高速一体化轴承实验器结构设计
2021-2-1 来源:上海航空电器有限公司 作者:闫云雪,朱锦超,宫 伟
摘 要:一体化轴承因其优越的性能越来越多的应用于航空领域,轴承使用工况主要为高速、高温、重载,因此研究轴承的失效模式对于优化轴承结构十分重要,结合已有的传动轴承实验机,设计高速一体化轴承实验器,实现对一体化球轴承的加载试验,校核轴承寿命。
关键词:航空领域;一体化轴承;加载试验
近些年来,一体化轴承因其优越的性能越来越多的应用于航空领域,并且航空领域等极苛刻的工作环境对其的需求量日益增长。一体化轴承在未来的发展趋势是外圈与轴承套合为一体,这样在安装时可避免轴承与轴承套的配合问题,减轻了轴承外圈的磨损;安装时采用侧面悬臂安装方式,更加方便快捷,具有明显的优势。
通过对国内外研究现状和研究结果进行分析,发现已有的轴承实验机在加载、供油和测试等方面做的比较粗糙,并且只能针对传统轴承进行实验,如果要对一体化轴承进行高速、高温、重载的实验,还需要重新设计实验器的结构。
该论文研究的是一体化球轴承实验器,并能兼顾一体化滚子轴承,实验器对轴承进行恶劣工况的实验,可以分析轴承在高速、高温、重载等工况下的失效模式和原因,进而优化轴承设计,提高轴承在恶劣工况下的工作能力,延长轴承的使用寿命。
1、实验器总体方案设计
主要考虑的是鼠笼轴承的一体化结构,实验器可以对一体化球(滚子)轴承进行实验,实验器的要求是可以模拟一体化轴承在高速、高温、重载条件下的工作条件,根据某项目提出的要求,技术指标如下:
实验轴承的尺寸 : 内径 Ф50- Φ100mm, 外径Φ80- Φ150mm,长度 100- 400mm;
实验载荷:径向 500- 10000N,轴向 500- 10000N;
系统可以实现的最大转速:24000r/min;
轴承运转时环境温度上限:250°C。
实验系统由驱动系统、加载系统、润滑系统、数据采集和处理系统、实验器主体组成,系统结构图如图1所示,轴承工况通过传感器对轴承的温度、轴心位移进行监测。
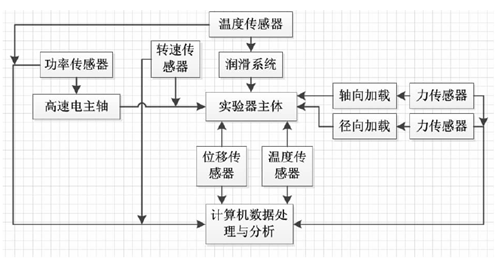
图1:实验器系统结构图
实验器主体是整个系统的核心,是系统的执行部分。实验轴承和支撑轴承安装于实验器的两端,加载轴承在中间,加载力作用在加载轴承上。在轴承端盖和轴承套上开有进回油油孔,润滑油要喷到轴承滚动体上,回油采用重力回油方式。传感器安装到箱体对应位置上,传感器的测量头要与轴承外圈接触。
2、实验器主体结构设计
实验轴承为一体化球轴承时,实验轴承需要承受轴向力和径向力,所以加载轴承选用承载能力较强的角接触球轴承;为了使轴向力可以直接传递给实验轴承,避免支撑轴承承受轴向力,支撑轴承选用圆柱滚子轴承。实验器的结构见图2。
