数控机床进给系统进给精度误差分析及优化
2015-12-7 来源:数控机床市场网 作者:中捷机床有限公司,洪寿福 轩广进 张洋
摘要:数控机床为缩短机械加工时间,进给速度及加速度的不断提高,对加工工件的精密性更加加强,对其进给系统传动精度要求更加严格,直线光栅尺闭环控制传动链结构,对优化进给精度误差简单可靠。
关键词:定位误差 进给系统 光栅尺 丝杠 支撑方式
在不断增长的竞争压力下,对现代化数控机床的生产效率和加工精度的要求也不断提高,同时机床的稳定性(各轴进给误差)和使用寿命也相应变得越来越重要。这些变化直接导致了对机床进给控制检测要求的提高。机床总误差中进给系统的定位误差为举足轻重。目前数控机床加工零件加工精度要求高时,本身机械装配已无法满足要求机床各进给轴。必须通过直线光栅尺直接反馈进给系统运动误差闭环控制进而通过数控系统精细补偿满足前述高加工精度要求。
1 进给传动系统的结构
数控机床设计多种多样,但进给系统结构大多相同。滚珠丝杠被用于实现伺服电机旋转运动到滑板的直线运动的转换。丝杠两端支撑座内部的轴承承受进给运动及加工的切削轴向分力。伺服电机通过联轴器与丝杠联接。而进给运动的位置值是通过直线光栅尺或电机编码器加载到丝杠旋转运动上的。单纯使用编码器对滚珠丝杠进行位置控制时腔制环检测到的数据是电机转子角度位置并非机床滑板的直线运动位置。为了从电机转子的角度位置精确推算出滑板的直线位置,驱动电机与滑板间一切传动系统的性能必须 已知重复性必须高。而直线光栅尺控制包含了整个进给系统。进给系统的机械传动误差由光栅尺测量通过数控系统进行补偿减少进给运动定位误差。
1.1 运动误差
直接采用旋转编码器十丝杠系统带来的是丝杠螺距误差。进给系统的间隙及螺距损失。由于滚珠丝杠的螺距用来直线测量的标准珠丝杠的螺距误差直接影响测量结果。进给系统内部间隙会导致1到10 μm左右背隙出现。丝杠运动一定时间后可达到伸长平衡状态。这个过程中会导致丝杠定位产生非线性误差。
误差补偿
数控系统由螺距补偿和背隙补偿。补偿值需通过激光干涉仪等检测测量。
进给系统的受力变形
在使用滚珠丝杠和编码器来进行测量时,滑板加速移动产生的惯性力、切削力、导轨内的摩擦力等机构变形力导致滑板轴向有位置偏移。经验值,直径40mm 滚珠丝杠,平均轴向偏移100/200N/μm之间。
惯性力
机床滑板的移动加速度越来越高移动惯性力对进给系统的变形也越来越大。
切削力
机床的切削力很容易达到几千牛不仅作用于进给系统还作用于工件几刀具上。而光栅尺补偿小部分的变形。所以一般在进行工件精加工时应用较小的进给力进行加工。
摩擦力
根据导轨形式不同摩擦力仅滚动导轨垂直方向力的滑动导轨垂直方向力的口左右。另外进给系统中最大的摩擦力产生于丝杠螺母。原因是丝杠螺母在进给运动中进行复杂的滚动及滑动相结合运动。
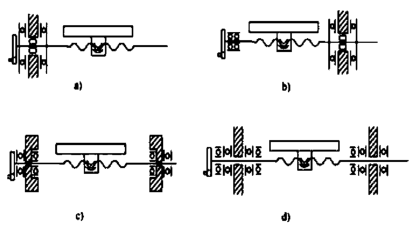
1.2 进给系统误差来源
丝杠发热产生定位误差
在采用编码器进行位置控制时由于滚珠丝杠发热而导致定位误差是最大的误差来源。
原因是,厂方面在将电机的旋转运动转为线性运动时丝杠要有高刚性,另一方面丝杠起长度标尺作用。这种双重功能使得机床设计时必须满足这两方面要求。而丝杠的刚性取决于丝杠的两端固定预紧。
滚珠丝杠支撑轴承对定位精度影响
如图a 丝杠单边固定安装时,丝杠可以按温度变化由紧固端出发自由伸长。通常用于短丝杠和垂直进给丝杠,承载能力小轴向刚度低。
如图b 丝杠单边固定安装,一端浮动时,丝杠可以按温度变化由紧固端出发有微量轴向浮动,通常用于丝杠较长情况。
如图c 丝杠两端固定安装,并对丝杠施加预紧力时,丝杠的轴向刚性大大提高但对热变形较为敏感。
如图d 由丝杠两端双重支撑固定安装,并对丝杠施加预紧力时,使丝杠有较大的刚度,还可以把丝杠热变形释放到推力轴承预紧中。所以必须考虑推力轴承的承载能力。
2 结论
机床进给系统因滚珠丝杠两端支撑轴承及丝杠螺母发热,在采用半闭环控制时会导致极大的定位误差。通过丝杠和旋转编码器定位的半闭环控制最大问题是滚珠丝杠的热身长。这类伸长过程常见时间常数为12小时,按加工程序的不同会产生 0.1mm 数量级的误差。而这类误差在数控机床整体误差中占主导地位。
综上述分析,为了减少进给误差满足机床精度及速度要求有必要采用直线光栅尺进行闭环控制。
投稿箱:
如果您有机床行业、企业相关新闻稿件发表,或进行资讯合作,欢迎联系本网编辑部, 邮箱:skjcsc@vip.sina.com
如果您有机床行业、企业相关新闻稿件发表,或进行资讯合作,欢迎联系本网编辑部, 邮箱:skjcsc@vip.sina.com
更多相关信息