浅谈基于 PLC 的刀库自动换刀控制系统设计
2024-5-11 来源:- 作者:蒋继红 朱洪亮 等
摘要:本文主要以圆盘刀库的机械手自动换刀控制器为主要工作目标,通过采用可编程控制器,完成了对圆盘刀库的旋转选刀、刀套翻转送刀和机械手旋转换刀程序等的自动控制。本文还着重介绍了刀具库中刀具手动转换控制器的基本构造、工作原理、硬件构成、软件设计等。通过全新的换刀更换体系,可使其换刀效率大为提高,进而获得较好的企业效益。经实践运用证明,这种方式具有系统全面、见效快、使用广泛的优点,各部门都可进行需要的操作,能充分满足加工中心的需要。
关键词:PCL;刀库;自动换刀;控制系统
据统计,在入世贸组织的 20 年间,我国向海外输送了近 60 万台带有自动换刀功能的 CNC 机床,对拉动 GDP 增长和制造业发展发挥了巨大作用。自动换刀刀库与机械制造业密不可分,随着科学技术的发展,以高品质、高效率的机械装置逐渐取代了常规的机床,自动化生产装备的技术水平也在不断地提升,这给机械制造业带来了很大的挑战与机会。
目前,由于数控加工中心的刀库刀具种类比较多,它可以实现比较复杂的工件,所以它的应用范围也变得越来越广。不过,实际生产活动中,刀库选刀时存在的问题也是十分广泛的,问题的存在也给设备质量带来了极大的困扰,希望可以给设备的保养与维护一些理论依据。本研究重点是根据江苏德速智能工具公司的 ADKY 圆盘系列 (BT40) 刀库,开发了一个可以精确选定刀具部位,并在该刀库上实现速度转换的圆盘刀库的控制器。
1、刀库自动换刀机械系统的基本原理
自动换刀装置是一种以ATC 电机,双爪机械手、气缸、活塞杆、定位刀套、刀盘等为主要部件的装置。其工作原理为接受指令,电机驱动,选择下一次要加工的刀具,并在机械手的控制下,将刀具送至心轴。刀库具有自动更换刀具和存储刀具的功能,可根据需要对刀具进行加工,如铣、钻、切丝、攻丝等。这样可以缩短工作时间,节约开支。刀库与换刀机器人要共存,没有刀库,就不能提前备好所需的刀具,没有换刀机器人,就不能进行换刀。
刀具库房中的刀具自动更换控制系统,实现了刀具的移动,刀套的翻转,机械臂的更换。刀库中刀具自动更换的基本工作流程如下:数控系统接收刀具更换命令,用马达将刀具库正向和反向选择指定刀具号码,圆筒推进刀杯 90°竖直向下,同一时间,将主轴提升到刀具更换的参照点,并对锭子进行定位。此时,机械臂将进行换刀,该换刀动作如下:(1)机械手旋转夹持库刀和主轴刀;(2)从主轴刀柄上抽出 180mm 的刀具库刀柄; (3)操作臂 180°的转动;(4)机器人抬起 180mm 的高度,把刀柄和心轴一起放进刀具库里;(5)机械手对齐。
2、PLC 控制系统要求
在制造过程中,对一个零件进行加工时,常常不是一次就能完成,而是要经过多次的加工才能完成。而无论是普通的还是普通的机床,哪怕是只有一种功能的数控机床,也只能完成一种工艺。在整个加工过程中,花费的时间最多的就是更换刀具,但是,现在自动化水平越来越高,手工更换刀具已经严重地影响了生产的效率,因此,在加工中,自动更换刀具系统的作用是非常重要的。本设计就是为这种情况而设计的,其具体要求如下。