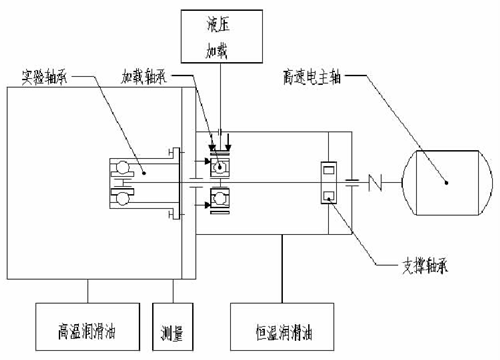
图2:一体化球轴承实验器结构简图
实验轴承为一体化滚子轴承时实验轴承只需要承受径向力,但是为了减少更换元件的麻烦,加载轴承依然选用角接触球轴承;如果支撑轴承还选用滚子轴承,整个轴系统轴向无法定位,实验过程中轴组件可能发生轴向移动,所以支撑轴承改用深沟球轴承即可。
可以看出,轴承实验器主体主要包括三个部分:即支撑轴承部分、加载轴承部分和箱体部分,下面主要介绍这三部分结构设计。
2.1、支撑组件
设计支撑组件需要考虑的是轴承的选择和定位方式、轴承的润滑、组件的密封方式。一体化球轴承的支撑组件的装配图见图3。
要求最高转速是 24000r/min,国内生产的轴承不能实现这样的要求,所以根据实验室的条件,圆柱滚子轴承选用 FAG 公司生产的 NU209 型,FAG 公司生产的轴承相比于国内同型号的轴承极限转速高很多,可以满足要求。
轴承的外圈通过法兰端盖与轴承套两端定位,轴承套卡在箱体上,实现了轴向定位,圆锥销可以防止支撑组件轴向旋转。内圈通过锁紧螺母与主轴两端定位。两个滚子轴承内圈通过一个隔套进行定位,隔套需要与喷油环一同加工,这样可以保证精度。常温润滑油由液压管接头 5 进入支撑轴承组件,由喷油环将润滑油喷至圆柱滚子轴承的滚动体和内圈接触处,这样润滑状况比较好。回油方式为重力回油。
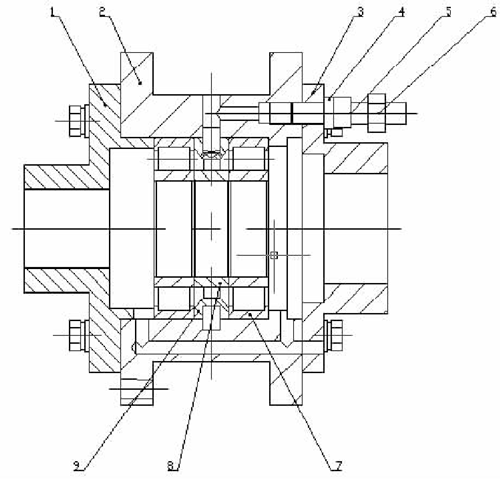
1- 支撑轴承前法兰;2- 支撑轴承外套;3- 支撑轴承后法兰;4- 垫圈;D10;5- 液压管接头;6- 液压管接头螺母;7- 圆柱滚子轴承 NU209;8- 支撑轴承隔套;9- 支撑轴承喷油环。
图3:支撑组件装配图(一体化球轴承)
轴承组件密封方法采用螺旋密封。螺旋密封的工作原理是当主轴旋转时,充满在槽内的液体产生泵送压头,在密封室内产生最高压力,与被密封介质压力相平衡,从而阻止被密封介质外漏。
一体化滚子轴承支撑组件相比于一体化球轴承实验时的支撑组件,不同之处在于将圆柱滚子轴承 NU209 更换为深沟球轴承 6209,喷油环的喷油口位置改变,其他零件尺寸及装配关系未变。
2.2、加载组件结构设计
一体化球轴承实验的加载组件如图 4 所示。加载组件在结构上与支撑轴承相似,图中还包含了液压加载组件。
要求的最高转速是 24000r/min,径向加载最大 10000N,轴向加载最大 10000N,加载轴承选用 FAG 公司生产的角接触球轴承 7211 型,FAG 公司生产的轴承承载能力大,相比于国内同型号的轴承极限转速高很多,可以满足要求。
