机器人 RV 减速器主轴承的设计及应用
2021-11-24 来源: 河南广播电视大学 洛阳轴承研究所 作者:王超俊 李智博 王东峰 孙建勇
摘要: 通过对 RV 减速器主轴承受力模型分析得知,要保证其具有足够的径向、轴向及力矩承载能力,则其接触角范围应为 30° ~ 50°; 工艺设计应重点控制内外圈沟位置、配合面平面度、凸出量偏差( 0. 1 mm) 、装配高散差等,而对于套圈宽度偏差、平行差、挡边高度等均可放宽控制标准; 轴承安装时可通过调整 RV 减速器某一侧的垫片厚度保证其具有合适的刚度。
关键词: 滚动轴承; 减速器; 角接触球轴承; 设计; 应用
RV 减速器广泛应用于机器人行业,具有轴向尺寸小,结构紧凑,速比灵活,运转精度高且使用时间长等特性,是在摆线行星减速机构形式上建立的二级封闭传动机构 。
目前,由于国外对 RV 减速器技术的封锁,加上我国在该领域的研究起步较晚,造成国内在该领域与国外差距较大。以其内部使用的关键部件主轴承( 角接触球轴承) 为例,国外厂商采用的均为非标设计,但关于该非标轴承的设计原理及使用方法鲜有报道。鉴于此,基于 RV 减速器的实际使用工况,介绍主轴承的设计和应用。
1、主轴承受力分析
RV 减速器结构如图 1 所示,在使用过程中有行星架输出( 固定减速器外壳) 和外壳输出( 固定行星架) 2 种动力输出方式。主轴承位于减速器外壳与行星架之间,受到减速器外壳与行星架之间的相互作用力,包括轴向力、径向力及倾覆力矩。
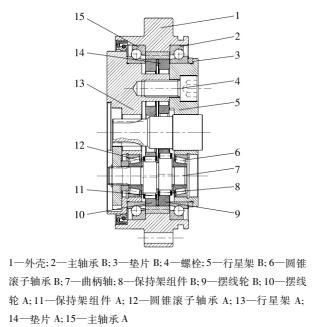
图 1 RV 减速器结构图
重载工业机器人 RV 减速器分布示意图如图2 所示,共装有 6 台 RV 减速器。负载( 也称持重)是工业机器人的一项重要指标,工业机器人在工作过程中工位不断变化,故作用于机器人手腕末端的负载对于 1#,2#,3#RV 减速器既可能是轴向力,也可能是径向力; 对于 4#,5#RV 减速器,在使用过程中主要受径向力; 对于 6#RV 减速器,不仅受到外部作用力,还要承受机械手臂的重力,其受力主要为轴向力和倾覆力矩,对于该位置减速器,必须能够承受尽可能大的轴向力,且具有良好的抗倾覆力矩能力。

图 2 RV 减速器分布示意图
RV 减速器主轴承受力如图 3 所示 ,载荷位于减速器外部,无论减速器在图 2 中何位置,外载荷 F1,F2 将形成施加在主轴承上的倾覆力矩 M1。在外载荷下作用下:

图 3 RV 减速器主轴承受力示意图
由( 1) ,( 2) 式可以看出: 轴承抗倾覆力矩性能不仅与其自身径向承载能力有关,也与其接触角所决定的受力作用点有关。以 RV100C 采用的 H76 /182 轴承为例进行说明,轴承主要结构参数见表 1。
表 1 H76 /182 轴承主要结构参数

参照图 3,基于 RomaxDesigner 建立相应轴系模型,轴承中心距 L 为 100 mm,施加外部倾覆力矩M1 为 1 000 N·m,采用不同接触角的 H76 /182 轴承进行仿真分析,轴承承载能力及径向变形量计算结果见表 2。
表 2 不同接触角 H76 /182 轴承的承载能力及径向变形

由表 2 可知: 接触角增大,额定载荷减小,但由于该轴承背对背安装,接触角增大时,两轴承受力支承点间距 Lmn也增加; 轴承径向变形量由 27. 43μm 减小为 23. 75 μm,说明增大接触角能够提升整个减速器轴系抗倾覆力矩能力; 同时,接触角增大能有效提升整个减速器轴向刚度,适用于受轴向载荷较大的减速器,尤其是图 2 中 6#减速器。
故对于 RV 减速器主轴承,需综合考虑其受力特点,在保证其具有足够径向承载能力的同时,要提升其轴向承载能力及抗倾覆力矩能力。这也验证了 RV 减速器技术指标中力矩刚性的说明。
2、主轴承结构及精度控制
RV 减速器主轴承结构设计时,必须在满足轴承承载能力的前提下,充分考虑减速器系统的结构特点,进而确定主轴承尺寸及精度控制方向。
2. 1 接触角
通过上文分析可知,主轴承接触角显著影响减速器系统的承载能力及结构刚性,通常情况下,采用 40°接触角即可满足上述性能需求。但减速器性能需求根据其在工业机器人中所处位置不同而有所侧重,图 2 中 6#减速器对轴向承载能力及抗倾覆力矩能力要求较高,该位置主轴承应选用更大接触角。分析国外减速器发现各减速器中轴承接触角也并非固定值,通常在 30° ~ 50°之间,接触角应根据其所处位置决定。
2. 2 外圈宽度
国外 RV 减速器用主轴承通常采用内、外圈宽度不等的结构,可以使轴承及减速器轻量化。减速器主轴承虽然也是配对使用,但对配对结果影响最大的是轴承装配高。轴承外圈非基面不与任何部位接触,真正起作用的是图 4 中 L2 部分,即轴承外圈沟位置。

