车铣复合加工工艺设计中的关键问题研究
2014-3-2 来源:北京航空航天大学 作者:史旭升 乔立红 胡权威
随着计算机技术、机床技术以及加工工艺技术的不断发展,传统的用单一加工方法分工序加工已不能满足人们对加工速度、效率和精度的要求。在这样的背景下,车铣复合加工技术应运而生。车铣复合加工的理念是“一次装夹,全部完工”,这种加工模式无需人工干预,在一次装夹定位情况下,机床可以进行车、铣、钻、镗和车铣等加工任务[1]。车铣复合加工技术作为一种高效率、高精度,且适应现代制造业多品种、小批量、个性化发展需求的先进数控加工技术,日益受到重视[2]。车铣复合加工为复杂零件、高精密零件和难加工零件提供了先进的解决方案,解决了传统加工中心难以解决的加工难题 。
车铣复合加工设备的主要优势在于加工工艺更加灵活、工序更加集中,从而可以缩短产品制造工艺链、提高工艺的有效性、减少零件在整个加工过程中的装夹次数、提高位置加工精度。但在实际应用中,却面临很多困难和挑战。主要原因是在车铣复合加工工艺过程设计中,面向车铣复合加工的加工方法决策技术、加工工步排序技术和干涉碰撞检测技术尚处于探索阶段,因此,车铣复合加工设计工艺水平低下成为制约加工设备应用的主要障碍。
随着车铣复合加工设备的广泛应用,研究符合车铣复合加工的先进工艺设计方法,充分挖掘设备的应用潜能,成为企业的迫切需求。为了解决该问题,本文通过分析面向车铣复合加工工艺设计中的加工方法决策、加工工步排序和碰撞检测3个关键问题的研究现状,探讨了相应问题的解决方法。
车铣复合加工方法决策技术
加工方法决策是影响工艺设计方案准确与否的关键环节,是实现工艺设计智能化的核心问题。加工方法决策的原理是根据产品制造特征信息和加工知识信息给出满足加工精度要求的加工方法。在现代计算机辅助工艺设计技术中,工艺推理的特征信息和加工方法知识信息一般分别用产品特征数据库和加工方法知识库来进行存储。由于传统工艺设计在构建特征数据库和加工知识库过程中都缺乏对同步加工相关知识的描述和表达,在推理决策过程中无法得到满足车铣复合加工的加工方法决策信息,因此研究符合车铣复合加工的加工方法决策技术具有重要意义。
目前,面向车铣复合加工方法的决策技术还处于起步阶段,但是传统加工工艺和五轴加工工艺的决策技术发展已经成熟。车铣复合加工方法与传统加工方法的单元都是加工操作方法,所以车铣复合加工方法可以分享传统加工方法的特征和知识信息;同时车铣复合加工方法具有同步加工的特性,这就要求对传统加工方法进行再组织和协调。北京航空航天大学课题组致力于先进制造工艺领域的研究,建立了较完善的特征数据库和加工知识库[5-7]。本研究在此基础上,继承其特征建模技术和构建知识库的方法,通过分析和总结现有车铣复合加工方法特点,构建面向车铣复合加工的特征数据库和加工方法知识库。通过基于特征与知识推理机制决策加工方法,解决现有工艺设计系统在车铣复合加工方法决策过程中知识乏力的问题,拓宽工艺设计系统的应用范畴。
车铣复合加工的突出特点是同步加工技术的应用,同步加工是指采用多刀架同时切削,这样能够减小加工时间,提高生产效率。以双主轴双刀架车铣复合机床为例,同步加工主要分为双刀架同时加工同一个工件的同一个特征、双刀架同时加工同一个工件的两个特征和双刀架同时加工两个不同的工件这3种类型。特征类型与加工方法之间是一对多的关系,如车削外圆可以采用双刀架同时加工一个特征,也可以采用双刀架同时加工车削外圆与钻轴向孔两个特征。因此,需要分析同步加工相关属性信息,在特征数据库和工艺知识库中进行准确表达和清晰描述。
特征数据库是描述产品特征信息的载体,包含了产品特征类型,及特征对应的几何信息和非几何信息。其中,几何信息是指特征包含的几何形面;非几何信息是标注在几何形面上的尺寸、粗糙度、形位公差、注释等信息。在构建特征数据库时以特征为单元,能够完整表达产品的设计信息,有助于实现产品设计与工艺过程设计之间的信息传递,支持工艺过程设计。