(1)通过自动切换系统的指令,可程控器自动选取最接近的切换路径,使刀具库自动旋转。(2)待要用的刀片移至机器人拿刀处时,刀库停止旋转,自动比对当前刀片的编号和位置,若对,则选择的刀片翻过来,机器人就可以随时更换刀片;如果是错的,那么机器就会自动停下来。(3)通过程控系统的指令,驱动自动切换马达,使机械臂进行切换。(4)当机械臂运动至取刀位时,停止动作,程序控制系统收到指令后,自动切换马达停止,机械臂取回刀具。(5)机械臂取出刀具后,由程控装置再一次发出指令,机械臂继续旋转,旋转至设定位置后,机械臂停止旋转。(6)当机械臂旋转至心轴时,程控器收到指令,自动切换马达停止,机械臂插入刀具。(7)机械臂进行刀具的切换动作,完成了主轴刀具的切换。
当可程控器发出指令时,机械手就会动作,当动作到达设定的位置时,可程控器就会收到讯号,让自动切换马达停止,机械手就会停留在起始位置,从而完成切换。
3、硬件电路设计
3.1 电源电路
图 1 显示了控制系统的供电线路,电源为 AC 380 伏,AC 380 伏到 AC220 伏的变换要求用一台绝缘变压器,再经过电闸,设计用来预防电击,并且增强了抗干扰性。这个系统是用一个程序控制装置来控制的,它的输入和输出电路都是 DC24V,并选用 AC220V/DC24V 的直流电压调节器,该稳压器为 S-150-24V。电源指示灯会发出警告信号,当灯会亮时,表示目前已接通。
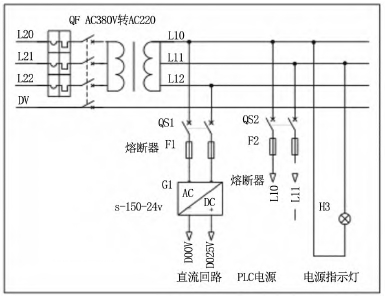
图 1 电源接线图
3.2 控制系统的电路设计
为了方便绘制 PLC 接线图和编写 PLC 程序,将每个输入 / 输出设备与 PLC 的输入 / 输出点相对应。
3.2.1 PLC 的 IO 接线
在这个设计里,首先设计了已有的 PLC 的输入点和输出点,接下来,按照目前的项目流程需求,为目前的设备设置了特定的 PLC 连接线,在程序设计中,这样就可以更清楚地看到当前设备的输入点和输出点。
3.2.2 电机接线
三相电机运转时,装置的工作部件,必须使用三相电源,而且还会出问题,此时,若在装置的进电线上加装一组防风开关,那么在电动机发生故障的时候,而不会影响其他部件的工作,对现有设备马达进行保护。三相电源通过交流保护空气开关的上端进入后,把它的下端头和 AC 接触器的上端头连接起来,当 220V 的电力供应完毕后。电动机在 PLC 的控制下运转,在接触器绕组通电和常开度连接处,电动机就能正常运转。
4、控制系统的程序设计
4.1 程序主流程图
按照设计要求,本文给出了该控制系统的主要程序流程图,如图 2 所示。
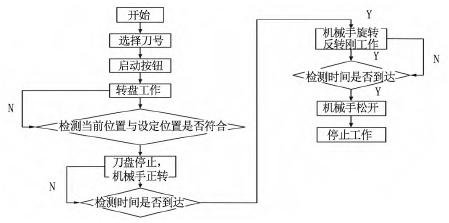
图 2 程序主流程图
4.2 控制系统程序设计
4.2.1 选择刀号传送程序
如图 3 中所示,如果输入继电器 X4 被打开,则此时,它将目前的位置 2 传递给数据寄存器地址 D100,以执行随后的目前的程序比较。
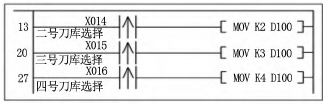
图 3 位置传送块程序
4.2.2 当前刀号位置传送程序
如图 4 所示,在程序在向网络 72 自动执行时,程序会自动判断输入继电器 X14 的状态,如果接受了这个任务,PLC 将常数 2 自动转移到了目前的数据寄存器 D102 上,在同一时间内,输入继电器 X15 被激活,此时,数据寄存器常数 3 也被转移到了数据寄存器 D102 中。
