圆盘类零件的专用铣床夹具设计
2022-7-25 来源:长安大学 作者:魏金
摘要:随着科学技术的飞速发展,我国机械加工行业发展迅猛,加工效率和质量均得到大幅度提高。同时,机械加工也逐渐趋于自动化和数字化,如数控机床的出现解决了人力短缺、效率低等问题。但数字化加工的出现对夹具提出了更高的要求,对于现有圆盘类零件的铣床夹具安装和拆卸复杂,严重影响工作效率。因此,笔者通过分析此类零件的加工工艺,明确零件的加工部位的技术要求,从夹紧装置、辅助装置、定位装置、夹具体结构设计等方面对该类零件的专用铣床夹具进行了设计。结果表明,设计了加工圆盘类零件的专用铣床夹具,具有结构简单、操作安全方便、夹紧效率高等优点,可满足大批量生产的需求。
关键词:铣床;铣削加工;夹具设计
0 、引言
随着我国机械加工技术的不断成熟,对于机床夹具的要求也越来越高。夹具在减少生产成本的同时,能大幅度提高工作效率;同一个夹具可以尽可能多地装夹不同规格和形状的零件;应用场合多,可以应用在各种现代化制造加工的场合以及对零件加工精度要求较高的场合;进一步提高夹具的标准化程度;以液压、气压作为夹紧装置的源动力,节省人力成本。夹具的发展大致可以分为三个阶段:第一阶段,夹具在各种零件的加工中仅仅被视为最基本的部分,只满足被加工零件夹紧的要求;第二阶段,由于被加工零件的精度要求越来越高,与被加工零件紧密接触的夹具的精度和刚度要求逐渐提高;第三阶段,数字化加工时代的到来,各种夹具的自动化和适应性得到进一步提升。
如今,机械加工已经向着数字化的方向迈进,比如,各种数控机床的出现,它在一定程度上可以实现无人加工,这极大地降低了人工成本且提高了生产效率。圆盘类零件在农用机械中是一种常用的零件,笔者设计了加工圆盘类零件的专用铣床夹具,以满足大批量生产的需求。
1、零件的工艺路线分析
被加工零件的零件图如图 1 所示,该零件材料选用的是 20Cr。这类零件虽然结构简单,但是加工精度要求较高,可大批量生产。此加工过程采用数控加工工艺,不仅能大幅度提高零件精度,还能提高整体加工效率。根据现有的机加工方法,对本零件进行工艺分析。加工工艺路线如表1所示。
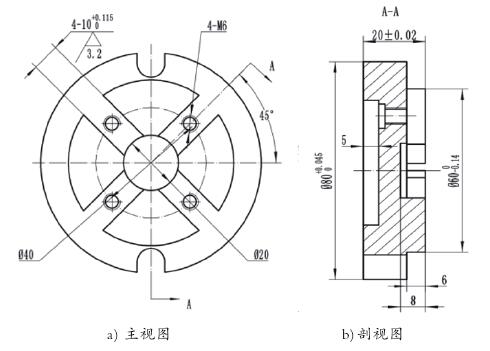
图1 零件图
表1 圆盘类零件加工工艺路线
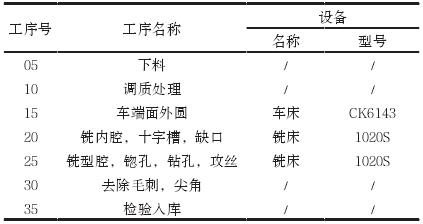
2 、数控铣床加工内容
2.1 圆盘类零件的原始材料分析
根据设计任务的要求,需要设计加工此零件有十字槽的一面,用铣床加工,包括铣内腔、十字槽、缺口、铣型腔、锪孔、钻孔、攻丝。所以对夹具和刀具的定位要求比较高。另外,本零件生产需求量较大,所以,需要严格控制成本且要提高生产效率。
2.2 主要加工工序及参数选择
该零件的下表面为铣床加工,主要工序及参数如下:
1)铣40×40,深5的型腔。根据零件的技术要求,切削深度取5 mm;查阅《数控加工工艺与编程》,得知铣削的最佳速度为 55 m/min~120 m/min,这里取90 m/min;
2)锪4-ø9深2的孔。根据加工的实际情况,锪孔的切削深度取 2 mm;铣削速度取 100 m/min;由转速公式n=1 000 Vc/πd,计算得主轴转速n=2 000 r/min;通过计算得进给量为1 000 mm/min。