加工方法知识库是对加工方法适用范围的形式化表达,包含加工方法及其所适应的工件材料、几何形状及经济加工精度的定义。知识库除了描述加工方法信息以外,还要反映加工方法与产品制造信息的对应关系,以便根据加工方法知识匹配适合产品设计要求的加工方法,从而为加工方法决策提供理论支持。
加工方法决策是根据产品的特征信息和加工知识进行推理,决策出满足产品精度要求的加工方法。车铣复合加工方法决策流程如图1所示,主要步骤如下:

特征信息提取:根据零件的几何模型,获取零件包含的技术要求和特征信息,以及特征对应的几何信息和非几何信息。
特征信息预处理:按照加工方法知识模型所要求的格式对特征信息进行预处理。如产品特征信息中的精度上下限需要转换为精度等级的形式,便于在加工方法决策中进行匹配。
加工方法决策:从加工方法知识库中获取加工方法知识,将知识库中给定的属性值与特征数据进行比较,与几何特征、材料、精度及热处理等信息进行匹配,得出符合条件的可行加工方法,选择最优的加工方法作为决策结果。
车铣复合加工工步排序技术
在车铣复合加工设备上加工复杂零件时,零件在一次装夹下的工步数目多、排序规模大,单靠经验难以得到较好的排序方案。工步排序不仅影响工艺方案的优劣,还会影响加工设备的使用率和产品的加工质量。为了充分发挥车铣复合机床的加工能力,在加工条件允许的前提下,通过双刀架的同步操作实现零件多个工步同时加工。但为实现这样的同步加工,就需要分析车铣复合加工同步工步之间的优先关系,合理安排工步之间的串行和并行加工顺序。
传统工步排序一般是线性工步排序,不存在同步加工问题,采用改进的智能算法可以有效地解决工步排序问题[8-9]。车铣复合工步排序是同时涉及资源调度和工步排序的复杂问题,资源调度是指车铣复合加工设备包含的主轴和刀架的分配,因此在排序过程中不仅要考虑同步工步的组合关系,还有分配合理的主轴和刀架。Nan-Chieh Chiu等[10]针对多主轴多刀架加工中心的工序排序问题,采用了改进的遗传算法,但是在工艺排序过程中却没有考虑车削工艺与钻削工艺的同步加工方式;Dae-Hyuk C等[11]以产品的加工时间为优选目标,采用枚举法列举了车铣复合加工的所有可行加工方案,但该方法仅适用于工步少的零件,否则计算量将呈指数形式增加。
随着智能优化算法在计算机领域的应用,利用人工智能技术进行工艺排序的研究,对提高工艺排序的自动化和智能化水平,都起到了积极的推动作用。图2给出了一种建立在工步有向图基础上的解决车铣复合加工工步排序方法示意,该方法结合零等待微资源分配算法,可实现同步工步与主轴和刀架的动态组合。
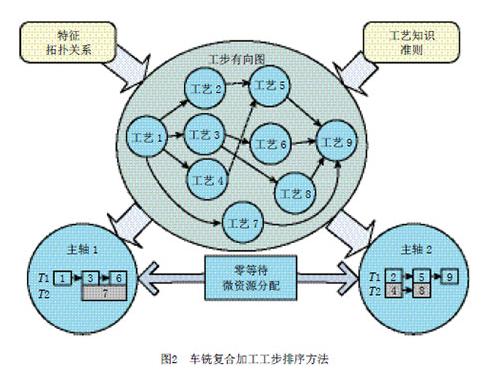
工步有向图的基本原理是根据产品特征之间的拓扑关系和工艺知识准则,以有向图的形式表达工步之间的优先关系。工步有向图以最简洁的效果,形式化地表达了工步之间的优先关系。图2工步有向图的箭头从优先加工工步指向后加工工步,如工步1优先于工步3加工。为了在有向图中准确地表示工步之间的关系,引入逻辑与和逻辑或的关系,其中实线表示逻辑与的关系如工步9必须在工步5、6、7、8加工之后加工;点划线表示逻辑或的关系如工步5在工步2或者工步4之后加工。
零等待微资源分配是指合理选择车铣复合加工的同步工步,及时分配相应的主轴和刀架,使所有的工步都尽量在第一时间得到响应。在分配过程中,力求提高主轴和刀架的使用效率,减小刀架等待时间。其中刀架和主轴的使用遵循以下规则:一个主轴在一段时间内最多只能安装一个工件;一个刀架在一段时间内最多只能加工一个工步;不同的刀架可以同时加工不同的工步。