轴承的外圈通过法兰端盖与轴承套两端定位,轴承套通过一个定位元件实现轴向和径向定位,内圈通过锁紧螺母与主轴两端定位。两个滚子轴承内圈通过一个隔套进行定位,隔套需要与喷油环一同加工,这样可以保证精度。
2.2.1、轴向加载原理分析
通过图4可知,轴向加载组件由法兰、橡胶垫、加载体、承载盘、压头和基座几部分组成。
轴向加载的工作原理:高压油从轴向加载法兰 5 径向的油孔进入,压力作用在加载体 8 上。当加载力最大时,加载体是直径为 10mm 的圆柱体,共有 10 个,呈圆周状均匀放置在承载盘7 的 10 个孔中,若加载力变化,加载体的直径和个数也作相应的变化。压力作用于加载体后,加载体轴向移动,通过加载膜片8 将压力传递给加载压头 10,压头与箱体接触后,会停止移动,这时产生的反力就作用在了加载轴承的外圈上,由于轴承内圈与轴双向固定,所以轴向力通过轴传给了实验轴承。橡胶垫的作用是密封,防止液体泄漏。加载膜片由许多层的叠压弹簧组成,起到缓冲的作用。
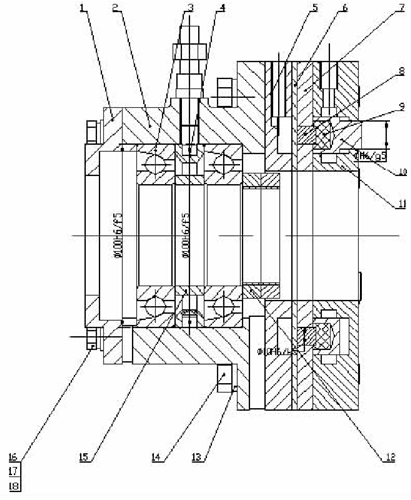
1- 加载轴承前法兰;2- 加载轴承外套;3- 角接触球轴承 7211;4- 喷油
环;5- 轴向加载法兰;6- 橡胶垫;7- 轴向加载承载盘;8- 轴向加载加载
体;9- 轴向加载膜片;10- 轴向加载压头;11- 轴向加载基座;12- 锁紧螺母;13- 弹性垫圈 D12;14- 螺栓 M12X70;15- 加载轴承隔套;16- 螺栓M8X30;17- 弹性垫圈 D8;18- 垫圈 D8。
图4:实验器加载组件(一体化球轴承)
轴向加载基座的圆周方向上还有通入冷却液的孔,呈 70°分布,用于冷却压头。
装配时轴向加载组件通过加载轴承外套进行轴向定位,用螺栓进行连接,未通入高压油时压头端面与箱体内壁距离为2mm,压头可移动的距离是 5mm。
表1是不同压力对应的压强谱:
表1:轴向加载压强谱
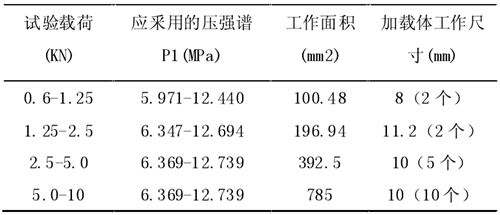
常温润滑油由液压管接头进入加载轴承组件,由喷油环将润滑油喷到角接触球轴承的滚动体和内圈接触处,回油方式为重力回油。
当实验轴承当实验轴承换为圆柱滚子轴承时,由于不需要轴向载荷,所以轴向加载组件用法兰替换。
2.2.2、径向加载原理分析
径向加载组件包括法兰、加载体、承载盘、橡胶垫、加载端盖、压头、冷却体组成。径向加载组件的装配图如图5所示。
径向加载原理:径向加载的原理与轴向加载相似。高压油从法兰油孔进入,通过严封垫 2 作用于加载体 9。加载力为最大161700N 时,加载体为直径 50mm 的圆柱体,当力作用于加载体上,加载体轴向移动,通过加载膜片缓冲,将力传至推杆 5,推杆5 与加载轴承接触,径向力就作用在加载轴承上了。
