自制气动分度盘在框架类零件加工中的应用
2022-6-30 来源:贵州航天南海科技有限责任公司 作者: 陈天进
某型号产品本体属于典型的框架类零件,用这个产品作为气动分度盘在框架类零件加工中的试验案例。该产品采用的毛坯材料为铝合金整料,原试制数控加工工艺根据工序集中原则,采用精密三轴加工中心多次装夹完成大量的工作内容,加工成本高,零件变形严重,尺寸精度不易保证,合格率不高。经工艺改进后,采用重新设计的气动分度盘工装即可完成零件的精加工。
气动分度盘是利用气缸将压缩空气转换成动力来锁紧产品的一种气动夹具,然后在其基础上加装防振工装,减少产品在加工过程中的振动,可以实现一次装夹,多面加工。
1. 零件的总体分析
零件本体的材料为镁硅铝合金,属于铝合金的一种,其硬度较小、韧性较好,在加工过程中容易产生热变形。
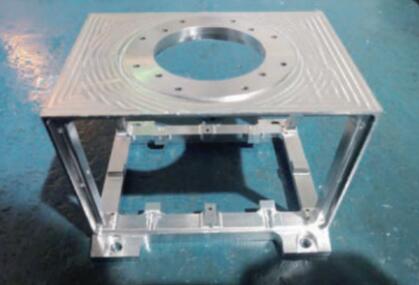
图 1 某型号产品本体
如图 1 所示,产品是将一整块铝原料,经过机械加工成型,且零件型腔内无任何加强筋和支撑,仅靠 4 根支柱支撑,刚性差, 且圆形凸台上表面平面度要求为 0.005mm,内孔公差为0.03mm。
2. 零件加工存在的主要问题
原加工工艺为粗加工→热处理(高低温去应力处理)→依次精加工 6 个面,受铝合金原材料易变形特性所限,尤其在加工最后面的时候,产品内部没有支撑,加工质量不稳定,导致零件线性尺寸超差。
在加工过程中极易产生变形和振刀的现象,从而影响加工精度,导致几何公差超差而造成产品不合格。传统的加工工艺方法为先对毛坯材料进行粗加工,单边留 2mm 的精加工余量,然后进行去应力热处理,最后在三轴立式加工中心上进行精加工,即用虎钳夹持多次翻面进行加工。
由于产品内腔没有任何支撑,在加工的过程中很容易造成产品变形,致使产品圆形凸台上表面的平面度公差超差,零件接刀痕较严重和尺寸超差,对操作人员的装夹要求很高,每次装夹必须要控制好夹紧力。加工效率很低,产品加工质量不易保证。
3. 解决方法和途径
针对产品易变形的特性,按照先粗后精,基准先行的加工原则,先对产品进行粗加工,然后进行去应力热处理。精加工工序 : ①加工基准面。②自制气动分度盘(见图 2)和增加防振工装进行加工后面的面。③半精加工圆形凸台上表面留0.3mm 的精加工余量。④待所有面加工完以后,用精镗刀精加工圆形凸台上表面和内孔的内容,以保证其几何公差。
4. 确定数控加工内容
数控加工一般采用工序集中原则,新加工工艺是以原工艺为基础改进而来的,是对原工艺精铣加工工序内容的加工方法和加工顺序进行改进,将其确定为数控铣削加工工序。基于此,设计了该工装夹具。
由于改进后的工艺采用自制工装加工该框体上的全部型腔、孔,适合放在加工中心设备上加工完成。该零件加工内容只有半精铣、精铣及钻等工步,所需刀具不超过 20 把,故采用现有设备 V20i 立式加工中心即可满足上述要求,工件装夹后可自动完成零件加工。
V20i 立式加工中心各项参数 :X 轴行程为 500mm,Y 轴行程为 450mm,Z 轴行程为500mm,工作台尺寸为 600mm×500mm,定位精度和重复定位精度分别为0.005mm和0.010mm,刀库容量为 20 把,采用机械手换刀。