3)精铣十字槽。根据零件图上对于十字槽的加工要求,切削深度与十字槽深度保持一致,取6 mm;通过查阅《数控加工工艺与编程》,铣削速度取100 m/min;主轴转速公式为 n= 1 000 Vc/πd,刀具直径 d 为 8 mm,计算得转速 n 为 1 955 r/min,实际取值 2 000 r/min;通过计算得进给量为700 mm/min。
4)锪 ø20 内腔。根据加工的实际情况,锪 ø20内腔的切削深度取 6 mm;铣削速度取 100 m/min;由 转速公式 n = 1 000 V c / π d ,计算得主轴转速n=1 993.2 r/min,实际取值 2 000 r/min;通过计算得进给量为 1000 mm/min。
3、专用铣床夹具设计
3.1 设计概论
夹具的作用是迅速、方便、安全地安装和夹紧被加工零件,设计夹具时需注意以下几点:
1)夹具中的定位元件能准确确定被加工零件与刀具、机床的相对位置,便于提高被加工零件的精度;
2)夹具的刚度需足够大,防止定位元件和支承元件发生变形,尽量使得定位元件不受到力的作用,以免影响工件精度;
3)夹具能快速实现夹紧和拆卸被加工零件,尽可能减少辅助时间,提高生产效率;
4)夹具能适用于多种加工工艺场合,如车床、钻床、镗床等,进一步提高夹具的使用价值。
3.2 夹具结构设计
3.2.1 确定工件的定位方案
根据六点定位原理,由于该专用夹具装夹的是圆盘类零件,所以除 z 轴的转动自由度不需要限制外,x、y、z 的移动自由度和 x、y 的转动自由度均需要限制。所以,采用固定 v 形块和活动 v 形块来限制 x、y 的移动自由度,采用两个支承板来限制 x、y 的转动自由度以及z的移动自由度。
定位元件包括固定 v 形块、活动 v 形块和支承板,其中固定v形块和活动v形块的材料选用20钢,且渗碳的深度为0.6 mm~1.0 mm,热处理为55 HRC~62 HRC;支承板分为平板式和斜槽式,材料选用 20钢,渗碳深度为0.6 mm~1.2 mm,热处理为55 HRC~62 HRC。
3.2.2 确定工件的夹紧方案
1)夹紧系统的组成。夹具的夹紧系统由三部分组成,分别是动力源、传力机构、夹紧元件。动力源可以是液压驱动,也可以是电驱动,但考虑成本和夹具的简易性,本夹具动力源采用人力;传力机构是动力源和夹紧元件之间的重要媒介,传力机构能直接影响夹具的夹紧效率和夹紧的质量,由于螺杆是最常用的传力机构,且具备良好的自锁性,因此本夹具的传力机构选用螺杆;由于被加工零件为圆盘,同时考虑到加工精度,选用夹紧精度较高的v 形块,v 形块是标准件,易加工制造,且成本较小。
2)夹紧机构的选用。该专用夹具采用螺旋机构夹紧,其具有扩力比大、夹紧效率高、自锁性好等优点。该机构是从斜楔夹紧机构转化来的,通过转动与压紧螺钉相连的手柄就可以使得活动 v 形块沿导轨水平移动,从而夹紧和松开工件。
3)夹紧力的计算。根据力矩平衡的原理,可以得到螺旋夹紧机构的夹紧力 Q为:
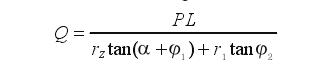
式中:P 为源动力(N);L 为力臂(mm);rz为螺纹中径的一半(mm);r1为压紧螺钉端部的当量摩擦半径(mm);φ1为摩擦角(°);φ2为螺杆端部与工件处的摩擦角(°);α为螺旋升角(°),通常取2°~4°。
