高精度数控双柱定梁立式车磨加工中心的研制
2021-1-27 来源: 齐重数控装备股份有限公司 作者:白光勇
摘要:为了完成偏航轴承和变桨轴承桃形沟滚道淬火后硬车削粗、精加工及磨削等高效率精加工,研制了高精度数控双柱定梁立式车磨加工中心,实现滚道的高效硬车削及磨削加工。
关键词:风电轴承;淬硬滚道;车磨加工
0 、引 言
由于海上风电具有风速高、风向稳定、风能资能丰富、不占用陆地资源等优势,已经成为未来发展可再生能源产业的重要组成部分,可以促进沿海地区能源转型,是国家实现能源结构调整的有效保障,对我国转变经济发展方式具有重要意义。随着我国风电行业的发展和产品质量的提升,风电类轴承出口量越来越大,而国外对轴承的精度要求逐渐提高,传统的工艺加工方法和设备已经很难达到要求。
开发具有自主知识产权的高精度双柱定梁立式车磨加工设备是国内亟待解决的国产化瓶颈。针对风电系列关键核心部件, 完成偏航轴承和变桨轴承桃形沟滚道淬火后硬车粗、精加工及磨削等高效率精加工。可以实现零件内外圆柱面、内外圆锥面、平面的车削加工;同时适用于陶瓷、树脂结合剂及烧结刚玉砂轮对零件进行磨削加工。
1 、技术参数及主要结构
工件材料为42Cr Mo4,滚道硬度为60~63 HRC,沟心距公差为±0.02 mm,表面粗糙度为Ra0.4 μm,曲率半径为R±0.08 mm,接触角为45°±1°。机床回转及加工直径为3500 mm,最大加工高度为400 mm,工作台直径为3500 mm,工件最大质量为10 t,工作台转速为1~45 r/min,车削主传动电动机功率为55 k W,水平滑板行程为650~2600 mm,垂直滑板行程为500 mm。磨削主轴电动机功率为75 k W。机床总体结构方案如图1所示。
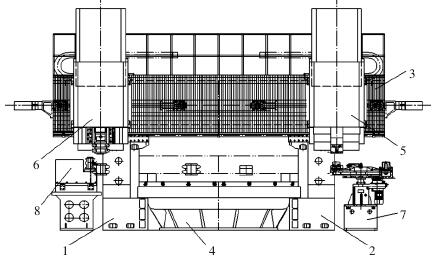
图1 总体结构方案
1.左立柱 2.右立柱 3.横梁 4.工作台单元 5.右车削刀架 6.左磨削刀架 7.车削刀库 8.砂轮修整装置
为了保证风电轴承具有较高的加工精度及较好的表面粗糙度,需要轴承在粗加工后进行淬火热处理,由于热处理后工件硬度高达58~63 HRC,硬度高,加工难大,采用磨削作为后期加工工序。根据工件的加工特点,工件高度不超过400 mm,机床采用定梁龙门架式结构,龙门架由左立柱1、右立柱2、横梁3组成,与工作台底座形成封闭框架结构,整体动静刚度高,满足双刀架高刚度、大抗力切削要求。该机床创新实现工件在工作台单元4上进行一次装卡,用右车削刀架5及左磨削刀架6完成工件淬火半精车、半精磨、精磨加工;减少了采用通用车床及通用磨床的多次装卡、反复找正的误差对加工精度的影响;该机床右车削刀架5和左磨削刀架6创新采用滑板式结构,实现工件淬硬后的大载荷、高速高效车削及高效磨削,同时具有良好的吸振抗振性能;该机床创新采用75 k W超大功率磨削主轴,配置双滚道砂轮卡持主轴,通过高刚度双滚道砂轮修整装置8,一次完成双滚道同时磨削,实现较高的曲率半径及沟心距要求。
2 、主要部件的结构设计
该机床为双柱定梁结构,双立柱贴合在工作台底座左右两侧,横梁安装在左右双立柱上,形成封闭框架。左数控磨削刀架和右数控车削刀架在横梁上左右移动。砂轮修整装置及车削刀库分别布置在工作台单元左右两侧,整机防护装置、液压气动控制装置及电气控制系统布置在主机外侧。
1)定梁龙门架。
定梁龙门架由横梁、左立柱、右立柱组成,经有限元分析进行结构优化。左立柱、左立柱、横梁、工作台底座形成矩形封闭框架结构,满足机床动静刚度要求。左右立柱为左右对称设计,采用阶梯箱形结构,在立柱型腔内部设计有方形筋板,既满足了安装结构尺寸要求,又实现高刚度要求,内部铸造采用封砂结构,增加立柱的整体刚度及整机刚度,减振及抗振性好。左右立柱在前后方向采用大跨度支承,与地基之间采用重型地脚垫铁支承,地脚垫铁环形分布在立柱底座外侧,提高了整机及加工的抗倾翻能力及地基联接支承刚度。横梁采用箱形结构形式,整体矩形两导轨结构,刀架左右移动导轨采用直线导轨与滑动导轨组合的结构形式。刀架左右移动导轨采用高刚度滚柱形直线导轨,在实现大切削力车削及磨削时,在切削力的作用下,刀架与横梁滑动导轨面贴合,并实现滑动移动,既实现了高精度进给,又实现了大承载切削[1]。