径向加载法兰 4 和推杆 5 上还有用于推杆冷却的孔,避免温度过高对零件造成损伤。径向加载组件要加密封圈,防止冷却液泄漏。
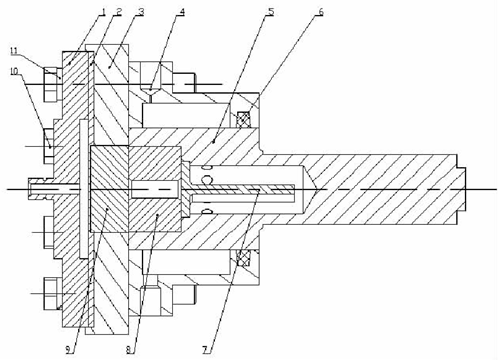
1- 径向加载法兰;2- 橡胶垫;3- 径向加载承载盘;4- 径向加载端盖;5- 径向加载推杆;6- 毛毡圈;7- 冷却体组件;8- 径向加载膜片;9- 轴向加载膜片;10- 螺栓 M12X80;11- 弹簧垫圈 D12。
图5:径向加载组件装配图
径向加载的加载体也是圆柱体,当加载力变化时,改变加载体的直径和即可,表2是不同压力对应的压强谱:
表2:径向加载压强谱
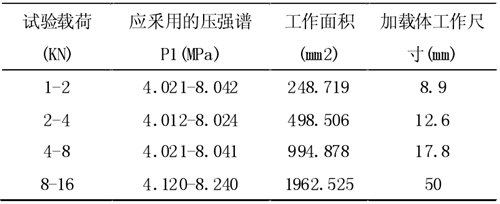
2.3、箱体结构设计
箱体三维图见图6。包括箱体前盖、后盖和箱体底座。箱体底座通过 8 个地脚螺栓固定在实验器平台上,箱体底座和箱盖之间通过螺柱进行连接。箱盖的上方开有小孔,是用来放置传感器或油管、冷却液管通过的。箱体底座和箱盖径向侧壁还有凸台结构,凸台上有螺纹孔,用于径向加载组件的固定。箱体侧壁还开有一些圆孔,用于通油。箱体内部还有加强筋和排油孔。箱体底座底板上还有一圈隔板,可以阻止回油流出箱体。箱体底板长 961mm,宽 560mm,箱体总高 415mm,箱体壁厚 25mm。
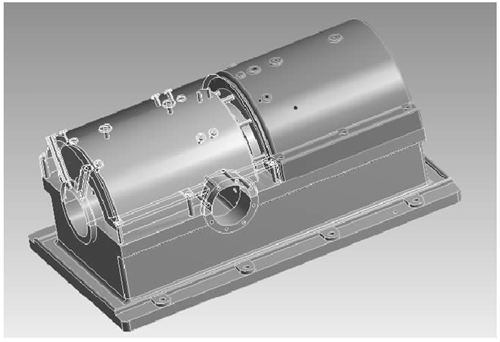
图6:箱体结构图
对实验器箱体进行了静力分析和模态分析在静力分析中,将实验器底座和上盖粘成一体,在近似位置上加载荷,得到了应力、应变分布和最大应力值处,对结构进行优化,可以看出,加强筋是很有用的。
在模态分析中,分析了箱体的六阶振型和对应频率,得到了导致箱体共振的频率对应的转速,分别为:18328.2r/min、19687.8r/min 和21125.4r/min。在自动控制转速的过程中,要尽快避开这些转速。
3、结论
所设计的是集成高速、高温、重载的一体化轴承实验器。在设计的过程中,建立了实验器的三维模型,具有一定的工程应用价值。实验器箱体是实验器最重要的组成部分。通过 Ansys 对箱体进行静力分析和振动模态分析,可以优化实验器的结构设计,增强实验器的极限实验能力,并能获得实验器箱体的共振频率等动态特性,这样就能为自动控制转速提供依据。
投稿箱:
如果您有机床行业、企业相关新闻稿件发表,或进行资讯合作,欢迎联系本网编辑部, 邮箱:skjcsc@vip.sina.com
如果您有机床行业、企业相关新闻稿件发表,或进行资讯合作,欢迎联系本网编辑部, 邮箱:skjcsc@vip.sina.com