同步加工是两个没有约束关系的工步,在加工设备主轴和刀架允许的情况下,采用的一种高效加工方式。同步加工策略主要有同步车外圆、同步车端面、同步车外圆和钻孔、同步铣削和同步径向钻孔等理论可行方案。在实例化工步排序过程中,应该使同步工步之间的加工时间差最小,减少刀架的等待时间。
车铣复合工艺设计中的碰撞检测技术
在车铣复合加工过程中,由于车铣复合加工设备结构复杂、运动部件多、空间小,刀具与刀具,刀具与刀架之间极易发生碰撞现象。车铣复合工艺设计中的碰撞检测是验证工艺方案的可行性,检测同步加工工步、刀轨路径和加工参数正确与否的一种重要手段,因此,研究碰撞检测技术显得尤为重要。
随着计算机技术的发展,虚拟仿真技术在减低成本,提高效率方面都有显著优势。碰撞检测算法主要有空间分解法和层次包围盒法两种算法,其核心思想都是尽可能减少相交测试对象的数目来提高检测速度。空间分解法适用于稀疏的环境中分布比较均匀的几何对象间的检测,层次包围盒方法则应用更为广泛,适应复杂环境中的碰撞检测[12]。车铣复合加工环境复杂,运动对象多,因此,在本研究中选用了基于层次包围盒的方法。
传统检测方法是进行一次或多次试切、不断调试,直到确认能够完成预定的加工要求,这种方法效率低、周期长、成本高。为了提高检测效率,基于虚拟仿真技术的碰撞检测算法[13-15]为工艺方案的修正提供了依据,但是在修正过程中需要工艺人员根据经验预估修正方式,由预估引起的不确定性和偶然性,给生产计划带来一定风险,如果不能及时解决,可能影响生产进度。为了避免盲目的方案预估,减少反复修正的次数,提高准确率,保证精度,准确计算发生初始碰撞时间和位置信息可有效解决该问题。图3给出了以初始碰撞时间和位置为检测目标,采用改进OBB包围盒碰撞检测算法对车铣复合工艺方案中可能存在的碰撞进行检测的流程。
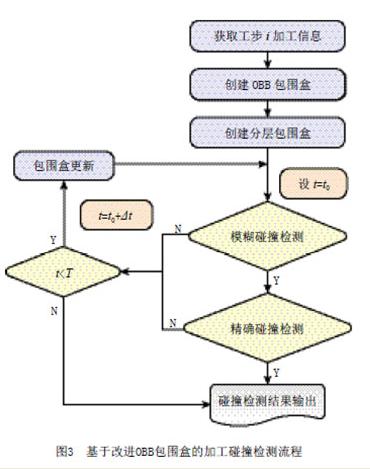
车铣复合加工是一个动态过程,在该方法中,将时间参数作为一个自变量,把工步分为若干时间节点,求解每个时间节点的碰撞情况,简化了碰撞检测算法的难度。算法以车铣复合加工工步为单元,根据工步包含的几何对象创建各对象的OBB包围盒及其层次包围盒树;基于分离轴理论的模糊检测,快速剔除不发生碰撞的对象,减少运算对象,提高检测效率;基于矢量法的精确检测和三角面片相交算法,计算发生初始碰撞的时间和位置。
在模糊检测阶段,当不发生碰撞时,计算下一时间节点的碰撞情况;当发生碰撞时,进入精确检测阶段。在精确检测阶段,当不发生碰撞时,返回模糊检测阶段,计算下一时间节点的碰撞情况;当发生碰撞现象时,输出检测结果。直到遍历完该工步的所有时间节点,完成碰撞检测过程。该计算结果能帮助工艺设计人员更快地进行工艺方案或运动参数的修正,提高了修正效率。该算法适用于车铣复合加工所有的加工类型,即常规加工工步和同步加工工步。
结束语
车铣复合加工工艺设计是目前工艺设计领域研究的热点,也是难点之一。本文在分析车铣复合加工工艺特点的基础上,研究了车铣复合加工工艺设计中的加工方法决策、加工工步排序和干涉碰撞检测3个关键问题。根据车铣复合加工中的“同步加工”特点,提出了解决上述问题的方法:包括建立面向车铣复合加工的加工方法决策机制;应用同步加工策略,采用工步有向图和零等待微资源分配的方法;将基于OBB包围盒的碰撞检测算法用于快速检测车铣复合加工中的碰撞。这些方法可以验证工艺设计方案的可行性和准确性,解决车铣复合加工工步排序问题,提高工步排序的效率和水平。
投稿箱:
如果您有机床行业、企业相关新闻稿件发表,或进行资讯合作,欢迎联系本网编辑部, 邮箱:skjcsc@vip.sina.com
如果您有机床行业、企业相关新闻稿件发表,或进行资讯合作,欢迎联系本网编辑部, 邮箱:skjcsc@vip.sina.com