图 4 RV 减速器主轴承安装结构示意图
因此,除轴承外圈沟道直径、沟位置重点控制外,只需控制轴承配合面平面度即可,对于外圈宽度偏差、平行差,均可放宽控制标准。
2. 3 外圈基面挡边高
对于常规轴承,外圈基面挡边高应保证轴承在允许的外力作用下接触椭圆长轴不超出挡边边缘。而对于 RV 减速器主轴承,外圈挡边实际高度远超上述需求,这是由于该挡边需要对图 1 针齿的轴向位移进行限制。在某些 RV 减速器中,外圈挡边还需对摆线轮的轴向位移进行限制。外圈基面挡边高的确定需要考虑针齿及摆线轮在 RV 减速器外壳中的实际位置。
2. 4 内圈参数
与外圈相同,需严控沟道参数和基面平面度,挡边高度仅需保证其在允许的外力作用下接触椭圆长轴不超出挡边边缘。此外,内圈宽度明显大于外圈,且在轴承预紧后,内圈非基面通常高于外圈基面,即凸出量为正,采用该设计方案可以适当限定摆线轮轴向位移,避免轴承外圈由于挡边高度不足而在运转过程中与摆线轮干涉。
2. 5 凸出量
对于标准角接触球轴承,凸出量是轴承能否组配使用的关键,但对于 RV 减速器主轴承,凸出量对轴承应用影响不大,仅对摆线轮轴向位移有一定的影响,其尺寸公差控制在 0. 1 mm 即可。
2. 6 装配高
角接触球轴承若要发挥其高精度、高刚性等性能优势,需对其施加一定的预紧力 ,而装配高将极大影响轴承预紧状态,在生产过程中需精确控制。装配高影响参数众多,若将其严格控制在某一尺寸范围,会增加制造难度及生产成本。在生产过程中仅需控制每批轴承装配高散差即可,轴承预紧力可以通过选配垫片尺寸进行调节。
3、主轴承应用
由图 4 可以看出轴承分布在行星架两侧,背对背安装,轴承预紧方式为定位预紧,可以得到整个减速器装配尺寸链如图 5 所示,图中: TA 为左侧轴承 A 装配高,L1 为外壳挡肩宽,TB 为右侧轴承B 装配高,L3 为垫片理论厚度,L 为行星架左右挡边之间的距离。

图 5 RV 减速器装配尺寸链
在整个装配尺寸链中,为便于控制预紧力,调节右侧垫片厚度 L3 最方便,可以此为整个装配链的闭环,间接保证其尺寸并进行选配安装。装配高 TA,TB 在整个装配链具有重要影响,其尺寸增加( 减小) 将导致 L3 的减小( 增加) ,由于已严格控制装配高散差,垫片厚度 L3 散差也相应得到了控制,选配难度降低。
在上述装配尺寸链中,轴承预紧通过垫片施加,垫片实际尺寸 L'3应在 L3 基础上加上 2 套轴承预紧后的轴向变形量,H76 /182 轴承预紧力与轴向位移的关系如图 6 所示。在实际应用中,可根据减速器整体设计目标确定预紧力,以保证整个
系统具有合适的刚度。

图 6 H76 /182 轴承预紧力与轴向位移的关系
4、结束语
对 RV 减速器主轴承主要受载模型及结构特征进行分析可知: 在主轴承设计时应重点考虑其主要设计参数及结构参数; 在加工制造过程中应重点控制其关键工艺参数,在满足轴承主要性能的同时,考虑其加工经济性; 在轴承应用过程中,应根据其受力情况、使用部位,合理选用配合尺寸、预紧力等,以满足轴承使用性能。
投稿箱:
如果您有机床行业、企业相关新闻稿件发表,或进行资讯合作,欢迎联系本网编辑部, 邮箱:skjcsc@vip.sina.com
如果您有机床行业、企业相关新闻稿件发表,或进行资讯合作,欢迎联系本网编辑部, 邮箱:skjcsc@vip.sina.com