横梁采用预变形工艺方法,保证刀架水平移动与工作台导轨的平面度要求。根据前期有限元计算、左右刀架质量、切削力等数据,在机床加工过程中,通过横梁上部加载重物及压紧力,使横梁变形达到工艺要求的数据。横梁精加工完成、去除压重物,横梁上导轨为一个上凸曲线,在安装完左右刀架后,使刀架水平移动与工作台导轨面的平行度不大于0.02 mm/1000 mm。右车削刀架、左磨削刀架水平进给机构布置在横梁上下导轨之间。水平进给电动机安装在横梁左右两端,伺服电动机经行星减速器降速后驱动滚珠丝杠,带动左右刀架实现进给及快速移动。两个刀架采用左、中、右三套防护罩防护,在横梁下端安装有超长导向杆,防护罩两侧采用固定联接,并在导向杆上进行左右方向移动,移动平稳,支承刚性好。机床两个刀架采用左、中、右3套防护罩防护,在横梁下端安装有超长导向杆,防护罩两侧采用固定联接,并在导向杆上进行左右方向移动,移动平稳,支承刚性好。
2)工作台单元。
工作台单元由圆形回转台、工作台底座、主轴单元及车削主传动变速机构等组成。圆形回转台和工作台底座为整体铸造结构。圆形回转台为环形结构,在圆周方向上分布有放射形筋板,在径向方向上分布有环形筋板,圆形回转台下面设计有环形导轨,与工作台底座形成静压导轨副,实现对工件及圆形回转台台面的承重支撑,圆形回转台面上设计有T形槽及止退槽,用于安装卡盘爪,实现工件的卡紧放松。
工作台底座布置有环形恒流静压导轨腔,静压油腔共计12个。工作台静压导轨采用多点齿轮等量对每个静压腔进行单独单腔供油。为了实现圆形工作台导轨副的安全保护,工作台底座上安装有油膜测厚电子元件,当油膜厚度小于0.04 mm时[2],将信号反馈至电控系统,使圆形回转台和工件停止转动。工作台主轴单元由回转主轴、径向定心轴承及轴向预紧轴承组成。主轴单元通过螺栓把合在工作台底座上。径向采用高精度双列短圆柱滚子轴承作为定心支承,轴承内环与主轴采用锥面定位,锥度为1:12,通过调整轴承内环的轴向位置,实现径向间隙的高整,达到图样要求的高精度回转及寿命要求。
轴向预紧轴承安装在主轴上端,通过法兰盘固定在主轴上,对圆形工作台的浮升量进行有效控制,同时提高了工作台静压导轨的油膜刚度,保证工作台单元稳定可靠地运转及工作。工作台底座芯部设置有主轴编码器,实现螺纹加工及恒线速切削功能。车削主传动机构采用立轴传动形式,直流主电动机及各传动轴采用立式平行轴结构布置,通过变速油缸控制,实现主传动两种转速变换,达到车削及磨削的主轴转速范围要求。为了有效降低传动噪声,主传动机构中的所有齿轮均采用优质碳钢或合金钢材质,齿轮齿形表面采用淬火后磨削及修缘的加工方法,提高了传动效率及精度,降低传动振动[3]。
3)右车削刀架。
车刀架为滑枕结构,刀架回转滑座贴和在横梁滑座前面。车刀架垂直进给导轨为滑动导轨,并配置减摩导轨副降低摩擦因数,提高刀架微量进给及定位精度。车刀架垂直进给采用西门子伺服电动机与滚珠丝杠采用直联结构,由两套滚珠丝杠副同时单个刀架(滑板)进行垂直进给运动,传动刚度高、实现主从无间隙微量进给控制。车削滑枕固定在滑板前端,滑枕下端安装有
刀夹快换接口,实现刀库内快速换刀。刀夹采用锥面定位、四角油缸卡紧的方式,实现强力切削。车刀架水平、垂直进给采用光栅尺闭环控制。
4)左磨削刀架。