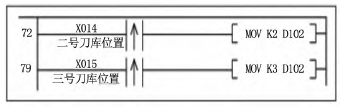
图 4 刀库位置传送程序
4.2.3 电机正反转判断程序
在程序开始的时候,要判断所选刀具编号 D100 和当前刀具编号 D102 的尺寸,当 D100 大于 D102 时,M10表示,把它打开,并计算其差异,然后把它放到 D300的数据寄存器里,再次判定 D300 中的数据是否大于 4,要是电机的话,然后执行一个逆向的操作,当 D102 大于 D100 时,M12 表示,在各种情况下,这将会产生非常不同的结果,结合刀库中的刀具选择,根据当前刀与目标刀的最短距离计算,来选择刀具库的正反两面旋转,实现了快速选择刀具的目标。
4.2.4 机械手气缸工作程序
在副继电器 M1 的作用下,刀罩及机器人竖直圆柱形电磁阀启动,从而实现刀罩的翻转及机器人的竖直运动。当两个人都走到了正确的位置,按下了极限开关,机器人就会从刀库里拿出一把刀来。4s 后,机器人开始夹紧 2s,然后开始反向,放松 2s,等待主轴取刀,然后正转回起始位置,刀套和机器人返回原位。
4.2.5 故障指示灯
如图 9 所示,M1 开启,意味着选择的刀号与目标刀号重合,刀片止动,在准备更换刀具的时候,当刀套翻转以及机械臂液压缸的推杆在 10s 内没有触碰到极限开关时,这时,故障显示灯亮起,提示员工机器出现故障。
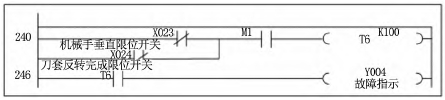
图 5 故障指示灯
4.3 程序设计
转刀装置的基础工作是转刀。刀鞘的倒扣,就是用来抓刀的。刀套翻转的过程是:在 PLC 的控制下,通过电磁阀的开关,带动气缸中的活塞旋转,因为活塞杆连接到机器手臂的构造刀套上,这样,活塞的移动就能使刀片翻过来。在汽缸上安装了两个固定开关,用来检测汽缸中活塞的位置。由此判断刀鞘有没有被彻底翻转过来。PLC 根据定位切换信号决定是否进行切换动作。根据这一步,结合系统的控制流程,编制了控制系统的梯形图。
5、结语
本文基于可编程控制器,设计了一种基于可编程控制器的刀库自动换刀控制系统,详细阐述了该系统的工作原理,并进行了硬件电路的设计、可编程控制器的编程、组态软件的设计与调试以及组态仿真软件的运行调试,实现了快速高效的换刀,大大提高了 CNC 加工的效率。下面是从功能测试中得出的结论:
(1)优化了刀库房自动化更换的控制逻辑,使刀具的选择和位置更加准确,缩短更换时间,在运行中避免了一些低级的失误;(2)本实用新型具有很好的适应性,尤其适用于多道工序,需要不断地更换刀具的复杂工件,可减少因多次更换而引起的误差,从而提高了加工精度;(3)该系统具有操作简便、造价低廉、易于维护、组态接口好、工作稳定性好、抗干扰性强等优点。
作者:蒋继红 1,殷红梅 1,刘晓宇 1,朱洪亮 2
来源:1. 江苏电子信息职业学院 ;2. 涟水思麦柯动力机械有限公司 )
投稿箱:
如果您有机床行业、企业相关新闻稿件发表,或进行资讯合作,欢迎联系本网编辑部, 邮箱:skjcsc@vip.sina.com
如果您有机床行业、企业相关新闻稿件发表,或进行资讯合作,欢迎联系本网编辑部, 邮箱:skjcsc@vip.sina.com