5. 气动分度盘的设计与制造
为降低生产成本,充分合理利用设备资源,使用自制气动分度盘,通过气缸来锁紧工装,一次装夹(通过转位分度)完成对零件 4 个面的精加工,从而减少了因人为装夹不当或者力度控制不好而造成的零件尺寸超差。
工装设计要求定位精度和分度盘回转精度控制在 0.02mm 以内,结构尺寸合理,同时为了防止产品在加工过程中变形和振动,还加装了防振装置。加工与机床无干涉,装夹方便可靠,满足了加工需要。
工装固定座底面与零件定位面的垂直度控制在 0.02mm 以内,工装回转中心轴与固定座的底面垂直度控制在 0.02mm 以内。定位销与活动转轴的定位孔的配合采用 φ8H6/h5(滑合),固定底座回转中心孔与活动转轴的配合采用 φ63H8/h6(滑合)。
工装的主体采用模具钢,定位销采用优质合金钢(40Cr)经调质处理具有综合力学性能。在定位销上安装一根弹簧,以实现其自动定位的作用。活动转轴的中心孔和定位孔采用镗削和铰削,然后再进行研磨来保证其孔的精度,定位销钉先用数控车床进行加工,然后采用磨削和调质处理,以保证各定位孔和轴的几何公差控制在 0.02mm。自制气动分度盘工装的组成部分如图2所示,先加工产品基准面,把产品固定到工装上,打开气缸,用尾座顶住产品右边的面,加工前后框架面 ; 然后关闭气缸,用防振装置把已加工面支撑好,防止产品加工时变形和振刀,打开气缸,加工上、下两个框架面 ; 最后再关闭气缸,取下产品进行测量,检测合格后进行下一工步的加工。
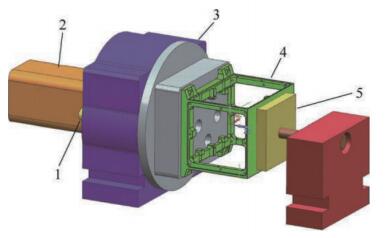
1- 弹性定位销钉 2- 气缸 3-工装固定座 4- 产品 5- 防振装置
图 2 自制气动分度盘
6. 气动分度盘在产品加工中的验证
工装设计是否合格要用科学的检测方式,通过对工装用千分表对其垂直度和回转精度进行检测,均在0.02mm以内;通过高精度三坐标检测机对利用工装加工的首件零件进行检测,尺寸全部合格。经对工装加工的批量产品进行抽检,零件变形量在图样要求公差范围内,批产品检验合格率达 99% 以上,证明工艺改进和工装设计可行可靠。工装效果如图 3 所示。
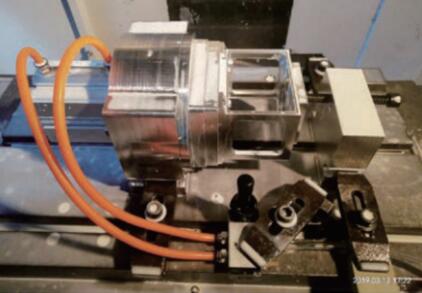
图 3 工装与机床连接示意
7. 结语
通过对该产品的研究和试制,利用自制的气动分度盘和防振装置在某型号产品本体加工中的应用,其技术难度得到有效解决,加工质量完全满足图样要求,合格率达到 99% 以上。实践证明,在加工中心上加工该产品时采用合理的工装装夹方式,可以避免多次装夹过程中对零件造成的变形现象,减少了因多次重复定位而造成的装夹误差,使装夹操作更加方便、准确和便捷。
投稿箱:
如果您有机床行业、企业相关新闻稿件发表,或进行资讯合作,欢迎联系本网编辑部, 邮箱:skjcsc@vip.sina.com
如果您有机床行业、企业相关新闻稿件发表,或进行资讯合作,欢迎联系本网编辑部, 邮箱:skjcsc@vip.sina.com