精加工仍使用夹具四和夹具五,夹具使用时不再使用压板压紧,而是采用夹具阻力夹紧,情况不好可以使用油脂垫底,冷却为空冷,不再加注油雾以免切削不稳定。更换零件时家具一定要清理干净。
编程路径使用外形铣削注意进退刀,使用直径4mm 铣刀,最后一层0.02mm 修光时编程不使用进退刀采用直接下刀改善表面纹路。两工步完成后检测零件平面、平行度,如有超差重复精加工工步即可。
2.4 加工时注意事项
(1)随时注意零件的切削状态、刀具使用状态、气流压力及零件震动情况及时调整参数或更换刀具。(2)根据切削表面粗糙度变化调整油雾浓度。(3)装夹时一定要注意力量不能过大。(4)清理夹具一定要仔细,不能有残留细切削。(5)安全生产,佩戴防护用具。
3、结束语
通过以上方法加工后的零件达到图纸要求。这些加工方法都是从实践中获得,在现在的加工中得到了应用,利用这些方法可以有效地解决这类薄壁零件在加工中遇到的问题,这些方法只是解决方法的一部分,其他更有效的方法还有待总结和发现。
参考文献
[1]武凯.航空薄壁件加工变形分析与控制[D].南京航空航天大学,2002.
[2]何永强.薄壁件数控铣削加工切削力及变形误差分析[D].西安工业大学,2008.
投稿箱:
如果您有机床行业、企业相关新闻稿件发表,或进行资讯合作,欢迎联系本网编辑部, 邮箱:skjcsc@vip.sina.com
如果您有机床行业、企业相关新闻稿件发表,或进行资讯合作,欢迎联系本网编辑部, 邮箱:skjcsc@vip.sina.com