经过计算,得到的夹紧力 Q=5 320 N。
3.2.3 辅助装置
1)对刀装置。一般夹具上的对刀装置的类型主要分为成形刀具对刀装置、高度对刀装置、直角对刀装置、组合刀具对刀装置。
加工表面以及零件的结构决定对刀装置的类型。由于该道工序使用数控铣床来加工十字槽,因此选用直角对刀块,材料选用 20钢,热处理55 HRC~60 HRC。
2)定位键。为了确保夹具体与机床工作台紧密贴合不发生相对位移,同时提高被加工零件的加工精度,夹具体与机床工作台之间需要用定位键连接,且需要成对使用以进一步提高连接的稳定性。定位键有矩形和圆形两种结构,圆形定位键,一般应用较少。矩形的定位键最常用,其又可以分为两种结构,一种是在键的侧面开有沟槽的,键分为上下两个部分,其中上部分与夹具体地面的纵向槽配合,部分与机床工作台上的 T 形槽相配合;另一种是上下两部分尺寸相同的矩形键,它经常应用在精度要求不高的场合。为了使夹具体与机床工作台的紧密贴合,选用第一种矩形键。定位键的材料选用 45 钢,热处理为 35 HRC~40 HRC。
3.2.4 夹具体设计
1)夹具体结构的选用。由于各个零件的加工要求均不相同,导致夹具体很难标准化。夹具体大体可分为开式、半开式和框式三种结构,考虑到排屑,选用开式结构;为使废屑沿斜面自由滑下从而排出夹具体外,采用切屑自动排除结构,这种结构是在夹具体上表面专门设置斜面来排屑,适用于废屑比较多的场合;考虑到夹具体能快速安装于铣床上,在夹具体底部设置纵向T型槽。
2)夹具体毛坯的选用。夹具体毛坯一般包括焊接式、铸造式、锻造式和组装式。由于铸造式可以铸造出各种形状的夹具体,且铸造的方法具有制造简单、成本低、生产时间较短等优势,因此夹具体的毛坯选用铸造式。
3)排屑机构。排除废屑一般有两种方案:增大容屑空间和自动排屑机构。增大容屑空间是指进一步增大储屑槽的体积,以防止体积过小导致废屑不能及时排出,从而影响到刀具的工作;自动排屑机构一般是设置斜面让工作中产生的废屑由斜面自由滑落,这种排屑方法结构简单、排屑效果好、能减轻夹具体整体的质量,相比于增大容屑空间的方法,不需要额外设置储屑槽。综合两种方法的优缺点,选用设置斜面的方法以实现自动排屑。
3.3 夹具装配图绘制铣床夹具装配图如图2 所示
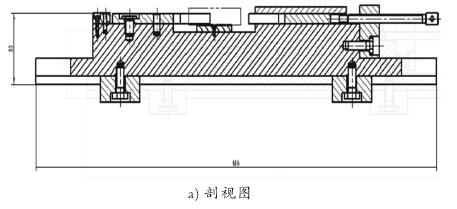
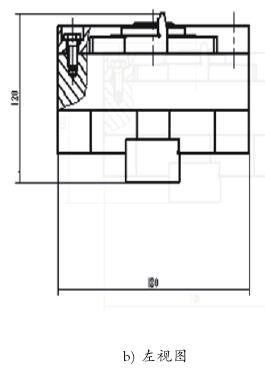
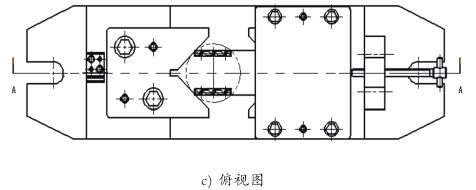
图2 夹具装配图
4 、小结
笔者讨论了数字化加工背景下机床夹具需满足的要求,并针对圆盘类零件的铣床加工工艺,在机械设备制造、数控机加工工艺等课程的基础下设计了该零件的专用铣床夹具,其具有结构简单、操作安全方便、夹紧效率高等优点,使得圆盘类零件的生产效率得到进一步提高。同时,对其他类型机床夹具的设计具有一定的参考意义。
投稿箱:
如果您有机床行业、企业相关新闻稿件发表,或进行资讯合作,欢迎联系本网编辑部, 邮箱:skjcsc@vip.sina.com
如果您有机床行业、企业相关新闻稿件发表,或进行资讯合作,欢迎联系本网编辑部, 邮箱:skjcsc@vip.sina.com