磨刀架为滑板结构,刀架回转滑座贴合在横梁滑座前面,可手动搬度。磨刀架垂直进给导轨为滚滑复合导轨,并通过滚动导轨和减摩导轨副降低摩擦因数,提高刀架微量进给及定位精度。磨刀架垂直进给采用西门子伺服电动机与滚珠丝杠采用直联结构,由两套滚珠丝杠副同时单个刀架(滑板)进行垂直进给运动,传动刚度高,可实现主从无间隙微量进给控制。通过对两套丝杠副的优化控制,可实现刀具在垂直面内圆周方向的微量调整,提高切削精度。车刀架水平、垂直进给采用光栅尺闭环控制。磨头固定在滑板前端,磨头采用内置电动机结构,主轴前端采用高刚度短锥1∶4结构,砂轮卡持器与主轴采用锥面与端面同时接触的安装方式,锥面为过盈配合,实现高刚度磨削要求[4]。
5)工件冷却及排屑装置。
车、磨刀架均配有工件冷却喷嘴,可对工件、刀具和砂轮进行冷却,以提高加工效果和刀具寿命。铁屑经排屑器分离后输送至铁屑箱内。冷却液通过工作台防护罩、排屑器,回收槽回收至冷却液箱,经过滤循环使用。排屑装置为加宽型链板排屑器。冷却液箱落水口设置有粗滤网、纸质精滤等多种措施,保证冷却液清洁,满足冷却使用要求。
6)工作台防护罩。
工作台防护罩具备安全防护、冷却液回收和铁屑回收功能,采用半防护式结构,车削刀库、砂轮修整装置均采用独立防护,通过气动控制,推开防护门,实现修裁砂轮、更换刀夹,由于机床庞大,拉门使用不频繁,故拉门采用手动结构。
7)砂轮修整装置。
配备单点金刚笔砂轮修整器和金刚滚轮砂轮修整器,修整器支架与地基固定,保证刚性。为了实现工件双滚道同时磨削的要求,金刚滚轮安装在支承主轴上,修整主轴外端配置了高刚度双列圆柱滚子轴承,支承刚度高。修整主轴由11 k W电动机经皮带降速后驱动,修整功率大,传动平稳。
8)车削刀库。
车削刀库采用盘式结构,配置8个刀夹,每个刀夹上安装有不同的刀具接纳口接口,接口采用山特维克C6型式,实现刀具快速准确定位,定位精度为0.003 mm。
9)液压气动控制系统。液压系统主要由液压油箱、主传动电磁滑阀变速控制装置、车削刀架及磨削刀架滑板液压平衡控制装置等组成。液压油箱内的液压油通过油冷机控制油温,保证液压系统的油温恒定,实现液压系统的稳定工作。气动装置经气动三联件进行过滤后,通过气阀控制实现刀具锥柄吹气、光栅尺清洁吹气、防护罩气动门控制等功能
10)电气控制系统。机床采用西门子828D数控系统控制,配置专用电气柜,实现机床PLC及加工控制。高精度数控双柱定梁立式车磨加工中心如图2所示。
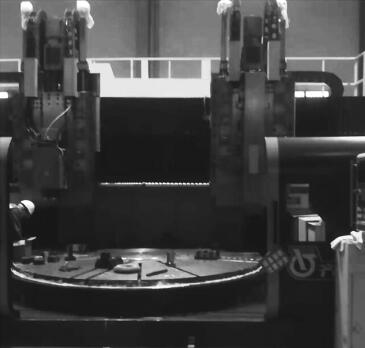
图2 机床现场安装图
3 、创新点
1)创新研制了封砂式定梁龙门结构,保证高速硬车及高精度加工时的整机刚度及高动静阻尼特性。
2)创新研制了车磨刀架垂直方向双丝杠进给驱动机构,消除传动间隙,保证了刀架高刚度微量进给要求,满足沟心距高精度加工要求。
3) 创新研制了砂轮双排桃形沟滚道成形修整机构,采用大功率动力驱动,实现砂轮快速成形修整。
4)创新研制了横梁防护罩保护结构,实现大尺寸风琴式防护罩可靠运行。
4 、结 语
高精度数控双柱定梁立式车磨加工中心成功研制,将打破加工风电轴承关键设备依赖进口的局面,为实现风电大型设备关键零部件国产化打下了坚实的基础。该机床在用户现场安装验收完成,通过了黑龙江省新产品鉴定评审,技术水平处于国内领先地位。随着各种风电轴承类零件规格逐渐增大,软车及硬车、车削与磨削复合加工设备的需求也逐渐增多。该机床具有全面稳定的车削及磨削加工能力,能够实现用户不同的工艺加工要求,功能齐全、精度保持性好、自动化程度高、适应能力强,有较强的市场竞争力,极具推广价值。可为机床制造商及零件生产厂商带来显著的经济效益和社会效益。
投稿箱:
如果您有机床行业、企业相关新闻稿件发表,或进行资讯合作,欢迎联系本网编辑部, 邮箱:skjcsc@vip.sina.com
如果您有机床行业、企业相关新闻稿件发表,或进行资讯合作,欢迎联系本网编辑部, 邮箱:skjcsc@vip.sina.com